Walking on Waves
A pedestrian bridge in Singapore arches hundreds of metres above a six-lane freeway. Made entirely of wood and steel, the elegant undulating frame of Henderson Waves connects two picturesque hills in the country’s southern region. Paul Scott of structural engineering firm Adams Kara Taylor, explains how the bridge came to be built.

The highest footbridge in Singapore. The larger middle ‘wave’ was jacked into place as it was too heavy to hoist with a crane © MHJT
Rippling over the busy Henderson Road that runs through a ravine in Singapore’s hilly Southern Ridges, Henderson Waves is the country’s highest pedestrian bridge. Its design and construction is based entirely on algebraic equations created by UK-based architect George Legendre.
Henderson Waves was commissioned following an open international competition won in 2004 by Legendre’s architectural office IJP Corporation, along with RSP Architects, Planners and Engineers PTE Ltd and structural engineering firm Adams Kara Taylor (AKT). The design was created by applying three-dimensional mathematical wave formulae to structural requirements and local topography, which gives the bridge its flowing, organic appearance.
Scenic setting
The bridge spans two hills, Mount Faber and Telok Blangah Hill, sloping at a slight gradient for 284 m above Henderson Road, a six-lane freeway on the southern coast of Singapore. This location maximizes the visual impact of the structure over the gorge, while minimising its length, resulting in a man-made structure that smoothly integrates with the landscape.
The Henderson crossing has seven spans, six of which have a 3.5 m high arch and are 24 m long. The seventh is bigger with a 6 m high arch, measuring 57 m in length and weighing about 250 tonnes. The upside spans unfold above deck level and encourages activities such as sitting, lounging and sightseeing. The remaining spans unfold below deck level and are not accessible, there simply to ensure continuity of the form and structure.
Two inclined decks extend the bridge at both ends, linking it with the existing pathways and plazas on either side. The difference in elevation between springing and landing is equal to the full height of a seven-storey housing block. In order to achieve the required gradient between the two hills, the bridge takes on a slight horizontal curve which allows a 1 in 12 gradient to be achieved for the full length, together with a series of flat landings every nine metres.
Algebraic design
The design concept of Henderson Waves is based on a folded three-dimensional surface-form created by mathematical formulas. Architects IJP used proprietary mathematical techniques to define the form of the bridge, which bends, undulates, and ascends by 21 m in one movement; in the process it also deforms to provide adequate egress, sloping, shelter, and scenic viewing to pedestrians and cyclists.
The process employed on this project is, however, an important lesson in how the approach taken is just as important as the tools used. Although the project made the best use of the latest software tools, it was initially conceived with a sheet of paper and some creative thought, which set down the basic design parameters for the structure and architecture.
With this information, a formula was developed using Mathcad software, which defined both the skeleton and surface of the bridge. Unlike many projects, this gave both architects and structural engineers the benefit of having complete control over the geometry of the project from the early stages, using just one formula. On a practical level, this meant that the geometry could be moved between software platforms with relative ease and could be exported in a resolution to suit the different tasks required. On a strategic level, having total control of such a form meant the design could be progressed with absolute confidence.
3D modelling
Having set the principles, the IJP model was imported into AKT’s structural frame analysis software, with design loads and steel component properties added, which could inform the early stages of design. This enabled a real-time response to the development of the Mathcad formula and the design of the bridge. What was unusual about this project was that there was a high-level of clarity and co-ordination regarding the design at a very early stage.
A complete model of the bridge was used for analysis, comprising all primary steel members and the supporting pylon structures.
Long-span structures such as bridges bring with them different problems, not just with static loading such as cladding but also live loading and their dynamic response to events like high winds and the shifting pressure of feet on the move. The sensitivity of such structures to the dynamic response is usually a combination of many factors, some of which aren’t fully resolved in detail until the later stages, but in this instance we were able to use this data to refine the original design upfront.
Control over the geometry allowed for close collaboration between development of the bridge’s form and the analysis and production of a series of architectural physical models, which also added to the overall understanding of the design, which was taken to the next stage in collaboration with the engineers of RSP Architects and Planners and Engineers PTE Ltd.
Structure of the Waves
The surface of Henderson Waves is made of steel and timber. Steel is needed for structural purposes, whereas the timber is an aesthetic choice that celebrates natural forms – an important choice of material given that the bridge will form part of a nature walk through the Southern Ridges.
The primary structure of the bridge features a sequence of steel arches and catenaries (or down-facing arches) joined across, and resting upon, reinforced concrete support pylons. Except where the bridge crosses directly over the motorway, these pylons (the tallest of which reaches 38 m) sit between waves at the point where the surface self-intersects and tapers down to a single beam.
BARE BONES OF HENDERSON WAVES
The bridge is made up of several structural steel components:
Central spine: The central spine member follows the gentle curvature of the bridge to provide support to the deck at the mid-point. The section is a steel box that deals with the torsional effects resulting form the curvature of the bridge, which also improves durability and limits the need for maintenance.
Edge members: At the opposite side of the bridge, an edge member is used to support the open area to the deck and the balustrade above.
Central arch: The shape of the arch rises and falls in alternate spans to form a member which works in compression and tension. Its form designed to limit axial forces and provide an elegant support to the curved forms of the bridge.
Mid-height member: The mid height member forms a shallow arch which provides support to the curved steel restraint members. This avoids the need to restrain the arch using a larger spine member working in bending or the need to restrain the arch across the opening below which would obstruct the views to be enjoyed from the seating areas.
Curved steel restraint: The curved steel restraint members provide lateral stability to the central arch member and are located within the surface form of the bridge. They provide a continuous connection between the arch member, the mid-height member, the central spine and the edge member.
Considering the options
While the main structural work is undertaken by the deck members, the curved surface form and the attached components have a secondary role: providing damping to the dynamic performance of the bridge.
In order to achieve the true theoretical alignment of the arches in double curvature, the geometry would need to be defined by either the original formulae or a set of coordinates that ensures the steel box sections remain square to the deck of the bridge. In this case the steel fabricator would work to the set of coordinates to produce a member curved in two directions.
However, in discussions with steel fabricators a preference was expressed to avoid double curvature and work with single-curved arches. This would result in a much simpler central arch member, both in terms of manufacture and fabrication.
A second option considered using five arcs in a single plane to approximate the theoretical curve. This provided the advantage of curving members in one plane but required welding them together to form the arch. Five arcs were chosen as a reasonable split in terms of curvature and manufacturing. In this technique the error between the alignment of the designed arch and the fabricated arch amounted to a deviation of 5 mm for the typical span arches and a deviation of 45 mm for the central span arch.
A third option considered the central arch as a single arc in a single plane. This provided the advantage of curving the member in one plane and reduced the amount of welding. Although for the typical span of 25 m, this arch was likely to be made with a minimum of two pieces, and for the central span of 55 m a minimum of three pieces.
Using this technique, the error between the theoretical alignment of the arch and the fabricated arch amounted to a deviation of 280 mm for the typical span arch and a deviation of 460 mm for the central span arch.
Based on the above studies and the error generated by option two, it was agreed to split the arch into three arcs. This strategy was also to be applied to the curved restrained member (forming the member as a single plane multiple arch).
All members were thus rationalised to single-plane curvatures for the purposes of manufacture and fabrication.
Perfecting the pylons
Over the course of the project, three main schemes were considered for the pylon structures: the original competition scheme, an intermediate hybrid scheme, and a final scheme selected by the design team.
The original competition scheme was initially designed under static loads to give the correct sizes of steel components.The scheme was then modelled dynamically to give the fundamental vertical and horizontal frequencies of the bridge under live loads.
The hybrid scheme was initially developed following concerns over the appearance of the support pylons submitted for the competition. However, following dynamic remodelling, the horizontal frequency was shown to be around 0.8 Hz, which did not satisfy building standards.
Following a further review of the scheme it was concluded that the horizontal deflection of the bridge needed to be reduced. The additional deflections on this scheme, in comparison with the previous one, were caused largely by the deflection of the support pylon and it was therefore deemed necessary to replace it with one of greater stiffness in order to satisfy serviceability requirements.
Final testing
Working closely with IJP to maintain the architectural integrity of the scheme, AKT designed the final solution which was initially checked to conform to static loading requirements. The scheme was then modelled dynamically to give the fundamental vertical and horizontal frequencies.
The 1,500 m2 timber deck sitting on top of the steel structure is the centrepiece of the project, the geometry of which was all derived from the same mathematical formulae as the bridge structure itself.
This ensured that the manufacture of each piece of timber could be described in detail, controlling the final appearance of the surface and contributing to the success of the project. In addition to the bridge deck, the timber surface folds to form the seating areas throughout the length of the structure, providing a smooth transition between deck, seating, and ramped areas.
Ethical timber
To help establish the legal origins of the chosen timber (a tropical hardwood known as Yellow Balau) the Singapore-based timber supplier and global environmental initiative Certisource tested their innovative DNA-tracking techniques to identify appropriate individual DNA markers in trees and ensure they were from legal sources. The process is still pending as pilot studies of a species are typically carried out from six months to a year before the DNA is relied upon as sufficient evidence for certification.
The timber work was carried out locally by experienced timber craftsmen from mainland China, all of whom have been with the manufacturer for years and hand-cut the decking to fit.
Preparing the site
An initial geotechnical investigation for the site was carried out in June 2003 by PSL Engineering PTE Ltd. Further geotechnical investigations were briefed by design engineers RSP and formed the basis for the foundation design.
A series of large reinforced concrete pad foundations were set in the upper dense soils to support the vertical loads from the bridge and provided a base onto which the reinforced concrete pylon structures could be connected. Due to the variation in soil strata, site-specific investigations were undertaken in relation to the actual position of the column structures.

Henderson Waves opened in 2008 and acts as a thoroughfare for pedestrians and cyclists between the nearby parks. It offers spectacular panoramic views during the day and of the city lights at night © IJP Corporation
Construction
During construction, the typical 24 m span members were fabricated, welded, galvanized and painted off-site before being ferried and craned into position. The largest span, which was bigger and heavier than an articulated lorry, had to be assembled in situ on a makeshift platform raised above the freeway before being hoisted into position by hydraulic jacking.
Stability to the bridge structure was provided laterally by the column structures and longitudinally by the tying of the lower deck members. The timber segments were then installed in sequence, followed by the decking.
The Henderson Waves footbridge was officially opened in May 2008 and forms part of plans to construct a green pedestrian corridor linking the Southern Ridges to the waterfront in Bukit Chermin on the south coast. It provides spectacular views of the harbour in the day and of the city lights at night.
BIOGRAPHY – Paul Scott
Paul Scott is a Director at Adams Kara Taylor (AKT). Since joining AKT in 1997, Paul has had several opportunities to translate advanced mathematical concepts into structural forms. They include the Belgo Zuid restaurant in Notting Hill with Foreign Office Architects; Zaha Hadid’s Wolfsburg Science Centre, for which Paul was lead project engineer; and the Henderson Waves footbridge in Singapore.
Keep up-to-date with Ingenia for free
SubscribeOther content from Ingenia
Quick read
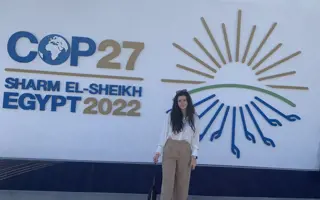
- Environment & sustainability
- Opinion
A young engineer’s perspective on the good, the bad and the ugly of COP27
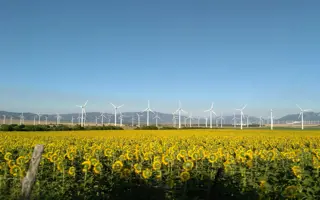
- Environment & sustainability
- Issue 95
How do we pay for net zero technologies?
Quick read
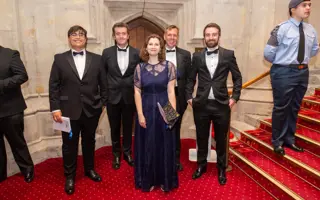
- Transport
- Mechanical
- How I got here
Electrifying trains and STEMAZING outreach
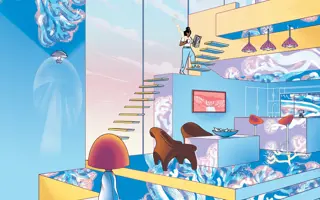
- Civil & structural
- Environment & sustainability
- Issue 95