
T5 goes live
Terminal 5 will be the new home for BA at Heathrow airport © Arup
Heathrow’s Terminal 5 is the biggest free standing building in the UK. The single span wave-shaped roof can be seen from miles around and inside creates a feeling of light and space. Dervilla Mitchell FREng led the Arup team and acted as Head of Design Management for this project. In this article, she writes about the logistics of building the Terminal building and installing the new air traffic control tower.
When Heathrow Airport opened in 1946, a group of tents and a few phone boxes formed the first passenger terminal. Facilities at the airport have moved on somewhat since then, but there is always scope for development and so, at the end of the 1980s, BAA started its ambitious plans for a fifth terminal.
Heathrow is one of the busiest airports in the world wit h the potential to be a crowded and stressful place. The intention of the design team was to create a building where both staff and passengers would feel relaxed and comfortable – as well as addressing the ever changing demands of the industry.
Designed and engineered by Arup, with architects Rogers Stirk Harbour and the steel manufacturer Severfield Rowen, the single span roof arching over the superstructure brings together the different activities within the building. This includes the latest check-in and baggage handling facilities, customer services, a massive open plan departure lounge – there are no separate gate rooms – as well as over 100 stores and restaurants across T5A and T5B, its adjoining satellite building.
The multi-billion pound project is aiming to bring back some glamour to air travel and creates for BAA a flexible internal space that allows them to alter the building in the future without the constraint of roof columns.
T5A Roof
The roof has a span of 156 m, and is 396 m long. It is supported by 22 pairs of 914 mm diameter steel legs that reach down to apron level in dramatic full height spaces just inside the façades. The three-storey superstructure of the Terminal is completely separate from the roof and the façades. Façades made up from over 5,500 glass panels enable passengers to look around them at the airfield as well as at the planes taking off and coming in to land. The glass for these panels is coated with a film which controls the amounts of sunlight coming in and prevents the terminal building from overheating.
For the roof, we had to design for manufacture and assembly, meaning that we had to make sure that our designs could be erected. We had to maximise offsite fabrication and we had to avoid any welding on this structure (owing to the danger element, the fact that it can be prone to error and is a relatively slow process).
The innovative design would not have been possible without applying the principles of risk management to the design and construction process. The main roof nodes and rafters were prefabricated and assembled into the largest pieces that could be transported to the site. This reduced the amount of work that would be done under more hazardous site conditions, thus improving safety and programme certainty. It also reduced the number of vehicles moving on and off the site.
Designing the roof
The structural geometry of the roof means that it deflects significantly when loaded asymmetrically. In order to ensure that we had fully accounted for the asymmetrical effects of wind loading, we carried out a time-history dynamic analysis of the results from the wind tunnel test – see Modal Buckling Analysis overleaf.
The structural action of this roof lies somewhere between the stone vaults of a cathedral and the portal frame steelwork of a retail warehouse. As in a cathedral roof vault, the self-weight of the roof and the steelwork generates compression in the rafters and legs, and the feet push outwards and downwards on the apron level slab. This outwards force is resisted by steel beams in the apron level structure. This ‘arch action’ in the rafters massively reduces the bending moments they would otherwise have to resist.
One of the crucial elements were the 35 tonne torso nodes that connected the arms, legs and wings, and could carry comprehensive loads of up to 18,000 kN. The final node design took inspiration from those old-fashioned wooden puzzles that you might find in your Christmas stocking. The nodes are made from pieces of steel plate 250 mm thick that are flame cut to shape and slot together. The bolts provide robustness but do not carry the primary forces.
Erection method
The design team recognised the complexity of the roof structure and the potential risks to the construction programme, so planned a full scale trial of one complete abutment structure at Dalton in North Yorkshire. This trial in 2003 allowed the erection team to practice with little risk and highlighted over 140 issues which were then addressed prior to real production – preventing considerable delays.
When it came to the on-site assembly, the roof was put together in five phases of 54 m and one of 18 m. The central arched section of each phase was assembled, clad and pre-stressed at ground level, and temporary works frames used to position the abutment steel for each phase accurately. The centre section was then jacked 30 m vertically into position and bolted to the abutment steel. Once each phase was complete the temporary works frames were rolled north by 54 m ready for the next phase.
A new control tower
The original 39 m high control tower at Heathrow was built in 1955 and is located adjacent to Terminals 1, 2 and 3. Whilst this location was ideal for the original layout of the airport, the building of Terminal 5 in the west meant that there would be obstructions to the required sightlines between the tower and the aircraft. A new tower had to be installed and be operational prior to the opening of Terminal 5.
The air traffic control tower at Heathrow is run by the National Air Traffic Services. The air traffic controllers are responsible for the approaching and departing aircraft as well as the aircraft taxiing to and from the gates. A key requirement of the Visual Control Room, where they operate, is that visual contact is maintained with aircraft at all times.
The new tower consists of a four storey cab supported on a steel shaft some 87 m above apron level close to Terminal 3. The Visual Control Room floor uppermost providing accommodation for the controllers. Below this are equipment and plant rooms, offices, rest rooms and facilities for staff, together with an ‘active damper‘ which controls the tower‘s movement from the wind. The shaft below contains stairs, an internal lift and various mechanical, electrical and IT risers. There is also an external lift attached to the side of the shaft. A 100 m pedestrian bridge links the control tower building to the Terminal 3 building.
Design and construction
It was critical to minimize any disruption to operations, so the design of a control tower and the construction methodology had to be developed simultaneously. Having considered many alternatives, the team decided upon an early construction of the top 27 m of the tower away from the final site and the prefabrication of 12m mast sections fitted out with stairs, lift cores and services.
BAA identified a suitable open site on the southern perimeter of the airport, far enough away from aircraft and taxiways to allow unrestricted use of cranes. A benefit of this solution was that it would enable the cab construction and fit out to start early and be progressing in parallel with site clearance and the installation of the tower foundations at the final site.
Moving the Cab
Preplanning the cab for its 1.5 km move across the airport involved a number of criteria. The route north crossed the southern runway and involved using the main taxiways. The entire route had to be precisely assessed for its load-carrying capacity because at close to 900 tonnes, the transported load greatly exceeded the 400 tonnes of a fully loaded Boeing 747 for which the pavement was designed. Damage to the runway or breakdown of the transporter en route could cause effective closure of the airport incurring costs likely to exceed half the value of the entire control tower project!
The cone-shaped top section of the control tower was moved into place on an October night in 2004. The control tower section was carried along taxiways and across the southern runway by three remote-controlled hydraulic 144-wheel flatbeds run by a specialised team in just under two hours. The 144-wheel flatbeds were able to provided sufficient spread of the huge load with no damage to the airfield.
The structure was then slowly raised by the use of strand jacks until the first steel section of the tower could be inserted underneath it. The steel column, consisting of six sections and the tower were progressively raised one section at a time over several nights.
Prior to its use on site, the control logic of this custom-written jacking software had been tested and refined using a small scale test rig to differentiate between guy loads generated by wind on the tower and those created by the vertical lift of the tower. In order to establish the verticality of the tower during erection, both optical and GPS surveying was used to monitor the plumb of the mast. The top of the tower was maintained within 25 mm of plumb throughout most of the procedure. All five mast lifts were completed without incident and accomplished without interrupting normal airport operations.
Dynamic performance of the tower
The setting of appropriate dynamic performance or ‘comfort’ criteria for the air traffic controllers working in the tower was complex. In the case of wind-induced lateral movements the acceptable performance is both time dependent and varies with occupier sensitivity.
During the early design stages the levels of acceptable movement of the Visual Control Room were agreed with the air traffic controllers by demonstrating various levels of lateral acceleration on a motion simulator at Southampton University.
The air traffic controllers were put inside the Institute of Sound and Vibration Research’s simulator and windy conditions were imitated from slight breezes to much more violent forces - the sort of freak high winds you might get twice in a decade. The ATCs were aware of the fact that the floor was moving and that this is what it would be like in the new tower - but felt the sensation was at an acceptable level.
At Heathrow, where there are strong windy conditions on a regular basis, it was the lower strength winds that controlled the design of the tower rather than the less frequent high wind storms where the occupants’ tolerance of acceptable movement is higher.
The building was handed over to the National Air Traffic Services in March 2006 and following a period for fit-out of the air-traffic control systems followed by staff training and acclimatisation, the new tower went live in February 2007.
Sixty controllers have now moved into the £50 million tower at the geographic heart of Heathrow, giving controllers an unequalled 360 degree panoramic view of the airfield. The tower provides an unrivalled working environment with its advanced systems technology enabling the controllers to deliver a safe and efficient service for decades to come.
The tower will deliver capacity and service improvements to meet the needs of Terminal 5 and beyond. It has the very latest air traffic control technology, including state of the art electronic flight progress strips which provide for safety and service improvements.
Construction planning
For other parts of the project, the team took planning to a new dimension. There developed a system of 4D construction planning which uses software to produce an animation of construction works by linking CAD data to one or more schedules. The 4D (the fourth dimension being time) simulation was used for the Heathrow interchange which is a space between the T5A building, the T5A car park and the rail station. This was a complex building interface between projects.
Arup worked closely with software provider Autodesk NavisWorks to create a high-level integrated 4D CAD model identifying the overall build sequence. This added the model geometry – including contractor exclusion zones, crane usage, access, and general site logistics – to the programme generated from the detailed plans.
Once the model contained sufficient detail, everyone involved met at weekly planning sessions to continue building the 4D plan and debate site clashes. At the meetings, the model was projected on a big screen to show sequences at any time interval, down to as little as daily in some critical instances. Once issues were resolved, the model could be quickly updated and AVI (movie) files distributed around the team to improve communication.
The result was cost savings of £2.5million in the first nine months of use and a reduction in the length of the original master programme by six months.
Taking off
This is just a snapshot of the 37 million man hours of work involved in the Terminal 5 project during the 20 years from inception to completion and of course the verdict of the passengers passing through T5 – predicted to be 30 million per year – is still to come.
However, Heathrow’s T5 looks set to be remembered as one of the most remarkable engineering stories of the 21st century with innovative IT and engineering solutions at the very forefront of the achievement. The opposition and delays that the project faced in the 1990s meant that greater knowledge and understanding had been assembled by the time the go ahead was given in 2001.
In the end, this £4.3 billion project was delivered safely and well within agreed time and budget limits. It is part of a £6billion investment plan by BAA who want to replace Terminals 1 and 2 by 2012 – by which date almost the entire airport will have been rebuilt or redesigned – with an end result a mile away from the few tents and phone boxes that existed at its inception.
Biography – Dervilla Mitchell FREng
Dervilla Mitchell is based in London and co-leads the Arup aviation business. She spent six years at Heathrow in various different roles leading the structural teams there. Prior to T5 she worked on a number of projects including Portcullis House at Westminster and the redevelopment of the Goodwood Paddock.
The author would like to thank Richard Matthews, Steve McKechnie and Stuart Kerr and for their help in preparing this article.
Keep up-to-date with Ingenia for free
SubscribeOther content from Ingenia
Quick read
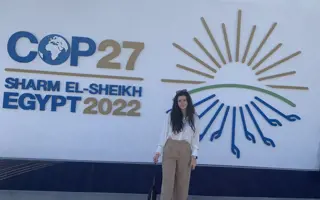
- Environment & sustainability
- Opinion
A young engineer’s perspective on the good, the bad and the ugly of COP27
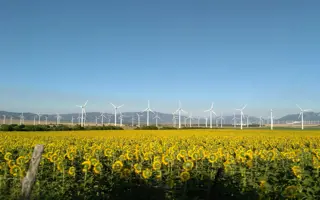
- Environment & sustainability
- Issue 95
How do we pay for net zero technologies?
Quick read
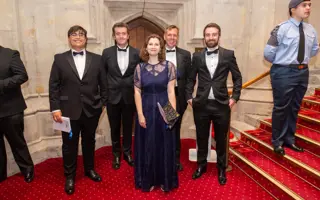
- Transport
- Mechanical
- How I got here
Electrifying trains and STEMAZING outreach
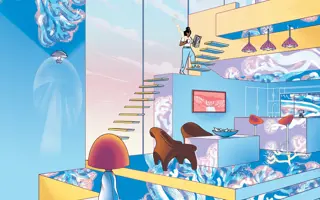
- Civil & structural
- Environment & sustainability
- Issue 95