
Modular construction of nuclear power stations
New nuclear power achieved a significant landmark with the agreement to proceed with Hinkley Point C power station. Currently, it takes many years and huge capital investment to build a nuclear power station, and much of this cost and time is due to the requirement to build large and complex civil structures onsite. Quality, efficiency, safety and programme reliability is currently achieved despite almost all manufacturing taking place onsite, much of it one-off designs, with large workforces often contending with adverse weather conditions at highly secure and sometimes very remote locations.
Modular construction, making many of the structural components off-site, is revolutionising many sectors of the construction and infrastructure industry
However, there is another way of building nuclear power stations that is quicker and cheaper. Modular construction, making many of the structural components off-site, is revolutionising many sectors of the construction and infrastructure industry, reducing building times with safer operations during construction and improved quality. A fleet of smaller, standardised and manufactured modular reactors could reduce these significant costs and timescales.
Small but efficient
Small modular reactors (SMRs) are smaller nuclear power plants (300 MWe (electrical megawatts) or less) than the current generation (1,000 MWe or higher). SMRs use factory fabricated reactor components that can be transported by truck or rail to a nuclear power site. The design concept of an SMR should be amenable to the manufacture of transportable components installed on their own or combined onsite with other modules.
In 2015, the UK government announced that £250 million would be allocated to nuclear research, some of which has gone towards a competition to identify the best-value SMR design for the UK
A recent report from the Energy Technologies Institute, published in September 2016, states that SMRs could be operating in the UK by 2030, but that the government has a crucial role to play in encouraging early investor confidence. There have been previous advances and research carried out in this field, with statistics from the National Nuclear Laboratory suggesting that there could be a potential UK market for 7 GW (gigawatts) of power generated by SMRs by 2035, which will account for 20% of the country’s electricity demand. In 2015, the UK government announced that £250 million would be allocated to nuclear research, some of which has gone towards a competition to identify the best-value SMR design for the UK. These steps are all contributing to making this alternative approach to generating nuclear energy more of a commercial reality.
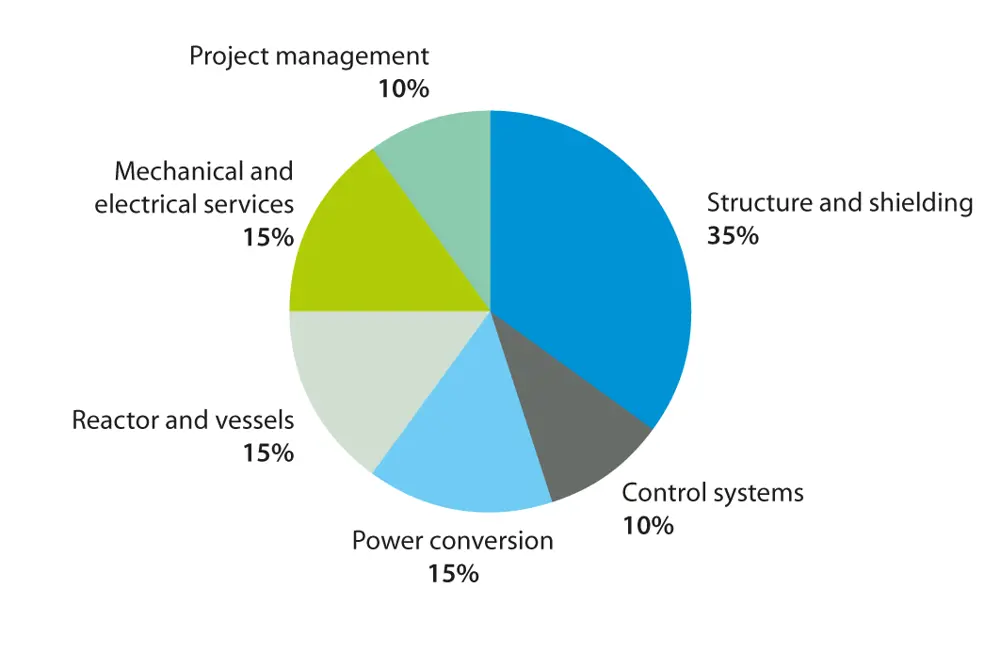
Typical SMR cost breakdown. Structure and shielding is often not a priority in construction of SMRs yet represents 35% of the cost (figures from the Cambridge Nuclear Energy Centre – TRaC)
Constructing SMRs
In 2013, Laing O’Rourke, Arup, the Building Research Establishment (BRE) and Imperial College London (and four separate co-funders: Innovate UK, Nuclear Decommissioning Authority, Engineering and Physical Sciences Research Council, and the then Department for Energy and Climate Change) collaborated on a three-year £2 million research project to investigate whether design for manufacture and assembly (DfMA) would be a suitable approach to constructing nuclear structures. Elements of the structure would be manufactured in factories before being transported to site for efficient and reliable assembly, a process that is already used in the building of skyscrapers, bridges, houses and railways. Recently, manufacturing capabilities have advanced to provide a range of modular components, including precast concrete columns, walls, beams and even smart walls and building systems.
In any industry, modularisation is easily applied to standard, repeatable units. Such methods are already applied in areas of the nuclear industry, but this project focused on road transportable concrete components to assemble large structures. It looked at two separate structures using precast concrete: standard shapes and sizes that are suitable for modularisation and complex ones that may contain difficult reinforcement details and irregular external geometry.
Five key principles for modular construction of nuclear power stations
☢️ From earthquake resistance and nuclear shielding to cost effectiveness
- Nuclear quality: nuclear projects must demonstrate that they consistently meet performance requirements such as earthquake resistance and nuclear shielding. Key elements need to be traced from initial raw materials, through a range of tests and checks, to execution of the required construction procedures onsite.
- Construction safety: the health and safety of the onsite workforce at remote locations is the immediate priority in the construction phase. It is a condition of the nuclear regulator’s site licence and is vital to the delivery of the project.
- Programme: delivering faster construction programmes ensures earlier generation of electricity and thus earns revenue sooner, helping to reduce overall financing costs that in large reactors can almost double the cost of construction.
- Onsite efficiency: competent delivery of the civil engineering components is vital to the delivery of economical power. Construction must be completed with a limited workforce and resources on remote sites.
- Off-site efficiency: where works are completed off-site, the additional costs of logistics and transportation must be balanced by more efficient manufacture ensuring that the project remains cost effective.
Standard Assembly
One example of a type of structure that is standard and repeatable is a cable tunnel, typically several kilometres of which are required in nuclear power stations. Cable tunnels carry essential electrical services underground around the nuclear power plant. Their simple geometry is typically a three-metre-square section with a 400-millimetre-thick wall. To verify the structural performance and assess productivity performance of the cable tunnels in this project, two full-scale trials were conducted using two different precasting methods. The solid precast method used elements that were manufactured off-site and subsequently transported and joined with minimum in-situ concrete, while the hybrid precast method used prefabricated reinforcement and permanent concrete formwork, which was subsequently filled in-situ with wet concrete. The trial components were manufactured in factory conditions on a concrete production line before being transported to BRE for destructive testing.

A computer-generated image of a solid precast solution (left) for a standard, repeatable cable tunnel and the equivalent hybrid solution (centre). The precast set up and ready for testing in the Building Research Establishment laboratory (right)
The results of this testing showed a huge reduction in time, effort and cost incurred onsite. The solid precast reduced onsite labour hours by 75% while the hybrid method reduced them by almost 50%. There is a balance to be struck: solid precast takes more value, time and effort off-site, but simplifies onsite activities, while hybrid construction enables greater use of road transport and cranes, as the weight transported is reduced.
Complex assembly
Unfortunately, many concrete elements in a typical power station are not as simple and repeatable as the cable tunnels. Modularising these more complex structures presents a larger technical challenge because of the existing designs, which include irregular external surface geometry and large wall thickness; large quantities of cast-in embedment plates; and very dense and complex reinforcement layout with large diameter bars.
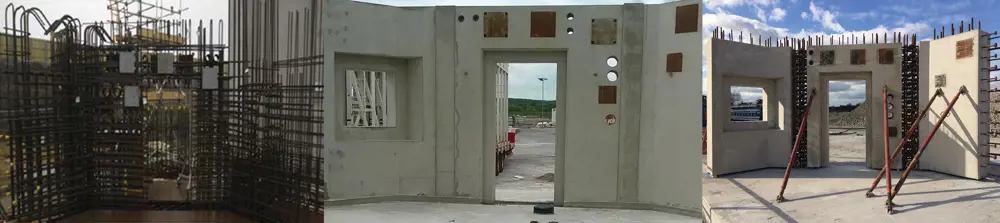
The three fuel building trials carried out during the project show the reductions in time achieved. The in-situ trial using traditional construction methods (left) was built in five days. The first DfMA trial using a solid precast solution (centre) was completed in one day. The second DfMA trial using a smart solid precast (right) saw the components manufactured 50% faster
On large nuclear power stations, the fuel building is used to store both fresh and spent fuel and is directly connected to the reactor structure. This building presents the most complex civil component of an SMR so three full-scale trials were carried out as part of this project to discover how construction should be tackled. The first trial used existing construction techniques, the second used solid precast, and the third focused on optimising the components for factory manufacturing techniques. To remove complexity from the construction site and move it into the factory, the trial constructions used standard, repeatable joints that only require onsite installation of preassembled reinforcement and relatively small concrete pours.
For this reduction in onsite duration to be translated into an accelerated construction programme, manufacturing innovation is required
The trials demonstrated that onsite construction can be reduced from five days to one day for typical reactor island designs. The site operation was simplified to assembly of, for example, three large premanufactured pieces, rather than fixing a cage of many individual bars, plates and components in-situ. A good example of this is Two Fifty One, a residential tower in central London, where 72% of the structure was manufactured off-site. This enabled a team of 24 people to build the structure at a rate of one floor every six days. Given that many SMR programmes envisage a 36-month construction period, compared to more than twice that for large reactors, SMR vendors may look to increase their building’s modularisation. For this reduction in onsite duration to be translated into an accelerated construction programme, manufacturing innovation is required.
Smart design for manufacture
Factories and construction sites have very different workforces, outputs and working conditions. These differences can change the structural concrete design: rather than producing a traditional design that is then manufactured, the focus of this project was on DfMA, which can make manufacturing construction more efficient. Inspired by lean production philosophies from other industries, such as automotive and aerospace, bent reinforcement bars were removed altogether, which fundamentally changed the process of assembling a reinforcement cage. By using entirely straight reinforcement, the steel fixing process was simplified by placing the reinforcing bar in a reusable jig. Rather than manual placing, tying and measurement of complicated three-dimensional (3D) shapes, the formwork determined the reinforcement geometry and improved the production rate, making it suitable for a factory environment and improving productivity.
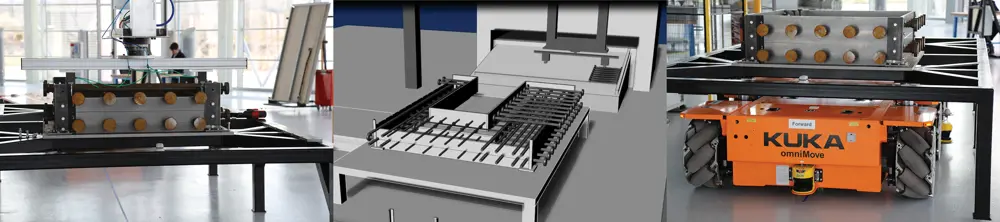
As part of the Innovate UK research project, robotic reinforcement placement trials were performed at the Advanced Manufacturing Research Centre with Boeing
SMRs represent an excellent opportunity to apply innovative manufacturing techniques to structures, ultimately reducing the construction capital cost of a fleet of power stations based on a standard design and manufacturing processes. In partnership with the Advanced Manufacturing Research Centre with Boeing at the University of Sheffield, a customised, standard gantry robot assembled reinforcement cages for a generic nuclear precast element. This technology led to the simulation of a robotic production cell for precasting nuclear components that were delivered 75% quicker than by manual manufacturing. However, there are several challenges in combining the high-precision world of robotic manufacturing with construction. For example, the allowable variations, or tolerances, on a construction site are 10 times greater than those of a manufacturing robot.
there are several challenges in combining the high-precision world of robotic manufacturing with construction
Continuing the smarter construction techniques employed on this project, every component and reinforcing bar was modelled in 3D. This allowed clash detection before the modular components were onsite. The manufacturing was directly driven by the model therefore eliminating manual work, and verifying the as-built component dimensions through laser scanning reduced the risk of the elements not fitting on site.
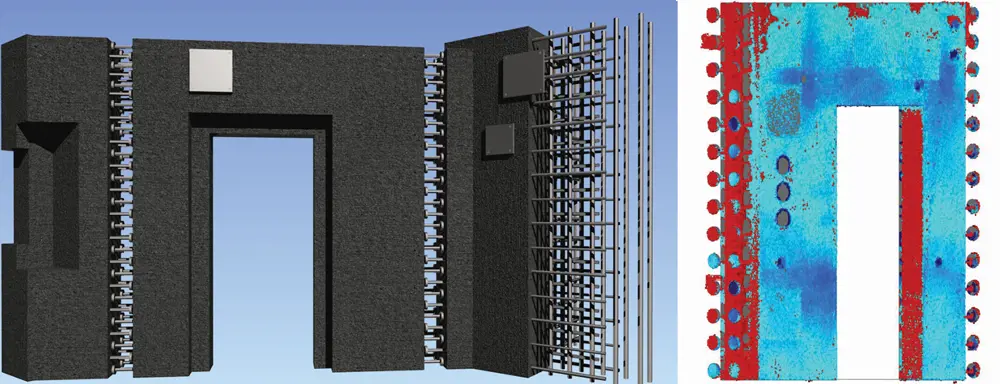
A 3D model of a nuclear component (left), and a laser scan of an as-built component compared against the 3D model (right). The government’s Construction 2025 strategy sets challenging targets for the construction industry: 33% lower costs, 50% faster delivery, 50% lower emissions and a 50% improvement in exports. Building information modelling (BIM) forms a central part of the government’s strategy and plays an ever increasing role on construction sites
Wireless sensor networks (WSNs) were integral to smarter construction on this project as they can continuously monitor environmental conditions (for example, temperature or noise) and communicate with each other. Continuous monitoring of the concrete temperature as it cured meant that its real-time strength could be calculated. When applied to a factory, this optimises the use of reusable moulds and equipment, and when applied to the construction site, it accelerates manufacture.
Benefits of modular construction
🦾 Positive outcomes of the research project
This research indicates that 70% of the civil engineering works involved in development of SMRs can be manufactured as elements in high-tech factories and delivered for efficient, safe and reliable assembly onsite, reducing time spent on construction by up to 80%. The research project developed:
- techniques for assembling nuclear structures out of prefabricated concrete elements, for both standard and complex structures, that reduce the onsite construction time and the risk of incurring cost and programme overruns
- techniques for manufacturing concrete elements for nuclear structures, using both existing manufacturing technology and new approaches in order to deliver programme and quality benefits without adverse construction cost impact
- flexible technologies to further improve the efficiency of manufacturing nuclear elements off-site, including fully automated robotic manufacturing and continuous monitoring solutions
- innovative methods for joining prefabricated elements that have been shown to deliver the performance required for nuclear structures.
Future applications
Few existing designs of nuclear power stations have considered fully modularising the structural parts of the power stations. This project has shown that modularising existing designs to meet the design requirements is possible. However, greater benefits are potentially available if designs and details are optimised to suit the modular and manufactured delivery approach. One of the major advantages of SMRs is the economies of multiples rather than economies of scale. By making a series of smaller standard designs, there is an opportunity to learn and improve processes between each one. According to researchers at the Cambridge Nuclear Energy Centre, current generation nuclear reactors have overnight capital costs of £4,000 per kWe (kilowattelectric) and electricity generation costs of £90 per MWh (megawatts per hour), while mature large reactors have overnight costs of around £3,000 per kWe and generation costs of £69 per MWh. For SMRs to be competitive, the costs of building a plant overnight should be around £2,200 per kWe, which would be consistent with electricity prices as low as £60–65 per MWh.
Further benefit could also be achieved by spreading manufacturing wealth across the country. A modern nuclear concrete precasting facility could be located in the North or Midlands and take processed reinforcement from South Wales for example. Politicians visiting construction sites already using DfMA solutions, such as Crossrail’s Liverpool Street Station, were impressed by the regeneration of the site of a former colliery in Nottinghamshire (now Laing O’Rourke’s Explore Manufacturing facility), which is currently supplying the precast concrete parts.
Modular civil engineering concepts can be developed to achieve high efficiencies on- and off-site, providing cost benefits and certainty while helping to achieve construction quality and compliance. By applying DfMA and advanced manufacturing approaches to civil engineering and nuclear construction, time onsite can be reduced by up to 80% while enabling opportunities to increase efficiency by using factory manufacturing. The current SMR development is ideal for early civil engineering engagement and modular civils could be a route to commercial success.
If this approach is exploited, we could see SMRs built with modular civil engineering component construction by 2030. Furthermore, this method is equally applicable to other large civil engineering structures, including in the transportation, utilities and energy infrastructure sectors.
***
This article has been adapted from "Manufacturing power stations", which originally appeared in the print edition of Ingenia 69 (December 2016).
Contributors
Harry Edwards completed an industrial placement year at Laing O’Rourke working on this collaborative project, ‘optimisation of large concrete DfMA structures for the nuclear industry’. He is now studying a PhD in structural engineering at the University of Cambridge, researching the seismic performance of modular concrete structures for the civil nuclear industry.
Adam Locke is a Project Leader for Energy Transition Infrastructure at Laing O'Rouke. At the time of publication, he was Partnership and Innovation Leader within Laing O’Rourke’s Engineering Excellence Group and led this project. Adam is a Royal Academy of Engineering Sainsbury Management Fellow, a chartered civil engineer, has an MBA from INSEAD, and holds degrees from the University of Cambridge and Imperial College London.
Dr Andrew Jackson is a structural engineer and was the technical leader on this project. He is part of the engineering design team of the BYLOR joint venture constructing the civil engineering works of Hinkley Point C power station.
Keep up-to-date with Ingenia for free
SubscribeRelated content
Civil & structural

Building the Shard
The Shard is one of London's most iconic buildings. The tallest in Western Europe, it was designed by Italian architect Renzo Piano and dominates the city’s skyline. Ingenia spoke to John Parker, project director for structural engineers WSP, who outlined the engineering decisions made in building the enormous steel and glass structure.

FlexiArch
Arch bridges are strong, durable and require little maintenance. However, very few had been built since the early 1900s until the FlexiArch was developed and launched in 2007. Now, there has been a minor renaissance for this ancient form of construction.

Creating user-friendly buildings
For Michelle McDowell, a former Business Woman of the Year, a passion for joined-up design thinking and building information modelling with a user-friendly approach has enabled her to pioneer revolutionary changes in her field.

Troja Bridge
In November 2014, one of the world’s largest network arch bridges was officially opened in Prague. The UK may soon have its first network arch bridge if the go-ahead is given for a new rail project in Manchester.
Other content from Ingenia
Quick read
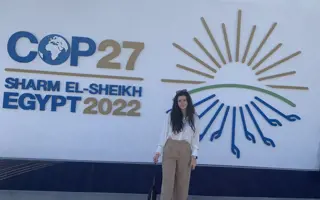
- Environment & sustainability
- Opinion
A young engineer’s perspective on the good, the bad and the ugly of COP27
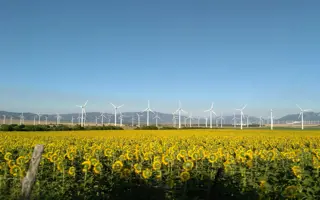
- Environment & sustainability
- Issue 95
How do we pay for net zero technologies?
Quick read
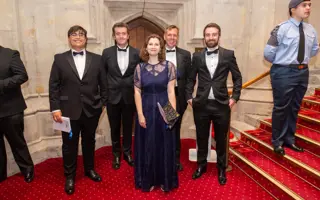
- Transport
- Mechanical
- How I got here
Electrifying trains and STEMAZING outreach
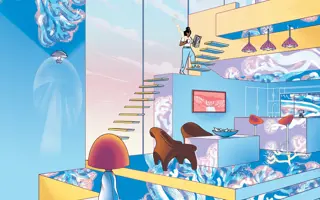
- Civil & structural
- Environment & sustainability
- Issue 95