
Intelligent prosthetics
Thousands of people each year suffer the loss of one or both of their legs to amputation following an injury or disease. There are some 45,000 people who rely on prosthetic limbs in England alone and across the UK around 5,000 people each year have lower-limb amputations. In the US, there are an estimated two million people living with an amputated limb. It is a completely life-changing event, robbing people of abilities that most take for granted, such as walking, running and even standing still.
While prosthetic limbs can help give amputees back some of their mobility, they can be far from perfect. Tackling obstacles such as ramps, kerbs and steps with a prosthetic leg can be intimidating, and many lower-leg prosthetic wearers have to carefully plan their days to avoid such tricky terrain.
However, new technology is transforming prosthetic legs from being inert supports to limbs that react and respond to different terrains and movement. Blatchford, a family run company based in Basingstoke, Hampshire, has developed the first ever prosthetic limb that combines robotic control of both the knee and the ankle to ensure that they work together much like a real human leg. According to Chair of the MacRobert award judging panel, Dr Dame Sue Ion DBE FREng, this innovative development “has combined a compassionate approach to patient needs with huge ambition and exceptional systems engineering”. The Linx limb system went on to win the Royal Academy of Engineering 2016 MacRobert Award.
The problems with prosthetics
Walking down a ramp without control of the leg joints will cause them to bend and flex on their own. If they rotate too easily, it can produce the sensation of constantly falling forward and the wearer needs to walk in a way that compensates for that. Equally, if the joints offer more resistance, it can make walking in the other direction, up a hill or a flight of stairs, a painful struggle. Without enough movement in the ankle, for example, a prosthetic leg wearer has to pivot around their prosthetic leg with their healthy leg to make progress.
Just standing still can also be a challenge for people with prosthetic legs, requiring extra energy and concentration to remain steady, which can quickly become exhausting
An amputee who has lost their leg from above the knee – known as transfemoral amputation – expends 60% to 80% more energy walking than someone with both their legs, while transtibial amputees – who have lost their leg below the knee – use 30% more energy. Running and other rapid movements require special limbs that are ill-suited to more mundane tasks. The famous running blades worn by athletes are not designed to be used when standing still and those wearing them can only stay balanced by moving constantly. Just standing still can also be a challenge for people with prosthetic legs, requiring extra energy and concentration to remain steady, which can quickly become exhausting. The toll that this can take on the human body is profound.
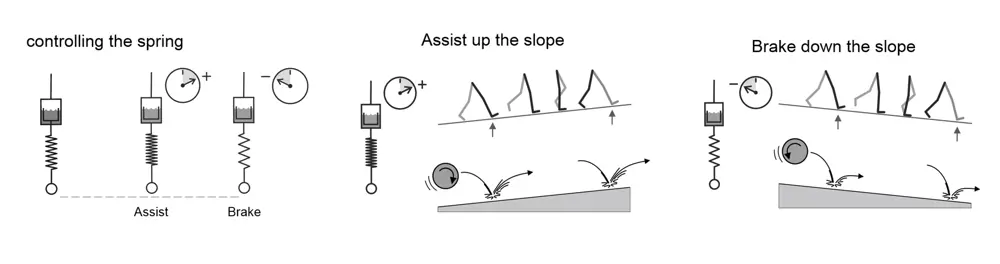
The Linx limb system’s springs are biomimetic viscoelastic models that control the level of energy absorption and damping resistance. When walking up a slope, the rollover of the spring minimises impact on collision with the ground to maximise forward momentum. When walking down a hill, the rollover maximises the damping on collision with the ground to reduce forward momentum
Amputees can suffer severe back pain that needs to be treated with powerful prescription painkillers because of the extra strain caused by the unnatural gait and stances they have to adopt. They are 17 times more likely to need a hip replacement after 20 years of using a prosthetic limb and 14 times more likely to need a knee replacement in their healthy limb due to the extra load that these joints are put under.
Blatchford’s Linx limb system uses data from seven sensors in the foot, ankle, knee and main body of the prosthesis to detect changes in the terrain, the user’s movement and the activity they are performing. These sensors essentially mimic what the nerves in a real leg would be doing, but rather than feeding the information to the brain, it instead goes to a central microprocessor, which then works out how to adapt the movement of the joints. A network of springs and dampers, which work similarly to the shock absorbers in a car, allow the joints to absorb energy and either return it when needed to help a movement such as walking upstairs, or provide a braking mechanism in situations including walking down a hill. As a result, wearers can walk more naturally and with greater stability than other prosthetic limbs allow.
Based on biology
Blatchford’s goal was to provide amputees with prosthetic limbs that behaved far more like the real thing, and the Linx system is the culmination of 40 years of development to introduce increased functionality and adaptability into prosthetic limbs. The company began thinking about how to replicate the action of the muscles in the human leg that pull against each other to control how joints bend. To do this, Blatchford first began to develop the use of hydraulic systems to control the movement of knees in prosthetic limbs in the 1970s and 1980s. Its engineers turned to carbon-fibre composite springs and hydraulic dampers to become the muscles’ mechanical equivalents. With each step, the springs in the knee, ankle and toes store energy, ready to release it again to propel the joint forward. The dampers help to control the springs, absorbing excess energy and providing resistance to prevent the joints from moving too quickly or too much. The key is how to adapt to the wide variety of terrain that people encounter during their daily lives.
Its engineers turned to carbon-fibre composite springs and hydraulic dampers to become the muscles’ mechanical equivalents
In 1989, Blatchford created the first limb with a microprocessor controller in the knee. This marked a gear change in the functionality that was possible, allowing the limb to control the speed of movement according to the activity, such as descending a staircase.
Through the 2000s, the company began developing innovative joints that produced smoother gait and better control, and the addition of independent movement to the heel and toe of the prosthetic limb created far more fluid movements. If the wearer is walking down a slope, for example, the system recognises the angle from the sensors around the limb. This increases the resistance provided by hydraulic dampers at the toes to stop the energy being absorbed by the spring, which would cause it to propel the limb forward.
Biomechanical analysis carried out by Blatchford showed that changes in resistance of the knee joint influenced the ankle-to-foot joint and vice versa. This led to a ‘brake’ mode being developed that not only worked to stop the knee sinking forward on a downward slope, but also acted in the ankle to reduce the amount of momentum transferred to the next step by 42%. This means amputees can put less effort into resisting gravity as they descend and gives them a sense of stability and support as they walk downhill.
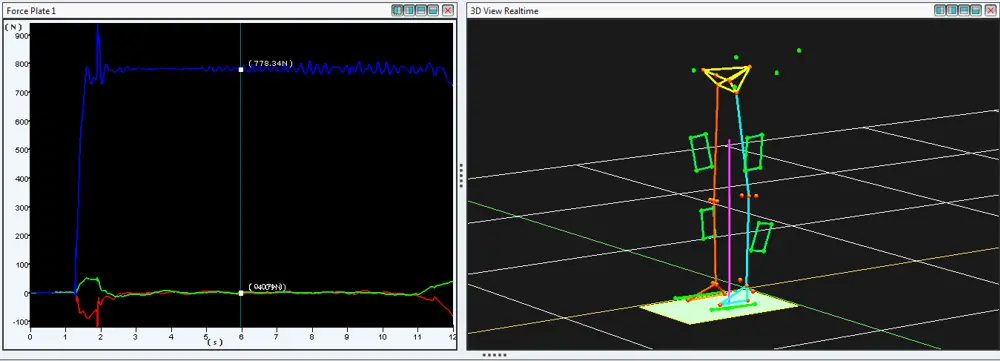
During development of the Linx system, a 3D motion capture system was used to measure lower-limb joint kinematics. Inverse dynamics methods (a process of calculating kinetic information) were used to quantify hip power reduction during movement and balance while standing with equal loading on an incline
However, when walking uphill, the damping at the ankle might be increased to absorb some of the energy but reduced at the knee so the springs can produce the right level of energy to take a step upwards. The result is that the amputee feels like they are being assisted up the slope by the limb.
In 2010, the company introduced the first hydraulic ankles; later on, these were given their own microprocessor to control the amount of energy they could absorb and release. For an above-knee amputee wearing both an artificial knee and ankle, the limbs would contain two ‘brains’ that each independently controlled the movement of each joint. However, the Linx is the first prosthetic limb to integrate the control of the knee and ankle together and produce a far more natural movement.
By combining these technologies, Blatchford believes it has been able to reduce by half the amount of extra energy a person wearing a prosthesis needs to expend to compensate for the lost limb. For example, the first microprocessor-controlled knee reduced energy expended by the wearer by 25%. Adding a microprocessor to the ankle reduced it by a further 18%, while integrating the control of both joints with a single processor in the Linx took it down by another 8%.
The Linx limb system has also been designed so that it will automatically enter a standing mode when the wearer remains still for longer periods of time. In tests it was found that the combination of stiffening both the foot and knee was most beneficial to reduce strain on the amputee. However, locking the ankle too early could be detrimental to stability and posture, so the Linx algorithm waits until the limb reaches a ‘steady state’ before stiffening up to provide support.
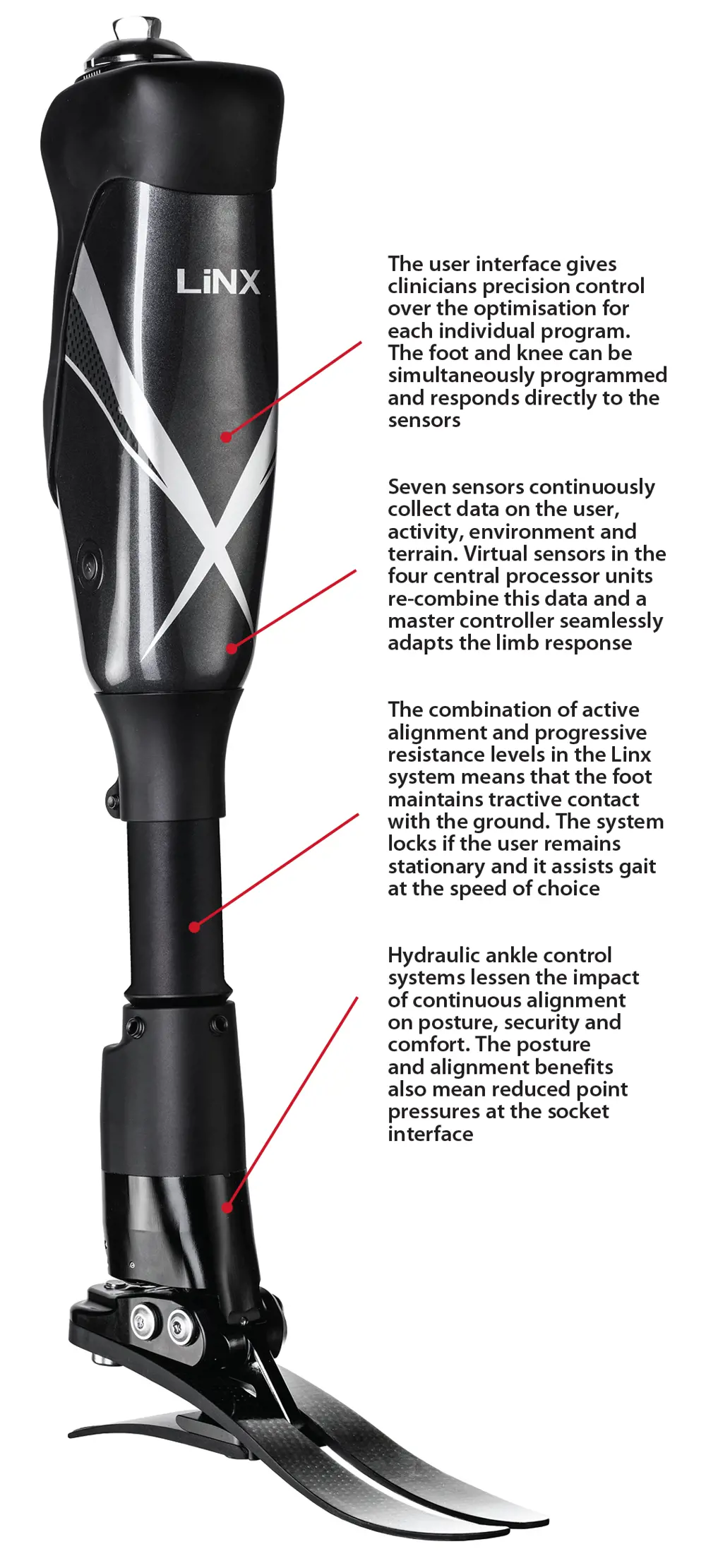
The Linx system fluidly provides physiological motion based on biomimetic principles of gait and posture. The master control unit coordinates the responses of the whole system to achieve smooth interaction between the system parts © Blatchford
Smart technology
The system is designed so that it can be fitted to a wide range of patients of different size and weight. Once fitted, the Linx’s central computer is programmed by a clinician so that it learns how the wearer walks naturally and adapts accordingly. This is done via a Bluetooth connection to a desktop program that shows in real time what the sensors are picking up as it detects the wearer’s natural speed and movements. A smart motion-integrated intelligence algorithm then calibrates the limb automatically in one simple step as the knee and the foot sensors ‘talk’ to each other, causing the limb to adjust more than 2,000 times a day to adapt to the environment. Previous prosthetics would require each set to be calibrated in turn in a lengthy process that would often require repeat adjustments.
An obvious approach might have been to actively power the limbs with actuators and hydraulics that propel the prosthesis, such as real muscles do. However, during development it was found that with the motors and batteries needed to power and drive them in this way, the limbs became too heavy. This extra weight would also make the leg harder to control as it swings and cancels out the extra power provided by the motors. Ultimately, a motorised prosthetic leg seemed unnecessary as the wearer can provide energy with each step as their weight pushes down onto the limb.
Blatchford developed the limb system’s onboard batteries so that they would provide enough power for several days, while the limb’s weight is kept to around two kilograms, less than a quarter of the weight of an average human leg.
Changing lives
The first Linx limb systems were manufactured in April 2015, and more than a year later there are now around 300 amputees wearing and using the Linx worldwide, mostly in the USA and Norway. However, at the cost of £25,000, the limb currently remains mostly outside NHS budgets.
Jack Eyres, a personal trainer from Bournemouth who had his right leg amputated at age 16, have found that with Linx they are now able to take part in activities that would never have been possible for them in the past
Some people, such as Jack Eyres, a personal trainer from Bournemouth who had his right leg amputated at age 16, have found that with Linx they are now able to take part in activities that would never have been possible for them in the past. Living close to the sea, Mr Eyres is able to hike along the uneven cliff tops near his home, something that he would have avoided in the past. He is also able to train as a boxer, using the Linx limb to keep himself steady as he throws punches into the punchbag.
Constant innovation
For Blatchford, this is just the start of a new era of prosthetic limbs that contain integrated, intelligent control but the goal of creating limbs that are as good as the real thing still remains some way off. The company is already working on the next step of integrating the whole leg so that the prosthesis becomes more a part of the body, and is working to improve the interface between the residual stump and the prosthesis, which will be a key aspect of any new designs. New liners that reduce sweating and enhance comfort will mean that amputees can wear their prosthesis for longer and with ease, and Blatchford wants to use this to integrate the machine and the human together. Initially, it may mean that the wearer can get feedback on the skin of the residual limb about what the prosthesis is doing, such as tiny electrical signals from sensors around the prosthesis that could stimulate the skin to help the amputee ‘feel’ the ground beneath them.
The company is already working on the next step of integrating the whole leg so that the prosthesis becomes more a part of the body
Beyond this, Blatchford is looking at potentially connecting the prosthesis to the nerve endings in the residual limb so those sensations can feed directly to the brain. It could ultimately lead to limbs that respond intuitively while giving the wearers a sense that they control it. With an ageing population and many people likely to live until they are close to 100, the need for a prosthesis that can let amputees go about their lives independently and maintain the lifestyle they want is crucial. Linx is a step towards that goal.
***
This article has been adapted from "Intelligent prosthetics", which originally appeared in the print edition of Ingenia 68 (September 2016).
Contributors
Richard Gray
Author
Professor Saeed Zahedi OBE FREng has been Technical Director at Blatchford for more than 10 years. He has over 40 years of experience in prosthetic innovation and is currently Vice Chairman of the UK delegation of the International Society of Prosthetics and Orthotics. Professor Zahedi has authored more than 125 papers, developed 35 patents and has won a number of awards, including a Special Commendation in the Prince Philip Designers Prize and a British Healthcare Trades Association lifetime achievement award.
Keep up-to-date with Ingenia for free
SubscribeRelated content
Health & medical

A gamechanger in retinal scanning
2006 MacRobert Award winner Optos rapidly became a leading medical technology company and its scanners have taken millions of retinal images worldwide. There is even a display at the Science Museum featuring the Optos development. Alastair Atkinson, of the award-winning team, describes the personal tragedy that was the trigger for the creation of Optos.

Kidney dialysis
Small haemodialysis machines have been developed that will allow more people to treat themselves at home. The SC+ system that has been developed is lighter, smaller and easier to use than existing machines.

Engineering polymath wins major award
The 2015 Queen Elizabeth Prize for Engineering has been awarded to the ground-breaking chemical engineer Dr Robert Langer FREng for his revolutionary advances and leadership in engineering at the interface between chemistry and medicine.

Blast mitigation and injury treatment
The Royal British Legion Centre for Blast Injury Studies is a world-renowned research facility based at Imperial College London. Its director, Professor Anthony Bull FREng, explains how a multidisciplinary team is helping protect, treat and rehabilitate people who are exposed to explosive forces.
Other content from Ingenia
Quick read
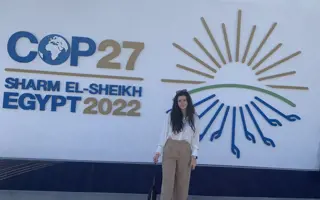
- Environment & sustainability
- Opinion
A young engineer’s perspective on the good, the bad and the ugly of COP27
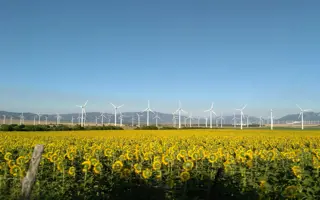
- Environment & sustainability
- Issue 95
How do we pay for net zero technologies?
Quick read
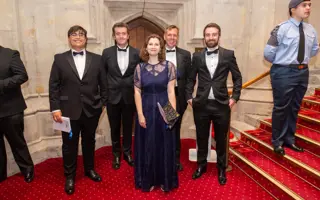
- Transport
- Mechanical
- How I got here
Electrifying trains and STEMAZING outreach
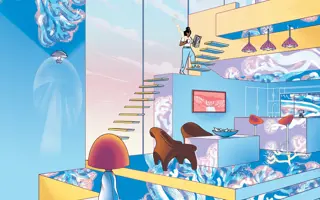
- Civil & structural
- Environment & sustainability
- Issue 95