
How a shrimp inspired nuclear fusion technology
Fusion power, a long sought-after solution to the world’s energy needs, offers effectively unlimited, clean and safe electricity generation that could stay on when the Sun goes down and the wind stops blowing. After many decades of international projects, in recent years dozens of startup companies have raised billions of dollars of private funding in the race to reach what sometimes seems like gold at the end of the rainbow. One of those companies is First Light Fusion (FLF), which has set its sights on using a novel approach to create energy by the fusion of atoms of deuterium (D) and tritium (T), the two isotopes of hydrogen favoured as fuel by fusion engineers.
The venture grew out of research by Dr Nicholas Hawker and Professor Yiannis Ventikos FREng at the University of Oxford. Hawker worked on hydrodynamic simulations of “shock-driven cavity collapse” – what happens when an external shock compresses a target. This laid the foundations for computer modelling to see if that shock-driven collapse would work as inertial confinement fusion (ICF).
What is fusion?
Fusion, the nuclear process that drives the Sun and the stars, combines two atomic nuclei in reactions that create a larger nucleus, throwing off energetic nuclear ‘ash’. In the case of earthbound power generation, the favoured fuels are deuterium (D) and tritium (T), two isotopes of hydrogen. In this case the ‘ash’ is helium (He) atoms and neutrons. Catching the neutrons and their energy can provide heat to run steam turbines and feed electricity to the power network.
For controlled fusion to happen in a pellet of deuterium and tritium (DT) the fuel must be at temperatures so high that it becomes an ionised gas, a mixture of nuclei and electrons, or plasma. Only then can the DT nuclei overcome their natural repulsion and come together fiercely enough to undergo fusion.
Conventional plasma containers are useless at those temperatures. They would cool down, or ‘quench’, and contaminate the plasma with unwanted materials that would rule out fusion. However, such is the electromagnetic nature of plasma, with its mixture of positively charged nuclei and negative electrons, that a carefully constructed magnetic field can bottle it up and keep it away from the container’s physical walls while fusion reactions take place.
The pursuit of fusion energy has historically involved building increasingly massive machines. The best known ‘magnetic bottle’ is the multinational Joint European Torus (JET) at the Culham home of the UK Atomic Energy Authority (UKAEA) near Oxford. In the final set of experiments before its shutdown earlier in 2024, JET set a record for the amount of energy created in a hot plasma, a mixture of D and T, the most likely fuel combination for fusion reactors.
Hawker took inspiration from the pistol shrimp. This small creature has a large claw that can click shut so quickly that the underwater movement creates a bubble and a shockwave in the water. As the bubble collapses, the shock wave heats the vapour in the bubble to tens of thousands of degrees, emitting a brief flash of light. The shrimp’s aim is that the loud noise from the shockwave will kill its prey.
When modelling the shrimp’s trick, and the interaction of the bubble and shockwave, Hawker decided to apply the computer simulations to a pellet of fusion fuel. Could a similar process to that clicked claw create a shockwave to heat fusion fuel to temperatures and pressures needed for nuclear fusion?
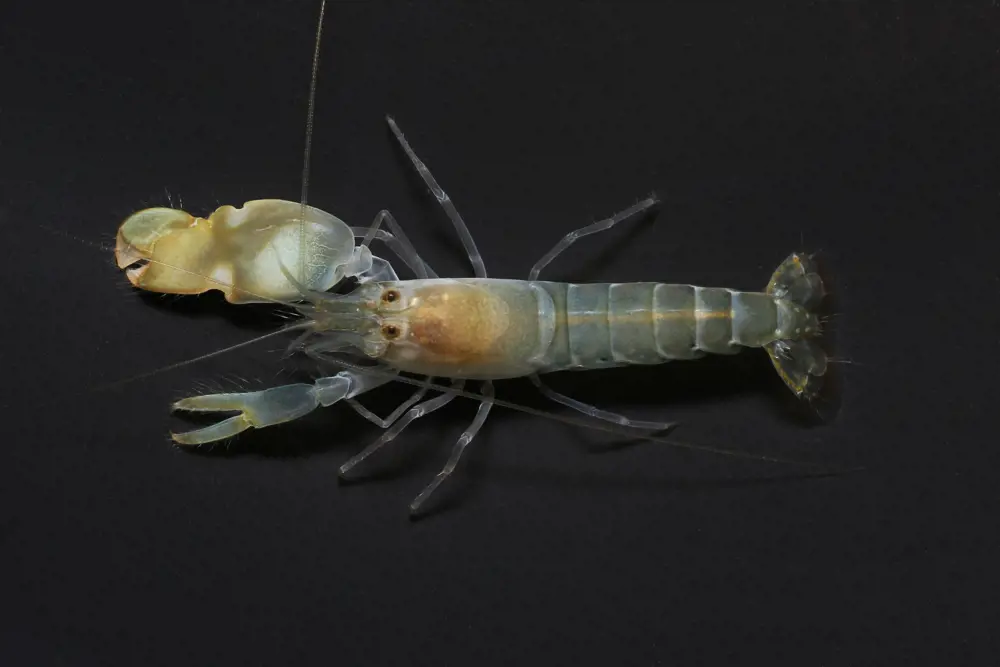
The pistol shrimp, which inspired First Light Fusion’s approach © Shutterstock
Fusion with impact
Set up in 2011, FLF is one of a handful of companies using a process known as ICF. FLF describes its variation of ICF as impact fusion. It starts with a small pellet of DT fuel embedded in a target, which implodes when it is smashed with enough energy. In the process, FLF’s targets are designed to work as amplifiers and to compress the fuel pellet from all sides until it reaches temperatures and pressures higher than those in the Sun.
The best-known example of ICF is the National Ignition Facility (NIF) at the Lawrence Livermore National Laboratory in California. Funded by the US Department of Energy and built at a cost $3.5 billion, the NIF – the world’s largest laser – officially opened in May 2009. It made headlines in 2022 when it reported that fusion reactions there had produced more energy than it took to heat and compress the fuel targets, one of the major benchmarks for ICF. The NIF uses 192 powerful laser beams as drivers, housed in a 10-storey building the size of three football fields, to blast tiny pellets of DT.
This was good news for FLF. As Hawker puts it: “Our approach leverages the same physics now proven by NIF but combines it with a unique approach that gets to a competitive cost point in a truly scalable manner.” FLF’s system doesn’t need a large array of lasers, just a single fast-moving projectile, launched by a driver at a carefully designed target.
FLF had already built two machines to test its target designs. One, dubbed the big friendly gun (BFG), uses gunpowder to aim a projectile at fuel targets. The second driver, called Machine 3, uses electromagnetic forces to launch a projectile at the fuel.
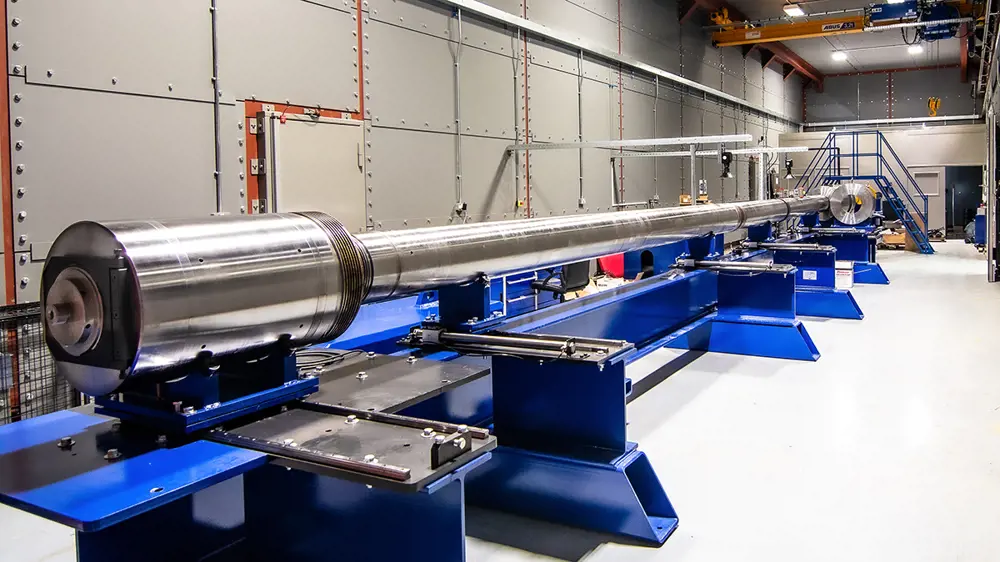
FLF tests its target designs with its big friendly gun (BFG). The first stage of the BFG pushes a piston that compresses hydrogen to high pressures, which powers the second stage projectile launcher. This launches a projectile at around 60 km/second at a target, about a millimetre in size. The impact compresses the target, creating the extreme temperatures and pressures required for fusion © First Light Fusion
In November 2021, FLF achieved fusion on its BFG machine. To confirm that FLF had created genuine thermonuclear fusion, it enlisted the help of the UK Atomic Energy Authority (UKAEA). The UKAEA’s Culham Laboratory is the home of the Joint European Torus (JET), the best-known example of magnetic confinement fusion. It has a long history of diagnosing what goes on in fusion projects. Its researchers pored over FLF’s diagnostic systems and confirmed its claims.
FLF had planned to build an even bigger driver, but the positive results from NIF were a cue to change direction. Ryan Ramsey, Chief Operating Officer, says that as more results came in from NIF they asked themselves “Why are we doing this?”. FLF decided to concentrate on developing its ‘shock amplification’ approach to ICF.
The NIF concept isn’t practical for a power plant, says Ramsey. “You can’t have 192 penetrations into a reactor chamber.” Instead, FLF hits targets on just one side. The target itself then creates a shockwave that compresses the fuel from all sides. “The convergence is created completely within the amplifier,” says Hawker. On impact, the pellet itself pushes the fuel to fusion conditions.
When it comes to getting fuel into its targets, the company can draw on the previous experience with ICF. FLF can then put that inside its own amplifiers.
“The key technology for us is the target design,” says Hawker. It is, he says, “the secret sauce”. When it comes to building a power station, Hawker has compared ICF to an internal combustion engine: drop in a fuel target, hit it with a projectile, recover the energy, and keep repeating the process.
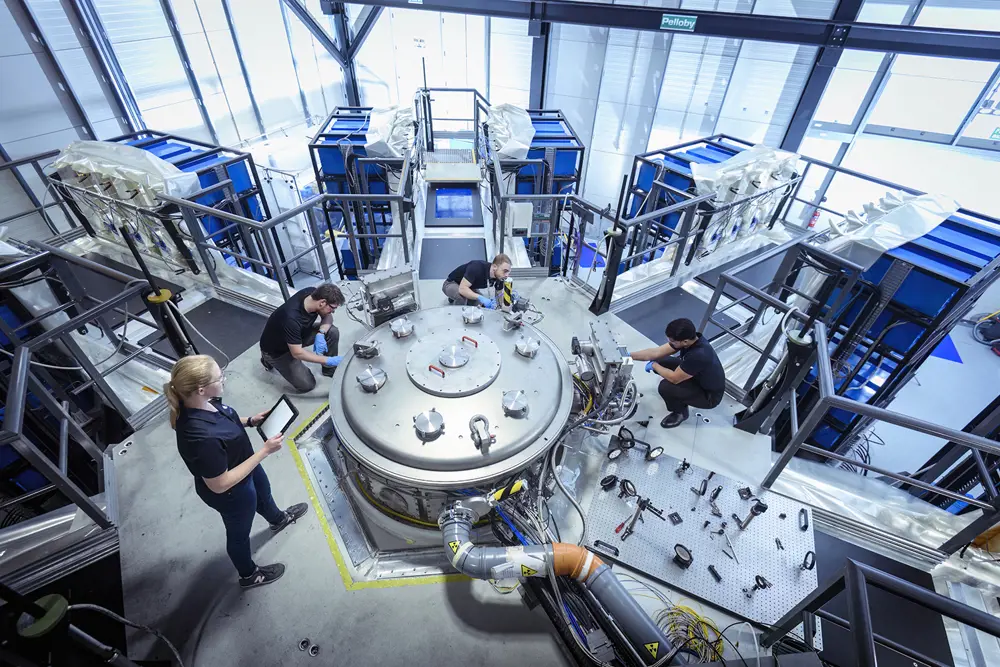
‘Machine 3’, built in 18 months at a cost of £3.6 million, stores electrical energy in banks of capacitors. It uses electromagnetic forces to launch projectiles at the hypervelocity speed needed to test fusion targets. The projectiles hits the amplifier at 20 km/second. The company describes this as “one of the largest pulsed power facilities in the world and the largest in Europe”. It is also the only one built specifically for fusion research © First Light Fusion
Test and amplify
Machine operated by Sandia National Laboratories in New Mexico in the US. The most powerful pulsed power facility in the world, the Z Machine can electromagnetically launch projectiles to higher velocities than any other facility.
FLF describes its approach to ICF as being “driver agnostic”. The driver just has to hit the target (and therefore the amplifier) hard enough.
Ramsey says with five different ICF driver technologies under development around the world, FLF’s approach could be relevant to all of them. Each driver will need different target designs, which is where the company’s expertise in accelerator modelling, computer simulations and target manufacturing come into play.
The modelling proved its power in February 2024 when measurements on the Z Machine broke the pressure record. FLF’s simulation predicted the pressure to within 2% of the measured result.
After keeping its computer modelling and simulation in house, mostly to protect this intellectual property, says Ramsey, the company is now preparing a cloud option to see if this can speed up the development and simulation of new drivers. “The cloud will give us significantly more computer power. We think this will make us quicker,” he adds.
For Ramsey, computing has been the game changer in amplifier design. Add machine learning and FLF can devise new amplifiers and analyse how they are likely to amplify the driver’s impact force.
FLF’s current business plan is to focus on designing amplifiers that others can use in their ICF reactors. To this end, the company is building a portfolio of patents on the design and production of amplifiers.
FLF’s amplifiers, cubes of about four centimetres, are made of “normal materials,” says Hawker. With model amplifiers to hand, the in-house precision manufacturing team can assess how easy it is to make new amplifier designs. As Ramsey puts it, there is no point in designing a great amplifier if you can’t make it.
The company’s idea is to design and validate amplifiers and licence production to specialist manufacturers who could make targets in the large numbers, perhaps thousands a day, that a reactor would need. To this end, FLF is investigating the manufacture of amplifiers with the support of the Advanced Manufacturing Research Centre in Sheffield.
Contributors
Dr Hawker's research into fusion began in 2007 as part of his master’s thesis at the University of Oxford. This work continued into a DPhil, where he performed hydrodynamic simulations of shock-driven cavity collapse.
Ryan Ramsey has a business background in energy, construction and offshore leadership. He has also led in the Royal Navy Submarine Service as captain of a nuclear-powered submarine and taught future submarine captains.
Michael Kenward OBE
Author
Keep up-to-date with Ingenia for free
SubscribeRelated content
Energy

Algae-powered architecture
An apartment block in Hamburg in Germany has been built that uses microalgae placed within its façade to generate heat and biomass. Jan Wurm, an associate director at Arup, was one of the chief designers of the energy system. He talked about the concept, execution and results from the world’s first photobioreactor.
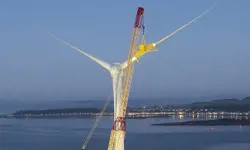
Digital hydraulics for wind energy and beyond
Research that has helped change the technology for harnessing wind energy has many other applications. The digital hydraulics system devised by Artemis Intelligent Power has received many accolades, the latest being the winner of the 2015 MacRobert Award.

New energy pioneers
London-based BBOXX supplies solar-powered battery boxes to customers in developing countries. Their remote monitoring and battery management system was one of the winners of the 2015 Bloomberg New Energy Finance Award.
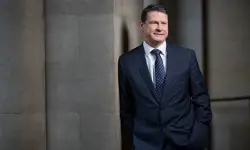
Energy with connections
When Steve Holliday FREng moved from the oil industry into energy distribution, the sector was seen as staid. In reality, during his years at National Grid, the sector became increasingly important as the need to tackle climate change led to a transformation in the UK’s energy mix.
Other content from Ingenia
Quick read
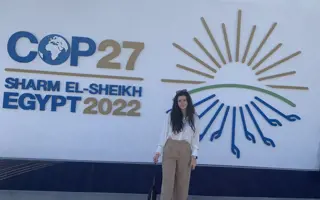
- Environment & sustainability
- Opinion
A young engineer’s perspective on the good, the bad and the ugly of COP27
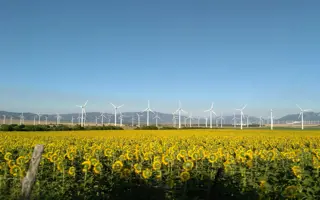
- Environment & sustainability
- Issue 95
How do we pay for net zero technologies?
Quick read
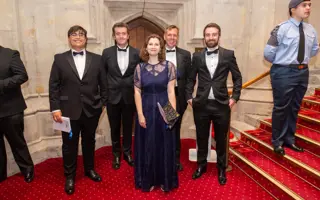
- Transport
- Mechanical
- How I got here
Electrifying trains and STEMAZING outreach
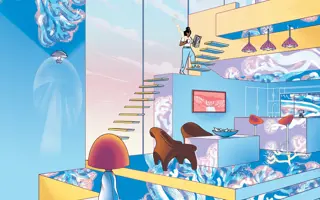
- Civil & structural
- Environment & sustainability
- Issue 95