The need for speed
Laying the groundwork for Britain’s first high-speed rail line
The team responsible for constructing the Channel Tunnel Rail Link is making engineering history with the 109 km line that is due to be completed in 2007. Stage 1 has already seen the movement of complete houses in one piece, the planting of 1.2 million trees and the construction of the longest high-speed rail bridge in Europe …
When the first section of the Channel Tunnel Rail Link opened for commercial services on 28 September 2003, passengers for the most part were unaware of the complex engineering required to build the new line. They knew only that they were going faster than any British train travellers had ever gone before – up to 300 km/h from the mouth of the Channel Tunnel to Fawkham Junction in north Kent.
The success of the Channel Tunnel Rail Link (CTRL) will be measured not only by the technology that underpins it, but also by the time it takes to travel between London and Paris. By that measure, the first section has succeeded by cutting the nearly three-hour trip by 20 minutes. When section 2 – from north Kent to central London – is completed in 2007, another 15 minutes will be shaved off and the entire journey will take as little as two hours and 20 minutes.
This is one of the largest construction projects in Europe and not simply a case of laying track across straight, unobstructed countryside. From the mouth of the Channel Tunnel, the route goes over (and sometimes under) hill and dale, traversing farmland and towns, then dips through a 3 km tunnel beneath the River Thames. Approaching London, it runs along a 1.3 km viaduct under the Queen Elizabeth II Bridge, then plunges into a tunnel near Dagenham and continues underground for 10.5 km to a new international station at Stratford in east London. It then heads into another 7.5 km tunnel before coming out into the light near St Pancras station, the eventual terminal.
The CTRL is 109 km long (section 1 is 74 km, including a 4 km spur line; section 2 is 39 km) and involves 150 bridges, 26 km of tunnels (19 km in London alone) and enough excavation to fill Wembley Stadium 12 times. The line will include new international stations at Ebbsfleet in north Kent and Stratford on section 2, as well as reconstruction of the Ashford International station on section 1 and the enhancement of St Pancras. The train deck at St Pancras is being extended 250 m to accommodate the 400 m long Eurostars, and Barlow’s original Victorian train shed – which once boasted the widest unsupported arch span in the world – is being substantially refurbished, including the restoration of the glazed roof and new facilities in the currently unused undercroft. In addition, three platforms will be created to accommodate new Kent Express services, and a new station on Thameslink will replace the existing King’s Cross Thameslink facilities – currently a lengthy walk from the main station.
Construction of the CTRL, which began in 1998, is managed by Rail Link Engineering, a consortium which includes engineering company Bechtel, design and planning firm Ove Arup & Partners, Britain’s Halcrow & Partners, and French rail project manager Systra. The consortium is building the line for Union Railways, a subsidiary of London & Continental Railways.
The project has produced a number of engineering feats, including two in one weekend in May, 2003 on section 2. The first involved sliding a large prebuilt concrete and steel bridge into place atop a newly built foundation. The other entailed pushing a concrete-box tunnel structure into a channel excavated under the North Kent Line.
The ‘build-and-move’ approach to both operations was designed to minimise disruption of regular passenger and freight train services. Sixteen months of planning prepared the construction team to complete the tasks within a 74-hour planned rail service outage during an early May bank holiday. A crew of 700 worked around the clock, excavating 45 000 m3 cubic metres of earth and lifting 500 m of track, before transporting the two structures into place.
The 111 m long, three-span, steel and concrete bridge was constructed in a clearing about 50 m from its final destination. With the suspension of rail traffic early on Saturday 3 May, the team began excavating a chalk embankment under the existing railway, creating four openings into which the span’s concrete abutments could slide. With the aid of 30 hydraulic jacks, the crew raised the 9000-tonne bridge, then inched it into position in a six-hour operation early on 4 May. During the installation, the bridge’s movement was constantly monitored to keep it within a tolerance of 8 mm.
In a second operation near the bridge site, about 10 000 m3 of chalk were excavated from an embankment to create a channel for a concrete open-base box culvert. Like the bridge, the tunnel, 60 m long, 8 m high, and 6.5 m wide, was fabricated a short distance from its final destination.
Once the area was excavated to level, the team raised the 2200-tonne culvert with jacks onto multi-wheeled hydraulic trailers. The trailers were then driven into the prepared location and removed, leaving the culvert to create a tunnel. Work crews completed the operation by backfilling soil around the structure and reinstating tracks.
One of the most important parts of section 1 of the CTRL is the Medway Crossing, which included construction of a bridge with a total length of 1.2 km. The bridge’s main span of 152 m is the longest ever built in Europe for high-speed rail.
Building the bridge presented engineering challenges. Concrete sections of roadbed exceeding 40 m in length and weighing more than 1000 tonnes were assembled sequentially in a launch area on either side of the river, then slid out on stainless steel bearings fixed on top of piers to span the river banks. Pairs of 900-tonne capacity hydraulic jacks pushed them into place. The main river span was constructed as two balanced cantilevers arising from piers in the River Medway.
About 3 km from the Medway Crossing is the site of another engineering achievement, the North Downs Tunnel. It’s the first high-speed rail tunnel in the United Kingdom and the largest diameter train tunnel. The 3.2 km tunnel was excavated from both ends using road-header machines. Crews worked 24 hours a day, 7 days a week to complete the tunnel during the excavation and primary lining phases. The tunnel was completed five months ahead of schedule in July 2001, at a cost saving of £5 million.
Because a quarter of the CTRL runs underground, tunnelling is a major challenge. To dig tunnels large enough to accommodate trains built to the largest European gauge, designers have made use of huge tunnel boring machines (TBMs) that look like space capsules turned sideways. Local community groups, such as school children and hospital nurses, have given them such names as Bertha, Annie, and Milly the Muncher Cruncher.
The first TBM put into action on the CTRL was Milly, a 95 m long, 1100- tonne behemoth made by the German firm Herrenknecht. It began work in July 2002, setting out from Swanscombe in north Kent toward Essex on the far bank of the Thames. Milly bored through around 100 m per week and completed the first of two tunnels under the river in March 2003.
On Milly’s journey, its 8.15 m diameter cutter head sliced through alluvium, terrace gravels and chalk at a depth of up to 40 m below the surface of the river. As it advanced it placed over 16 000 concrete ring segments behind it to reinforce the tunnel. A pair of 120 m long TBMs manufactured by Kawasaki Heavy Industries have been digging 7.5 km tunnels from Stratford in east London westwards towards St Pancras station, and similar machines are driving towards each other eastward from Stratford and westward from Dagenham to complete the 19 km of London tunnels. About 1.6 million tonnes of spoil will be removed from the Stratford tunnels. It is being taken by conveyor belt to Stratford to raise the ground level there for commercial development.
Along with standard engineering and construction techniques, CTRL designers have employed some cutting-edge technology in an effort to keep costs down. One example is technology that makes equipment easier to identify – and therefore harder to steal.
Project workers are marking expensive equipment with SmartWater Instant, a clear, water-based solution containing microscopic particles encoded with the owner’s information. The SmartWater is invisible to the naked eye, but it shows up under ultraviolet light. Then it is a simple matter to locate the owner’s identification number.
‘The plan is to make things as unattractive as possible to a thief, which is why we are marking all our products with stickers as well as with SmartWater,’ says Rail Link Engineering Security Manager Basil Haddrell. ‘It’s the first time this kind of initiative has been taken on this type of project.’
Throughout construction, CTRL personnel have sought to minimise impacts on the environment, and to mitigate any adverse effects. A team of up to 35 ecologists have overseen the planting of 1.2 million new trees and shrubs on section 1 in the Kent countryside, chosen to mirror native flora and to provide wildlife habitats. The project has also created 630 acres of woodland and 30 km of hedgerows. More than 100 hazel dormice have been taken to new breeding grounds in central England as part of a repopulation scheme. Thousands of bats, badgers, water voles and other creatures have been transported away from the CTRL route to new habitats, including artificial badger burrows and bat nesting boxes. In addition, Union Railways provided core funding of £2 million to the Rail Link Countryside Initiative, a scheme that funds projects to enhance nature conservation, ecological and landscape interests and public access near the railway.
The project has also taken pains to protect archeological relics discovered during excavation for the new line. Finds along the route have included an Anglo-Saxon burial ground at Cuxton and a major Roman complex and Anglo-Saxon water mill at Ebbsfleet. At Saltwood in east Kent, the newly discovered grave of an affluent woman in an Anglo-Saxon cemetery was found to contain artifacts of national importance, including a superbly preserved gold and silver brooch studded with garnets and emeralds.
Twelve buildings are being moved timber by timber or, in one case, slid intact, to new locations to make way for the CTRL. These include seven buildings of a historically important Georgian model farm at Hothfield. Yonsea Farm has been dismantled and is being re-erected at the South of England Rare Breed Centre in Woodchurch, where it will become a ‘living museum’ featuring animal breeds common in the nineteenth century. Bridge House in Mersham, a sixteenth-century timber-framed construction, was moved intact and in one piece in July 2000 to a new location to safeguard it from the construction of the CTRL. The 450-tonne house, supported internally and externally by concrete beams, was lifted off the ground by 15 vertical jacks and pulled 55 m by three additional jacks, sliding on a medium of greased rubber and polished metal.
By combining the technology of today with a sense of history, the project is helping usher in the future of rail travel in Britain. When the CTRL is completed in 2007, its anticipated success will be a source of pride for the engineers involved and the improved speed and comfort of transport a great benefit to the travelling public.
Bechtel
Keep up-to-date with Ingenia for free
SubscribeOther content from Ingenia
Quick read
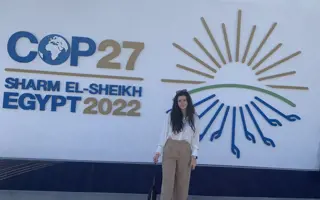
- Environment & sustainability
- Opinion
A young engineer’s perspective on the good, the bad and the ugly of COP27
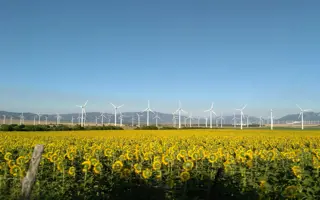
- Environment & sustainability
- Issue 95
How do we pay for net zero technologies?
Quick read
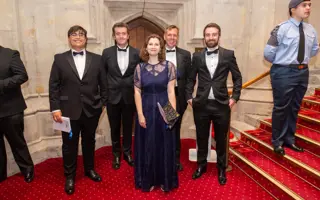
- Transport
- Mechanical
- How I got here
Electrifying trains and STEMAZING outreach
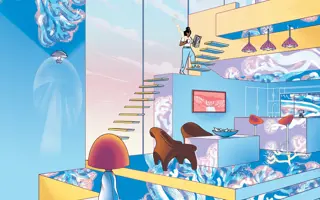
- Civil & structural
- Environment & sustainability
- Issue 95