
The engineers turning surplus feathers into packaging
In a world that’s relying on packaging more than ever, manufacturers are increasingly on the hunt for greener alternatives to plastic. It’s not easy replacing this uniquely versatile and strong family of materials. In their search, material scientists and engineers have turned their attention and ingenuity to a variety of natural materials, including seaweed, pea and rapeseed proteins, and even… feathers.
Feathers might strike you as an odd choice for a packaging material. But during her master’s at Imperial College London, Elena Dieckmann discovered that millions of tonnes of surplus feathers are generated globally every year. Figuring there must be a way to use them, Elena hit upon the need to keep items cold during transport. Known as the ‘cold chain’, major industries such as the life science and pharmaceutical industries face unique challenges when attempting to transport lifesaving but temperature-sensitive items.
Greener insulation
The cold chain may not get much airtime, but it is critically important for health. An increasing amount of novel therapeutics must be kept within a correct temperature range. If a vaccine gets too warm, it can begin to destabilise and lose efficacy. Lifesaving gene therapy products could instantly be destroyed by the formation of ice crystals if it gets too cold.
Known as the ‘cold chain’, major industries such as the life science and pharmaceutical industries face unique challenges when attempting to transport lifesaving but temperature-sensitive items.
Preserving the cold chain can be particularly challenging when shipments must be sent over large distances or to areas with poor ‘last mile’ logistical infrastructure. The biopharma industry alone is estimated to lose approximately $35 billion annually to temperature failures. To mitigate the risks in these scenarios, companies pack medical products in specially insulated boxes before shipping. These carefully designed solutions work as a package, combining insulation materials plus a coolant, which can include regular water-based materials or dry ice, if you need it really cold. (Pfizer used the latter to keep its COVID-19 vaccine at –70°C, which is colder than Antarctica.)
“If you want to ship a measles vaccine to Africa, you really have a very long logistics supply chain, and this is why you need a high-performance insulating material,” explains Elena. The current go-to is expanded polystyrene. Sometimes known by its trade name Styrofoam, expanded polystyrene is the plastic foam you might also find cushioning items such as electronics, or sometimes in takeaway cups and containers.
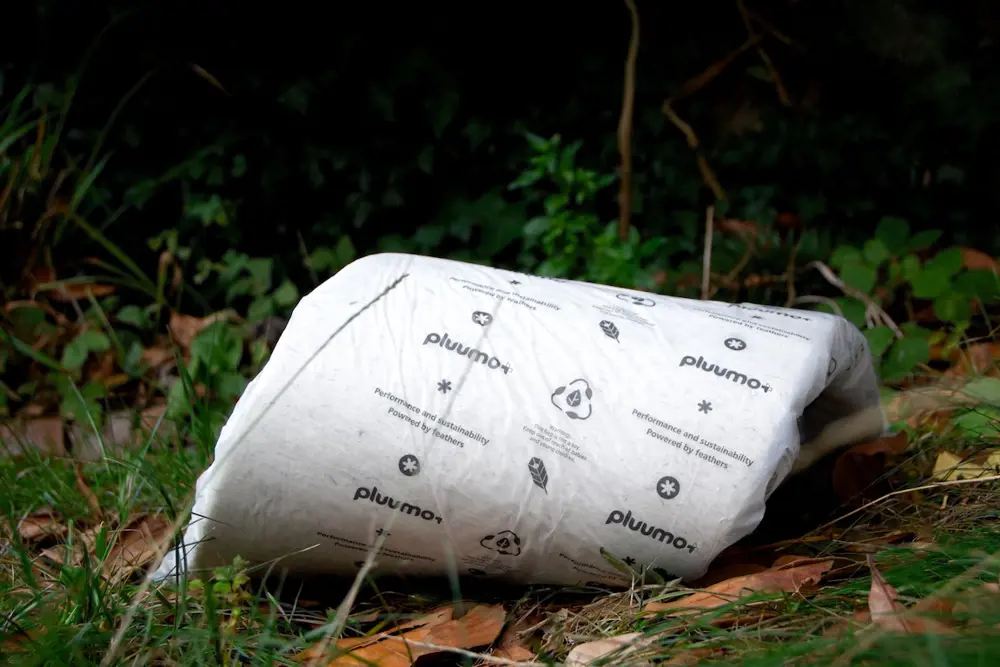
To make their insulating packaging material PluumoPlus, Aeropowder processes surplus feathers into a thick mat and encapsulates it in a biodegradable liner © Aeropowder
With sustainability in mind, companies are increasingly looking to phase out expanded polystyrene because it is extremely expensive to recycle. Elena quotes a cost of up to $3,000 per tonne, “so, it’s not a winning business,” she says. “Often [it] just gets chucked into landfill or incinerated sometimes. But there’s no healthy end-of-life option for polystyrene as it is.” Since hardly anyone is recycling it, that also means consuming more fossil fuels to produce new expanded polystyrene.
Instead of sending all this expanded polystyrene and all those feathers to landfill, why not just use the feathers for insulation instead? With this in mind, Elena and co-founder Ryan Robinson (who is now CEO) set up their company Aeropowder and began developing the product.
The avian wonder material
"Feathers are actually a real wonder material built by nature,” explains Elena. They’re at the heart of many birds’ mating displays – such as the peacock’s – and of course, are essential for creating lift and thrust in flight. As if this wasn’t enough, they also protect birds from the elements, providing crucial waterproofing and trapping heat.
These insulating properties are why people have been stuffing pillows and duvets with feathers for centuries. The secret behind feathers’ warmth comes down to their material properties. “They’re hollow inside, and if you look into the microstructure, they trap air,” says Elena. The main shaft of a feather extends from the tip of the quill, with tiny hair-like filaments protruding along its length. In flight feathers, the filaments are hooked together to give a more rigid form. The filaments in down feathers waft unattached from one another, to maximise air trapping and thus, insulation.
“Feathers are actually a real wonder material built by nature.”
Elena Dieckmann, Co-Founder, Aeropowder
Creating a new circular economy
Clearly, you can’t just pack a load of feathers into a box and call it a day. With their patented process, feathers are converted into a unique textile mat that can be produced in a variety of shapes and sizes for the requirements of clients.
“Our material intrinsically possesses excellent insulation properties, but like all other insulation materials, performs better when made thicker. This proved technically challenging for a number of reasons, but extra thickness is critical for delivering the required level of thermal performance for a pharmaceutical-grade product,” explains Elena. The material is cut to the sizes needed for the packaging box it will ultimately become, and then sealed in a biodegradable and compostable liner for ease of handling.
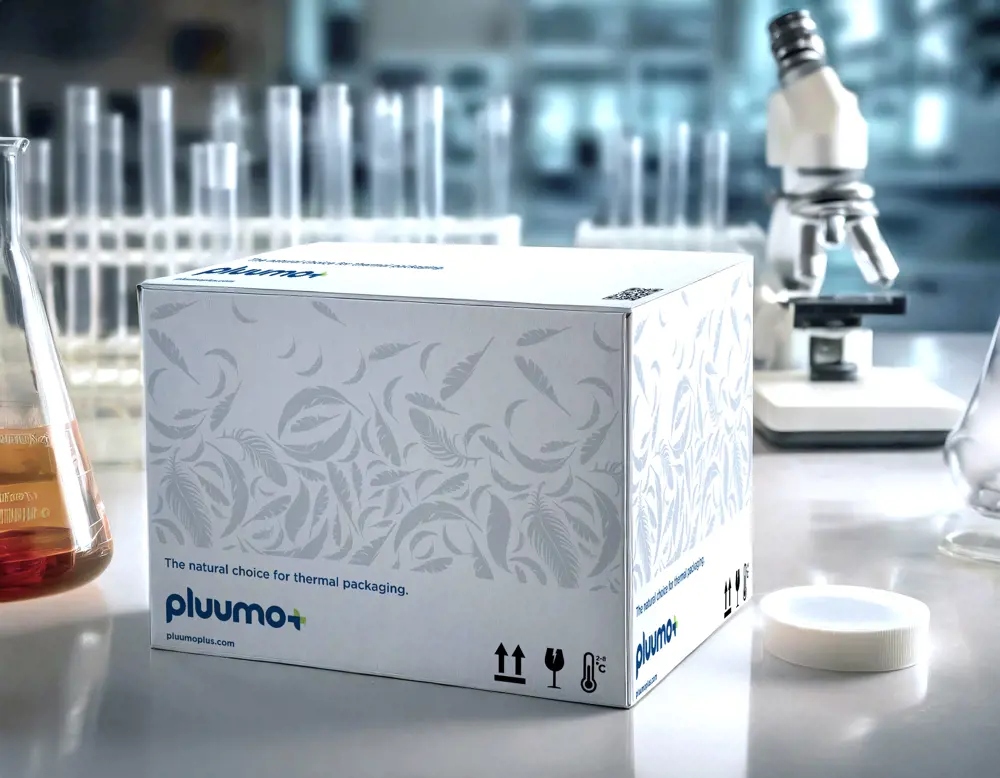
© Aeropowder
Aeropowder’s first target market for the product was in the direct-to-consumer food delivery space, where items such as meal kits needed to be kept cold for overnight delivery. Recognising the potential for their material to finally provide a required level of thermal performance for the higher-end pharmaceutical and life science industries, the company is about to launch PluumoPlus, a sustainable thermal packaging solution that can keep the products inside cold for 72 hours even under challenging industry-standing shipping conditions. This is a game-changing level of thermal protection for the industry, as generally the pharmaceutical industry has struggled to move away from expanded polystyrene given performance deficits of the current crop of sustainable alternatives.
Beyond packaging, Aeropowder has other potential products up its proverbial sleeve, including expanding the use case for its insulation to the construction industry or creating solutions to control oil-spill environmental cleanups. Having just raised £150,000 from the British Design Fund, the future looks bright for Aeropowder and its plans create a new circular economy from a fluffy wonder material.
Contributors
Florence Downs
Editorial Manager
Keep up-to-date with Ingenia for free
SubscribeRelated content
Design & manufacturing

Super cool(er)
Welsh startup Sure Chill has developed a cooler that uses the properties of water to keep its contents cool for around 10 days without electricity. This is ideal for storing items such as vaccines where electricity sources are unreliable.

R&D investment makes good business sense
In just five years, Dr Ralf Speth FREng has presided over a revolution in design and manufacturing that has helped create a new family of engines and has overhauled Jaguar Land Rover (JLR) production facilities.

Steel can arise from the ashes of coal
Thousands of people were laid off in the UK steel industry in 2015 and there are pessimistic future forecasts. Professor Sridhar Seetharaman of the Warwick Manufacturing Group argues that smaller, flexible steel mills implementing new technology would better cope with fluctuating global trends.

Integrating metrology in business and academe
Professor Jane Jiang’s interest in measuring began when she worked on a bus production line in China. She found that the best way to improve quality, consistency and productivity was through metrology, the science of measurement. Today, she runs the UK’s largest metrology research group.
Other content from Ingenia
Quick read
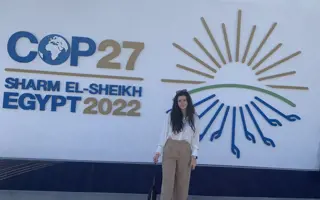
- Environment & sustainability
- Opinion
A young engineer’s perspective on the good, the bad and the ugly of COP27
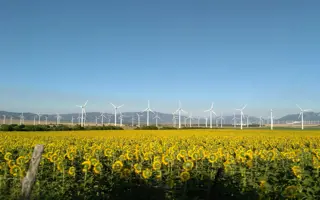
- Environment & sustainability
- Issue 95
How do we pay for net zero technologies?
Quick read
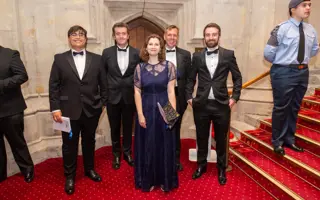
- Transport
- Mechanical
- How I got here
Electrifying trains and STEMAZING outreach
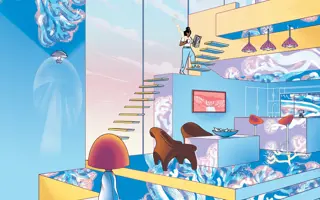
- Civil & structural
- Environment & sustainability
- Issue 95