
How engineers are fighting microplastic pollution
Did you know?
🔬 Minuscule plastic pieces
- Microplastics are fragments of any type of plastic smaller than 5 millimetres
- Most microplastic particles originate from larger plastic objects breaking down in the environment, with 35% shedding from synthetic textiles
- There are also even smaller plastic particles called ‘nanoplastics’. These are between 1 nanometre and 1 micrometre wide – at least an order of magnitude smaller than the width of a human hair
7 May 2024 marked the 20-year anniversary of when marine biologist Professor Richard Thompson coined the term “microplastics”. Now, scientists estimate that the ocean contains a “growing plastic smog” of over 170 trillion microplastic particles, with the extent of the harm it is causing marine organisms still not fully known. Meanwhile on land, scientists are urging further study on microplastics’ possible harms to human health.
Further estimates from researchers suggest that 35% of microplastic particles from this oceanic smog are shed from synthetic textiles during washing, and another 28% erode from car tyres into road run-off. These are just two of the pathways that microplastics can take into wastewater.
When wastewater treatment plants are in good working order, they filter out the majority of microplastics from treated water. However, when untreated wastewater overflows into UK waterways – a risk during storms – microplastics can spill out along with the sewage.
Even when everything is functioning as it should, microplastics wend their way into sludge, the sterilised by-product of sewage. Sludge is spread on farmland as a fertiliser and researchers believe it carries a volume equivalent to 20,000 bank cards of microplastics into agricultural soil each month. The smallest of these particles, called nanoplastics, can be taken up into the roots of fruit and vegetables, while microplastics on the surface are in danger of being swept into rivers through agricultural run-off. Unfortunately, separating microplastics from sludge is not a straightforward process (see box ‘Microplastics in sludge’).
Microplastics in sewage sludge
Why it's so hard to prevent microplastic particles in our wastewater reaching the environment
Conventionally, there are several steps in the water treatment where sludge and other bits of solid material are filtered, adsorbed and settled from treated water.
It’s one thing separating water from solid organic matter, and with it any microplastic particles, during wastewater treatment. Sludge, however, is “sticky and messy,” explains Dr Tom Bond, Senior Lecturer in Civil and Environmental Engineering from the University of Surrey. “Anything in the sludge is going to be difficult to filter out … The plastic fibres or particles would aggregate with the organic parts of the sludge.” Tom also cautions that other pollutants, especially metals, can stick to microplastics during sewage treatment, with the risk of them building up in ecosystems and in people.
While wastewater companies do treat sludge before it is applied to farmland, the focus is on removing water, so that it is easier and cheaper to transport, and ensuring it is free of pathogens. “It’s not the main concern of the wastewater companies to try and remove the plastics,” adds Tom. One reason for this is that plastic pollution is not yet regulated in sewage. This means there’s no regulatory driver for wastewater providers to filter out microplastics from sludge or the liquid component of sewage.
The obvious solution is to reduce plastic waste. While this is a massively complex ongoing challenge, one way that engineers are aiming to prevent microplastics from entering our waterways is by developing technologies to physically trap or break down the particles in our wastewater.
Mechanically trapping plastics
We are trying to solve the problem of environmental microplastics,” says Jess Middlemiss, Chief Technology Officer of Bristol-based engineering company Matter. Matter has developed a filter that mechanically captures microplastics to prevent them from getting into wastewater. Its first product fits to household washing machines, but the team is working on scaled up versions of the technology for wastewater and other industrial applications.
Jess explains how back in 2017, the company’s founder and CEO, Adam Root, who is a keen scuba diver, set his sights on the issue after seeing the problem of microplastic pollution firsthand. At the time, he was designing consumer products at Dyson, so decided to use his know-how to create a filter that could capture microplastics directly from washing machines. Armed with a £250 grant from The Prince’s Trust, he built a prototype microplastic filter and tested it with a bucket, an old washing machine and a shredded-up pair of pants.
It worked, and seven years later, Matter has expanded to a firm of 40 and last year secured almost £8 million in investment. Its washing machine filtering system, dubbed ‘Gulp’, has gone through many iterations of feedback with washing machine manufacturers and the team expects it to hit the shelves next year.
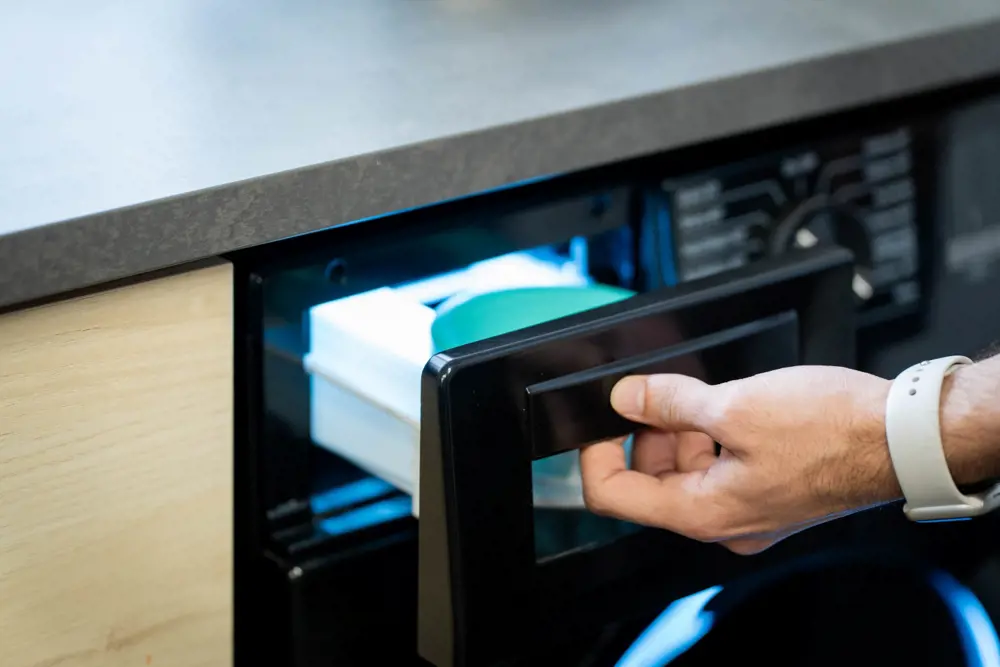
Matter’s first domestic-scale technology fits into the washing machine drawer and captures fibres in a mesh © Matter
A self-cleaning filter for washing machines
Like most types of conventional filter, the one inside Gulp captures fibres in a mesh, but the water flows towards it at an angle (rather than at right angles). This allows it to capture material even smaller than the 0.07-millimetre-wide holes in the mesh, including fibres as small as one micrometre wide and 10 micrometres long.
Unlike other filters, however, it is self-cleaning. Normally, such filters tend to become blocked over time and owners have to intervene to change the cartridges, to be either recycled or sent to landfill. When Gulp’s sensors detect that the mesh is full, it flushes already-filtered water back towards the mesh to join the flow of incoming water from the dirty side (with a small power draw). Jess describes it as operating like rapids in a river, where trapped fibres “get blown back into the fast-flowing stream of fluid”. This fluid flow eventually sweeps the collected fibres – resembling wet lint – into a capture area, which must be emptied every 15 washes on average.
In a perfect world, this “wet lint” would be recycled. But in reality, it is often made up of a real mixture of materials. “I, for one, will collect a lot of dog hair in [my Gulp] because I’ve got a very sheddy Labrador,” says Jess. “I’m not sure how useful people would find dog hair-infested, mixed-material lint, if I’m honest.” For now, it’s destined for the bin. However, Jess explains that this is significantly better than it continuing to go into water systems, because landfill sites are bunded (sealed by a wall that prevents material from escaping). “The escape of microfibres from a landfill is much, much lower than if it’s going into water systems or if it’s landing straight on farmland.”
While this is a definite improvement, it relies on every washing machine being fitted with a Gulp. Even just in the UK, that’s already about 27 million washing machines. In the coming years, there will likely be legal requirements for new washing machines to come with built-in filters – something that France has been pushing hard for. But for older models, where the owner has not installed the add-on, microplastics will still be entering wastewater.
Scaling up to wastewater and textile manufacturers
With this in mind, Matter is collaborating with wastewater treatment companies, whose microplastics footprint is much larger than the individual washing machines in people’s homes. “We always had an eye on the fact that it could be possible at a much larger scale,” Jess explains. “You have to choose one thing to focus on first when you’re a small startup, and it was easy for people to get the idea that you could put a filter on a washing machine.” The team was careful to prove the filter worked at a larger scale before patenting it, building a proof-of-concept device Jess informally describes as “the Mega Gulp” at its Bristol facility.
That’s not to say scaling has necessarily been easy. “Scaling any technology always comes with challenges,” says Jess. It is, she says, like baking a cake. “If you triple the cake recipe, you can’t bake it for the same amount of time. You need to adjust the cooking times; you need to adjust the temperatures.” For Matter, the process has involved a lot of computer-based simulation, but Jess emphasises “there is absolutely no substitute for physical testing.”
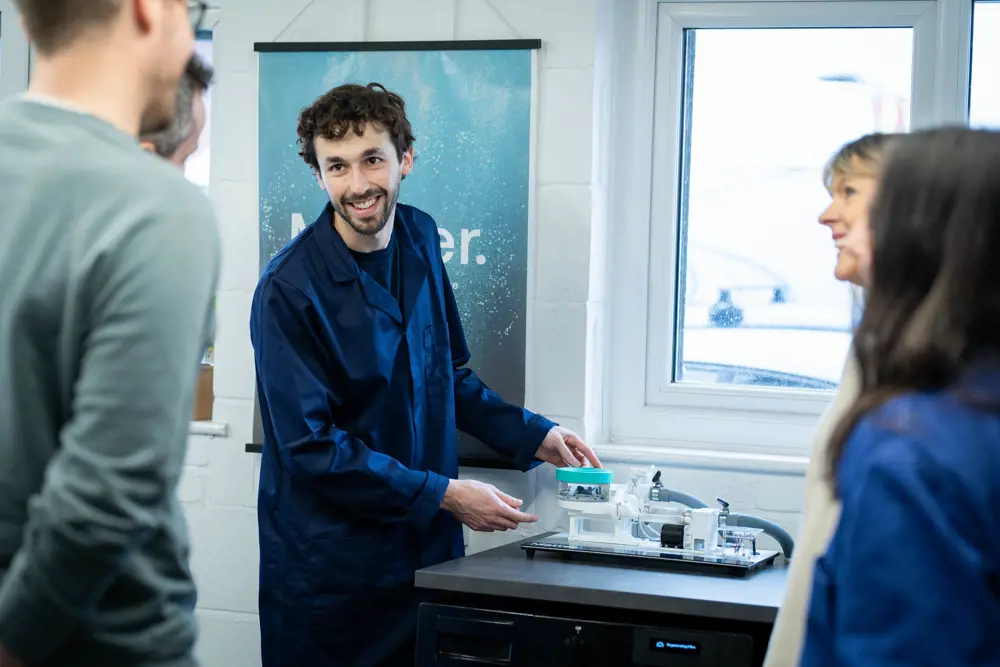
Matter is working with wastewater treatment companies and textile manufacturers to incorporate filters into their processes © Matter
At the moment, Matter is helping one wastewater company map their facility and work out where the filter might be applied to capture the microplastics. “They know that the microplastics end up in their sludge, and therefore it must be coming into their facility,” she explains. Matter’s target for wastewater facilities is a filter that can cope with almost 60 times more water than for a home washing machine, with 700 litres passing through a minute – as much as a million litres a day.
Matter has other collaborations underway with textile manufacturers – another significant source of microplastic pollution. Jess explains that as much as 2% of input materials sheds during manufacturing: the equivalent of one in every 500 T-shirts lost as microplastic fluff. Annually, this could equate to tonnes of material reclaimed in Matter’s filters.
What is especially interesting about this application is that wastewater from these factories has a much more controlled composition than that of a home washing machine. “If you’re in a polycotton factory, you’re catching a mixture of polyester and cotton, whereas if you’re in my house, you’re catching cotton, polyester, nylon, acrylic, polypropylene, dog hair, plaster, dust, soil, et cetera,” Jess says.
“The escape of microfibres from a landfill is much, much lower than if it’s going into water systems or if it’s landing straight on farmland.”
Jess Middlemiss, Chief Technology Officer, Matter
The plan is to recycle the reclaimed material, with the help of partners specialising in materials reuse and emerging recycling technologies. Jess stresses that material recycling technology is not Matter’s area of expertise. “We want to be part of this big circular economy ecosystem where we catch the material and then somebody else turns it back into monomers or processes it in a way that it can be reused as granules, then sells it onto somebody else who uses it.”
The star player in this ecosystem might just be organisms too small for us to see, and the tools they’ve honed over generations of evolution.
Can microbes and enzymes eat microplastics?
At Imperial College London, synthetic biologist Dr Jose Jimenez and his team are searching for bacteria that will grow on – and break down – plastics.
In the wild, bacteria can divide (reproduce) in as little time as a few hours. This means they can evolve quickly, allowing them to adapt to whatever food sources are at hand. So far, they’ve adapted best to the plastic polyethylene terephthalate (PET). The most famous bacteria that does this – Ideonella sakaiensis – was discovered in 2010, breaking down PET at a Japanese recycling facility.
The many types of plastic
♻️ And are they recyclable?
- Polyethylene terephthalate (PET) is the plastic that makes up polyester clothing; it is also the plastic normally used for soft drinks bottles, for example. It is easily recycled.
- High density polyethylene (HDPE) is used for packaging applications, and also easily recycled.
- Polyvinyl chloride (PVC) is tough and often used for things such as drainpipes and packaging but is rarely recyclable.
- Low density polyethylene (LDPE) is flexible and found in films and plastic vegetable bags. It is recycled at supermarkets.
- Polypropylene is often used for bottle caps or containers that hold hot liquid and is easily recycled.
- Polystyrene is often used in takeaway containers and is very hard to recycle.
Source: London Recycles
After discovering another promising candidate degrading the waxy coatings of leaves in compost with a special enzyme, scientists engineered it in the lab to break down PET instead. In April, French biotech company Carbios opened a facility that will break down 50,000 tonnes of PET a year with this enzyme. It works by breaking down PET into two constituent chemical components (called monomers), ethylene glycol and terephthalic acid. These are then purified and turned into virgin-quality PET.
To tackle such vast quantities of waste, the company purifies an enzyme extract from microbes grown in a reactor. As Jose explains, if you were to use microbes, there would be a lower concentration of enzyme, and thus a slower rate of plastic breakdown. This is one reason why Ideonella is not yet being used at this scale.
However, we don’t yet know how well this enzyme can work outside of carefully designed conditions such as in Carbios’ bioreactors. Jose cautions that conditions in wastewater treatment plants could be very different, including the pH, concentration of common ions in wastewater such as ammonia and phosphates, and temperature, too. He explains that although being exposed to higher temperatures could make the enzyme work faster, it could stop working if it’s too high. “It’s key to determine [which] enzymes are the most promising in real-world conditions of wastewater treatment,” he says.
Microbial matters
In his own work, Jose is exploring engineered microbes. As microbes already play several key roles in sewage treatment, it is not too much of a stretch to imagine that engineered plastic-eating bacteria could join the party.
One advantage of the microbial approach is that it would save in the costs and materials associated with producing and purifying enzymes. However, an important caveat is that the mixture must be sterilised afterwards because regulations do not allow genetically modified bacteria to be released into the environment.
After discovering a promising candidate degrading the waxy coatings of leaves in compost with a special enzyme, scientists engineered it in the lab to break down PET instead.
Jose is developing bacteria that degrade both the PET and its by-products. But his team is not using Ideonella, which, he says, is difficult to grow in the lab and genetically engineer. Instead, they are taking the enzymes they want from Ideonella and other organisms and putting them into a microbe that naturally consumes the monomers for energy. They did not have to travel far to find such a microbe: in the garden on campus, they isolated a strain that can feed on terephthalic acid and ethylene glycol. Ultimately, they plan to engineer it to upcycle the monomers into more sustainable chemicals and materials.
There’s still a long road ahead: studies suggest PET comprises about 11% of microplastic particles. What about the other 89% of microplastic particles? “Every plastic is different, and some are much harder than others,” says Jose. “Pretty much everything that you see in the news … pretty much everyone is going to be doing PET. All of them are hard, but that’s the easiest one.”
Jose’s group is also exploring how to break down a family of plastics called the polyolefins. These include polyethylene, one of the most widely used plastics that’s mainly used for packaging, and polypropylene, a rigid plastic used to make items such as luggage and car dashboards. “With the polyolefins, it’s really difficult. But it’s really difficult by any method that you can think of,” says Jose, referring to nascent chemical recycling approaches. (Critics say chemical recycling approaches are energy-intensive and create hazardous pollutants.)
In the hopes of meeting this challenge, the group is looking further afield than Imperial’s back gardens. One of its collaborators, from the University of Northumbria, has brought one bacterial species consuming polyethylene for growth back from a recycling facility in Abu Dhabi. Other research groups all over the world are searching for similar microbes in the wild.
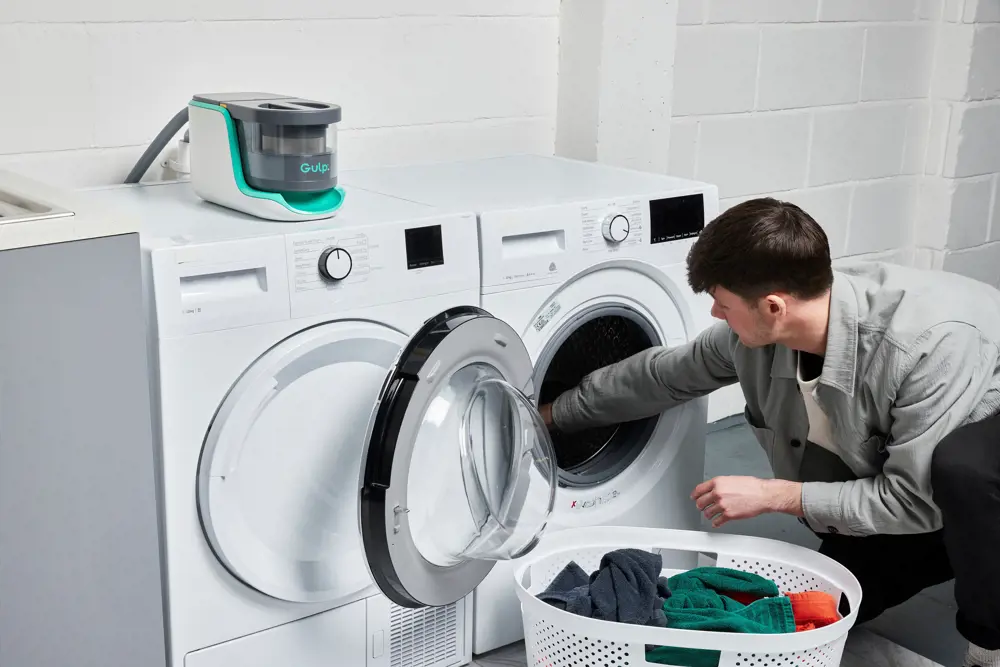
Users will be able to retrofit the Gulp technology on older washing machine models © Matter
Changing our approach to plastic waste
In a briefing paper in February, Jose and colleagues at Imperial set out recommendations for how microbes can successfully be used to combat microplastics in water and soil. Along with improving ways of measuring quantities of microplastics in the environment and working out what safe concentrations are, the authors argue microbiological approaches must be explored, feasibility tested, and proved in water treatment processes.
One of the Imperial team’s final takeaways, however, was the importance of tackling microplastic pollution at source, giving microplastic fibre filters in washing machines – such as Gulp – as an example. Dr Tom Bond, too, agrees that separation at source is likely to be the easiest way to tackle the issue.
Clearly, there’s no silver bullet, with the scale of the problem being so colossal. In 2021, petrochemical companies produced six million metric tonnes of new plastic – 120 times more than Carbios’ facility can recycle in a year. So, while engineering solutions are vital, there’s a lot to be said for more carefully considering how we consume plastics.
The ‘godfather of microplastics’, Richard Thompson, recently reflected in The Conversation on the two-decade anniversary of his discovery, in a year where the world aims to reach a global treaty on plastic pollution. He urged “reducing global production of plastic polymers and ensuring any plastic items we do produce are essential, safe and sustainable”. For us as consumers, this means avoiding single-use plastics, consuming less in general, and where we can, stemming the flow of particles from our washing machines and choosing textiles made from natural materials. It will be an uphill battle, but one we must start as soon as we can.
Contributors
Jess Middlemiss studied materials science and engineering at Imperial College London. Her career has spanned aerospace, consumer goods and biopharma. She spent two years as Head of Operations at The Dyson Institute and is a Fellow and active volunteer for the Institute of Materials Minerals and Mining (IOM3). Jess, her husband and their two children are passionate about improving biodiversity on their six-acre smallholding and she enjoys making delicious food from whatever she can grow and forage. She also keeps bees.
Dr Jose Jimenez Zarco has worked on synthetic biology of bacteria as a postdoctoral researcher at Harvard University and the Massachusetts Institute of Technology, and as a lecturer at the University of Surrey. Jose is interested in the environmental applications of synthetic biology, such as turning plastic waste into valuable products.
Dr Tom Bond is a Principal Consultant at the Water Research Centre, an environmental consultancy based in Swindon. He is also a Visiting Senior Lecturer in the School of Sustainability, Civil and Environmental Engineering at the University of Surrey. His work is primarily concerned with engineering solutions to the impacts of hazardous pollutants, through investigating the underlying chemical pathways which define their fate in aquatic systems.
Florence Downs
Author
Keep up-to-date with Ingenia for free
SubscribeRelated content
Environment & sustainability
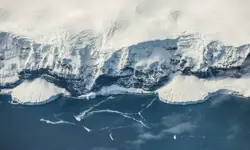
The extreme engineering behind life on an Antarctic station
Antarctica is one of the most challenging environments on the planet, but of enormous scientific importance to humanity. Technology and engineering is essential to enable the British Antarctic Survey's researchers to pursue their science effectively in this awe-inspiring landscape.

Recycling household waste
The percentage of waste recycled in the UK has risen rapidly over the past 20 years, thanks to breakthroughs in the way waste is processed. Find out about what happens to household waste and recent technological developments in the UK.

Upgrade existing buildings to reduce emissions
Much of the UK’s existing buildings predate modern energy standards. Patrick Bellew of Atelier Ten, a company that pioneered environmental innovations, suggests that a National Infrastructure Project is needed to tackle waste and inefficiency.

An appetite for oil
The Gobbler boat’s compact and lightweight dimensions coupled with complex oil-skimming technology provide a safer and more effective way of containing and cleaning up oil spills, both in harbour and at sea.
Other content from Ingenia
Quick read
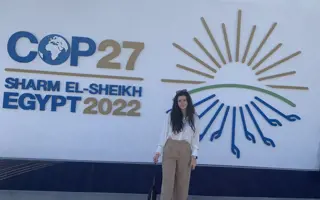
- Environment & sustainability
- Opinion
A young engineer’s perspective on the good, the bad and the ugly of COP27
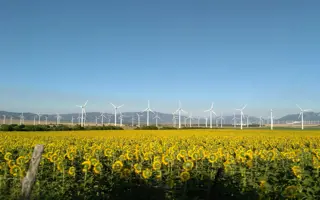
- Environment & sustainability
- Issue 95
How do we pay for net zero technologies?
Quick read
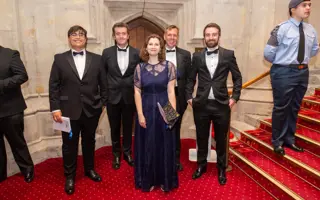
- Transport
- Mechanical
- How I got here
Electrifying trains and STEMAZING outreach
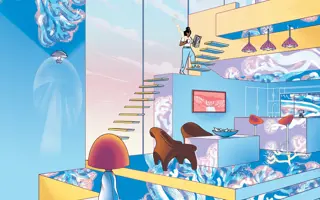
- Civil & structural
- Environment & sustainability
- Issue 95