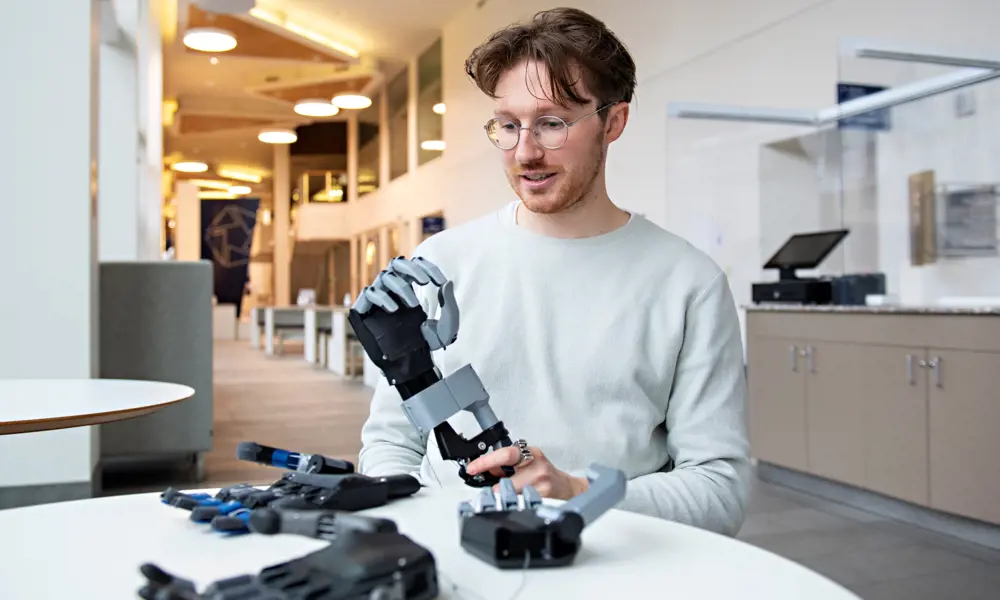
Making prosthetics without compromise
More often than not, the upper limb prosthetics that appear on the news are straight out of Iron Man: complex, powerful, and loaded with hardware. Yet despite the impressive technological advances in the field, some studies suggest that less than half of people with upper limb differences use prosthetics at all.
You might think it’s the prohibitive expense. Many high-tech myoelectric devices, able to sense the muscles’ electrical impulses, cost upwards of £30,000. At least, that’s what Fergal Mackie, CEO of University of Strathclyde-based startup Metacarpal, assumed at first.
Speaking to experts at the university’s prosthetics department, Fergal and his co-founder discovered that people were indeed trying to make such devices cheaper and therefore more accessible. But they realised that wasn’t the only issue with these devices.
Imperfect solutions
“The problems are really centred around the way they’re controlled,” says Fergal, explaining that the myoelectric arms tend to struggle with fine motor functions – for instance, picking up very small objects. Being stacked with batteries and motors also makes them weighty devices. Many people, including children and a lot of women, find them too heavy to wear all day, every day.
Enter the split hook. Invented in 1912, the split hook is one of the most popular upper limb prosthetics. It consists of two hooks that can open and close thanks to a mechanism controlled by the user’s shoulder. The mechanism is much like a bike’s brake. Pulling the brake lever pulls the cable, closing the brake pads on the wheel. On the split hook, a cable coming out of the hook goes around the user’s back to a shoulder harness on the opposite shoulder. Pulling this closes the hook’s grip.
“The split hook is arguably more functional, and still more popular, than myoelectric hands,” says Fergal. “And definitely for harder tasks, you would want the split hook rather than a myoelectric hand.” However, the split hook only provides a pincer-like grip – not so good for things like cooking utensils, “where you need a good, solid grasp”. And prosthetics are not just functional objects – they carry a psychological significance as well. “A lot of people [who] are recommended the hook would say, ‘no, no, I’m not wearing that thing’,” Fergal says.
Researchers have redesigned the split hook, including making hand models to cover the hook. But according to Metacarpal, no one has created a body-powered prosthetic with the aesthetic features of the myoelectric hands. “That’s one of the things that bionic hands have done really well,” says Fergal, referring to how some prosthetics users like the way bionic hands proudly exclaim their artificial nature.
The evolution of a classic
So, the co-founders of Metacarpal set out to make a more accessible and functional upper limb prosthetic, which also had some of the aesthetic appeal of the more technologically sophisticated devices. The initial design was centred on the intuitive body-powered mechanism of the split hook – but replacing the hook with a new terminal device, capable of different grips.
Metacarpal is perfecting its design bit by bit. “The first thing we looked at was the fingers, then the wrist, then the bits that go inside the palm to make it work. So now, you’re creating this whole palm to bring those together – and the thumb was a separate piece of its own as well,” says Fergal.
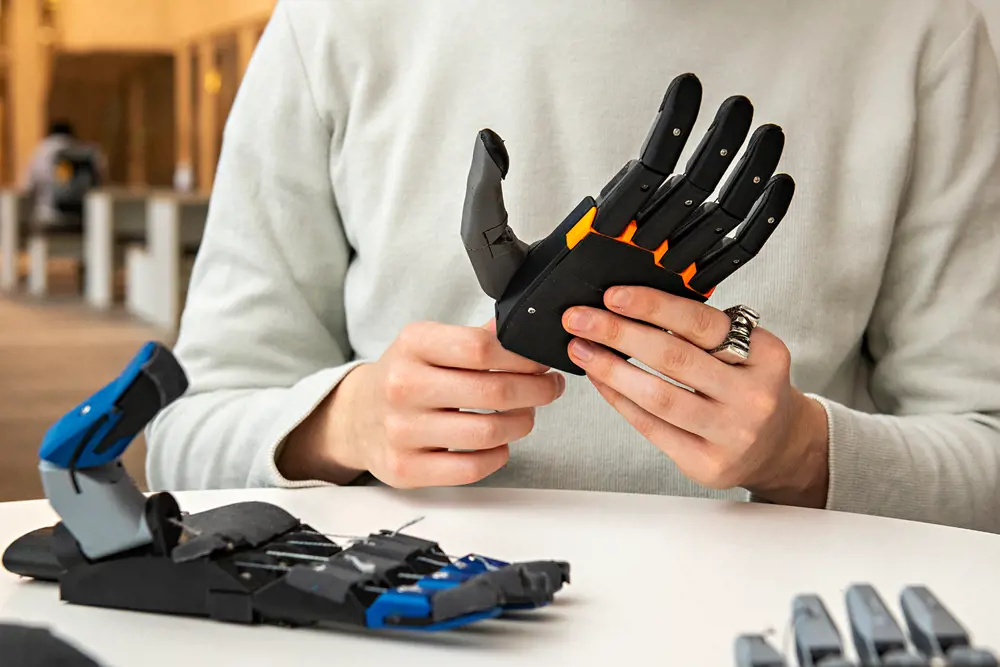
© Becky Duncan
To demonstrate the function and value of the idea, the founders created a prototype using their own 3D printer. They sought out feedback from their target audience to inform its development. “There’s a really helpful guy in Glasgow called Rico. He’d do stuff around his house that you would do every day – washing dishes, making a coffee, things like that – to test the device and see where it’s helpful and where it’s not,” says Fergal.
Beyond the prototype, they knew that it would need a combination of different materials and parts to get it working as functionally and as efficiently as they wanted. Now, with a workshop and access to more sophisticated tools, the team is exploring sheet cut metal, laser cutting, photoetching, and punching, for the bulk of the hand, and intend to use industrial-grade 3D printing for the parts that resemble the shape of the hand.
“We’re trying to make it as strong as possible. You can imagine [when] you can’t feel the device, it’s going to take a bit more wear than your natural fingers,” says Fergal. “There’s one major complaint that we always hear about the myoelectric hands and that’s that they just break all the time.” And without all the batteries and motors needed for a myoelectric hand, the team has a lot more weight to play with before the prosthetic starts to become too heavy.
However, creating different grips with the same body-powered mechanism as the hook is no mean feat. “You’ve got five fingers, but they’re all pulled from one cable,” Fergal explains. Upon meeting an object, such as a ball, all the fingers would stop at the same time. “But if I was to grab a ball, all my fingers would adapt around the ball.”
To address this, Metacarpal is testing a differential mechanism – meaning all the fingers can be pulled from one input, but their ultimate position can vary. But even testing out ideas is tough. “It’s pretty difficult to insert them into the model without just designing the hand around the system,” Fergal says. He’s confident in their ideas for mechanisms but says they will need to develop their testing rig so that it can measurably simulate how it might interact with objects.
Prosthetics without compromise
Now, the team is fundraising for a seed round closing in December 2023, and hope this will get the product to market. “We just want it to be the most functional prosthetic hand available, that doesn’t compromise the way it looks,” says Fergal.
And after that? “I think it’s all things in body-driven prosthetics. That isn’t to say that we might not incorporate electronics, but the control of them is always going to be driven by the user’s body. The harness is the first way we can do that, but we’re going to do a lot of research into other methods. And I think that’s something that we could really improve.”
Keep up-to-date with Ingenia for free
SubscribeRelated content
Design & manufacturing

Super cool(er)
Welsh startup Sure Chill has developed a cooler that uses the properties of water to keep its contents cool for around 10 days without electricity. This is ideal for storing items such as vaccines where electricity sources are unreliable.

R&D investment makes good business sense
In just five years, Dr Ralf Speth FREng has presided over a revolution in design and manufacturing that has helped create a new family of engines and has overhauled Jaguar Land Rover (JLR) production facilities.

Steel can arise from the ashes of coal
Thousands of people were laid off in the UK steel industry in 2015 and there are pessimistic future forecasts. Professor Sridhar Seetharaman of the Warwick Manufacturing Group argues that smaller, flexible steel mills implementing new technology would better cope with fluctuating global trends.

Integrating metrology in business and academe
Professor Jane Jiang’s interest in measuring began when she worked on a bus production line in China. She found that the best way to improve quality, consistency and productivity was through metrology, the science of measurement. Today, she runs the UK’s largest metrology research group.
Other content from Ingenia
Quick read
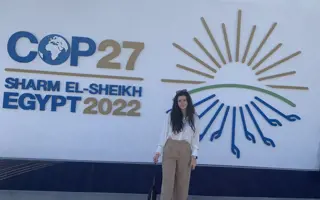
- Environment & sustainability
- Opinion
A young engineer’s perspective on the good, the bad and the ugly of COP27
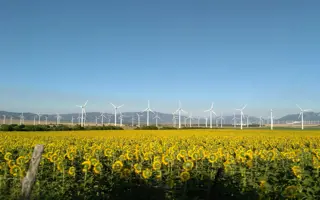
- Environment & sustainability
- Issue 95
How do we pay for net zero technologies?
Quick read
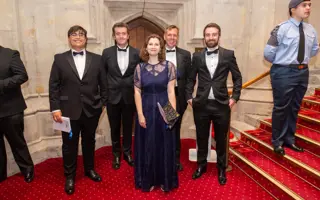
- Transport
- Mechanical
- How I got here
Electrifying trains and STEMAZING outreach
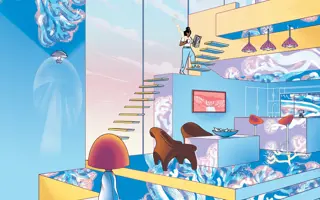
- Civil & structural
- Environment & sustainability
- Issue 95