
Restoration of the Forth Bridge
The Forth Bridge viewed from North Queensferry following the completion of the restoration works, November 2011 © John Andrew
The seemingly never-ending job of painting the Forth Bridge is coming to an end. The logistics and challenges behind the successful conclusion of the 10-year project to restore the bridge are outlined by John Andrew, the Business Development Director for Balfour Beatty Regional Civil Engineering, the principal contractor for the Forth Bridge Restoration Contract.
December 2011 saw the completion of a decade-long project to repair and completely repaint the Forth Bridge for the first time in its 121 years of operation. The restoration works involved one of the largest-scale tasks of its kind, featuring innovative scaffolding techniques and encapsulation methods that have since been replicated on other large civil engineering and building projects.
The Forth Bridge, which opened in 1890, had never before been subjected to this level of treatment. The logistics for this £130 million project, on the world’s first cantilever and Britain’s first all-steel bridge, were complex and carried out mindful of its protected status as a Grade A listed Victorian engineering icon. The entire 53,000 tonne bridge, standing over 110 metres above high water to the top of each cantilever, was stripped back to bare metal. Repairs were carried out and the latest surface coating materials, developed with technology employed on North Sea oil installations, were used to recoat the bridge to provide long-term protection for the structure.
An additional challenge was posed by the need to undertake the works with minimal disruption to rail services and in all weathers on a ‘live’ operating structure which can carry up to 200 train movements daily over the 2.5 km length of this key strategic transport route.
Balfour Beatty, founded only a few years after the bridge’s opening, was entrusted with the role of principal contractor for delivery of this unique restoration project on an iconic Scottish landmark. It worked for, and in partnership with, operating customer Network Rail.

The scaffolding and encapsulation on the Forth Bridge enabled access to every square metre of the structure and ensured the safety of those working at height on the restoration project © Balfour Beatty
Project planning
The scale of the project became evident at the turn of the millennium when Network Rail – then Railtrack – outlined a set of criteria that stretched well beyond its previous ‘care and maintenance’ approach. The bridge operator’s principal goal was to ensure the Forth Bridge structure remained not only a symbol of engineering excellence but also a fully functioning railway crossing, as fit for purpose as the day it was built.
The project work was undertaken in three principal strands. First, Balfour Beatty had to provide safe access systems for the restoration works which involved innovative scaffolding and encapsulation techniques; second, any corroded steel had to be replaced; and third, the old paint needed to be removed by grit blasting to bare metal, followed by recoating the steelwork with a high-tech three-coat system.
In order to deliver a world-class protective treatment to the bridge, it was fundamental to create robust and often very complex access systems to provide safe working platforms at each and every corner of this unique structure. Balfour Beatty implemented comprehensive procedures and systems to ensure safe and controlled workspaces at all times. This required the construction of an encapsulation system to maintain factory-like conditions for the works to be carried out in a protected environment. At the same time, it had to prevent any contamination of the Firth of Forth by retaining the grit-blasting materials and paints within the enclosures.
The physical work began in 2002 and grew year-on-year as what was effectively a rolling contract moved from one-year to three-year banks of work. These longer-term work banks allowed equipment such as hoists, cranes and accommodation units to be bought outright, thereby generating real efficiencies in resource deployment and economies of scale. New compounds – with offices, welfare facilities, parking, laydown and storage areas – were established at both ends of the bridge, followed by additional storage facilities constructed on the base of the Queensferry and Inchgarvie cantilevers. Access routes onto and throughout the bridge, via walkways remote from the permanent way railway line, were installed to provide dedicated ‘green zone’ separation from the operational railway. In many areas, this involved adding additional elements to the main bridge framework.

Scaffolders were employed to construct and remove the complex systems © Balfour Beatty
Specialist skills
At the peak of the project, up to 400 tradesmen were employed on a project which would total over 4.5 million working hours. Personnel involved included scaffolders, blasters, coaters, material handlers, labourers, plumbers, electricians, fabricators, welders and inspectors; all overseen by a team of experienced engineers, foremen and supervisors. Specialist abseilers were used for running cables and water pipes and painting by hand the ‘touch points’ which were inaccessible when the major scaffolding assemblies were in place.
Material handlers played a key logistical role in ensuring all resources were at the right place at the right time. Significant material movements were made by barge to the storage areas constructed at the bases of the Queensferry and Inchgarvie cantilevers. Other major material movements onto the bridge were made along the railway line from the storage yards at the south side of the bridge during a ‘possession window’ in the early hours of Sunday mornings, as agreed at an early stage with Network Rail.
Between midnight and 8am, as many as 70 material handlers sprang into action utilising hand-push/pull trolleys capable of carrying two tonnes of scaffolding. These crews often moved 120 tonnes of scaffold and other supplies to strategic points on the bridge for the following week’s work schedule. This operation was further enhanced with the use of a road/rail vehicle (RRV) which could both pull rail wagons loaded with the materials required and assist the offload at the designated storage locations. The RRV also assisted the removal of materials and redundant equipment at the end of each shift.
The paramount safety demands dictated that operational railway safety trained supervisors were on duty to control these weekly events and on any other occasion when the specially-qualified workforce crossed the railway line to undertake specific tasks.
Many of the bridge team worked on this project from its inception through to completion and for many it has become a career-defining experience. These people have come to see the bridge as ‘their bridge’ and as more than just a place of employment, taking huge pride in what they have contributed to the restoration.
Scaffolding
Design and erection of safe systems of access to all areas of the complex bridge structure, whilst also maintaining full operation of the East Coast mainline rail link across the Firth of Forth, were fundamental to the restoration contract.
The existing bridge structure was not conceived with a complex maintenance regime in mind and certainly the original designers, Sir John Fowler and Sir Benjamin Baker, together with contractor Sir William Arrol, could not have envisaged the scale of scaffolding systems required to access the bridge over a century after its construction. Therefore, at the project outset, Balfour Beatty had to investigate a range of scaffolding options, in consultation with Network Rail, to develop consistently safe systems of access to the full range of scenarios posed by the bridge structure.
Exhaustive trials established that traditional tube and fitting scaffolding, supplemented with the deployment of some ‘system scaffolding’ at specific locations, provided the best option for the works. Whilst the scaffold systems were then tailor-made to suit their particular application, the design of the existing structure with the similarity in cantilever layout allowed each major scaffold to be repeated a number of times. In turn, the two suspended spans between the Fife and Inchgarvie and Inchgarvie and Queensferry cantilevers provided similar repeatability.
The next challenge was posed as the scaffolding could not be assembled and supported as in a normal construction site environment, that is to say from the bottom up and to regular geometric principles. Few of the scaffolds were founded on traditional footings but were instead connected to the structure through additional pads and support points welded to the steelwork. Scaffolds were then supported from these points and either built up, constructed from the top down or, in certain circumstances, suspended from steel wire ropes connected to the higher points of the bridge steelwork.
Lighter materials were widely introduced to improve weight distribution as on average some 4,000 tonnes of scaffolding was in use on the bridge at any one time. Extensive use of aluminium scaffold tube, both in standard linear form and unit beam configuration, together with the use of recycled plastic scaffold boards on walkways and access routes, in place of traditional timber boards, helped to ease the load.
Load modelling
At all times during the restoration process, the structural integrity of the bridge was the primary consideration as the weather-resistant plastic membrane could have acted as a ‘sail’ and created additional wind loads to the structure. Bespoke software was developed by consulting engineers Pell Frischmann to calculate the additional loading on the bridge via a program mapping a model of the bridge against the areas of encapsulated scaffolding by calibrating scaffold weight against wind loads to ensure the structure was never placed out of balance.
The white encapsulated scaffold has been one of the more widely visible features of the project, as hidden behind the safety of the scaffolding and encapsulation, the restoration process could take place. Following its erection at each section of the bridge, an initial structural inspection was conducted to assess any repairs or steel replacement required. These inspections found the Victorian steelwork to be in excellent condition, the only repairs and replacement steel required were small angles and minor ties mainly in areas above the track where generations of steam trains had exhausted steam which had, over time, corroded the steel sections.
Once the steelwork repairs were completed, the main restoration works could commence. The opaque white encapsulation membrane created suspended climatically-controlled ‘encapsulation rooms’ which optimised light levels and provided the correct environmental conditions, by use of dehumidifiers and diesel-electric heaters, to ensure a safe and secure working environment without condensation, even when external conditions were far from perfect.
Just as importantly, the residue produced by the blasting process was contained to prevent any contamination of the Firth of Forth below, the external atmosphere or the local area which is home to a number of sensitive environments, including nature reserves, breeding colonies and sites of special scientific interest.
This encapsulation solution has since been employed at Heathrow airport, Sellafield and the neighbouring Forth Road Bridge and has attracted interest internationally from companies undertaking similar projects.

View from the top of the Fife cantilever looking south showing scaffolding and encapsulation © John Andrew
Blasting and Painting
One of the most extreme jobs of the restoration process was undertaken by blasters wearing protective clothing and helmets incorporating a head set with an umbilical cord containing an air line, communication link and power line for tools and lights.
The grit used in the blasting process was a byproduct of the copper industry – very hard, but inert. Stored in bulk in the main storage areas at the base of the bridge cantilevers, it was then mixed with air provided by large banks of compressors sited at the north and south compounds. The blasters drew the grit from huge reservoirs at up to 120 psi and fired it onto the structure at up to 200 mph in an operation one experienced and trained worker described as “like spending the day arm-wrestling”. Within seconds, multiple layers of paint and rust were removed to get to the bare steelwork.
Industrial vacuum extractor units then removed the grit and other debris at a rate of up to 20 tonnes of material per hour. By modifying internal workings such as the vacuum governors, the extractor’s ‘pull’ capability was expanded from a standard 200 to 500 metres, essential when work areas were often a considerable distance from the collection points sited at the base of each cantilever. From there, waste was bagged and moved by barge back to land and then on to recycling centres and licensed disposal sites. Here the grit was treated, paint and rust removed for disposal in approved facilities, with the cleansed grit available for reuse.
Finally came the paint, developed specifically for use on the Forth Bridge by Leighs Paints of Bolton, a 150-year-old family business which recently became part of global US coatings specialist Sherwin Williams. The three-part coating system originated from the North Sea oil industry where it had been used to protect offshore structures in severe marine environments. Independent trials specific to its use on the bridge, conducted by Network Rail, verified that the topcoat will last for at least 20 years.
The paint system began with a holding primer, containing zinc phosphate to boost its anti-corrosive property, thinly applied at 25-50 microns to the steel by spray techniques.
The area was then cleaned down again before a ‘stripe coat’ of high-build epoxy glass flake paint was applied by hand to the 6,500,000 rivets and sharp edges of angles and plates to ensure that the specified thickness was achieved.
The glass flake element of the epoxy paint is micronised to give an even surface as the flakesorientate themselves parallel to the surface to give barrier protection and physical reinforcement. The same coating was then progressively sprayed onto the entire 255,000 m² surface to a minimum thickness of 400 microns when cured, having measured a film thickness of 500 microns when wet before solvents are lost as it dries and cures.
Finally the trademark topcoat, in the form of 50 microns of ‘Forth Bridge Red’ paint, was applied – mixed to match the original red oxide colour used in 1890. The epoxy paint applied in the first two coats does not provide good light resistance, so the final coat was of acrylic urethane, giving good colour stability and gloss retention along with an indefinitely recoatable surface to keep preparation to a minimum for future maintenance works.
Following inspection and approval of each completed section, the task of dismantling and removing all the scaffolding, encapsulation and support services was systematically undertaken and the rolling restoration programme moved on to the next area.
An End to Continuous Painting
This pioneering project has used some 240,000 litres of paint to completely recoat the bridge in a single operation for the first time since its construction. Train passengers and the many visitors to the shores of the Forth will now enjoy uninterrupted views of this most photographed of bridges. It is important that the bridge looks its best now that it is under consideration for UNESCO World Heritage site status. Whatever the outcome, the use of modern technology now protects this iconic feat of Victorian engineering and much-admired Scottish landmark as the Forth Bridge continues to serve into the 21st century.
Pell Frischmann won the Structural Heritage Prize at the Structural Awards 2014 for their work on finding a solution to the endless repainting of the bridge http://www.istructe.org/structuralawards/2014/the-shortlist/structural-heritage/forth-rail-bridge
Keep up-to-date with Ingenia for free
SubscribeOther content from Ingenia
Quick read
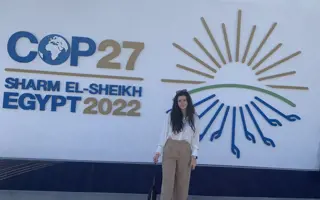
- Environment & sustainability
- Opinion
A young engineer’s perspective on the good, the bad and the ugly of COP27
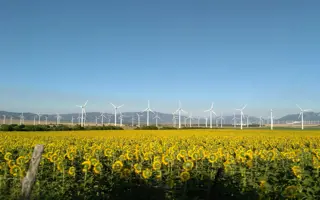
- Environment & sustainability
- Issue 95
How do we pay for net zero technologies?
Quick read
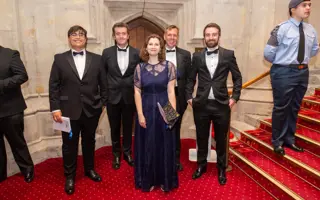
- Transport
- Mechanical
- How I got here
Electrifying trains and STEMAZING outreach
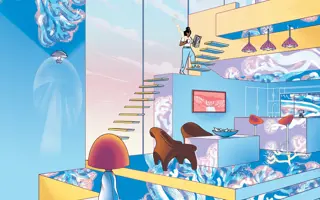
- Civil & structural
- Environment & sustainability
- Issue 95