
Q&A: Simon McGuinness, process systems engineer
Why did you first become interested in science/engineering/STEM?
As a teenager at school, my favourite lessons were those that involved a practical element or problem-solving – such as physics, design and technology, and even maths. Class-based lessons such as geography, although interesting, could be a challenge for someone who struggled with being cooped up in a classroom sitting still. I knew that when I had the chance, I would leave school as soon as I could and do something with not just my hands but also, hopefully, with my mind. I was fortunate at 16 years old to get a place on Nestlé UK’s apprenticeship programme as an electrical engineering apprentice.
The first year was spent away from the factory at an engineering school and during the first few months we were given exposure to different engineering disciplines such as lathe work, milling machines, fabrication, and welding before moving to our specialised disciplines. After that first year it was back to the factory where we rotated through internal departments (there were actually three factories on the one site so lots of different departments to experience with differing skillsets across them – a chocolate manufacturing/wrapping plant and two different coffee production plants). There was everything from manufacturing processes and production lines to packaging departments and all the associated services that are essential to factories. I even had to spend a couple of months in the forklift truck ‘garage’ to gain practical experience. I also spent one day a week at a college to work on my qualification.
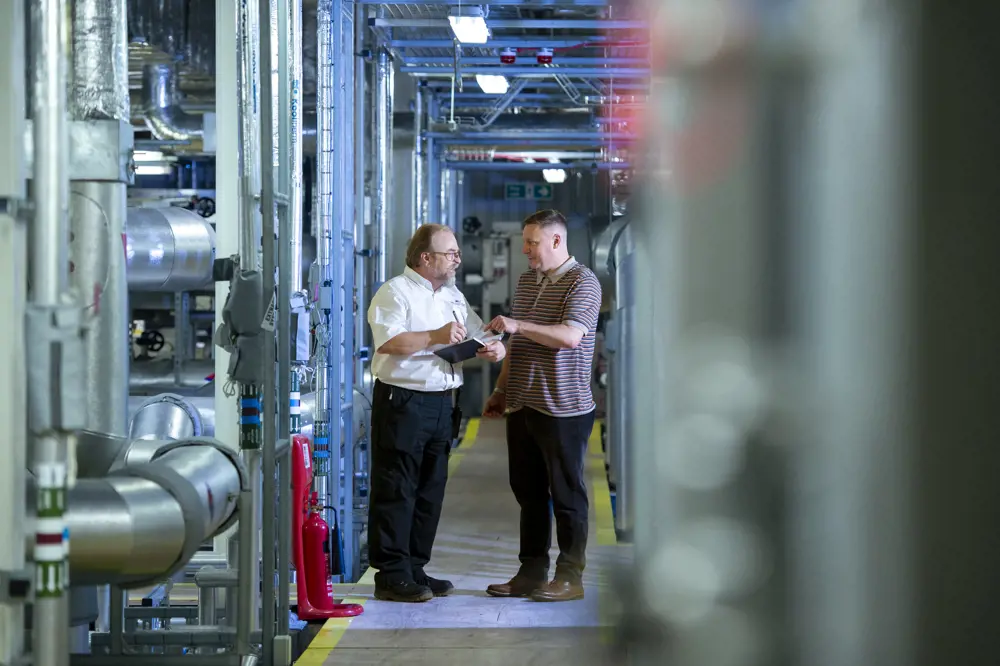
Simon, right, with colleague Keith Martin
How did you get to where you are now?
A good question, and one on which I now look back with wonder! I wanted to do industrial electrical installation work, at some point during my apprenticeship this type of work was outsourced. I was offered the chance to learn about instrumentation, automation and process control. I left with a wide skill base, as they had modern processes but also some from the 1970s using old pneumatic computers. I went on to work in a brewery, in wastewater, in an energy-from-waste plant, in bank note manufacturing, and then light pharma before ending up where I am now. While a lot of the equipment was very similar in each of these differing plants, the processes and science/chemistry behind the production or treatment was not.
There were also different methodologies employed by different organisations (some better than others!) but there were always challenges to face and learn from at each of them. As automation continued to evolve, I learnt more about programmable logic controllers and SCADA (supervisory control and data acquisition) at the brewery than I ever would have if I’d stayed at Nestlé.
There would also be development projects happening periodically at any site I’ve worked at, which would invariably involve the use of the latest ‘on the market’ technology available at the time, so it kept you up to date with what was happening elsewhere. At the papermill it was like stepping back in time 25 years as they still had a lot of very old equipment, some of which I’d not seen since it was being replaced at Nestlé many years before. So, my grounding in older tech and processes all those years ago came back to good use for me there.
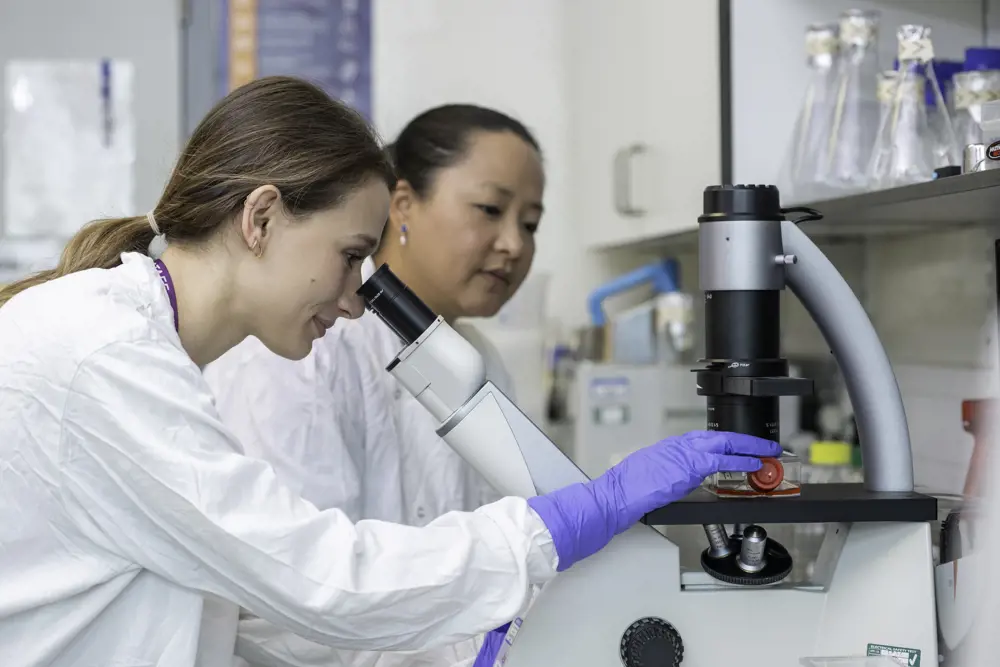
Researchers at The Pirbright Institute
What has been your biggest achievement to date?
Although I worked at an energy-from-waste facility built from scratch and have been involved with various-sized projects, I would still say my biggest achievement has been qualifying from my apprenticeship as an electrical instrumentation engineer and then getting offered a job at Nestlé all those years ago. There were no guarantees that anyone would receive a job offer on finishing an apprenticeship. Six apprentices were taken on in my year, but only three of us were successful in being retained. If I hadn’t had that chance I may not have continued in engineering and drifted into something else. I ended up staying at Nestlé for 13 years. After three and a half years there as a qualified engineer I was seconded onto a project to optimise and increase reliability and output throughout one of our manufacturing processes. From the work I did on that project I was then offered an engineering team leader role and put on a team leadership development programme. I completed that and remained in that role until about a year before deciding to leave at 29 to see what else there was out there for me to try.
What is your favourite thing about being an engineer?
There are two parts to this. First, problem-solving. Being able to apply logic to situations and resolve problems: fixing something that isn’t functioning is deeply satisfying.
Second, passing knowledge and skills to new engineers and seeing them develop. I haven’t forgotten the engineers who, when I was young and learning, took the time to help me understand. As with everything in life, learning and mastering a new skill – be it in sport, learning a new language – gives one a great feeling of achievement, but also allows the trainer or coach to stand and watch with a sense of pride and satisfaction.
Quick-fire facts
What's Simon's most-used technology
Age:
50
Qualifications:
Nothing spectacular when I qualified: City & Guilds in electrical installation, pneumatics, mechanical engineering fundamentals, instrumentation. I’ve been learning ever since.
Biggest engineering inspiration:
My dad, and those that took the time to help me learn/improve, even today. Every day is a school day!
Most-used technology:
PLCs/SCADA/human machine interfaces
Three words that describe you:
Inquisitive, structured, simplistic.
What does a typical day involve for you?
The Pirbright Institute (where I work now) is a world-leading centre of excellence in research and surveillance of virus diseases of farm animals and viruses that spread from animals to humans. My role now as a process safety engineer takes a more strategic approach mostly, rather than ‘hands on’. At present I am part of a team developing a process safety management framework for our site. It’s a highly regulated environment and we have regular health and safety visits to audit our systems, people and processes. One day I could be writing a high-level site standard document; the next I could be developing or performing proof testing regimes on our barrier systems, and the day after I could be reviewing failure modes and the effect they have on our processes and systems. With the potential for harm to animal and human health and the economy because of the viruses we handle/store on site, my role is to look at the design, operation, maintenance, and integrity of our facility and ensure nothing harmful can leave. To put it in a more visual term, process safety’s aim is to keep the jam in the doughnut!
What would be your advice to young people looking to pursue a career in engineering?
Technology constantly moves on. Don’t pigeonhole yourself, learn the importance of diversifying to make yourself more employable. The company or organisation you start at/are with now, may not always be there or you may want to try different sectors to work in. Adding new strings to your bow by cross-skilling can open up greater opportunities for yourself.
What’s next for you?
I have just been offered a place on the career development programme into senior leadership at The Pirbright Institute. The institute is looking at succession planning in the next couple of years. There are no guarantees at the end of the programme, but there are always new skills to be learnt!
Keep up-to-date with Ingenia for free
SubscribeRelated content
Design & manufacturing

Super cool(er)
Welsh startup Sure Chill has developed a cooler that uses the properties of water to keep its contents cool for around 10 days without electricity. This is ideal for storing items such as vaccines where electricity sources are unreliable.

R&D investment makes good business sense
In just five years, Dr Ralf Speth FREng has presided over a revolution in design and manufacturing that has helped create a new family of engines and has overhauled Jaguar Land Rover (JLR) production facilities.

Steel can arise from the ashes of coal
Thousands of people were laid off in the UK steel industry in 2015 and there are pessimistic future forecasts. Professor Sridhar Seetharaman of the Warwick Manufacturing Group argues that smaller, flexible steel mills implementing new technology would better cope with fluctuating global trends.

Integrating metrology in business and academe
Professor Jane Jiang’s interest in measuring began when she worked on a bus production line in China. She found that the best way to improve quality, consistency and productivity was through metrology, the science of measurement. Today, she runs the UK’s largest metrology research group.
Other content from Ingenia
Quick read
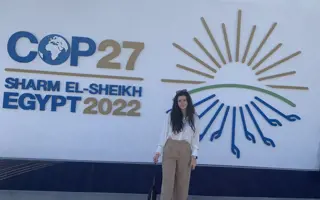
- Environment & sustainability
- Opinion
A young engineer’s perspective on the good, the bad and the ugly of COP27
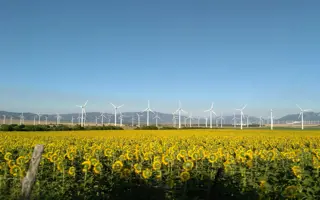
- Environment & sustainability
- Issue 95
How do we pay for net zero technologies?
Quick read
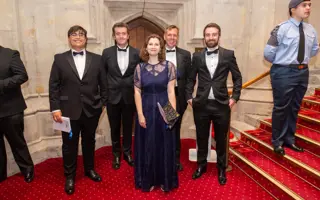
- Transport
- Mechanical
- How I got here
Electrifying trains and STEMAZING outreach
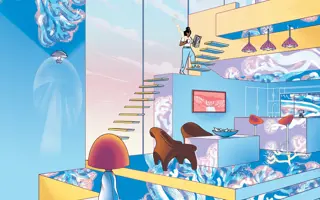
- Civil & structural
- Environment & sustainability
- Issue 95