Jane Atkinson FREng - Licence to troubleshoot
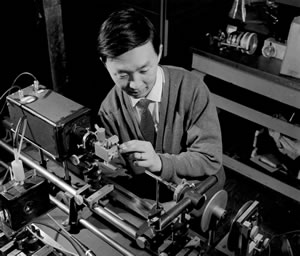
Jane Atkinson FREng
A shortage of metallurgists at British Steel gave chemical engineer Jane Atkinson an early break and a chance to develop her skills as a troubleshooter. Her expertise subsequently proved invaluable in commissioning and fixing steel plants and more recently in running a sustainable energy business. She talked to Michael Kenward about her past work and current campaign to persuade young people that engineering is a rewarding career.
Like most school-age youngsters, Jane Atkinson (née Tapper) rejected her father’s advice when it came to choosing a career. She was determined to become an engineer despite his reservations. Mr Tapper, a chemist at ICI, saw it as a mucky business dominated by men. But his daughter was good at and enjoyed chemistry and maths. Her response was, in effect, ‘Sorry dad, that’s what I want to do’.
Mr Tapper worked at Tioxide’s Seal Sands, Hartlepool, with responsibilities for health and safety, an area which is also now a part of his daughter’s remit. As a schoolgirl she had spent two weeks at the plant as work experience. “I absolutely loved it,” Jane Atkinson says. “I liked the idea of wearing a hard hat, going outside and seeing all the work that goes on at a big plant.”
It was British Steel that sponsored Atkinson’s degree in chemical engineering at Loughborough University, gave her summer holiday jobs and work for her sandwich year. The company also offered her a job at Redcar, back on Teesside, when she graduated. “I loved the steel industry. I still do. It is such a visual process, so dramatic, so dangerous in a way, with all its hot metal.”
Jane Atkinson was one of a dozen chemical engineers among a workforce of 4,500 at British Steel. Metallurgists dominated the workforce, but universities were abandoning the subject, so they became harder to recruit. Chemical engineers, with their additional knowledge of systems and processes, could fill this gap. She says: “They saw us as a bridge to the technology department and the metallurgical department. But to be honest, they just didn’t understand what a chemical engineer did.”
IN AT THE DEEP END
In 1994, when Atkinson was still only 23, she says: “British Steel was having a problem with an electrostatic precipitator. They said to me, ‘It is all chemistry bits, you can sort it out,’ and they just dropped me in it! As it turned out, it was a great way to learn.” Graduate engineers can wait years before anyone trusts them with real problems. Dealing with this one convinced Atkinson that she didn’t want to continue with day-to-day plant operation. “I liked the troubleshooting side of things. I liked an adrenaline rush.”
Atkinson knew that to be a fixer she needed to learn how to run the sort of big plant that had attracted her into chemical engineering. She asked her boss to let her run the cast house on a blast furnace at Redcar. He responded positively, telling her to spend six months finding out how to do the job. Atkinson then notched up the first of what would become a string of firsts, when she became the first woman in the world to manage a blast furnace. She credits her boss with having faith in her. “Today I still smile,” she confesses. “I don’t know how I had the nerve and guts to do it.” She now champions the role of good mentors for young engineers.
Her time running a blast furnace led to a series of important jobs commissioning and fixing problems on steel plant. British Steel sent her to Alabama in the US with just a few days’ notice to commission a new ‘direct reduced iron plant’. It was new in the sense that the plant hadn’t been used before. Built in Scotland, two decades before Atkinson got her hands on it, British Steel had mothballed the plant without processing a gram of iron. The company took it apart and shipped the 28,000 pieces across the Atlantic.
The scale of the task that faced her was enormous. The potential for things to go wrong was great. The suppliers of some of those pieces, compressors and pumps for example, no longer existed. “We had to work with a bunch of old manuals,” explains Atkinson. Then there was the problem of training an unskilled workforce, mostly local farm workers, unfamiliar with safety at a chemical plant which had, as Atkinson puts it, “lots of carbon monoxide and the potential to go bang”. Atkinson had to bring British Steel’s approach to safety to this novice workforce.
No one knew if the plant would work. She made sure that it did. Invited to stay on and run it, Atkinson did this for two years but, still keen to troubleshoot, moved on. So the company sent her to Tuscaloosa to sort out a ‘mini-mill’ producing steel for oil and gas pipelines. For 10 years, the mill had rolled out 40-tonne slabs of steel containing bubbles, an unwanted addition to pipeline steel, resulting in too many rejects. “Eight months later, and after a lot of trial runs, I managed to solve it,” says Atkinson. It was, she explains, a case of keeping air out of the process at crucial stages. Her solution, which increased output by 20%, wasn’t just of local interest; the industry could use her approach on any mini-mill.
After nearly five years, Atkinson was coming to the end of her stay in the US. She had to get a green card or return to the UK, so she returned to Teeside to the job of Manager, Coke Making. Once again, Atkinson sorted out various technical problems. Here, she developed an innovative and economic way to repair gas mains on line. The repair prolonged the life of the Redcar coke ovens and was once again universally applicable beyond the local plant.

The Wilton 10 biomass power station became the UK’s first large scale wood to energy plant when it began full commercial operations in 2007. The station takes its 300,000 tonnes a year wood fuel requirement from three separate sources: recycled wood is supplied in chipped form, offcuts from sawmills and round wood logs are chipped on site. Once mixed, the woods are fed into a fluidised bed boiler to generate more than 30 MWe from a steam turbine set. The plant also has the capacity to export steam to the Sembcorp site if required © Sembcorp
UTILITIES PROVIDER
After 14 years with British Steel, then Corus, she was headhunted for the post of Vice President, Utilities Operations with Sembcorp, at Wilton on Teesside, a few miles from Redcar. By the time Atkinson moved to Sembcorp, ICI, the previous owner of the Wilton site, had divested itself of much of the heavy duty processing plant that had once been its bread and butter. Wilton International had become a ‘processing park’ with various owners running different plants rather than a company site.
Sembcorp provides services to these
plants which are run by some of the world’s leading chemical and manufacturing companies. Once again, Atkinson had entered unfamiliar engineering territory, running what is in effect an energy company. Sembcorp’s power stations don’t just deliver electricity, they also provide steam and some of the gases that are essential inputs for processing plants. In all, the company can deliver around 250 MW of power for local use or to sell to the National Grid, more than 800 tonnes of steam every hour and 175,000 cubic metres of water.
Her portfolio includes one coal boiler, two gas turbines, four package boilers and a biomass boiler, along with high voltage, infrastructure and nitrogen facilities, as well as the water treatment plant. Sembcorp needs this capacity to meet the needs of five large processing plants. These include Huntman’s polyurethanes plant, facilities where Lotte makes purified terepthalic acid (PTA) and polyethylene terephthalate (PET) and SABIC operates a large olefins ‘cracker’, an ethylene liquefaction facility, as well as making low-density polyethylene (LDPE).
This mix separates Atkinson’s operation from run-of-the-mill energy operations, with its focus on delivering electricity profitably. As a chemical engineer, Atkinson understands the needs of her customers. Electricity is important but so is steam for many, and in quantities that can change in an instant. For example, one customer operates an oil cracking process that takes 15 tonnes of steam an hour when it is running smoothly, but if the plant goes off for any reason, steam consumption soars to 200 tonnes an hour. “I always have to have that capacity available,” says Atkinson. Usually that steam drives a generator and Sembcorp sells the electricity it provides. But when the plant’s steam demand rises, Sembcorp can stop electricity production and divert the steam to the cracker.
She is so keen to keep her eye on the processing plants that Atkinson insists on having her office in the thick of it rather than in the company’s more modern local HQ. “Here, I open the windows, stick my head out when there is a noise and I know which bit of the kit is making that noise.” Atkinson can also look at the steam coming out of the top of one of her power station stacks and offer a commentary on the state of the plant.
EYE ON THE WIND
The need to respond to short-term fluctuations at customers’ plants complicates the everyday economics of Sembcorp’s operations. Atkinson now needs to keep an eye on local wind conditions, as the growing number of wind turbines influences the spot price for electricity. Throw in the ‘boom and bust’ nature of the chemicals sector, with its five- or six-year cycles, and it is easy to see why she likes to serve a broad range of businesses on the site. For example, one plant on the end of her pipelines is Ensus, which turns grain into biofuels.
Atkinson’s plant also supplies power and steam for waste processing firms at Wilton and she is keen to attract more of these. For example, Biffa Polymers operates a large recycling operation at Wilton with two plants capable of processing around 40,000 tonnes of waste plastics a year. “One of the attractions is that we can sell green energy, green steam and offset their carbon as well. We are keen to attract these types of new industries to Wilton”. Driving around the near-800 hectare site, Atkinson points to empty plots and derelict plants where there is plenty of room for development.
And if this wasn’t enough variety, in addition to running a portfolio of power stations burning coal and gas, Sembcorp also gave Atkinson the UK’s first commercial biomass boiler to run. The £64 million plant, which came online in 2007, produces 35 MW of electricity – enough to power a small town – utilising around 300,000 tonnes of wood a year as its fuel, drawn from a variety of sustainable UK sources.
Much of the wood is recycled and collected at local authority waste disposal sites throughout the country. It is low value and with no alternative use – most of the wood was previously sent to landfill. The station is also fuelled by sawmill residues and small roundwood logs from managed forests throughout the north east.
Atkinson’s troubleshooting skills have proved handy at the biomass plant. In just six months, tapping into her knowledge of coal handling, she raised the available operating time of the biomass plant from 45% to 83%. Sembcorp is now drawing on its experience in the UK to make biomass a part of its global strategy, she says.
PROMOTING ENGINEERING
So, reflecting on her father’s comment all those years ago about a profession dominated by men, how does Atkinson feel now about women in engineering? She is, she insists, an engineer who just happens to be a woman. As someone who has been singled out for her work – among numerous accolades, the CBI honoured her as Britain’s top female engineer in 2007 and in 2010 she became the youngest woman Fellow of the Royal Academy of Engineering – Atkinson sometimes finds herself sharing a platform with other high-flying women. While some may complain about glass ceilings, Atkinson isn’t having any of that. Maybe it is the blunt northerner coming out, a cliché that she laughs at, but then again, maybe it is the pragmatic engineer.
Yes, there may have been times when companies failed to provide facilities for women, and sometimes still do, and there are not enough women in engineering today. That is down to the wider message that young girls receive, says Atkinson, and not just from reluctant fathers. While she sees signs of progress, such as more women taking up engineering degrees, Atkinson wants to do more to persuade young people that engineering is an enjoyable and rewarding career. She naturally focuses on Teesside. “We have really struggled in the north east to get young people into engineering. People think that this is an industrial wasteland.” Far from it, she insists, “It is a beautiful area.” And there are plenty of career opportunities.
While Atkinson isn’t likely to jump at invitations to sit on a platform of ‘professional women’, she finds it almost impossible to turn down opportunities to talk to youngsters. You have to catch them at 11 or 12, she insists, when they are making their first subject choices. You then need to get to them again in the sixth form when they are beginning to think about careers. Sembcorp hosts a constant stream of youngsters wearing hard hats. They just love the idea of visiting a ‘green energy’ plant, she says.
Atkinson has also played her part to plug the skills gap at another level, the plant operatives. There are plenty of schemes for traditional apprenticeships, such as “mechanical, electrical and ‘instrumentation’”, she says, “but we couldn’t get operations people, the shift people who sit there running the plant.” With Atkinson in charge, Sembcorp became the catalyst for a sitewide apprentice programme addressing not only the technical but also the operations skills that young people need at the plant.
More than 10 years on, the scheme extends beyond Wilton as the Tees Valley Production Technician Apprenticeship, a fast-track scheme for youngsters with A-levels. The first cohort of apprentices emerged about nine years ago: two of them are already shift managers. “Some are now also going on to do degrees, which is great.” she says.
When it comes to those degrees, it helps to have a local university that works closely with the processing industry. Atkinson chairs the external advisory board of Teesside University’s School of Science and Engineering. The problems facing part-time students are high on the board’s agenda. Industry likes the ‘part-time’ idea because it does not disrupt the work pattern too much, while for the university it increases student numbers and income, without breaking government quotas for student numbers. Atkinson also works with the university to improve the ‘employability’ of graduates. “One bit of work that we have been doing with the university, and this has come off the back of the Royal Academy of Engineering’s report on employability skills, Jobs and Growth, is how do we get it embedded in an undergraduate course?”
Jane Atkinson’s background as an experienced technical troubleshooter and a senior manager running major facilities has equipped her well for the task of attracting youngsters into engineering and ensuring that they have the right skills. And now, another new challenge has landed on her desk, a plan to build yet another power station at Wilton.
In April this year, Atkinson learned that, along with the ability to burn oil, coal, gas and wood, the Wilton site is going to tackle the challenge of burning household waste. In a contract worth £1.18 billion over 30 years, SITA Sembcorp UK, a consortium led by SITA, will manage over 430,000 tonnes of ‘residual household waste’ each year from the Merseyside Recycling and Waste Authority. Atkinson is enthusiastic about this project, but it may mean the end of her cherished observation post in the middle of the action. Her office may have to be demolished to make way for the power station. Somehow, this seems like a minor inconvenience for an engineer who has taken on and solved so many challenges in her career already.
Keep up-to-date with Ingenia for free
SubscribeOther content from Ingenia
Quick read
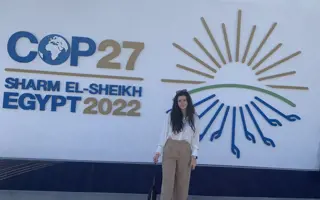
- Environment & sustainability
- Opinion
A young engineer’s perspective on the good, the bad and the ugly of COP27
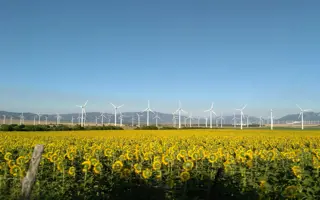
- Environment & sustainability
- Issue 95
How do we pay for net zero technologies?
Quick read
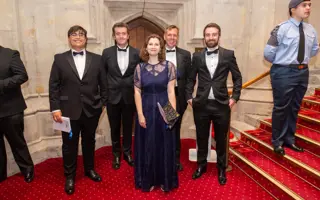
- Transport
- Mechanical
- How I got here
Electrifying trains and STEMAZING outreach
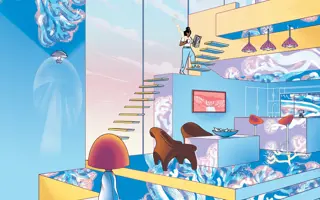
- Civil & structural
- Environment & sustainability
- Issue 95