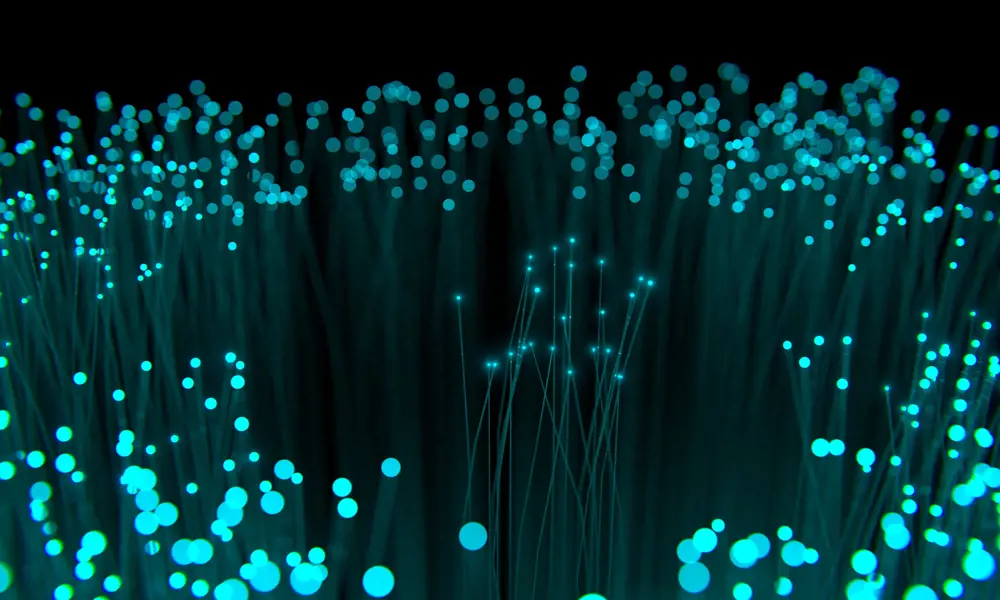
Hollowing out a future in fibre optics
Optical fibres are the foundation of the modern digital society. Since the first commercial cable was laid for the Dorset police in 1975, fibre optic communications has dominated telecommunications with estimates of around 325 million kilometres of fibre now being sold across the world every year.
The optical fibres in cables consist of thin strands of glass (around 125 micrometre diameter) surrounded by a thin polymer coating (around 250 micrometre diameter) and thicker plastic protective layers. These outer layers protect the fibres when they are in place and include, in some cases, metal armour to prevent external damage, for example from seabed disturbances and sea life.
However, the thin central glass strand is the important part for transmitting light. These solid glass strands transmit light via total internal reflection, which occurs at the interface between two materials of a differing refractive index. Light approaching the boundary from the higher-index region is totally reflected for all incident angles below a specific value (the critical angle). In the case of fibre optics any light that enters the fibre at or below this angle will be totally internally reflected along its length.
While ubiquitous, these solid-core fibres (essentially as first envisaged by the late Professor Sir Charles Kao KBE FREng FRS in the 1960s) have limitations. For example, the glass makes the light travel 30% slower than in air or a vacuum: this is how lenses bend rays of light and why solid fibres work at all.
Additionally, light travelling in solid glass leads to other unwanted effects, in particular so-called non-linear effects that cause the light to change its wavelength. In a system with closely packed wavelength channels these non-linear effects ultimately limit the achievable data rate of above 100 terabits per second.
When looking at their use for higher power laser delivery, such as for cutting and welding metal, solid fibre can become damaged as the power of the light increases. A very small amount of light is absorbed and scattered by the silica; at kilowatts of power, this small amount causes damage to build up and can result in complete destruction of the fibre.
Given the limitations of existing solid glass fibres, it has been no surprise that many research groups have begun developing and deploying a new generation of optical fibres with air rather than glass cores. This new approach is called hollow core fibre optics.
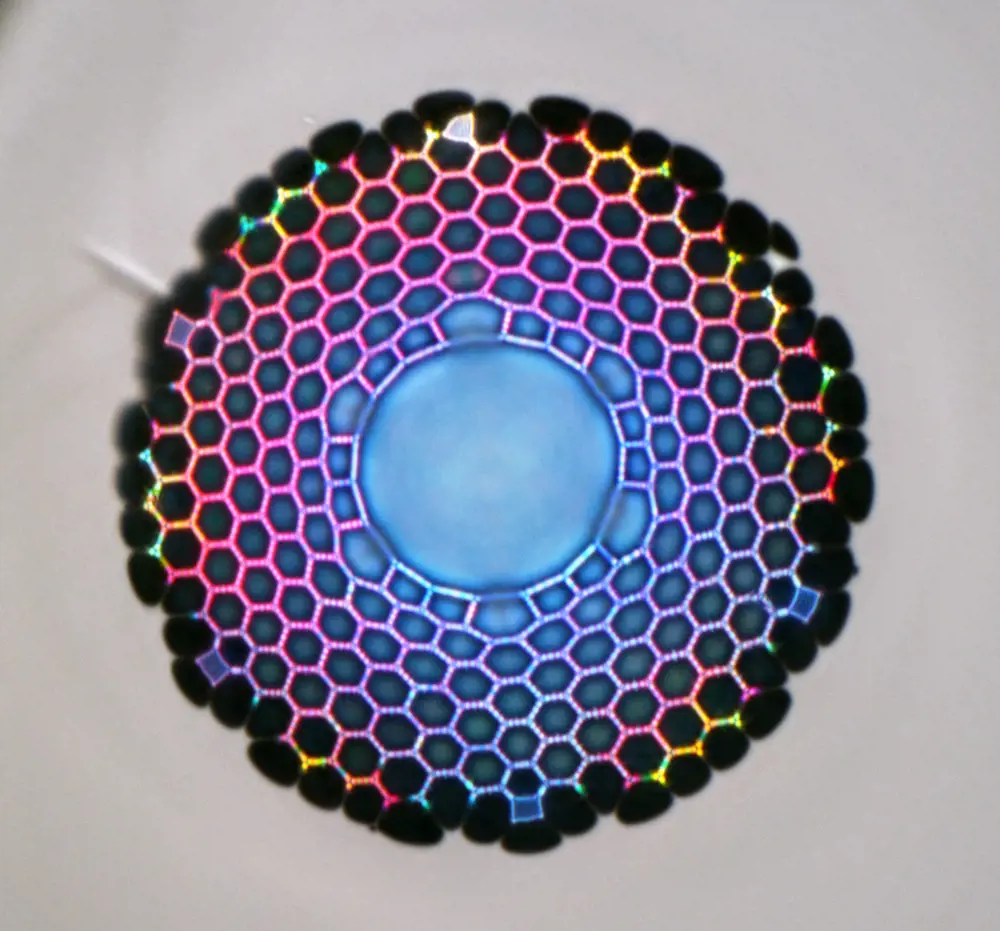
A photonic bandgap type hollow core fibre with a large central core and honeycombed cladding © Dr Seyed Reza Sandoghchi
Hollow cores in use
Hollow core fibres are at the cutting edge of fibre optic technology currently in development and, as a technology, are in their infancy. However, this has not stopped their rollout into applications previously dominated by solid fibre optics.
One of the biggest fibre optic markets is the telecommunications industry and it is an area where innovative new fibre designs can have great impact. A significant amount of the research and development has focused on this market with the goal of developing a low transmission latency, high bandwidth, low-loss hollow core fibre. There have been considerable advances in fibre performance and data transmission experiments over recent years, with key demonstrations of these characteristics. Data rates of more than 50 terabits per second have already been transmitted over lengths of hollow core fibre, illustrating their potential for high capacity data communications. Development of a fibre with a signal attenuation below that of current solid silica fibres
(0.2 decibels per kilometre (dB/km)) would allow for increased repeater spacings and improved system capacity. The lowest attenuation levels currently reported for a hollow core fibre are higher than the best solid silica fibres. However, recently the University of Southampton announced that it has produced a novel hollow core fibre design with a record low loss of 1.3 dB/km with clear scope for further improvement – at least theoretically to values well below 0.2 dB/km, which is the loss for silica fibres.
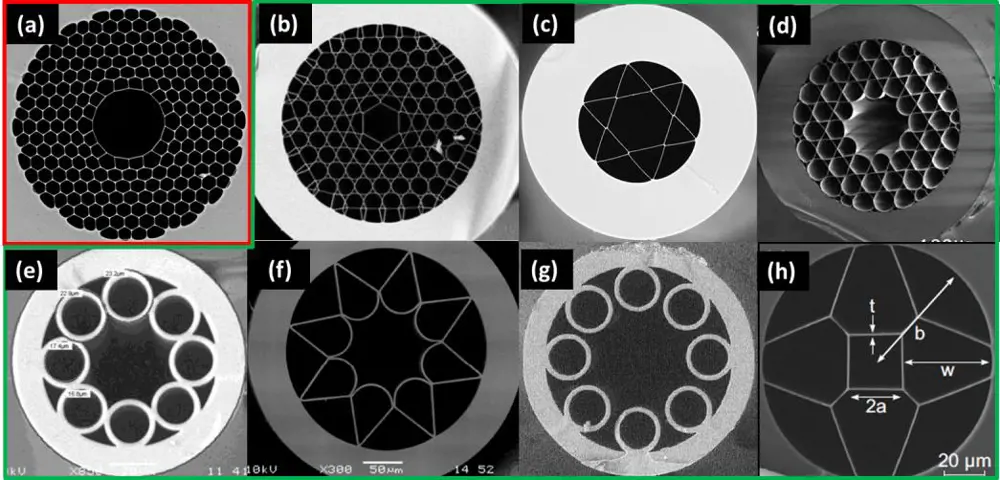
The range of hollow core fibre types available: a) Photonic band gap fibre; b to h) Various anti-resonant fibre designs (reproduced from Poletti F (2014) ‘Nested antiresonant nodeless hollow core fiber’, Opt. Express 22, 23807-23828)
Beyond telecommunications, hollow core fibres are also being applied to various sensing and laser applications. They offer several advantages as sensors from their easily bespoke structure, tolerance of high powers and easily accessed internal gas paths. Early in 2018, GE Global Research announced the development of a hollow core sensor to detect leaks in oil pipelines. This sensor design consisted of using a solid core fibre to transmit laser light along the length of a pipeline. At several points the light from the solid core is coupled out and into a short section of open-ended hollow core fibre. This open-ended fibre is mounted inside sampling points in the pipeline where it can be purged and pumped with samples of surrounding gas. The light travelling through the hollow core can then be interrogated by spectroscopy (the absorption and emission of light) at the other end of the solid fibre. Methane has a clear spectroscopic fingerprint, which can then be used as an indicator of leaks.
The fibres’ air-guiding properties also have an advantage in high-power laser delivery as the laser light is not travelling through glass but the hollow space in the core. An air-filled hollow core allows increases in power that can be delivered through a fibre, particularly for ultrashort pulses where the resulting high peak powers are a problem, caused by the dissipation of power into solid silica. In applications where ultra-high power is needed, it is possible to prepare a hollow core under vacuum rather than filled with air, allowing for an even greater level of power transmission for applications such as drilling and industrial materials processing.
How do they work?
Hollow core fibres appear very similar to existing solid optical fibres; they are made from a thin strand of glass of around the same thickness. However, whereas solid fibre central cores are made from solid glass, a hollow core fibre has a core formed by microstructured hollow tubes.
In solid fibres the light is guided within the glass core. If this core was simply removed, then light launched into the fibre would not totally internally reflect and any light entering would refract out through the walls. In hollow core fibres the position and size of the surrounding microstructure provides conditions whereby the light is optically nudged by these thin membranes (as determined by a large number of variables including thickness, geometry and refractive index of the glass tubes) to keep it within the hollow central region. There are two main types of hollow core fibre microstructure that allow light to be guided this way.
In both types the majority of the light travels in the centre of the hollow core and has very little interaction with the glass, making the light ‘air guided’ along the fibre
Hollow core band gap fibre (or crystal fibre) surrounds the hollow core with a structure similar to honeycomb and the critical parts of this structure are the nodes or junctions between membranes. These nodes create a structure that will not allow certain wavelengths of light to pass, trapping them within the hollow core in the middle.
In the second type, hollow core anti-resonant fibre, the critical parts are the membranes themselves. When the thickness of these thin (around a micrometre or less) membranes is tuned correctly they act to reflect a wider range of wavelengths of light. There are many different structural types of anti-resonant fibre with a variety of benefits for bandwidth and loss. For example, the nested tubular variety is getting a lot of attention because of a recent record-breaking result of 1.3 dB/km for hollow core fibres (compared to the previous record of 1.7 dB/km – a 25% improvement).
In both types the majority of the light travels in the centre of the hollow core and has very little interaction with the glass, making the light ‘air guided’ along the fibre (so called because of the air-filled core).
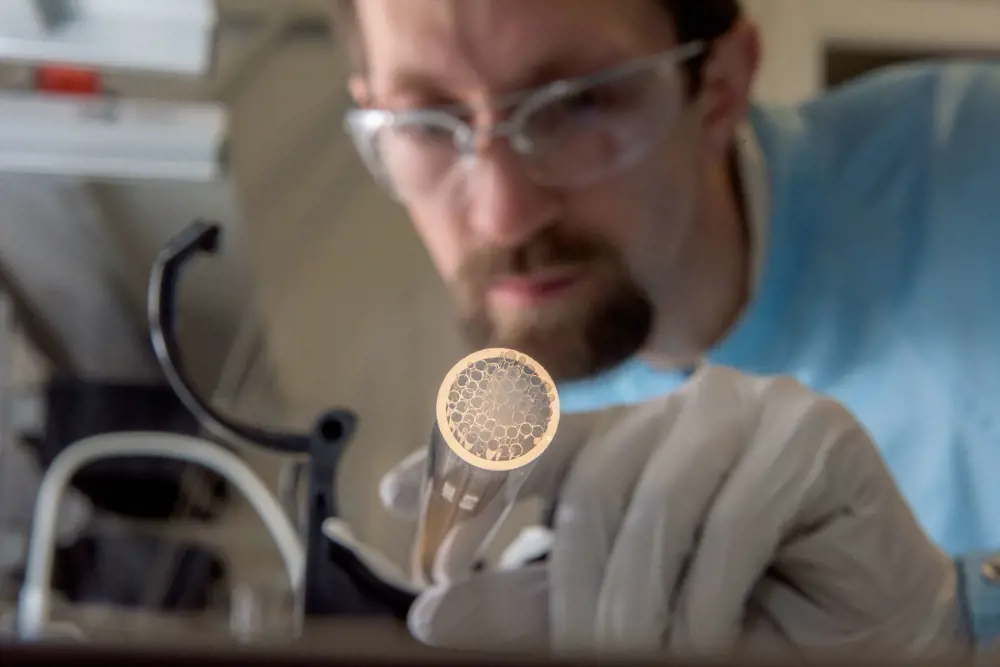
A cane preform being prepared in the Optoelectronics Research Centre lab in the University of Southampton’s £120 million cleanroom complex
Fibre optic cores
The production of hollow core fibre follows a similar approach to that of making solid core fibre, but with several additional controls over the final guiding structure. A typical hollow core fibre is produced in four stages: cane preform stacking, drawing the preform into a cane, construction of a fibre preform using cane and finally drawing this into fibre.
Cane preform stacking is where a large-scale version of the fibre is produced using capillary tubes. These typically have a diameter on the millimetre scale, and are about a metre in length. They are laid together in a capillary stack and inserted into a larger glass tube known as the stack jacket. A completed cane preform is typically around 25 millimetres in diameter and looks like a thick glass straw filled with intricate smaller glass straws.
Preparing a cane preform and positioning tubes into specific points to create the required spacing involves the use of various removable spacer rods, which hold each tube in the required position. This requires great precision and control as micrometre positioning errors can fatally effect the guiding properties.
The cane preform is then drawn down to form a cane that is similar to the final fibre but larger. The draw down process consists of pulling the cane preform through a furnace, which causes the glass to soften. As the preform is pulled it reduces to around 3 millimetres thick. During this stage the individual capillaries may be pressurised to allow for expansion or contraction of specific elements in the stack. This allows for some early control over the final fibre and splitting this in to two steps reduces the risk of problems such as movement, twisting or breakage of individual tubes.
Finally, the cane is inserted into a further glass jacket tube to form the final fibre preform, which is mounted at the top of a tower (known as the draw tower) that can be many floors tall. When the fibre preform is mounted, various elements are then pressurised using inert gas (either argon or nitrogen) and the fibre preform is attached to a gripping device, which can slowly move it up and down. During a fibre draw, the fibre preform is lowered into a furnace that heats it to around 1800°C. The first glass strands are manually pulled and attached to a tractor system that applies a constant controllable tension to the glass as it passes though the furnace.
As the fibre is pulled out of the furnace it passes through diameter monitoring equipment to allow feedback and variation of the draw speed, which in turn changes the diameter of the fibre produced. It also often passes through one or more coating dies, which uniformly coat the outside of the fibre with a protective polymer jacket. Finally, the fibre is spooled and ready for use. The intricacies and design of these fibres has only been possible through techniques learned from solid fibre drawing experience and the development of specialist glassware handling and drawing processes and facilities.
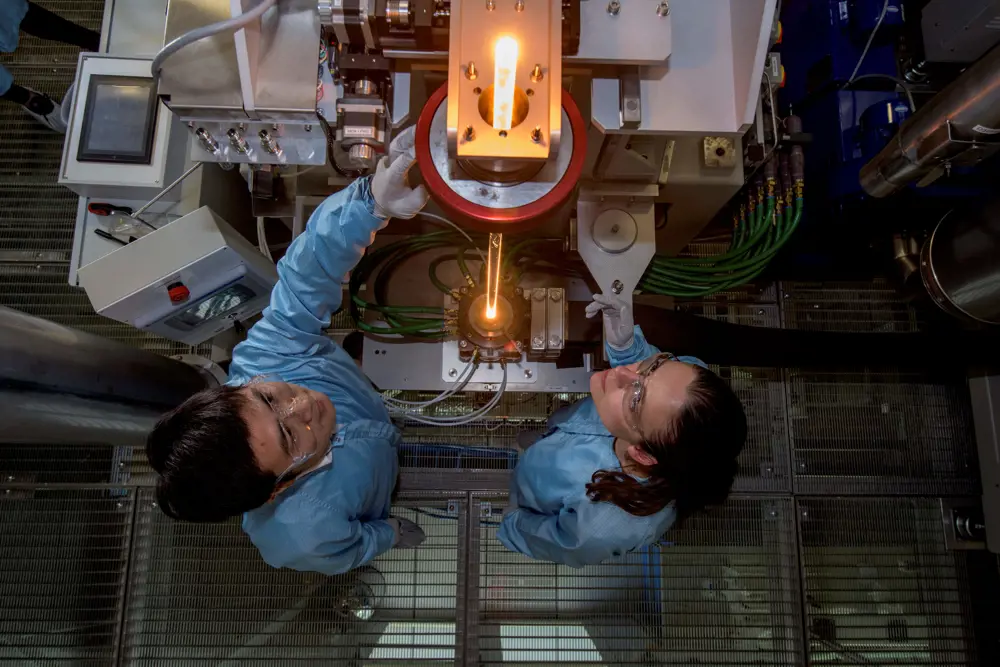
A fibre preform being fed into the furnace at the top of the fibre optic draw down at the Optoelectronics Research Centre fibre optic draw tower
Solving challenges
There are still several challenges to solve before wide-scale adoption can take place. The challenges include scaling up production of some of the more intricate designs and finding coatings that ensure that the fibres are as robust and flexible as their solid core counterparts. Previous work on coating and protection of solid fibres can help inform and facilitate rapid progress. The intricacies of the core designs are a unique problem to hollow core. Designing the stack layouts and then producing methodologies to achieve such layouts is one of the biggest challenges. However, as with solid core fibres these technical challenges are being solved alongside their commercial uptake.
In the last year, two large-scale initiatives focused on hollow core fibre have been launched: the Engineering and Physical Sciences Research Council awarded the University of Southampton £6.1 million for its AirGuide Photonics project, which works with 32 collaborating companies. Second, Southampton-based spinout company Lumenisity Ltd has recently been formed to help commercialise the technology, with a focus on telecommunications and data communication applications.
Anyone with an interest in telecommunications, 5G connectivity, high-power laser applications, fibre lasers and sensing should start looking at hollow core fibre as the future
Hollow core fibres are a technology that is poised to move from the lab into applications across the engineering industry. They are set to help solve some of the challenges and limitations of the current generation of solid silica fibre and expand fibre optics into new and exciting areas. While they are still evolving and developing, they are already showing significant promise. Anyone with an interest in telecommunications, 5G connectivity, high-power laser applications, fibre lasers and sensing should start looking at hollow core fibre as the future.
***
This article has been adapted from "Hollowing out a future in fibre optics", which originally appeared in the print edition of Ingenia 79 (June 2019).
Contributors
Dr Matthew Partridge is a cartoonist and writer at ErrantScience. At the time of writing, Matthew was a Senior Research Fellow at the University of Southampton. His work focused on the application of fibre optics to a wide range of real-world problems, from nuclear waste storage to medical diagnostics.
Keep up-to-date with Ingenia for free
SubscribeRelated content
Technology & robotics

When will cars drive themselves?
There are many claims made about the progress of autonomous vehicles and their imminent arrival on UK roads. What progress has been made and how have measures that have already been implemented increased automation?

Autonomous systems
The Royal Academy of Engineering hosted an event on Innovation in Autonomous Systems, focusing on the potential of autonomous systems to transform industry and business and the evolving relationship between people and technology.

Hydroacoustics
Useful for scientists, search and rescue operations and military forces, the size, range and orientation of an object underneath the surface of the sea can be determined by active and passive sonar devices. Find out how they are used to generate information about underwater objects.

Instilling robots with lifelong learning
In the basement of an ageing red-brick Oxford college, a team of engineers is changing the shape of robot autonomy. Professor Paul Newman FREng explained to Michael Kenward how he came to lead the Oxford Mobile Robotics Group and why the time is right for a revolution in autonomous technologies.
Other content from Ingenia
Quick read
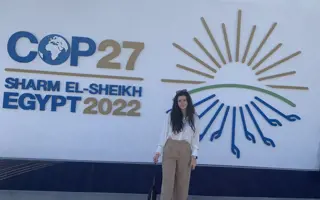
- Environment & sustainability
- Opinion
A young engineer’s perspective on the good, the bad and the ugly of COP27
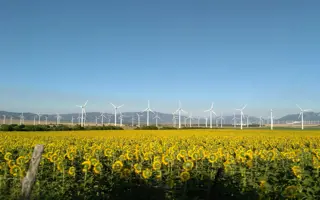
- Environment & sustainability
- Issue 95
How do we pay for net zero technologies?
Quick read
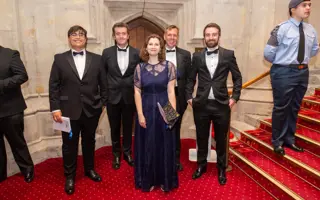
- Transport
- Mechanical
- How I got here
Electrifying trains and STEMAZING outreach
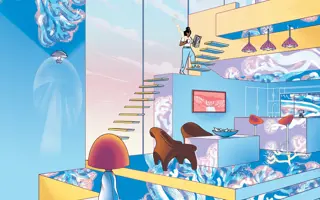
- Civil & structural
- Environment & sustainability
- Issue 95