
Tattoo's New Grandstand
Visualisation of the new stand. To maintain and boost the existing seat count, more efficient use needed to be made of the space at the East end of the Esplanade (on this picture the far end stand). To achieve this, the new north and south stands were designed to sweep around and connect to the east stand, creating a bowl shape which gives much improved sightlines for that section of the audience © The Royal Edinburgh Military Tattoo Ltd
During the summer of 2011, visitors to the Royal Edinburgh Military Tattoo enjoyed the spectacle from a brand new grandstand. The newly completed temporary structure can be erected in half the time of the previous stand and can hold over 8,800 spectators. Ian Lumsden, the Design Manager and Structural Engineer for the project, explains how the flexible stand was conceived, designed and built.
First established in 1950 and now drawing some 217,000 visitors a year, the Royal Edinburgh Military Tattoo is known the world over for its spectacular military musical displays. Over the years more than 12 million people have watched bands march across Edinburgh Castle’s drawbridge on the Castle Esplanade – bringing in an estimated £80 million a year to the Scottish economy. This year, the audience sat in a brand new grandstand, representing the Tattoo’s biggest infrastructure project in 40 years.
Changes needed
The festival grandstand is set up anew each year for mid-July when a series of concerts and events precede the Tattoo. The previous temporary structure was designed some 35 years ago, based on the ‘Mero’ space frame system. This system is constructed from individual elements connected together using a series of spherical threaded nodal joints. Capable of holding up to 8,600 people, the structure took around three months to erect and then 10 weeks to dismantle. However, in recent years this time-frame and the disruption caused had become unacceptable.
While the grandstand was under construction, visitors had only limited access to the castle and its Esplanade. With this in mind, the Royal Edinburgh Military Tattoo Ltd set out to design and build a new grandstand that halved the set-up time and improved visitor access to the castle during this process.
They wanted the new grandstand to provide more comfortable seating for at least 8,600 people. Not easy for a structure perched on the top of a hill with steep banks sweeping down from its sides. They also needed to resolve health and safety issues and provide good sightlines for all members of the Tattoo audience. Without these changes it was likely that the Tattoo would have ceased performances within 10 years.
The setting
Edinburgh Castle was built on Castle Rock. The Rock was created millions of years ago when retreating ice sheets deposited glacial debris behind a hard volcanic plug, leaving the distinctive ‘crag and tail’ formation in which a rocky hill is isolated from surrounding ground. The city’s main thoroughfare, the Royal Mile, was built after the castle, running down the spine of the crag and tail to Holyrood Palace.
The Castle Esplanade is a long, open, level area, some 3,000m2 in size, located between the Castle and Edinburgh High Street, part of the Royal Mile. Now the venue for the annual Edinburgh Tattoo, it is also designated a World Heritage Site, whose promenade is lined with a number of statues and monuments. It was these that posed the first engineering challenge for the grandstand designers.
In preparation for the new grandstand, the Tattoo construction team had to relocate two of the Esplanade’s historic monuments - a statue of Scottish military figure Earl Douglas Haig and The Scottish Horse, firstly to avoid them getting in the way of the stands and secondly to optimise pedestrian, disabled and emergency access.
The former was moved to a new location within the Castle walls, while the second was relocated to a new bastion. However, these relocations only took place after considerable work on each of the monuments. As part of their treatment, conservationists removed biological growth, copper stains and graffiti, repaired cracks and filled pits while painstakingly preparing each new site so that each monument could be safely relocated, reassembled and remodelled. In each case, a conservation sculptor also studied the sculpture and then remodelled any missing components.
Another important preparatory step was to investigate the geological conditions below the grandstand. The geology beneath the Esplanade is complex, partly because of its volcanic origins but also due to man-made changes that would have taken place during the construction of the Castle and Esplanade. Extensive site investigations provided the much needed geotechnical information to design the grandstand foundations.
Works commence
Armed with this information and aware of the construction time-frame and space constraints imposed by the Esplanade engineers from Arup designed 326 mini-pile foundations to be drilled up to 22m deep including a maximum 6m socket onto the castle bedrock using small drilling rigs. Mini-pile foundations are quick to install and can also withstand heavy loads. This was crucial as calculations indicated the piles would each need to support 1,000kN vertical forces (equivalent to around 100 tonnes weight).
The mini-piles were then capped using 120 tonnes of steel reinforcement and 810m3 of concrete. Additional raking piles were introduced to resist the significant 30 tonne horizontal forces on each mini-pile from the strong local winds and exposed site.
The groundworks were completed over two winters by Sir Robert McAlpine, the main contractors on the project. With the new foundations successfully in place, it was time to build the grandstand. With this in mind the free standing cover and structure architects’ Nussli/formTL Radolfzell designed a new structure that, when put together, formed a new grandstand with a new geometry. Various structural options were considered in the design. Typical proprietary seating systems principally comprise scaffolding type structures made up of lightweight materials that are manhandled into place. But while these systems can be quick to erect , construction is labour intensive and importantly, such a lightweight structure would not have the strength nor stiffness to deal with the large cantilever spans over the edge of the esplanade. The team settled on a hybrid scheme comprising a bespoke steel frame structure with elements from a proprietary seating system.
This relatively simple hybrid scheme proved quick to erect with large pre-fabricated trusses transported to site during construction, assembled into pairs with intermediate steel girders, and then lifted into place by cranes.
Grandstand layout
The steel supporting structure for the north and south sections of the new grandstand comprises so-called fishbelly lattice girders, with curved chords connected by a lattice web. For the south sections these 28m girders are spaced 3.5m apart and mounted around the perimeter, enabling the actual stand to extend up to 9m beyond the crag of Castle Rock. Meanwhile the main girders for the north grandstand are mounted on a horizontal two-chord truss, distributing the load over tower supports.
The north and south stands, aligned parallel to each other (unlike the old stands), are connected by a relatively short east stand in which the main girders are held by numerous supports. The resulting U-shaped geometry makes the most of the limited space on the Esplanade, with the total number of seats now 8,825, compared to 8,600 previously. The new geometry creates a rectangular performance space that is much easier to use for the show.
Up to 26 rows of seats are arranged across the girders in the north and south stands, which means that spectators in the top rows are sitting 13m above the parade ground. Indeed, many in the audience now have a better view than before and there are more open areas beneath the stands. The minimum seat width is now 500mm while row to row spacing is 800mm; this represents a 35% increase in space per seat compared to past stands, giving the spectators more knee and elbow room.
In line with today’s standards, the designers also explored various options to provide higher capacity and more choice for disabled spectators. While previous grandstands provided space for 30 wheelchairs with attendants as well as 20 additional spaces for ambulant disabled, the latest design incorporates a total of 73 wheelchair seats – with adjacent seats for companions. A lift also provides disabled access to a number of levels, including the VIP boxes and production control rooms on the east stand.
Designers used dynamic pedestrian modelling to work out which layout would provide spectators with the quickest access to and from stands. They looked at how the visitors could best circulate around the grandstand and tested various spectator loading and unloading scenarios. Modelling indicated that relocating the exit from the rear of the stands (as in the old design) to the front of the structure could reduce the time taken for spectators to leave the show.
Open for business
From 2012, the new £16 million grandstand will be erected in just 40 days (compared to the three months that it used to take). Dismantling is predicted to take 37 days. There were 6,799 pieces of steelwork used which required 1,700 crane lifts. Even with all this crane activity, set-up and dismantling times have been halved. And with the number of available seats also increasing all requests from the Edinburgh Tattoo partners have been satisfied.
A purpose-built 230m2 VIP reception area with seating for 148 people has been created. The portaloos that used to service the facilities have been replaced with built-in toilets with hot and cold running water. The production amenities have been improved, creating more room for lighting and sound equipment. There are also new rest areas for about 350 performers.
The Edinburgh Tattoo now has a larger, more comfortable temporary grandstand system that can be erected and dismantled much more efficiently, freeing up access to the Esplanade and the views of the Castle for around two months more per year than previously. And as the Tattoo’s Chief Executive, Brigadier David Allfrey, put it, “Demand for tickets this year has been incredible, particularly given the current economic challenges. On the day we opened for business, we sold 660 preview tickets over the counter, phone and internet in just 10 minutes!”
Keep up-to-date with Ingenia for free
SubscribeOther content from Ingenia
Quick read
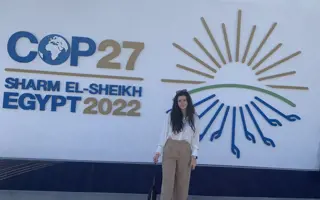
- Environment & sustainability
- Opinion
A young engineer’s perspective on the good, the bad and the ugly of COP27
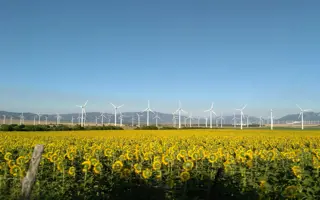
- Environment & sustainability
- Issue 95
How do we pay for net zero technologies?
Quick read
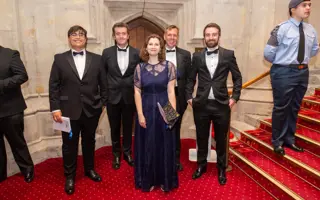
- Transport
- Mechanical
- How I got here
Electrifying trains and STEMAZING outreach
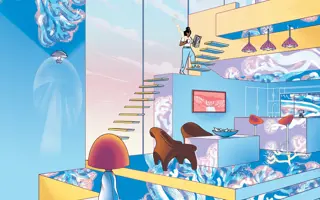
- Civil & structural
- Environment & sustainability
- Issue 95