
Pragmatic Engineering
A Motivation Rough Terrain wheelchair is assembled by Oscar, a wheelchair technician in Gulu, Uganda © D Constantine
The charity Motivation was established in 1991 following a competition held by the Royal College of Art in London. In the 21years since its formation, it has designed and supplied thousands of wheelchairs to disabled people in developing countries. Ingenia talked to one of the co-founders, David Constantine MBE, to see how engineering has been used to enhance people’s confidence and make their world more accessible.
It is estimated that up to 105million people worldwide need a wheelchair. By using a pragmatic approach to design and engineering, the UK charity, Motivation, produces 16,000 low-cost wheelchairs every year, especially tailored to suit the harsh terrain of life in developing countries.
The charity produces wheelchairs that enable cheap and easy maintenance and ensures that they are appropriate for the needs of the user. The funding to support their work often comes from international donors who will make a grant to Motivation to support programmes that deliver not only the wheelchairs but also set up supportive services and training.
Since its foundation in 1991, Motivation has provided assistance to 136,000 people in 90 countries around the world. The charity employs a staff of50, half in the UK and the rest in offices across Africa and Asia. Motivation products were awarded Millennium Product status by the Design Council, and the Worldaware business award for innovation in 2001. Co-founder David Constantine has received numerous awards and plaudits, including an MBE, and the Royal Society of Arts (RSA) Gold Medal for services to design.
The charity originated in a competition held at the Royal College of Art (RCA) in 1989.
Bad break
Back in 1982, David Constantine, then 21, was studying agriculture when he broke his neck diving into deceptively shallow water on Fraser Island in Australia. Back in the UK many months later, while still coming to terms with life as a tetraplegic (Constantine has no use of his legs and no grip in his hands) he swapped his farming ambitions for a career in IT with IBM. It was there that he met a group of industrial designers, a meeting that inspired him to return to education and pursue a creative career.
Constantine left IBM to take up a place on a master’s course in product design at the RCA. It was on this course that he and fellow student Simon Gue were tasked with designing a wheelchair suitable for use in developing countries. They created a prototype robust enough to cope with potholes and uneven ground that could be made from affordable, locally available materials. Their design was the best submitted and won them the Frye Memorial Prize.
The pair teamed up with their friend Richard Frost and used the prize money to travel to the Indian subcontinent to see how well their wheelchair would work in situ. In Bangladesh they visited the Centre for the Rehabilitation of the Paralysed in Dhaka, where they found a workshop producing a locally made copy of an orthopaedic Everest & Jennings wheelchair originally designed in the 1930s. This wheelchair was still ubiquitous, seen everywhere from hospitals to supermarkets and airports.
The chrome folding wheelchair was all too familiar to Constantine as it was the first wheelchair he had used following his accident. The Bangladesh version of the wheelchair had castor barrels for the front wheels made from the headstock of a bike, about six inches long, and very heavy. The rest of the chair was made of heavy gauge water-pipe steel, with 28-inch rickshaw wheels.
As well as being heavy, very hard to use and difficult to get in and out of, these locally‑made wheelchairs were ugly. The Everest & Jennings had been a revolution in wheelchair design when it was first launched, but designs had moved on, to slimline wheelchairs where the user is more visible than the wheelchair. This distinction is important in a place where disability is not really accepted or understood – in the streets of Dhaka, crowds of people would frequently gather around disabled people and stare.
The three co-founders built a version of their wheelchair design in the Centre for the Rehabilitation of the Paralysed workshop using local tools and materials. It was well received and the organisation asked the team to help them start producing the wheelchairs on a larger scale. Recognising that people with disabilities were the poorest of the poor and that providing them with an appropriate wheelchair was the fastest route out of poverty, the team needed little convincing.
Tailoring chairs

The first Motivation chair to go into production in Bangladesh
On completion of the RCA master’s course, the three travellers founded Motivation and raised funds to return to Bangladesh and set up production. Once on the ground, the team looked at the local context in more detail and visited the local markets to find what other materials were available rather than just using what was in the workshop. They also helped the workshop to move from making one chair at a time to making them in batches, streamlining production as well as the design.
The design was also revised to encourage better posture in the user. Where wheelchair users had got used to slouching and leaning on the large square armrests of the Everest & Jennings copies, the Motivation armrest was streamlined to follow the curve of the back wheel, deliberately incorporating a fall away at the back of the rest to encourage good posture. If the user sat up straight, they could lean their elbow on it, whereas if they leant forward, their arm would slide off.
The biggest engineering challenge was to think through a future for the wheelchair with potentially little maintenance, and how to repair and replace parts locally. This approach was key to the development of Motivation workshops as they spread across the world. The designs all used the most common bearing size, the most common tube size, and had to be made to withstand abuse of the product and all sorts of terrain. They would get rained on, covered in mud, and may not be cleaned or maintained.
An example of this pragmatism was displayed when the charity set up a project in Cambodia, a country ravaged by the Khmer Rouge. There was no infrastructure, no industry, and barely any steel around. Motivation bought all the steel they could to use for push-rims and axle tubes and looked for other materials. Mahogany was then a very cheap and strong material, so they came up with a design that combined mahogany with steel joints. It could be flat packed, and the mahogany could be cut easily. It was locally available, people were used to working with it, and it was easy to maintain. Even scratches could be covered with a bit of bees wax.
When the wooden chairs did come back for repairs it would be because the metal parts had become corroded and were falling apart, while the mahogany was fine. For years, this worked but, over the years, mahogany became much more expensive and Cambodian workshops are now planning to produce a steel framed wheelchair.
First decade
For the next 10 years, Motivation continued to set up projects that made everything locally. During that time, they saw changes in the availability of components and the emergence of MIG welding as a widely available technology – replacing brass‑brazing and some highly dangerous arc welding.
After this first decade, the founders of Motivation looked back and asked themselves: “What have we achieved, what can we do better?” The 22 different projects they had set up had produced around 18,000 wheelchairs.
They studied the approach taken by other organisations. In the US, charities would purchase ‘off-the-peg’ wheelchairs from a factory, usually in China, and hand them out en masse in developing countries. Others would collect old wheelchairs and distribute them. These methods would distribute high numbers of wheelchairs but offered no follow-up or repair facilities. Often the parts weren’t compatible with any product in that country. For example, 24” wheelchair tyres are not available in many countries.
Motivation decided to combine the two approaches. Their partners on the ground were reporting that the hardest part of successful supply was the workshop; managing the staff, keeping the orders coming in – with some having to turn to manufacturing ladders or wheelbarrows to keep the workshop open. A worse problem in the long term was that quality of manufacture could slip, leading to workshops producing bad wheelchairs that could affect the quality of life for the user.
After 10 years of building wheelchairs locally, Motivation decided to use their extensive knowledge to design a flat‑packable wheelchair that could be produced in China, allowing them to produce higher volumes and giving the organisation more control of the quality.
They would continue to work with local partner organisations on the ground, only now they would teach them how to assemble the imported wheelchairs and how to set them up appropriately for individual users. This took a lot of pressure off local organisations to constantly produce wheelchairs.
Fine tuning
The wheelchair designs have also been refined to best exploit the advantages of mass manufacture. People on the ground continue to feed their problems, needs and ideas back to Motivation in the UK, where decisions are made on any changes. Constantine acknowledges that designers and engineers will continue refining until someone draws a line and signals when to stop tinkering and start producing. This is often leads to difficult decision having to be made, and one where funding constraints help to keep focus.
Motivation uses digital modelling, but they have to over-engineer products to allow for the extremes of the environment on the ground. Using computer modelling software allows them to get to prototype quicker, but with so many other factors in play, including the quality of the materials and discrepancies in welding, they still need to build a prototype and hammer it to bits to see if it will cope.
The very first wheelchair produced in Bangladesh had been designed for use in a rehabilitation centre or around urban areas. Over the following years, the Motivation team noticed a pattern. All the projects after the wooden wheelchair in Cambodia involved producing a three-wheeler for rural areas. After Cambodia, the next project to focus on people living in very rough environments was Afghanistan, where in 1996, they converted the three‑wheel concept into steel. This gave Motivation the template, which they took to Sri Lanka and then to Tanzania, repeating this three‑wheeler again and again. This design became the rough terrain model that they still produce today.
As well as supplying the flat‑pack wheelchairs for assembly, Motivation is keen to enable existing projects to access the price advantage created through volume production, using a catalogue approach to provide items like wheels and pressure-relieving cushions for use with locally manufactured wheelchairs. Similarly, the organisation encourages partners to source wheelchairs through both the workshop and the flat-pack model, enabling them to sustain the benefits of both systems while maximising the quantities of wheelchairs available tousers.
Sports wheelchairs

With angled wheels for increased manoeuvrability and an anti-tip back wheel, Motivation’s sports chairs were used in Afghanistan’s first national wheelchair basketball tournament © D Constantine
Motivation’s reputation led to an approach by the International Paralympic Committee (IPC), who were looking for an affordable sports wheelchair to support sports programmes in the developing world. Working with the IPC, International Wheelchair Basketball Federation and the International Tennis Federation, the charity designed chairs forwheelchair basketball, tennis and racing.
What began as a range of chairs for the developing world was soon the subject of enquiries from charities and sports clubs in the UK, Europe, Canada and Australia. Even performance track athletes sought out the Motivation ‘Flying Start’ athletics chair, when they realised they could get a training chair for the cost of the wheels on their competition model. Soon, the organisation was shipping containers of sports chairs to an enthusiastic worldwide customer base.
At the opening ceremony for the Paralympics, charity members watched the athletes’ parade, spotting half a dozen people in everyday Motivation wheelchairs that had made it to the Games, including an athlete from Haiti, one from Iraq and another from the Solomon Islands.
Looking forward
Twenty-one years since it was formed, Motivation has come of age and is internationally recognised as a leader in designing, producing and distributing high-quality, low‑cost wheelchairs for developing countries.
Its co-founder, David Constantine, said: “People with disabilities in developing countries are often viewed as objects of charity. With their family and friends frequently making decisions for them, it’s not surprising that many disabled people have low self-esteem and lack confidence in their ability to live happy, healthy lives.
“Led by wheelchair users for wheelchair users, our peer group training transforms the way disabled people feel about themselves and their futures. Participants learn wheelchair skills, get active through wheelchair sports, find out how to prevent health problems like pressure sores, talk about sex and relationships and discuss their rights. We design wheelchairs but we also focus on the user to help people regain confidence and self-esteem, enabling them to become useful members of society.”
Read more at www.motivation.org.uk
David Constantine MBE and Chris Rushman, design engineer at Motivation, spoke to Tim Rushby‑Smith
Keep up-to-date with Ingenia for free
SubscribeOther content from Ingenia
Quick read
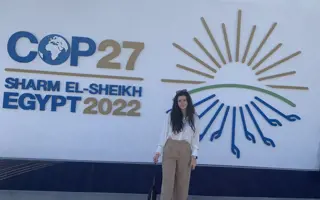
- Environment & sustainability
- Opinion
A young engineer’s perspective on the good, the bad and the ugly of COP27
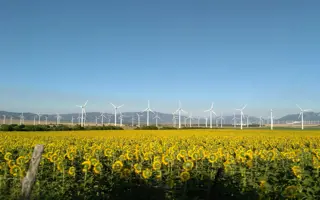
- Environment & sustainability
- Issue 95
How do we pay for net zero technologies?
Quick read
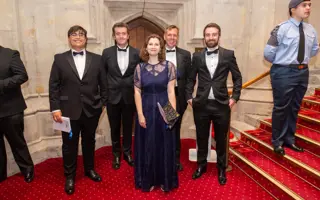
- Transport
- Mechanical
- How I got here
Electrifying trains and STEMAZING outreach
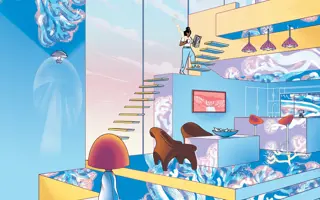
- Civil & structural
- Environment & sustainability
- Issue 95