
Raising and conserving the Mary Rose
On 19 July 1545, an army sent by Francis I, King of France, tried to enter Portsmouth Harbour to land troops and go into battle with the English. As skirmishes began, a strong wind picked up enabling the 34-year-old English warship Mary Rose to gather speed and confront the French galleys.
What happened next, and why, has been the subject of much conjecture; a mix of poor communication, strong winds and overloading did not help the Mary Rose. What is certain is that the 600 tonne warship suddenly heeled over to its starboard side where water rushed into its open gunports and it quickly sank.
The warship sank 15 metres and lodged itself at a 60-degree angle to starboard on the soft clay of the seabed. The first attempt to salvage it was attempted a few days later, but the tried method of lifting wrecks from shallow waters did not work as the cables could not be passed under the hull and only some rigging and guns were brought to the surface. Apart from cursory excavations by pioneer divers in the 1830s, the hull laid untouched for over 400 years.
Apart from cursory excavations by pioneer divers in the 1830s, the hull laid untouched for over 400 years
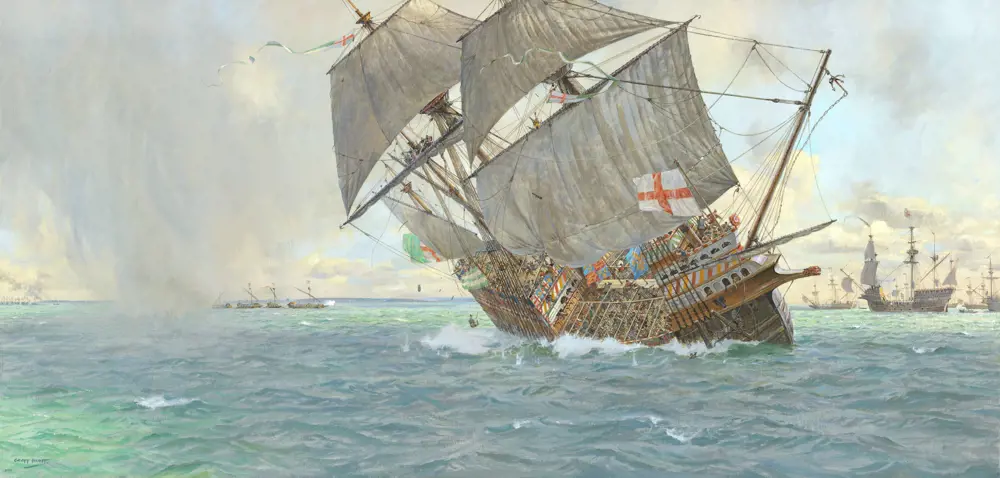
When Henry VIII’s flagship the Mary Rose heeled over with water rushing into the lower open gunports many men were trapped by the antiboarding netting on the upper deck, which was designed to stop raiders getting on. It is estimated that more than 400 men drowned that day © Geoff Hunt (artist)/Mary Rose Trust
Archaeological excavation
The destructive activity of fungi, bacteria and wood-boring crustacians and molluscs began to break down the ship’s structure. After exposed parts of the ship had collapsed, the site was naturally covered by silts and eventually became the same level as the seabed. A hard, shelly layer of sediment sealed the site and helped to prevent microorganisms from further damaging the ship’s wooden frame and locked in its remaining contents, as well as hiding the vessel from sight.
The search for, and discovery of, the Mary Rose was driven by a local historian and writer Alexander McKee, who later became Director of Excavations. From 1965 onwards, in conjunction with the local branches of the British Sub-Aqua Club, he set up ‘Project Solent Ships’ to look for wrecks in the Solent. For the first time in the UK, sub-bottom profiling, using sonar scans to identify and characterise layers of sediment or rock under the seafloor, was carried out by his team to look for archeological sites.
In the late 1960s, a combination of dual-channel sidescan sonar, which is a sonar device that emits conical or fan-shaped pulses toward the seafloor and records the acoustic reflections, and sub-bottom profiling revealed an anomaly in an area of the seafloor thought to be the resting place of the Mary Rose. The monitoring equipment sent down sound pulses to reflect or penetrate the seafloor. Those that did penetrate were either reflected or refracted as they passed through different layers of sediment and these signals were gathered by the surface vessel. A second geophysical survey using two pingers operating at frequencies of 5 and 12 kilohertz discovered four more anomalies. This was sufficient enough to point the search team to the vessel’s resting place.
A team of volunteer divers explored the area. Using water jets and airlifts, they began to excavate and were encouraged by the appearance of stray pieces of timber. The breakthrough came in May 1971 when a diver found three of the port frames of the Mary Rose.
Between 1979 and 1982, 28,000 dives brought up 19,000 artefacts, including cannons, gun carriages, wooden tankards and even nit combs. The objects went into ‘passive’ storage to stop any deterioration before conservation could begin
The silt had preserved the buried items and divers began to bring a veritable Tudor treasure trove to the surface. Between 1979 and 1982, 28,000 dives brought up 19,000 artefacts, including cannons, gun carriages, wooden tankards and even nit combs. The objects went into ‘passive’ storage to stop any deterioration before conservation could begin.
The dives had revealed a significant part of the hull, which was shown to be worth saving. There was plenty of publicity around the sunken ship with the world’s first live underwater broadcast taking place on the wreck site. This, and further funding raised under the patronage of HRH The Prince of Wales, meant that the project attracted enough finance and expertise to attempt to raise the hull.
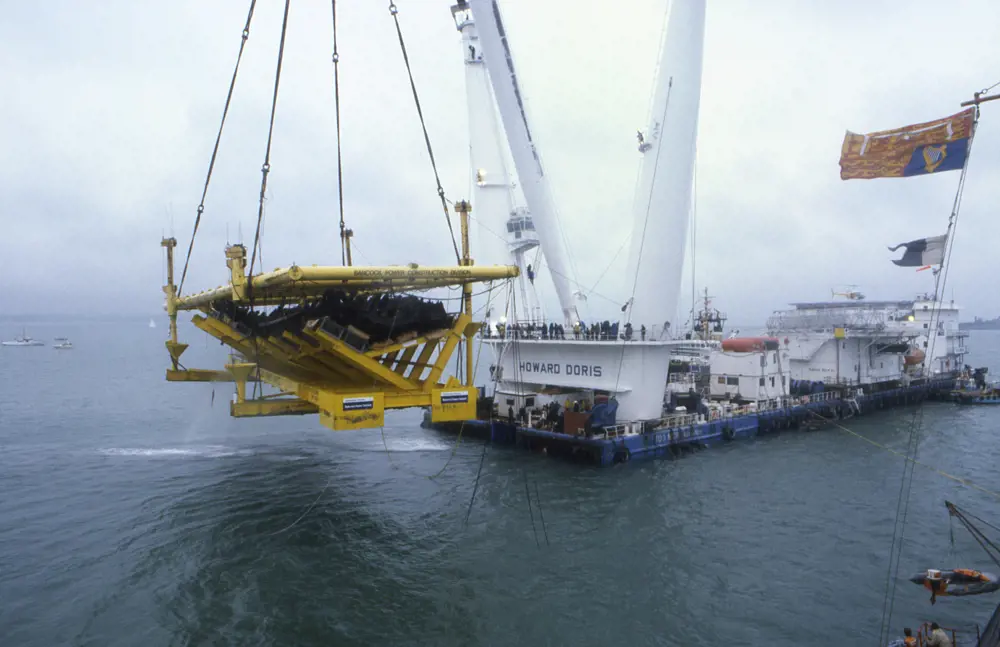
The crane lifting the Mary Rose hull out of the Solent, lying on its yellow cradle, is an image that millions of TV viewers retain from the memorable morning of Monday 11 October 1982 © Christopher Dobbs/Mary Rose Trust
The link to the Swedish warship Vasa and bringing the Mary Rose back to land
There were few precedents for raising centuries-old sunken ships onto dry land. The most relevant was the Swedish 17th century warship Vasa, which had been lifted to the surface of Stockholm harbour 20 years before. There is a strong link between the teams who work on the Mary Rose and the Vasa, who continue to contact each other at all levels, be it for conservation, research or even museum activities.
The Vasa had been lifted using cable slings passed underneath the hull, which were then attached to two pontoons above and gradually raised. The Vasa had rested upright on the sea bed and had most of its hull intact. However, this was not the case with the Mary Rose and so a new method had to be developed.
In 1979, a meeting of salvage consultants and contractors, structural engineers and naval architects agreed that it should be possible to reinforce and recover the hull. Although the remaining hull was an open shell, rather than a complete cross section with transverse strength, a plan was drawn up [ see Raising the Mary Rose].
an estimated 60 million people watched the raising of the hull on television
On 11 October 1982, media gathered from all over the world and an estimated 60 million people watched the raising of the hull on television. Above the water, a giant floating crane called Tog Mor took the strain and transferred the hull frame onto the cradle as divers monitored the process on the seabed. The crane winched the cradle very slowly to the surface, where the hull encountered air again for the first time in 437 years.
There was an initial scare when the filming showed one corner of the frame slipping toward the hull due to a mistakenly applied strop and some securing pins. However, shortly after, the crane placed the yellow frame on a barge and took it to Portsmouth Historic Dockyard’s dry dock number three, close to where Henry VIII had the warship built nearly 500 years before.
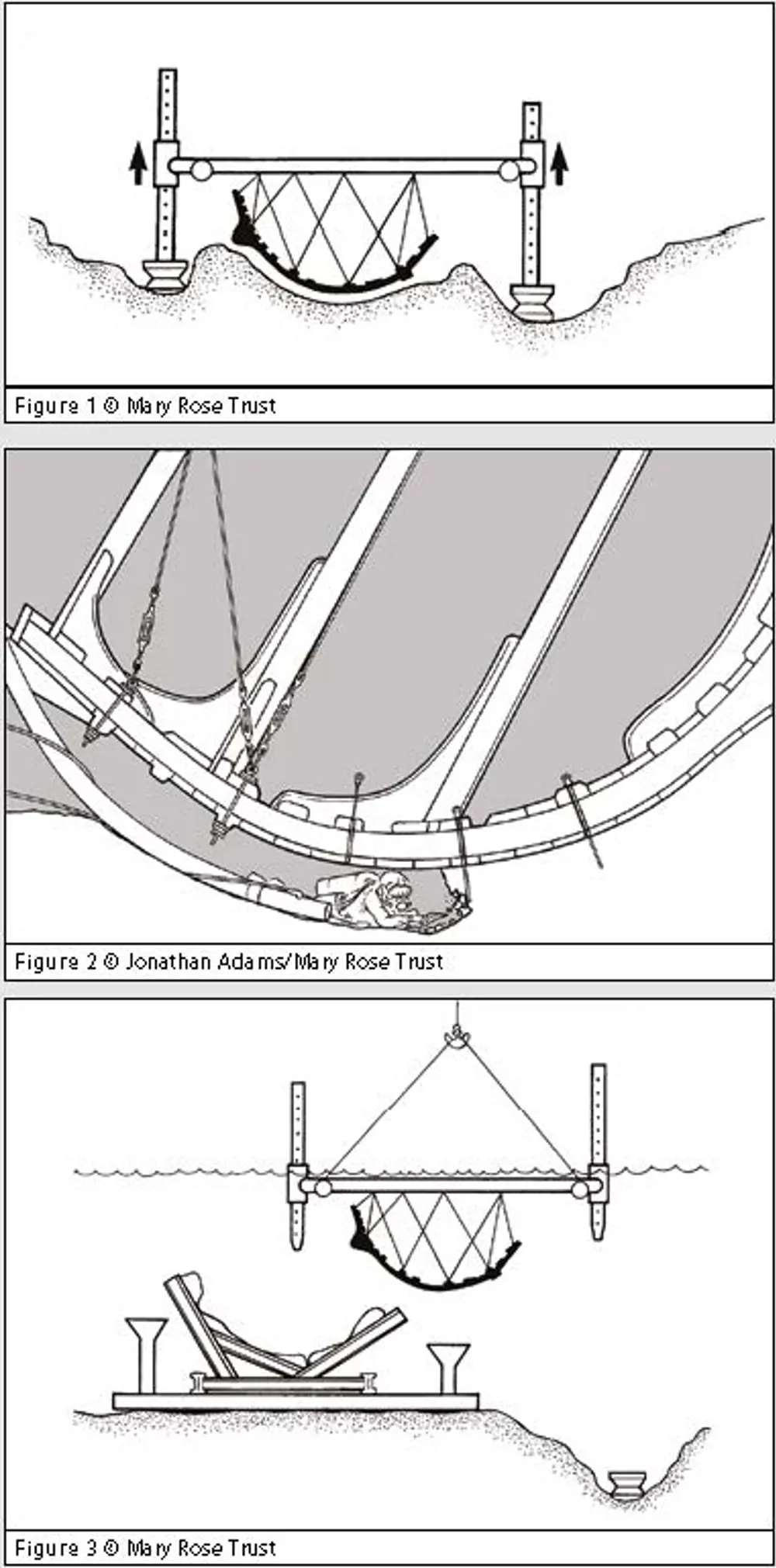
Raising the Mary Rose
The first step of the plan to lift the Mary Rose tackled the problem of ‘bottom suction’, whereby the ship was embedded within the silt and clay of the seabed. This was achieved using 12 hydraulic jacks raising a lifting frame slowly [Figure 1], over a period of several days, up its four legs.
A network of bolts and internal lifting wires was created, rather than the traditional salvage method of using external strops. This spread the loading of the lift across the entire structure of the hull, avoiding the need for heavy stiffening inside the hull. Each of the 67 main lifting points had a bolt passed through the hull that, when tightened down onto the internal and external spreader plates, acted as clamps to hold the hull firmly together. The salvage diving team fitted a further 103 bolts to act as additional clamps.
Once each section of the hull was wired up to the lifting frame, the hull was undercut to find the next row of backplate positions. This meant that the divers always worked under areas of the hull that were held up from above. The divers carried out this work using a combination of a water jet to cut through the hard clay with a 150-milliimetre airlift to extract the spoil [Figure 2]. It was too dark and murky to see anything, so the team placed steel rods in the bolt holes that helped the divers to locate the next area by feel.
The team carried out this work during 1982, with an October deadline for the lift. At that point, the newly exposed hull would be at the mercy of winter tides and currents that would be archaeologically damaging. Nevertheless, the last two months represented diving marathons for the professional divers, staff and Royal Engineers working to the underwater salvage timetable.
Babcock Power Construction commissioned a lifting frame and a cradle to place the Mary Rose into. Sub-contractor Barnshaws Section Benders used section drawings made from the archaeological surveys to produce beams that formed the cradle that would hold the 35-metre-long, 14-metre-high hull of the warship. The cradle, lined with air bags, dropped down beside the hull a few days before the lifting operation began.
Once the hull was hanging freely from the lifting frame, clear of the sea bed, it was transferred underwater to the cradle [Figure 3]. This supported the hull, which was sitting on inflated air bags, both below and above and meant that it was ready to lift.
Persevering the hull
For the first few weeks of ‘passive holding’, a pumping system kept the timber work of the Mary Rose soaked, enabling thousands of litres of seawater a minute to pass over it. The ship’s conservators then switched this to freshwater and a chilling system held the water at 2°C to discourage microorganisms. They then placed a temporary building around the hull, which was to stay in place for the next 30 years to enable both public viewing and a controlled environment.
Left exposed to air to dry out, the ship’s wooden structure would have collapsed and shrunk as the water evaporated from its cellular structure. The freshwater soaking continued for a decade while the Mary Rose team worked with experts around the world to decide on the best method for conserving the hull. The team sent sample parts from the ship for testing in France by passing cold dry nitrogen over them and to Holland for controlled air-drying.
The Mary Rose team settled on using polyethylene glycol (PEG) to replace the water in the cellular structure of the wood. In the 1980s, the team that raised the Swedish warship Vasa sprayed this solution on the ship for 17 years
The Mary Rose team settled on using polyethylene glycol (PEG) to replace the water in the cellular structure of the wood. In the 1980s, the team that raised the Swedish warship Vasa sprayed this solution on the ship for 17 years, and the team that preserved the Bremen cog in Germany, a late medieval merchant ship, immersed the vessel in a giant tank of the solution for 18 years.
From 1994 to 2006, a low-grade polymer with a short chain length was used, which goes further into the wood and is liquid at room temperature. Then from 2006 to 2013, a higher-concentrate PEG, which is a solid at room temperature, was used that needed to be heated to approximately 28°C to form a solution in water. The chamber that contained the hull for all these years was dubbed ‘the hot box’, even more apt when, in the final few months, the temperature reached 30°C and the humidity was nearly 100%.
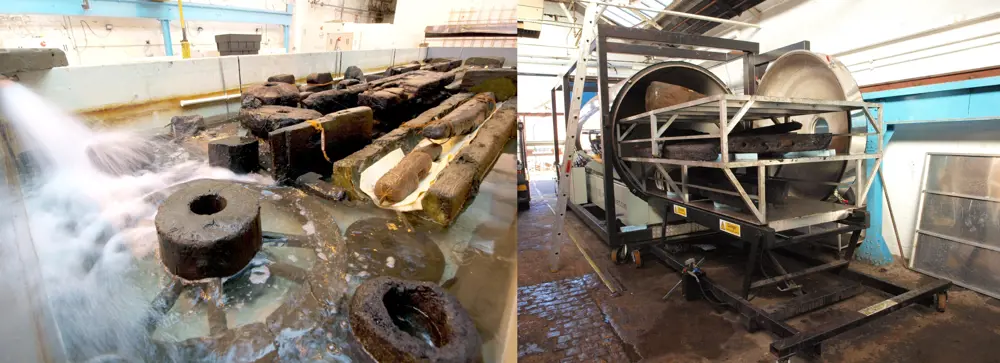
The Mary Rose team soaks the wooden artefacts in PEG for a few years and then, because they still have water in them, freeze-dry them. At six metres long, the Mary Rose freeze dryer (right) is the largest in the country. The chamber freezes the items and any remaining water turns to ice. A vacuum then applies pressure that causes the ice to sublimate and turn straight from solid to gas. Because the water comes out very quickly, it means that the dimensional changes are minimal and the process is relatively quick. The gun carriages, for example, only took three months © Mary Rose Trust
As well as stabilising the hull with PEG, further measures have protected the wood. One of the major enemies of sunken wrecks is the corrosive effects of iron. The Vasa warship has suffered greatly from this as the bolts, nails and metal fittings corrode, leaving iron deposits. It was also discovered that PEG corrodes iron and the PEG spray treatment can carry the iron deeper into the timber where it can catalyse the oxidation of sulphur, forming sulphuric acid.
The timbers on the Mary Rose hull were fortunately held together using trenails, hard wooden pegs. However, there was still some iron in the wood probably caused by nearby artefacts and seawater, and the bolts used to salvage the hull needed to be replaced. Titanium bolts replaced the steel ones before the PEG spraying and titanium was used for the modern support beams that hold up the decks to this day.
Titanium was used because it is strong, light and inert, so would not corrode. A support system was designed whereby titanium beams ran along the main and upper decks. Titanium props were fitted in between as they are adjustable and give flexibility as the ship moves over time. Before the deck timbers were put back in place, the hull had to be turned into an upright position in a major engineering operation performed in 1985. It is not perfectly upright in relation to its keel as the structure is more comfortable leaning back at an angle of three to five degrees.
Pegging archaeological wood
⚓ How PEG works to conserve wood
There are different grades of PEG according to how many repeated units of it (CH₂-O-CH₂) make up the polymer chain. PEG works by replacing water in cell cavities and partly by bonding onto hydroxyl groups in decayed cellulose fibres. PEG embeds wood in a stable matrix.
Different concentrations of PEG were tried for differing amounts of time to see what dimensional change there was to the warship’s wood. These tests were also done to see what the end result would look like, as a heavy dose leaves the wood looking black and plastic-like.
The Mary Rose Trust ethos has always been to conserve rather than restore and so went for a concentration that stabilised the hull with minimal change to its appearance.
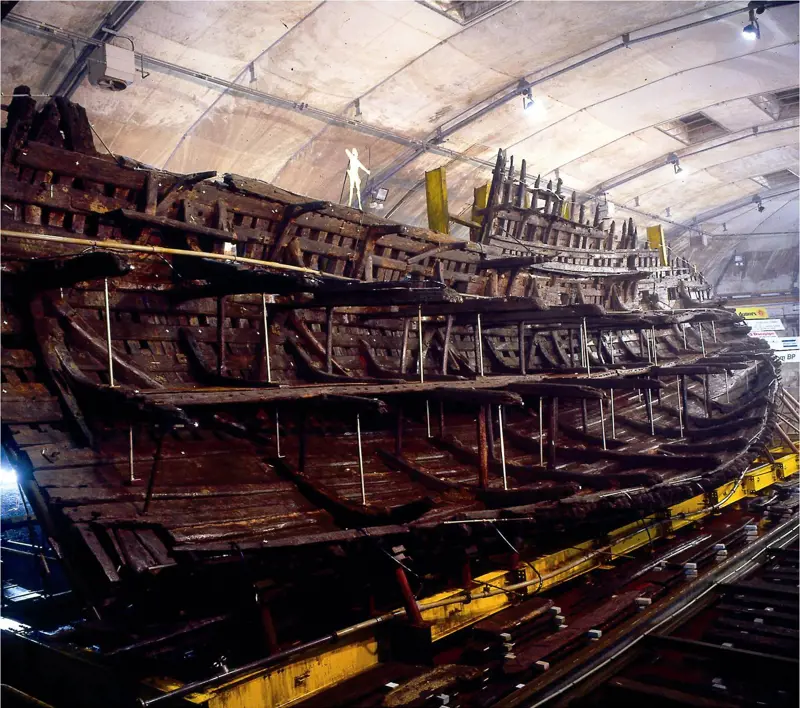
Sprays cover the Mary Rose hull with water in 1991. The hull is still on the same yellow cradle that lifted it out of the sea in 1982. It sits on the barge deck, which was cut away when it arrived at the dry dock, and rests on brick piles at a slight angle so that water and PEG solutions could drain away © Mary Rose Trust
Building a museum
In 2013, when the correct level of PEG was reached, as determined by gel permeatation chromatography, the decision was made to turn off the sprays within the hot box and to start drying out the Mary Rose. A few years before, thanks to fundraising efforts and a generous allocation of Heritage Lottery funds, the Trust had started to prepare a new museum to house the hull and display its artefacts.
Since 2009, building work had been going on around the hot box and a new building had been devised from the inside out. It all developed from the hull sitting in the dry dock contained within the hot box. The hot box would switch from 28–30°C for PEG application to cooler 18–20°C for air-drying in 2013 and then the hot box would be taken down altogether a few years after the museum was opened. The logistics for maintaining the stable pegging and drying of the hull were complex [see Controlling air flows].
The end result was a building with a low elliptical shape that was partly designed to minimise the space around the hull and make it easier to maintain the temperature and humidity needed
The end result was a building with a low elliptical shape that was partly designed to minimise the space around the hull and make it easier to maintain the temperature and humidity needed. The wooden-clad exterior was stained black as a nod to traditional boat sheds, and the interiors were decked out to reflect the dark conditions that the crew of the Mary Rose had to work in.
The museum opened in 2013 and the following year was named Building Magazine Project of the Year. At the end of 2015, the ship was sufficiently dry to take out the drying ducts and at the same time the hot box wall around the ship was taken down, expanding the volume around the ship from 9,000 m² (square metres) to 12,000 m². Air locks were fitted between the gallery and the ship hall to help prevent too rapid changes of humidity and temperature when visitors circulate. Glazing was installed in 2016 to allow unobstructed viewing for the first time, instead of peering through narrow windows in the wall. There are now nine galleries that visitors can view situated on three floor levels. Most of the artefacts on display are arranged opposite the corresponding decks of the hull where they would have been found or used.
Controlling air flows
💨 Using computational fluid dynamics to overcome the challenge of drying the Mary Rose
Consulting engineers, Ramboll UK and K8T, used computer fluid dynamics (CFD) to work out the placing of ducts and extractor fans for when the Mary Rose switched from PEG application to air-drying in 2013. The challenge with the drying process was to get each part of the wood to receive the same amount of air at equal velocity, relative humidity and temperature as warping and cracking would occur more rapidly if they did not. A laser scan of the ship was done, which was then used in a CFD model that took in the volume of the ship hall and then fed in the inlets and proposed pathways of the drying equipment.
Repetitions of the model were done that determined air velocities, dwell times and the shear stresses caused by air movement. Using these models, it was determined that the minimum volume of air supply needed was 25 m³ (cubic metres) per second and three massive air-handling units (AHUs) each supplying 8.3 m³ per second of air were placed in the dry dock with ducts feeding the air into the ship hall and around the hull.
Further stress-testing of the model identified which nooks and crannies of the ship would be missing out on air and decided the positioning of the two 1.2-metre-diameter ducts that ran the length of the hull, which in turn dropped down to supply 14 smaller ducts threaded around the beams. The designers were aiming to supply conditioned air with a maximum velocity of 0.25 m³ per second adjacent to the hull. In order to maximise the AHU’s air dehumidification, the chilled air was supplied at 2°C with the ability to rise to 6°C for the main part of the building.
To read more about the CFD modelling, see the Chartered Institution of Building Services Engineers Journal article Home and dry (September 2013).
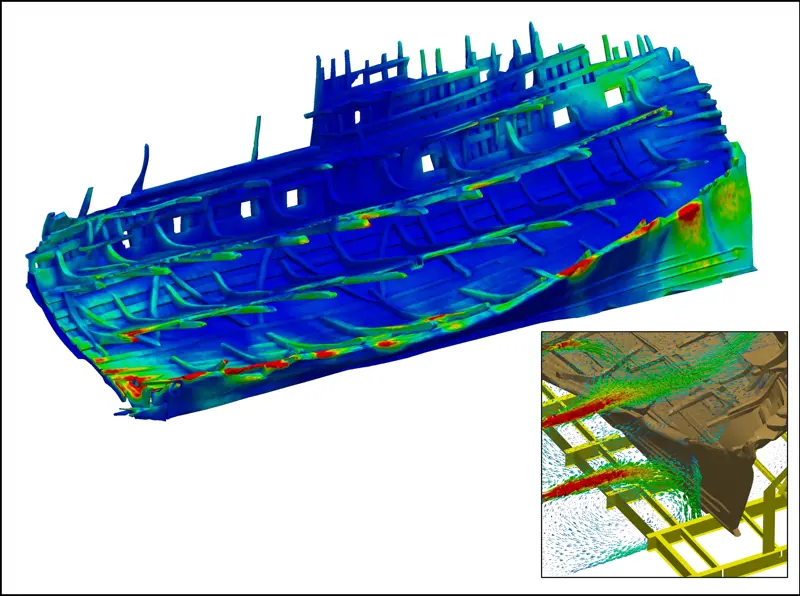
Models of the shear stress (above) and airflow velocity (below) on the inside of the hull © K8T Limited
What next?
There have been plenty of firsts achieved with the raising and conserving of the Mary Rose and there are more advances that will be made in the coming years. Osteoarchaeology, the study of human remains, has made great advances thanks to the discovery of the warship, as has archaeogenetics, which is the study of ancient DNA – the likely birthplaces of the ship’s crew was determined by what was found in the enamel of their teeth.
Among the ongoing innovative projects that Dr Eleanor Schofield, Mary Rose Trust’s Head of Conservation and Collections Care, is involved with now, is one monitoring the evolution of sulphur and iron in the warship as it dries. Her team has taken core samples measuring approximately five millimetres in diameter and 200 millimetres long to the Diamond Light Source synchrotron facility at Harwell in Oxfordshire since 2012. By accelerating electrons to near light-speed, Diamond generates brilliant beams of light from infrared to X-rays, the latter of which the team has used to determine how sulphur and iron compounds evolve in the Mary Rose’s wood when exposed to air, and the associated threat level of destructive acid formation. Gradually, the researchers have been able to pin down the transformation of the sulphur within the wood. This study of the hull at a cellular and molecular level has established that the current controls of the hull’s immediate environment are working but has given the researchers an insight into how to combat deterioration in the wood should it occur.
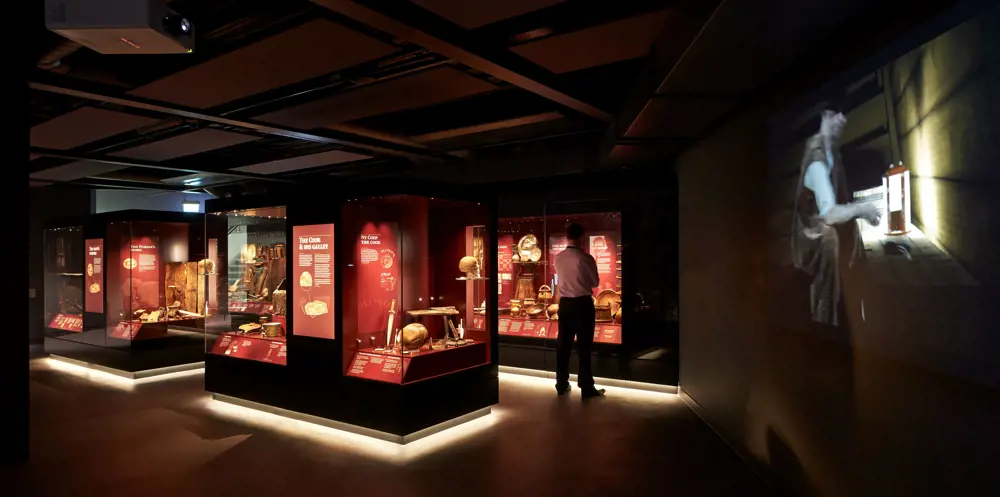
Museum display units often have a system of humidity control within the cases. The Mary Rose Museum has a micro-air-conditioning system for its display cases, each independent of the others, which are in turn connected to the chilled water system. The museum staff set the cases to 55% humidity and 19°C, which is typical for storing organic artefacts © Mary Rose Trust
Other projects include a research study developing ‘smart’ magnetic nanoparticles whose surface chemistry can be tailored with sequestering agents to remove harmful species from targeted artefacts. The Corr Group, based at the University of Glasgow’s School of Chemistry, is working with Dr Schofield to help remove free iron ions in waterlogged wood, thus preventing reaction with sulphur compounds. The aim then is to find ways to sequestrate the sulphate ions.
Another ongoing project involves analysing the laser scans taken over decades at different stages of the PEG and drying process. These scans provide a unique insight into how the ship has moved, deformed, and where cracks have formed and propagated over the decades, and will help evaluate the stability of the hull and inform its future care.
It seems that even after more than 400 years on the seabed, the Mary Rose is the Tudor ship that just wants to keep on giving.
***
This article has been adapted from "Raising and conserving the Mary Rose", which originally appeared in the print edition of Ingenia 74 (March 2018)
Contributors
Dominic Joyeux
Author
Dr Eleanor Schofield is Head of Conservation and Collections Care at the Mary Rose Trust. She completed a PhD in Materials Science at Imperial College London in 2006, then held research posts at Stanford Synchrotron Radiation Laboratory and the University of Kent. She joined the Trust in 2012 and is responsible for the conservation of the Mary Rose hull and associated artefacts, the care and management of the collection, and research into novel conservation treatments and characterisation methods.
Christopher Dobbs is Head of Interpretation and Maritime Archaeology at the Mary Rose Trust. He has 40 years of experience in the Heritage Sector in a wide variety of roles, mostly based at the Mary Rose Trust in Portsmouth. Chris has also carried out major roles outside Portsmouth including Vice-President and former Chairman of the Nautical Archaeology Society
Keep up-to-date with Ingenia for free
SubscribeRelated content
Arts & culture
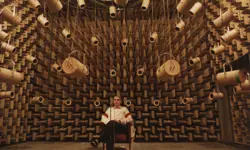
How to maximise loudspeaker quality
Ingenia asked Dr Jack Oclee-Brown, Head of Acoustics at KEF Audio, to outline the considerations that audio engineers need to make when developing high-quality speakers.

Engineering personality into robots
Robots that have personalities and interact with humans have long been the preserve of sci-fi films, although usually portrayed by actors in costumes or CGI. However, as the field of robotics develops, these robots are becoming real. Find out about the scene-stealing, real-life Star Wars droids.
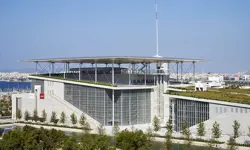
Design-led innovation and sustainability
The Stavros Niarchos Foundation Cultural Center, the new home of the Greek National Opera and the Greek National Library, boasts an innovative, slender canopy that is the largest and most highly engineered ferrocement structure in the world.
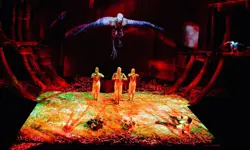
The technology behind ‘The Tempest'
William Shakespeare’s The Tempest is a fantastical play that features illusion and otherworldly beings. Discover how cutting-edge technology, such as motion capture and sensors, has brought the magic and spectacle to life on stage.
Other content from Ingenia
Quick read
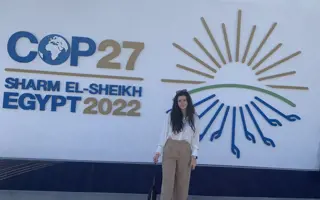
- Environment & sustainability
- Opinion
A young engineer’s perspective on the good, the bad and the ugly of COP27
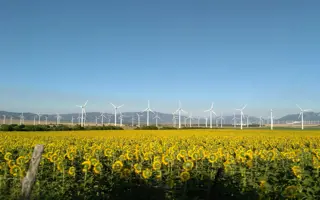
- Environment & sustainability
- Issue 95
How do we pay for net zero technologies?
Quick read
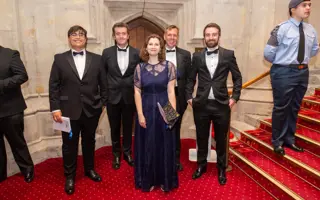
- Transport
- Mechanical
- How I got here
Electrifying trains and STEMAZING outreach
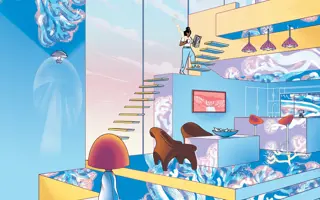
- Civil & structural
- Environment & sustainability
- Issue 95