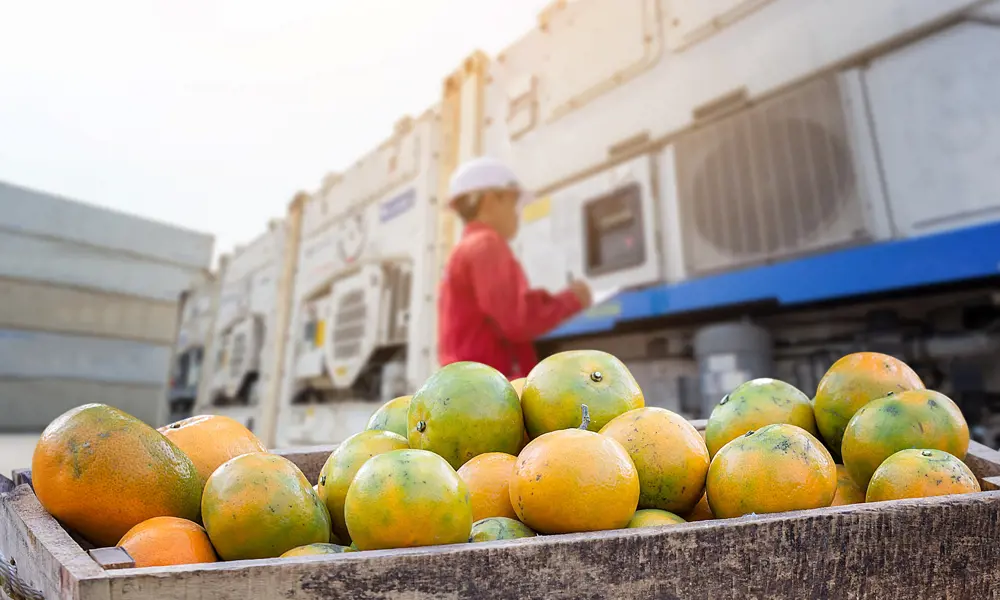
Phasing in greener refrigeration techniques
Did you know?
🚛 What are some of the most polluting road vehicles?
- Some of the most polluting road vehicles are those with onboard refrigeration. However, these are essential to keep food waste in the supply chain at a minimum
- This is because larger trucks and lorries often use diesel-powered engines with fewer emission standards than regular engines
- Phase change materials – a bit like the ones used in hand warmers – could be used to keep perishables at the right temperature instead
According to the latest Department for Transport report, in 2020, domestic transport produced 24% of the UK’s total greenhouse gas emissions, making transport the largest overall emitting sector. Not enough is being done to change this – there was a mere 3% reduction in emissions from domestic transport between 2009 and 2019. Some of the most polluting vehicles are those with onboard refrigeration, which is imperative for the transport of perishable food and medicine.
What’s more, 13% of all food is lost after harvesting and before being sold, due to insufficient cooling and temperature control in the supply chain. Engineering a better solution for transporting perishables could therefore contribute towards meeting the government’s targets of the UK becoming a net zero economy by 2050.
Current vehicular refrigeration systems work in the same way as your fridge at home.
A compressor compresses a gaseous refrigerant, which causes it to heat up. This hot gas flows through condenser coils on the outside of the fridge. It loses heat to the environment and condenses into a liquid. The pressure of the liquid drops down as it is passed through an expansion valve and it becomes a liquid/vapour mixture. Then the refrigerant flows into evaporator coils, where it evaporates and expands into a low-temperature, low-pressure gas, making these coils – and therefore the inside of the fridge – cold. The gas then returns to the compressor where it becomes a liquid again, and the cycle continues. A thermostat measures the temperature inside, and automatically initiates this cooling cycle when the inside of the fridge reaches the upper limit of acceptable temperature.
In smaller vehicles, this system takes power from the vehicle’s main engine, but larger trucks and lorries use an auxiliary engine – usually diesel-powered. There are fewer emission standards for these extra engines than there are for standard vehicle engines, so these systems are noisy, polluting and increase fuel consumption. Furthermore, they are based on a thermostat system, which means the temperature inside fluctuates within a range. They’re also reliant on the engine running, putting the contents at risk in the event of breakdown.
The challenge, then, is to engineer a portable cooling and temperature control system that doesn’t rely on diesel-powered engines.
The challenge, then, is to engineer a portable cooling and temperature control system that doesn’t rely on diesel-powered engines.
How phase change materials are being adopted for refrigeration
One solution is switching from a conventional refrigeration system to one based on solid-to-liquid phase change materials (PCMs). A familiar example of PCMs is sodium acetate heat pads, like the ones in hand warmers. Click the flexible metal disc inside the liquid-filled plastic pouch and crystallisation is nucleated in the supersaturated solution of sodium acetate. This phase change releases pleasantly warm heat. The pads can be reset by placing the pouch in boiling water, thereby re-dissolving the sodium acetate.
The material itself remains at a constant temperature during the phase transformation. The heat energy released or absorbed by the material during the transformation is called latent heat, and it’s this that could be exploited in PCM-based systems for refrigerated vehicles.
In the vehicle, the PCMs can be encapsulated into tubes, beams or plates inside an insulated unit. The melting or freezing point of the PCM can be selected to match the ideal storage temperature of the perishable produce. The idea is that the system can be ‘charged’ (the equivalent of boiling the sodium acetate heat pads) by plugging it into the electricity grid at night when demand and prices are low, and then provide cooling in the vehicle during the daytime. If the temperature inside the unit becomes too warm, the material will melt, absorb heat from the unit and cool it down. If it gets too cold, it will freeze and release heat, thereby helping to maintain a steadier temperature.
The PCM materials in these systems must be carefully selected to have freezing/ melting temperatures that match the requirements of the goods being transported. Often these are paraffins, salt hydrates or salt-water solutions, with modifications and additions to provide long-term performance and stability. Hubbard Products Ltd is one company developing PCM and systems that they believe will make an impact on the food transport sector.
Prototyping phase change cooling
To prove the concept, Hubbard tested a prototype of a PCM-based refrigeration system in Spain that represents a hybrid between the traditional refrigeration units and a fully PCM-based one. “This system combined a PCM storage tank with a conventional carbon dioxide-based refrigeration system,” explains Lin Cong, design engineer at Hubbard. In it, the PCM tank was used as a subcooler – a component that deliberately cools the liquid refrigerant in the condenser coils before it expands, making the conventional refrigeration cycle more efficient.
The researchers found that this hybrid system increased cooling capacity by 5% and reduced electrical power consumed by 18%. “The PCM‑based passive cooling unit part also served as a backup source of cooling in the event of unexpected shutdown of the conventional cooling system,” says Lin.
The potential savings from PCM systems depend on how cold the fridge unit needs to be, and also the ambient temperature outside; long and hot summer periods are particularly challenging. The cost of Hubbard’s proof-of-concept system involved prototyping and commissioning one-off components; the engineers hope that by upscaling and engaging with the tank and coil suppliers to achieve a single source design, they could reduce the price at least by half.
But the path to realising the potential of these technologies isn’t straightforward. While conventional refrigeration units are heavy, each PCM-based unit contributes to the weight load onboard. The more food crates there are, the more units will be onboard. If the total weight of PCM-based units onboard is too high, this could reduce fuel efficiency. As a result, developers and manufacturers must cooperate to ensure PCM modules are used in the supply chain effectively. This could be achieved with several approaches, including calculating the PCM weight according to the cold load requirement; using favourable PCMs with high latent heat, or fully replacing the refrigeration units with PCM modules and recharging the material at a charging port station. It will also need initial financial investment, in order for cost and fuel savings to follow.
Future developments of these materials include formulating solutions with larger latent heat and thermal conductivity, adding gelling agents to avoid phase separation and trying to limit corrosion on parts, either by using more compatible container materials or adding corrosion inhibitors. Their green credentials also rely on the energy used in the ‘charging’ processes coming from renewable sources. So, it could be necessary to liaise with energy suppliers to ensure the energy stored in the PCMs comes from sustainable sources. “The results we’ve seen from the testing that we’ve done are very promising,” says Derek Chapman, Design Section Manager at Hubbard.
The potential applications for PCMs extend beyond road transport. PCMs used in static settings – like a cold room, for example – would work “like a battery,” says Derek. “During high energy cost and demand periods, we can significantly reduce the electrical load required for the system. Then, at low energy cost and demand periods, we can recharge PCMs [the equivalent of boiling the sodium acetate heat pads to reset them]. It’s not necessarily a huge efficiency gain but it can be a huge gain in terms of cost, and if it’s done on a large enough scale, it could have big implications for demand in the national grid.”
“Currently, there is major demand during daytime and significantly reduced demand at night,” adds Lin. “It’s incredibly inefficient to start and stop power generation facilities regularly, so there is a lot of wasted energy. Using PCM technology in the cold chain is one way of addressing this.”
These static applications could be used in energy-efficient buildings and supermarket fridges. They could even be incorporated into textiles, embedding microencapsulated PCMs into the fabric, to serve as smart, temperature-regulating clothing.
And the future of the sector is promising. “There are numerous exciting opportunities for aspiring engineers in the food and drink industry,” says Derek. “Robotics and automation in factories and warehouses, and refrigeration design for maintaining the cold chain from farm to fork all requires mechanical and electrical engineers to name but a few. The impact that food and drink engineering has on the world is so massive, but it often gets overlooked.”
Contributors
Lin Cong, a design engineer at Hubbard Products, was awarded her PhD by the University of Birmingham. She has a profound knowledge and experience in thermal energy storage and cold chain.
Derek Chapman is a design engineer for Hubbard Products with a master’s degree from the University of Sheffield. He has 12 years of experience in the research and development of new refrigeration systems and technologies.
Dr Anna Ploszajski is an award-winning materials scientist, author, presenter, comedian and storyteller based in London. Her work centres around engaging traditionally underserved audiences with materials science and engineering through storytelling, as well as delivering training courses and undertaking academic research storytelling in science.
Keep up-to-date with Ingenia for free
SubscribeOther content from Ingenia
Quick read
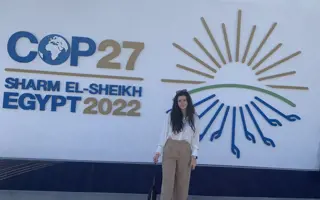
- Environment & sustainability
- Opinion
A young engineer’s perspective on the good, the bad and the ugly of COP27
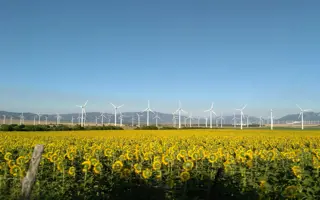
- Environment & sustainability
- Issue 95
How do we pay for net zero technologies?
Quick read
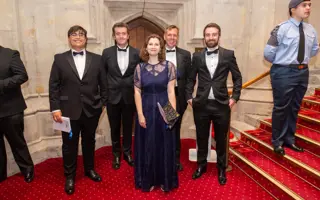
- Transport
- Mechanical
- How I got here
Electrifying trains and STEMAZING outreach
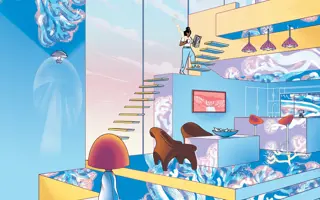
- Civil & structural
- Environment & sustainability
- Issue 95