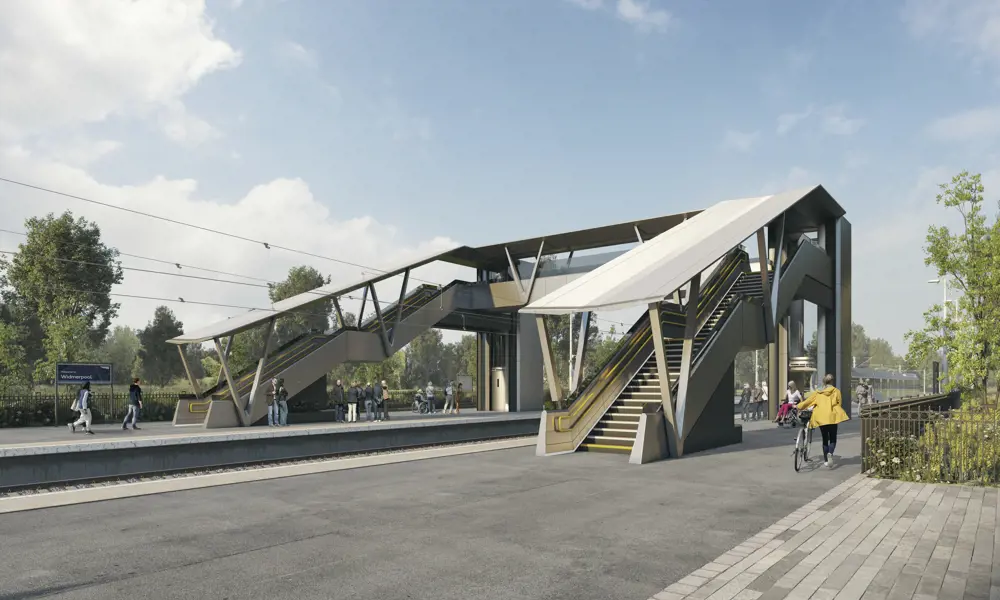
The ‘flat-pack’ footbridge for train stations
Did you know?
🦶 Footbridge facts
- Railway station footbridges can cost more than £4 million each, take a year or more to build, installation closes railways multiple times, and they are expensive to maintain
- The design, manufacture and construction of these footbridges hasn’t been updated in decades
- The new AVA footbridge can be manufactured and built off-site, then slotted together like a giant Meccano set when installed
Although probably not given much thought by many, the railway footbridge plays an important role at numerous train stations across the UK, allowing travellers to access their required platform and continue their journey. Yet, the design, manufacture and construction of these ordinary structures have changed little over the past century. And all have significant impact: basic railway footbridges cost £3 million to £4 million each, with more modern designs costing more; take a year or more on site to build; require multiple disruptive ‘possessions’ of the railway; and are expensive to maintain. With many also being in place for several decades, upgrades are needed for stations to become more accessible and greener.
To address these challenges, Network Rail brought together a consortium of firms that were relatively new to railway work (with one exception) and SMEs with specific expertise, with the reasoning that these kinds of companies would be more agile in developing and responding to new ideas. The result is the modular design of the AVA footbridge, which aims to revolutionise how footbridges are built, reducing time, cost and whole-life carbon emissions. It can be adjusted to fit any station anywhere.
The modular design of the AVA footbridge aims to revolutionise how footbridges are built, reducing time, cost and whole-life carbon emissions.
Building a bridge in a factory
The key aspects of the bridge’s design are factory production and low maintenance. One of the new contractors, X-Treme Systems, a stainless steel fabricator, had particular expertise in manufacture from stainless steel sheets. This and its experience of constructing bespoke storage systems from cut and folded sheets neatly fitted the brief. The consortium chose stainless steel as the core material, which is expensive initially, but also rustproof, vandal proof and never needs repainting. Also, steel sheet can be laser cut, drilled and folded to almost any shape with tolerances as tight as 0.2 millimetres, by robotic machines controlled by fully integrated 3D software models that include every nut, bolt and plate.
The footbridge’s structure is created from a standard 3 metre by 1.5 metre plate, which can be as thin as 6 millimetres. The designers were careful to maximise the use of each sheet to minimise waste, using software to match the number of parts to be cut from a standard sheet. Although about 5% of the bridge’s joints have been welded (using high heat to melt the parts together, which then cool and fuse), the extreme accuracy of the machine-cut parts means that bolted connections are more appropriate and allow the whole bridge to be snapped together like a Meccano set. Elements are factory-connected into 1.2-metre-long modules, then taken to an assembly shop for connection into about nine units (including the bridge deck, stairs units, roof units and V-shaped roof supports) for transport to site.

Manufacturing the AVA Bridge (L–R): The computer screen shows a 3 metre by 1.5 metre steel sheet marked up multiple parts to be laser cut, using 92.9% of the sheet, resulting in less wastage and carbon emissions. The sheet is cut by the computer-controlled laser and then folded © X-Treme Systems
Building a better lift
Lifts are essential to keep stations accessible for everyone
Very early on, the Expedition team identified a major deficiency in the initial brief: it did not include a requirement to innovate with the lifts, now an essential element of station footbridges as part of Network Rail’s Access for All Programme to provide accessible routes to and between platforms. They are also the source of most public complaints about existing footbridges.
Network Rail currently relies on ‘standard’ lifts that are designed for office environments. They require major works on site, including construction of a ‘building’ to house each lift and excavation of deep lift wells. They also conform to the manufacturers’ business model, which relies on follow-up maintenance work. They are also notoriously unreliable and frequently out of service, the most common faults occurring in the door mechanisms.
The consortium brought in SCX Special Projects to look at the lifts. The Sheffield-based company responds to complex and difficult engineering challenges, including mechanical handling for the nuclear industry. Its highest-profile projects are the sliding roofs for Wimbledon’s Centre Court and Number One Court, and the retractable football pitch for Tottenham Hotspur’s new stadium (The football pitch in three pieces, Ingenia 77). The only lift it designed was a specialist fitting for a Royal Navy hospital ship more than 20 years ago.
SCX quickly discovered some of the peculiarities of station lifts. They are often located in areas open to the public and can be subject to rough handling. This can vary from forcing doors open or accidentally dropping a box of screws on the floor (some of which then jam the door mechanism), to behaviour including riding on top of the lift car, camping in the lift well or, in one case, setting fire to a mattress placed in a shopping trolley, pushing the trolley into the lift and pressing ‘go’, then sharing a video of the resulting inferno on social media. The new lifts needed to be safe and robust.
Unlike the structure of the bridge itself, the lift is a mechanism that will require regular maintenance throughout its life. Maintaining standard lifts frequently requires operatives to stand on the lift roof, and even to sit in the lift well while the lift descends – both with clear (and largely avoidable) safety issues. So the lift design had to simplify maintenance.
SCX established three principles for the new lift: fully modular construction, independent of the adjacent bridge; full commissioning completed in the factory, with the lift then transported to site and simply ‘plugged in’; and sufficient redundancy in the mechanisms to minimise downtime.
Most challenging of all were the myriad of British Standards and Network Rail regulations governing the design and operation of lifts, all for very good safety reasons, but presenting a bureaucratic obstacle to innovation and change.
SCX chose to substitute the more conventional hydraulic or cable drive with a belt drive, both to keep the system simple and to provide 100% redundancy. Two motors drive six thermoplastic polyurethane belts, each of which encases 20 steel cords.
The design’s key element was the lift cab itself. This needed to be visually attractive, comfortable to operate (especially for wheelchair users) and reliable – particularly the doors. Current lifts typically have four-part concertina doors with large numbers of moving parts, making them vulnerable to failure. Instead, a semicircular shape was chosen for the cab, with two curved glass sliding doors driven by relatively simple belt mechanisms. To verify its robustness, a prototype of the door is undergoing 24/7 operational tests, including with SCX’s ‘virtual foot’ and ‘virtual hand’ to mimic blockages, to replicate the 15 million cycle design life.
The two 1.1 metre doors are on opposite sides for simple entry one side and exit the other, but the cab contains a 1.6-metre turning circle, so where site constraints limit the options to a single door, wheelchair users can turn and do not need to reverse out. Passengers also have a continuous view out, through the glass.
The welded tubular steel structure of the lift, clad in stainless steel, is manufactured in three modules: the base and top units, and a spacer module in between. The three units are joined, the mechanisms and cab inserted, and the completed lift is tested and commissioned in the factory. It is then laid flat on a lorry, transported to site, lifted upright and placed alongside the new bridge. It sits on any foundation type and is connected to the bridge by simple expansion joints: the lift is structurally independent and capable of resisting the strongest winds without support from the bridge. The whole installation process is intended to be as quick and simple as installing a new washing machine at home.
Maintenance is assisted by innovative remote monitoring, with alerts sent if repairs are needed. The system’s redundancy means the lift can still operate until repairs can be made. Also, all maintainable items are at ground level or within the cab, and access panels and hatches allow full system inspection.
The new lift is already receiving interest for use with other bridges besides AVA.

A cut-away of the bridge and its integrated services, showing the preassembled and precommissioned lifts simply delivered and ‘plugged in’ like a new washing machine © Expedition Engineering
Site preparation for the bridges normally avoids the disruptive and time-consuming ‘wet trades’, in this case mixing and using concrete, with the option of installing some grillages or screw pile anchorage systems. A relatively shallow lift well will need to be excavated, requiring less disruptive and expensive temporary works. The bridge parts can then be lifted into place and bolted together, and the precommissioned lifts attached [see ‘The lift’]. Initially, construction will require possession of the railway over two weekends, but the aim is to reduce this to one.

Modifications made following testing of the prototype resulted in the primary structure of a U-frame formed from two longitudinal girders, concealed within the parapet and linked by crossbeams. The main girders are made of 1.2 metre-long panels folded to make a C, with the top and bottom flanges strengthened by extra plates, and all elements bolted together to form a continuous structure. This allowed a continuous glass window to be provided above the parapet, improving the user experience. (The U-frame above is supported on an improvised construction trolley, made from recycled parts of the original prototype) © X-Treme Systems
Perfecting the prototype
As part of the design process, a full-scale prototype was built both to test manufacturing efficiency and to help promote the concept at Network Rail and outside of it. Lessons learned prompted design changes.
As a result, the roof is supported on V-shaped pillars, and although the bridge is open at the sides, a roof increases the winter deck temperature, to minimise the use expensive and corrosive de-icing salts. Inside the bridge and stairways, the finishes are also in stainless steel, folded and bolted. The finishing – including glazing – is done before shipping to site.
The stainless steel sheets are bead blasted (have glass or steel beads shot at them at high pressure) to dull the surface and reduce solar glare, which could distract train drivers. The process creates an attractive finish and does not affect one of the material’s main advantages: graffiti can be sprayed with a water jet or wiped off relatively easily. The design also had to discourage other forms of vandalism, including tampering with the structure or climbing on the outside – the engineers employed a solid parapet approach to make it harder to climb.
What makes flat-pack a better fit for footbridges?
Cost and carbon comparisons with conventional footbridges are complicated by the current high volatility of material and component costs. Stainless steel is more expensive and contains more carbon upfront, but mild steel requires three or four coats of paint after manufacture.
Critically, mild steel footbridges must be repainted every 30 years or so, causing serious disruption, while stainless steel used for the AVA footbridge should last a lifetime of more than 120 years and will result in lower whole-life carbon emissions.
Network Rail estimates that current footbridges take 9 to 12 months to construct on site and cost £3 million to £4 million each – less than 17% of which is for the superstructure and materials; the remainder goes towards items such as contractor’s preliminaries, project management and risk costs. The AVA footbridge aims to reduce capital costs by a third, time on site by two-thirds and overall project time by three-quarters. There will also be a reduction in whole-life carbon emissions. Its service life will increase by 200% and lift reliability by 100%.
Response to the design has been extremely positive, with the first order – for Stowmarket station in Suffolk – placed even before the ‘demonstration’ bridge was installed over Network Rail’s live test track at Widmerpool in Nottinghamshire later in 2022. However, to achieve the main benefits of factory production, manufacturers of the bridge will need a steady stream of orders. Policymakers make decisions on railway investment separately for each region, and spending on each individual bridge may require Department for Transport (DfT) approval at various stages: for example, Stowmarket bridge has been ordered by local train operator Greater Anglia but required approval from both National Rail and the DfT.
X-Treme Systems believes that at least five orders a year will be required to maintain a production line. There are some 2,500 stations in the UK, some with more than one footbridge and many in urgent need of replacement. If demand grows, the process allows other SMEs (in the UK or elsewhere) with similar robotic equipment to simply take on the manufacture, fed by the same 3D software.
Companies across the world have also shown serious interest, including Irish Rail, Los Angeles Metro, Toronto Metro, Indian Railways, and New South Wales Railways. There is also clear potential for other uses, such as pedestrian bridges over highways, and Network Rail is already looking at how a similar approach could improve station design.
Success with the AVA footbridge could well pave the way for wider adoption of manufactured infrastructure.
***
This article has been adapted from "A 'flat-pack' footbridge", which originally appeared in the print edition of Ingenia 92 (September 2022).
Keep up-to-date with Ingenia for free
SubscribeRelated content
Civil & structural

Building the Shard
The Shard is one of London's most iconic buildings. The tallest in Western Europe, it was designed by Italian architect Renzo Piano and dominates the city’s skyline. Ingenia spoke to John Parker, project director for structural engineers WSP, who outlined the engineering decisions made in building the enormous steel and glass structure.

The return of arched bridges
Arch bridges are strong, durable and require little maintenance. However, very few had been built since the early 1900s until the FlexiArch was developed and launched in 2007. Now, there has been a minor renaissance for this ancient form of construction.

Creating user-friendly buildings
For Michelle McDowell, a former Business Woman of the Year, a passion for joined-up design thinking and building information modelling with a user-friendly approach has enabled her to pioneer revolutionary changes in her field.

Troja Bridge
In November 2014, one of the world’s largest network arch bridges was officially opened in Prague. The UK may soon have its first network arch bridge if the go-ahead is given for a new rail project in Manchester.
Other content from Ingenia
Quick read
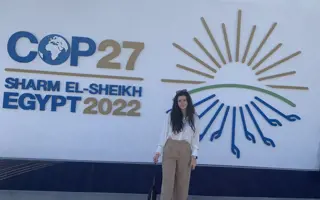
- Environment & sustainability
- Opinion
A young engineer’s perspective on the good, the bad and the ugly of COP27
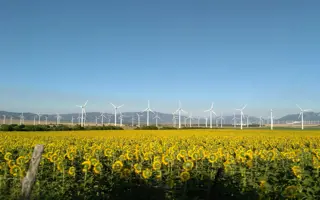
- Environment & sustainability
- Issue 95
How do we pay for net zero technologies?
Quick read
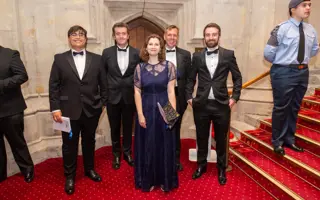
- Transport
- Mechanical
- How I got here
Electrifying trains and STEMAZING outreach
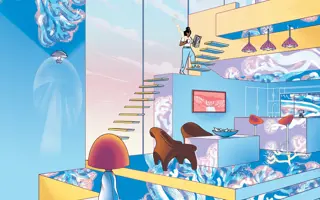
- Civil & structural
- Environment & sustainability
- Issue 95