Pitch Perfect
Prepared in time for the kick-off of the new football season, Arsenal’s innovative Emirates Stadium has already received plaudits from fans and media alike. Consulting engineer Buro Happold provided multi-disciplinary engineering on the project and Ian Liddell CBE FREng was in charge of the design reviews of the Emirates Stadium structures. He introduces some of the stadium’s significant features and explains how engineering was used to help deliver these.
The route from Finsbury Park station to Arsenal Football Club’s new Emirates Stadium in north London takes you past the club’s former Highbury ground, with its famous North Stand dominating the terraced housing around it. Unlike Wembley Stadium, now a very visible landmark for the capital, Arsenal’s new home stays hidden until one has crossed the footbridge and arrived at the raised plaza that surrounds it. When entering the arena, the scale and achievement of this project become clear. A view of the whole bowl, capable of holding 60,000 fans, demonstrates how light and open it is. The inward sloping roof disappears and the transparent sections illuminate the seating. The focus is entirely on the pitch where the action of the day is to take place. To achieve this on such a tight urban site required careful design, plus imaginative engineering and technology.
The original stadium
Arsenal’s stadium at Highbury in north London was built in the 1910s following the club’s move from its original home in Woolwich. Over the years, the terraces were exchanged for seating and new stands built to create an all-seated capacity of approximately 38,000. But with the growing popularity of football and the club’s success in the 1990s, it was clear that Arsenal needed a new home. Not only limiting the financial income from matches, the stadium was squeezed into a dense residential area which quickly became over-crowded during match days, making crowd movement difficult and potentially hampering access for emergency vehicles.
By the late 1990s the club had located a potential site nearby, at Ashburton Grove. This is a triangle of land squeezed between two railway tracks: the mainline out of Kings Cross and a suburban line leading to Old Street in east London. The site was an industrial estate, containing many small businesses and the Islington waste transfer station, all of which had to be relocated.
The club’s aim was to build a modern stadium with modern facilities. Sight lines would be improved and seating would be more comfortable compared to Highbury, with row spacing typically increased from 720mm to 850mm. Seating tiers would be steeper to ensure a better viewing experience for all spectators, regardless of location in the stands. In short, the aspiration was for a new stateof- the-art stadium with the best views, turf and ‘atmosphere’, predominantly meaning crowd noise, in the Premiership. The design team, with HOK Sport as architects and Buro Happold providing the full range of engineering,was appointed in 2000 to prepare concept designs. This was made on the basis that when a contractor was appointed the designers would be transferred to the contractor to form a design and build partnership.
Design drivers
A stadium isn’t just a place where fans can go and watch football. It can form the nucleus of regeneration efforts for an area, and become the focal point of a community through hosting events and providing employment for local people.
The stadium must make enough money to enable Arsenal to compete at the top Other vital functions for the stadium include crowd movement, safety and adequate provision of toilets – an important part of the overall visitor experience and something that has to be considered at the design stage. On the plaza, spectators are guided by colour-coded quadrants to lettered turnstiles where their ticket is read by a laser scanner, ensuring they only enter the correct zone. Upon entering the foyer areas, fans are immediately faced by food and drink counters that provide quick service, as well as an extensive number of toilets. From the foyer, fans are directed towards a vomitory that accesses the aisle adjacent to their seat. The whole system is simple to ensure the efficient handling of the large crowds that will regularly use it.
Of course, cost is always an issue and spend on amenities has to be fully justified. With an anticipated project cost of approximately £390 million, the stadium is a major expenditure for the club. This amount includes the cost of land, planning, stadium design and construction as well as relocation of local businesses and services, including building a new waste recycling centre, and regeneration of the surrounding area. Outlay had to be considered with regard to the overall business plan, which is tied in with anticipated income and running expenses.
The grass is greener
Arsenal was considered by many to have had the best playing surface in the Premiership at Highbury and the club wanted to continue that tradition. Ensuring good turf growth is an ongoing problem for any stadium with a fully enclosed bowl. It requires water, from rain or pipe, wind and sunshine in the right mix as well as the correct soil, drainage, fertilisers and maintenance regime.
Factors that can be controlled by the design of the building are sunlight and wind. In order to maximise natural light on the pitch, the roof cladding is fixed to the underside of the steelwork and the entire roof pitched down towards the turf from the constant height perimeter eaves. This lowered the level of the opening, thus increasing the solid angle of sky that is seen by the pitch. Illumination levels were checked by considering the geometry of the roof, the sun angles and the average amount of cloud cover.
Additional light was provided by making the inner ring of the roof translucent. This also softened shadows on the pitch and allowed more light into the seating areas. Harsh shadowsnon the pitch create problems for television coverage and for footballers, to the extent that some avoid running into brightly sunlit areas because they are then unable to see action on the opposite, dark side. In stadia with separate stands, wind can enter from the corners. For Emirates Stadium, the rectangular geometry of the front of the seating area interacts with the elliptical form of the perimeter to lower the seating at the corners. With the perimeter of the roof kept level, this leaves gaps at the corners where wind can blow through. The dished profile of the roof helps deflect it on to the pitch to dry the grass after dew has fallen.
Site constraints
The site had a remarkable number of existing buildings and other features that had to be addressed before construction could begin. The railway lines on two sides of the site restricted access for fans arriving and departing from the stadium and for emergency vehicles. Two bridges were therefore required to facilitate access. The building was designed to use all of the available space between the railway lines. Indeed, parts of the surrounding podium circulation space had to oversail existing railway land in order to ensure that there was adequate space for safe egress.
The waste transfer station was in the centre of the site and an alternative had to be built before it could be removed. This affected the planning of the whole project because the stadium had to be constructed in segments around it. Structures beneath the surface were also affected. While a deep main overflow sewer running across the site was left in place, a shallower sewer had to be diverted. The amount of time required to achieve vacant possession of the whole site meant that staggered possession of the land was necessary.
Structure
A height limit was set for the building by Islington Council as part of the planning approval. To meet this, the bowl design had to be as compact as possible. The design team generated over 100 bowl-sections in the quest for the optimum arrangement. To separate vehicle access from pedestrian access, a raised external concourse (known as the podium) was constructed around the building so that fans entered at the top of the lower seating tier. As well as facilitating comfortable and safe entry and exit, this reduced the height required to get fans to the upper terrace.
The bowl structure and back-of-house areas are constructed primarily from concrete, but with the upper tier supported by a steel frame. The seating steps are in pre-cast concrete, supported on stepped raking beams. Vertical cores provide routes for the escape stairs and vertical service runs as well as primary stability for the whole stadium.
The roof structure features two 15m deep primary trusses spanning 204m and supported on tripods on top of the stadium’s end cores. These carry secondary trusses above the ends of the pitch. Tertiary trusses span from the perimeter truss to the primary and secondary trusses and carry the roof sheeting on their underside. All of these are three chord trusses which were self-stable during erection which meant savings in time and temporary propping. This was an important consideration given the problems of site access and the inter-relation of demolition of the waste transfer station, construction of the bowl and assembly of the roof steelwork.
The thermal expansion of the roof structure is accommodated by longitudinal sliding bearings at the ends of the primary trusses, and by the flexibility of the tripods in the other direction. The perimeter truss was propped by a series of articulated stanchions around the perimeter, which transfer load down to the rear of the upper-tier rakers below and also carry the external cladding.
Because of their relatively shallow depth, the primary trusses have an inherently low natural frequency. Modelling of the interaction between the roof and the wind-loads allowed the engineers to demonstrate that the roof behaviour will be acceptable in all weather conditions.
Mechanical and electrical systems
As with all modern buildings, Emirates Stadium relies on its servicing systems. These made up a substantial proportion of the construction cost. Alongside provisions for water supply, drainage and the heating of occupied areas there were unusual specifications for the ventilation system to ensure it can cope with the surge of people arriving for a game – particularly when raining because humidity will be brought in as well. Car park ventilation was also a challenge. Jet flow fans were specified, their effectiveness having been validated using computational fluid dynamics software.
With the roof sloping down to the centre, pumped drainage for rainwater is required. A total of 50 pumps send water up to down-pipes at the rear of the bowl. They have been sized to deal with very high-strength storms, while overflows have been provided in case of power cuts, blockages or other malfunctions. Electricity is supplied through three transformers with diesel generators as back-ups. In the event of a power failure there is a prioritisation plan for discarding users, starting with electric cooking and heating. The escape lighting, of course, has to be maintained at all times.
Communications networks are of vital importance to the running of the stadium. Voice and data links are provided to all areas, as well CCTV and public address networks. There are also TV screens in most areas to allow fans and staff to follow the match or take part in the onscreen betting network. While this is not exceptional, with a perimeter distance of around 700m, the amount of cabling required to install and commission these systems meant the work was significant and challenging.
Procurement and construction
The scheme design for the stadium was presented in 2001. Sir Robert McAlpine was appointed in February 2002 as the main contractor for the project, which included building the new Waste Recycling Centre. The appointment was based on a two stage process with a lump sum for Sir Robert McAlpine’s preliminaries and a fixed percentage for overheads and profit. There was also a rigorous proposed programme duration imposed on the project and a specific Sir Robert McAlpine project team assigned. Once the bulk of the works packages’ allowances were agreed the contract was converted to a Guaranteed Maximum Price (GMP). Sir Robert McAlpine has a clear aim of achieving cost certainty before committing to a GMP and that means securing an agreed design and firm prices from the package contractors. For this project a great deal of negotiation was required – for the new Waste Recycling Centre there were 87 works packages and for the stadium 110.
Many of the key packages required a substantial design input. For example, the structural steelwork contractor was responsible for the design of connections and preparation of shop drawings, as well as detailing the cladding fixings. These details all require input from the design team to ensure the interfaces between packages run smoothly. Clarifying the design input and defining these interfaces reduces risk and makes for an efficient construction process.
On time, within budget
Having agreed to the GMP and a completion date, with hefty penalties for late delivery, hitting deadlines was key for Sir Robert McAlpine. The philosophy of the project director was continually to aim to bring the milestone dates forward, gaining extra time if it was required.
The stadium was completed over two weeks early, having incorporated a significant number of the client’s upgraded finishes on budget and the result is a stunning new landmark structure for football. The first game, the Bergkamp testimonial, was played on 22 July 2006 to a rapturous welcome from fans, players and media alike.
Biography – Ian Liddell CBE FREng
Ian was one of the founding partners of Buro Happold. The practice was founded in 1976 in Bath and is now a worldwide organisation with 1,300 staff. He is now retired from the partnership and is a Visiting Professor at Cambridge University Engineering Department and a consultant on a number of other interesting and challenging projects. He was awarded a Gold Medal from the Institution of Structural Engineers and an International Award of Merit from the International Association of Bridge and Structural Engineers. Ian was elected a Fellow of The Royal Academy of Engineering in 1996.
Keep up-to-date with Ingenia for free
SubscribeOther content from Ingenia
Quick read
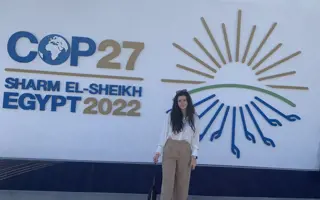
- Environment & sustainability
- Opinion
A young engineer’s perspective on the good, the bad and the ugly of COP27
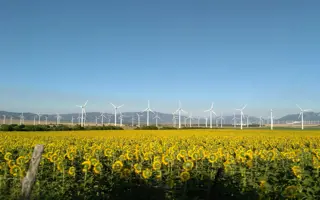
- Environment & sustainability
- Issue 95
How do we pay for net zero technologies?
Quick read
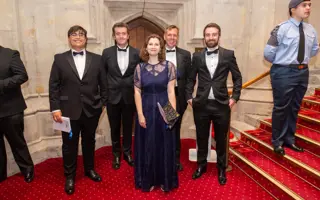
- Transport
- Mechanical
- How I got here
Electrifying trains and STEMAZING outreach
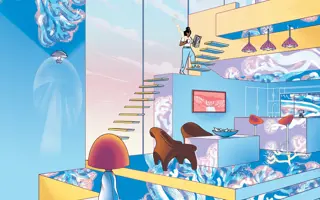
- Civil & structural
- Environment & sustainability
- Issue 95