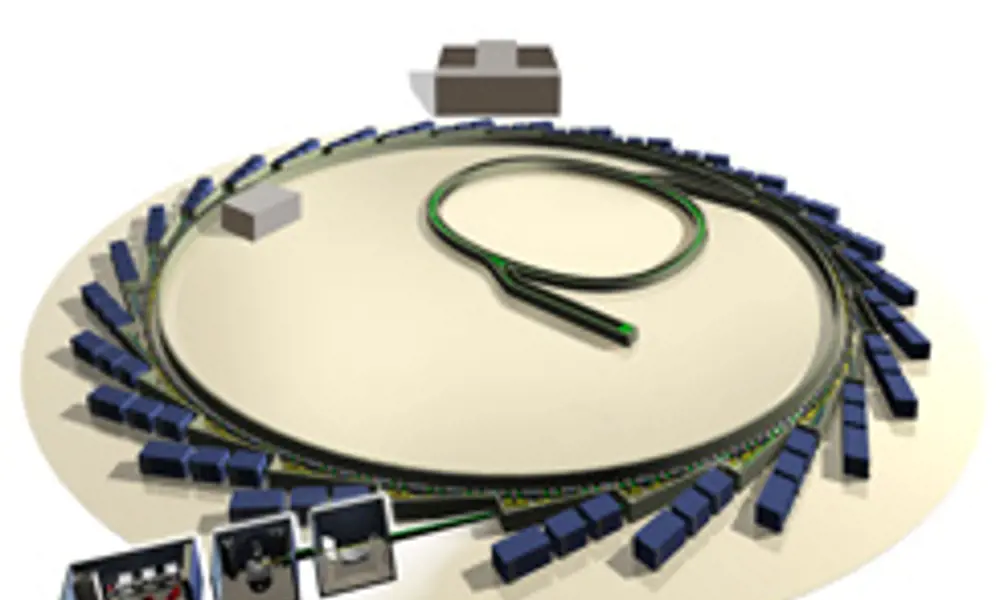
Research Powerhouse
Illustration of the synchrotron layout © Diamond Light Source Ltd
The Diamond Synchrotron under construction at Harwell in Oxfordshire is the largest science facility to be built in the UK for 30 years. The photon beamlines that are part of the synchrotron will enable research opportunities for thousands of scientists and engineers. Jim Kay, Head of Engineering for Diamond Light Source Ltd, writes about overcoming the engineering challenges to make the science possible.
The Diamond Synchrotron can be described as a series of ‘super microscopes’, housed in a striking doughnut-shaped building over three quarters of a kilometre in circumference. Construction of the synchrotron began in March 2003 and its doors will open to researchers from both the academic and industrial communities in January 2007.
This huge construction and engineering project was jointly funded by UK Government (86%) through the Council for the Central Laboratory of the Research Councils (CCLRC) and the biomedical charity The Wellcome Trust (14%). Phase I funding of £260 million includes Diamond’s buildings, the machine and the first seven experimental stations/beamlines. An additional £120 million Phase II funding has also been allocated for 15 further beamlines, which will be constructed between 2007 and 2011.
Diamonds are for energy
A synchrotron uses electrons to generate extremely powerful light in the form of X-rays, infrared and ultra-violet. This light, also known as synchrotron radiation, can then be harnessed to enable scientists to study a wide range of biological,material and chemical samples right down to molecular and atomic level. Diamond will be a third generation facility and a medium energy source, with an electron beam energy of three giga electron volts (three thousand million volts).
Diamond has been designed using the latest technology, ensuring that when it becomes operational it will be one of the brightest light sources in the world. Academic and industrial researchers from all areas of science will be able to benefit from Diamond, making it a powerhouse of new ideas and scientific breakthroughs.
Diamond and industry
The majority of Diamond’s users will be academic researchers with long-term fundamental research needs. However, industrial researchers from a wide range of sectors (see figure 1) will be encouraged to use the facility. Industrialists need to know how components are affected by production processes and treatments, and how products and systems cope when exposed to strain, ageing and fatigue.
Dr Alexander Korsunsky at the Department of Engineering Science at the University of Oxford has been helping Rolls- Royce to develop innovative techniques using synchrotron light. In a number of research and development projects conducted by Rolls-Royce, heat treatment procedures were sought that would minimise the residual stress within combustion system components.
In a collaborative experiment with Dr Korsunsky’s group, conducted in France at the European Synchrotron Radiation Facility (ESRF) using high energy X-ray diffraction, a family of components were studied that had undergone different heat treatment procedures. As a result the researchers found that a particular procedure resulted in the optimal reduction in residual stress, giving Rolls-Royce the processing capability that they set out to establish.
Building on experience
The UK’s knowledge in this field is second to none, having built the world’s first dedicated synchrotron at the Daresbury Laboratory in Cheshire back in 1980. A report to Government in 1993,The Woolfson Report, paved the way for research and development to commence on a new synchrotron facility.
The electron beam the synchrotron produces is measured in micrometres (40 micrometres equal the diameter of a human hair) and is just 290 micrometres wide and 15 micrometres high. It is no surprise that the stability of the building, the atmosphere, and the machine components are all critical to the efficient and effective operations of the synchrotron. Consider also that scientists’ samples are positioned some 50 metres from the storage ring where the synchrotron radiation is initially produced, and the need for a highly stable environment becomes even more apparent.
The first challenge in the achievement of stability was the geology of the land that Diamond is built on. In this particular part of Oxfordshire, around the Chilton Hills, the soil is mainly chalk. Each year the water table varies between 4 and 12 metres under the surface. This variation of 8 metres in structureless chalk formation causes a shrink swell behaviour, which varies the ground surface by 1cm. This movement would be disastrous for Diamond’s performance, so consequently the floor slab was constructed on a piled foundation.
To achieve the stability required, it was necessary to go below the water table and contact a stratum of solid chalk at a depth at which the shrink swell behaviour does not occur. An extensive exercise of analysis was carried out to calculate the optimum pile spacing and slab thickness. 1,500 piles were cast 15 metres down into the chalk soil at 3 metre spacings. A collapsible cardboard support was laid under the floor slab, which is 600mm thick under the experimental hall and 800mm thick under the storage ring. Water was then injected to collapse the cardboard and create a 50mm void,which means that the shrink swell can go on year after year without affecting the performance of the floor slab.
The floor surface performance is analysed in terms of both deflections – the rigidity of the floor slab when loads are imposed or when traffic passes – and settlement,which relates to the longer term settlement of the building. Design brief targets for deflections were that displacement 2 metres away from a 500kg load should be no greater than 1 micrometre. In addition, the maximum vibration acceptable at the beamline is 1 micrometre peak to peak. With regard to long term settlement, the maximum differential movement of the Storage Ring, Booster and Linac floor is 100 micrometres (250 micrometres for the Experimental floor) over 10 metres per year.
Services stability
Extremely tight controls surround the building’s services because the performance of the synchrotron can be compromised as a result of seemingly small things like noise vibrations and minor temperature variations. Temperature control is particularly critical because many of Diamond’s machine components are made from steel, one metre of which will expand by 17 micrometres for every °C rise in temperature.
The air conditioning strategy has been to concentrate on achieving 22°C ± 1°C in the four metre zone nearest to floor level, despite the fact that the building is 15 metres tall. This zone houses all the sensitive operating equipment. The storage ring tunnel is divided into ten service sectors, and each is fed by a dedicated air handling unit, conditioning and re-circulating air drawn from the zone. During commissioning the tunnels that house the linear accelerator, booster synchrotron and storage ring are kept at 22°C ± 0.5°C and the temperature control will improve further when Diamond is fully operational. The sections of each experimental station – where the synchrotron light is focused and directed on the samples – can be controlled to an even tighter 22°C ± 0.1°C.
A circulating water cooling system is also used to absorb unwanted radiation and protect metal vacuum vessels from melting. The temperature of the circulating water and the air temperature are closely matched to further improve the machine’s stability.
Built to task
Left to their own devices, electrons would take a straight path, lose no energy, and emit no synchrotron light. Magnets are the key to guiding the electrons so that they bend and emit synchrotron light in the form of X-rays, infra-red and ultra-violet. Diamond has 564 magnets, which bend and focus the beam. Each magnet has its own power supply for individual tuning: a feature that is unique to Diamond.
The electrical engineers at Diamond have faced a great challenge to ensure the magnets and instrumentation receive no electrical interference, going to great lengths to ensure electro magnetic compatibility (EMC). This has involved extensive use of segregation, separating power from analogue signals and digital signals. No variable speed drives have been used, so that noise on to mains can be avoided. An extensive range of filters have been installed to keep the power supply both clean and stable.
The power supply stability has to be better than 1 part in 100,000 – not a trivial undertaking in a building of this size.
Control and Instrumentation Areas (CIAs) are used to house Diamond’s 800 electrical control racks. The CIAs provide a secure, dust free, temperature controlled environment. These areas are important because dust will affect the life of the electronics, and temperature variations will affect the magnet power supply output which in turn affects the beam stability.
Innovative mechanical engineering plays a key role in Diamond’s main storage ring; a 561.6 metre long vacuum ring where the electron beam produces the synchrotron light.
The storage ring contains 72 girders. Each girder has a selection of magnets and a portion of the vacuum vessel mounted on it. Each girder is remotely adjustable via a motorised positioning system that gives micrometre resolution. When fully developed,Diamond can measure the error signals relating to the electron beam position. This will mean the girders can be automatically adjusted in five motorised axes to reduce the errors.
The 72 girders are split into groups of three, and each group is known as a cell. The various cells can be individually tuned so that they optimise the synchrotron light output for each specific experimental station on Diamond.
New generation
Diamond is what is known as a third generation light source. It is the special magnet systems, known as insertion devices, that make it third generation. Insertion devices are at the heart of every third generation light source. They consist of about 300 small permanent magnets that cause the electron beam to wiggle along the 300 North/South poles. This wiggling provides more intense and coherent X-rays.
The energy output of the insertion devices can be varied by changing the gap between the two magnet arrays. However, the closing force increases dramatically when the magnet arrays come together, to such an extent that a 5mm gap on a 2 metre long array of magnets gives a closing force of 2 tonnes. A stiff support structure is required because the magnets need to be kept flat to within 5 micrometres to ensure the stability of the electron beam and the optimum output of synchrotron radiation.
Each experimental station has a bespoke insertion device, with its own unique magnet settings. A sophisticated control system is required to adjust the gap of the insertion device magnets while maintaining the accuracy. The control system is also vital for a range of other adjustments on the beamlines, including achieving the correct angle on the monochromator (a spectrometer capable of selecting a single wavelength), re-setting the mirrors that focus the light, and manipulating the experimental samples.
One of the current challenges on the beamlines is to achieve a ‘micro-focus’. This is the focusing of the synchrotron radiation down to one thousandth of a millimetre dimensions. The next challenge is to achieve ‘nanofocus’, which is 1000,000th of a millimetre. This will require active feedback systems to control optical elements to compensate for the tiniest of movements.
The front ends of Diamond contain cooled radiation absorbers and also the heavy shutters that open and close each beamline to the synchrotron radiation. Before the X-ray beam leaves the storage ring and travels down to the various beamlines, it needs to be measured in position and angle. The beam position monitors are installed in the front ends and are set 5 metres apart. These front ends help deliver the stable operation of each beamline and give adjustment information to the beamline control system.
Designed for excellence
The quality of the science that is achieved at Diamond over the next 30 years will largely depend on the scientific researchers that come to use the facility. During the design phase, the Diamond team were conscious of the human aspects of working in such a large building and the fact that users could be located up to half a kilometre away from the office building,Diamond House. In addition to the synchrotron and beamlines, the building houses 11/2km of laboratory and office space around the edge on the ground and first floors. This means that university or company research teams will have facilities to prepare their samples on site, carry out their experiments on the beamlines and also undertake post experimental processing of their data. There are also 12 entrance points, each with meeting rooms and coffee areas nearby. 360º parking around the building will minimise traffic journeys.
To encourage scientists from similar disciplines to mix with each other, share ideas and collaborate, the beamlines that serve similar scientific areas are grouped into a ‘village’ structure. The villages include Engineering and Environmental Science, Materials,Macromolecular Crystallography, Soft Condensed Matter, Spectroscopy, and Surfaces and Interfaces.
Future timelines
Diamond’s engineering team are approaching the end of the design and construction of the seven beamlines that will make up Phase I of the facility. In October 2004, Lord Sainsbury announced funding for the 15 Phase II beamlines and these will require engineering effort between 2007 and 2011. Beyond this,Diamond has a capacity for up to 40 beamlines so Phase III funding will be sought to ensure that the facility is used to its full potential.
There is also a huge amount of scope for making use of technological developments; the engineering team will be proactively looking for opportunities to improve the performance of both the machine and the beamlines as new technology and scientific initiatives allow.
For further information on Diamond Light Source see www.diamond.ac.uk
Biography – Jim Kay
Jim studied Mechanical Engineering at Leeds University and became a Chartered Engineer and Member of the Institution of Mechanical Engineers in 1992. He joined the Daresbury Laboratory in 1990 as a Senior Engineer in experimental equipment for the Nuclear Structure Facility (NSF). After the NSF closed in 1993, Jim worked on a range of new projects at Daresbury, including the designs for Diamond. In 1998 Jim was appointed Engineering Group Leader of the synchrotron at Daresbury,working full time on the design case for Diamond. In October 2002 he became Head of Engineering for Diamond Light Source Ltd.
Keep up-to-date with Ingenia for free
SubscribeOther content from Ingenia
Quick read
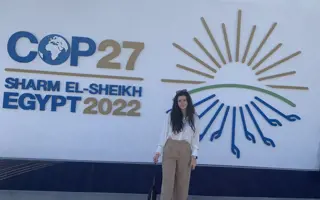
- Environment & sustainability
- Opinion
A young engineer’s perspective on the good, the bad and the ugly of COP27
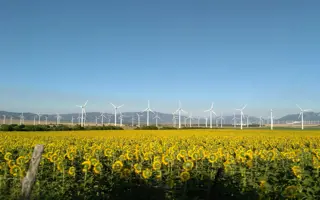
- Environment & sustainability
- Issue 95
How do we pay for net zero technologies?
Quick read
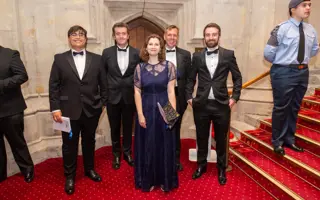
- Transport
- Mechanical
- How I got here
Electrifying trains and STEMAZING outreach
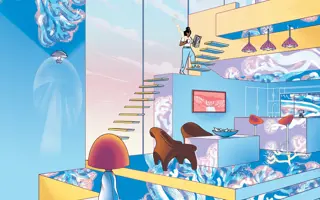
- Civil & structural
- Environment & sustainability
- Issue 95