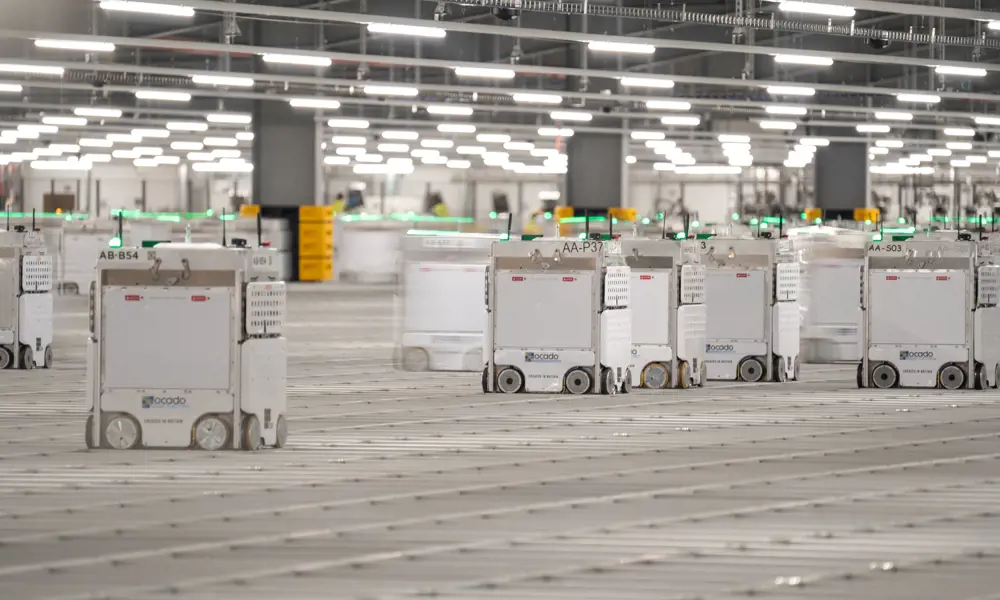
Hives of activity
Grocery shopping has always been an unwieldy process. Items are delivered by lorry on pallets to a supermarket warehouse, where they’re broken down onto smaller cages and then stacked onto shelves. Customers pick these items and place them into a trolley or basket before depositing them on checkout conveyors, packing them into bags, transporting them home, and putting them away.
The development of online grocery shopping helped to eliminate several steps from this inefficient process, but the remaining stages still relied on human labour. When Ocado debuted in 2000 as a specialist online grocery retailer, its founders recognised the efficiency of automation. The following year, it unveiled a Customer Fulfilment Centre (CFC) in Hatfield, which had automated as many of the picking and packing stages as possible.
While Hatfield remains one of the world’s biggest and most futuristic online grocery warehouses, it’s recently been eclipsed by a new facility in Erith. Measuring over 52,000 square metres and taking over three years to build, this CFC demonstrates how much of the grocery supply chain can be streamlined through investment in everything from swarm robotics technology to pioneering software modelling.
Scalable shopping solutions in unexplored territory
As Ocado’s Chief Technology Officer, Paul Clarke has played a key role in developing the world’s biggest online-only supermarket brand. He points out various inefficiencies in the traditional online grocery model: “With an average item price of £2, there is about 60p of margin to pay for the decant, storage, picking, packing and delivery to customers’ kitchen tables in one-hour slots. It was therefore a cornerstone of our founding vision that the only way to do online grocery delivery scalably, sustainably and profitably would be through the application of a huge amount of technology and automation.”
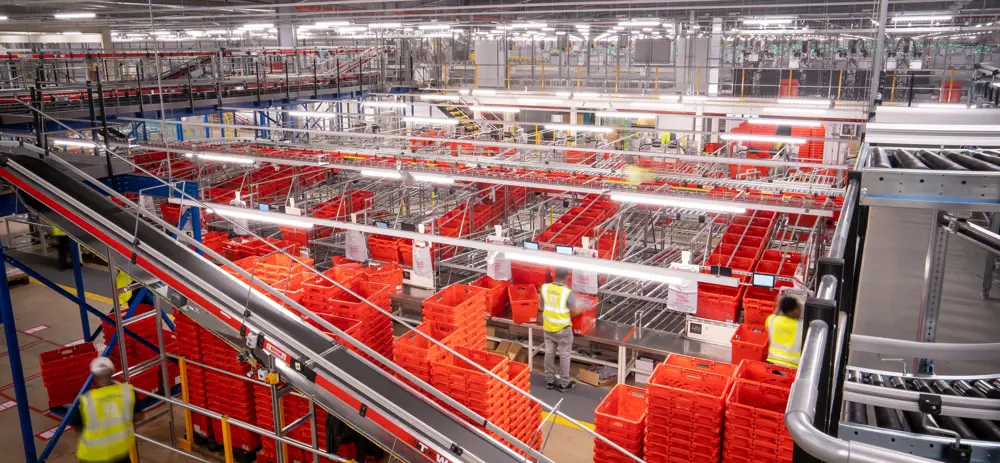
At any one time, there are around 8,000 plastic crates on the move across 32 kilometres of conveyor. Over 150,000 orders per week are dispatched from this warehouse © Ocado
This was unexplored territory, because there was no template for automated warehousing. Ocado had to develop almost all of its software and hardware in-house. This is evidenced by the engineering inside the initial Hatfield warehouse, which at over 16 years old is still one of the largest and most advanced online grocery warehouses in the world. At any one time, there are around 8,000 plastic crates moving across 32 kilometres of conveyors, with cranes, shuttles and machines moving around under software control.
This type of warehouse design makes sense in the UK, which has one of the most evolved online grocery markets in the world. Per head of population, only South Koreans buy more groceries over the internet than we do. Ocado knew that in other emerging markets, it needed a solution that was more modular and scalable, while still efficient. This drove Ocado to evolve the swarm robotics technology that powers its Erith CFC.
Robotic chess to source and assemble customer orders
In Ocado’s second-generation CFC at Erith, thousands of robots help to source and assemble customer orders. They inhabit one of two huge chessboards, referred to as hives – one for ambient products, and another for chilled goods. With two perpendicular wheels at each corner, the cubic robots move across rows or columns of rails surrounding square bins, each of which contains a specific item. Bins are stacked up to 21 deep, creating a truly three-dimensional storage model and the densest storage possible. Simulations worked out that 21 was the optimal number of bins for a stack, based on factors such as fulfilment needs, space available and strength of tote material. Robots are programmed to stop above a particular stack and lower a grabbing mechanism to pick up a bin. They will then either drop it off on another stack to access the bin below it, or bring it to a pick station where humans place the items in a customer’s order basket.
On a busy day, the total distance covered by Erith’s chilled and ambient hive robots could reach 179,778,363 metres – equivalent to travelling around the Earth four and a half times
Each hive is the size of three football pitches, populated by over 1,700 identical robots that are collectively capable of picking a typical 50-item customer order in around five minutes. The real ingenuity of this system is that every robot is working collaboratively in real time, as Paul explains: “There is no way we could achieve the required throughput if the robots were autonomous, moving around the grid dodging one another. Instead, the swarms of robots are orchestrated by a machine learning-based system that is playing chess many moves ahead. It knows which bins need to be where, and which robots it needs to schedule to complete every order in a perfect pick sequence.”
On a busy day, the total distance covered by Erith’s chilled and ambient hive robots could reach 179,778,363 metres – equivalent to travelling around the Earth four and a half times. This all takes place in a relatively confined environment, with robots passing one another at 8ms-1 with less than 10 millimetres clearance. To achieve this level of precision requires the control system to talk to each robot 10 times a second. To do this, Ocado developed a proprietary communication system, with LTE mobile technology operating across the unlicensed spectrum. The system involves slicing the time/frequency spectrum up into cells, and each robot gets one cell that only it is able to use. If a robot needs to communicate more, it can be allocated extra cells.
Working in harmony
Each robot is granted clearance to move to a particular location within the hive. As it moves away from a square, it raises a notification that the square is clear for another robot to enter. As well as optimising movement, this ensures robots don’t collide, even if one unexpectedly stops working due to a mechanical breakdown. This rarely happens, since the robots are constantly providing feedback data. If a machine needs repairing or servicing, it can be temporarily removed from the swarm and repaired off-grid while other robots seamlessly take up the slack.
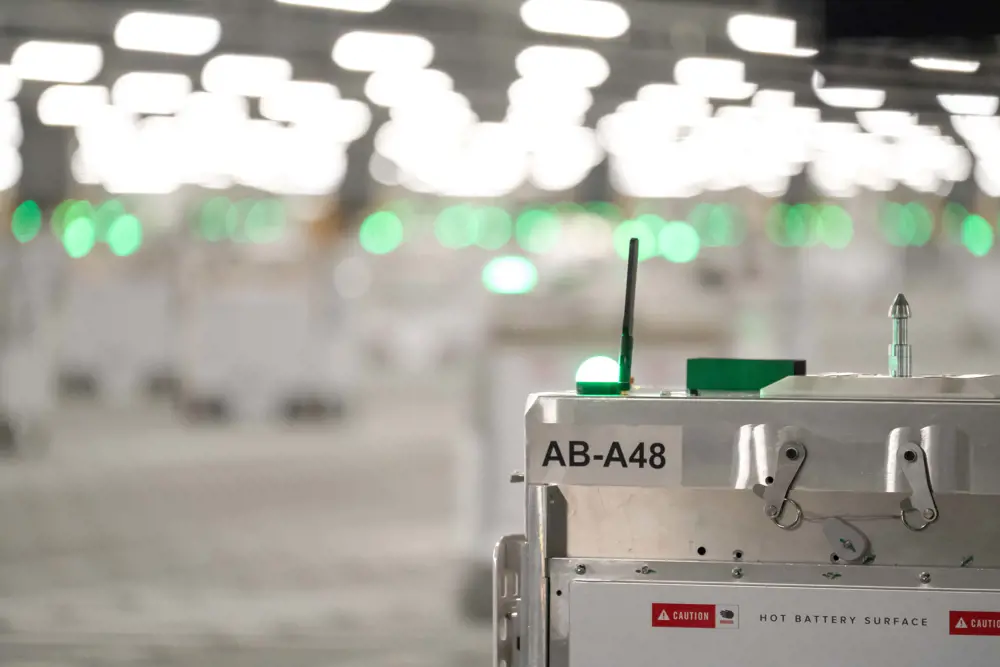
Bots generate about 5,000 data points, 1,000 times a second – that’s one gigabyte of data per bot per day © Ocado
The control system managing this synchronised three-dimensional ballet not only optimises the routing of the robots on top of the hive in real time, but also optimises the three-dimensional storage of the bins underneath the robots. It does this while looking forward in time to ensure that when bins are moved, they’re in optimal positions based on when they’re likely to be needed next.
The bins aren’t grouped according to their contents, so you won’t find 10 brands of kitchen roll in 10 consecutive baskets. Instead, the control system optimises the layout of the hive, based on when each bin is programmed to be needed next. This is calculated using a combination of variable factors, including the customer orders that have been placed, the orders that are expected to be placed, and external factors that alter the demand for each product, which might include weather, promotions or celebrity chef recipes.
Digital twin
🤖 What is a digital twin and how does Ocado use them?
Ocado has also developed a digital twin of the Erith hive. The phrase ‘digital twin’ describes a virtual equivalent of a real-world product or service. As an example, modelling software creates virtual copies of objects already in existence, so they can be stress-tested and used to generate diagnostics in a safe environment. Data from Erith is fed back to its digital twin, as Paul explains: “We use these digital twins to test new algorithms, to examine production software before deployment. Then we are able to playback and visualise production data for analysis and troubleshooting.”
Waste not, want not
The resulting centralised fulfilment model offers many efficiency and productivity advantages over alternative solutions such as store picks. This was the traditional method of online grocery fulfilment, with staff manually navigating around customer-free stores designed to suit the needs of packing personnel rather than shoppers. Erith also stocks a larger product range than any conventional UK supermarket, with around 54,000 products across three distinct temperature regimes. Because a computer is overseeing everything from orders in progress to impending goods deliveries, customers are spared the frustration of ordering items that are out of stock by the time their order is fulfilled.
Substitution levels are also among the lowest in the industry thanks to computerised stock control and just-in-time ordering processes. In 2018, 98.8% of orders were delivered exactly as ordered
There are other benefits to a highly automated warehouse system for groceries. Algorithm-controlled picking and packing slashes waste compared to normal supermarkets. Where a conventional supermarket might ultimately throw away three items out of every 100, the ratio at Erith is one in 6,000. Substitution levels are also among the lowest in the industry thanks to computerised stock control and just-in-time ordering processes. In 2018, 98.8% of orders were delivered exactly as ordered.
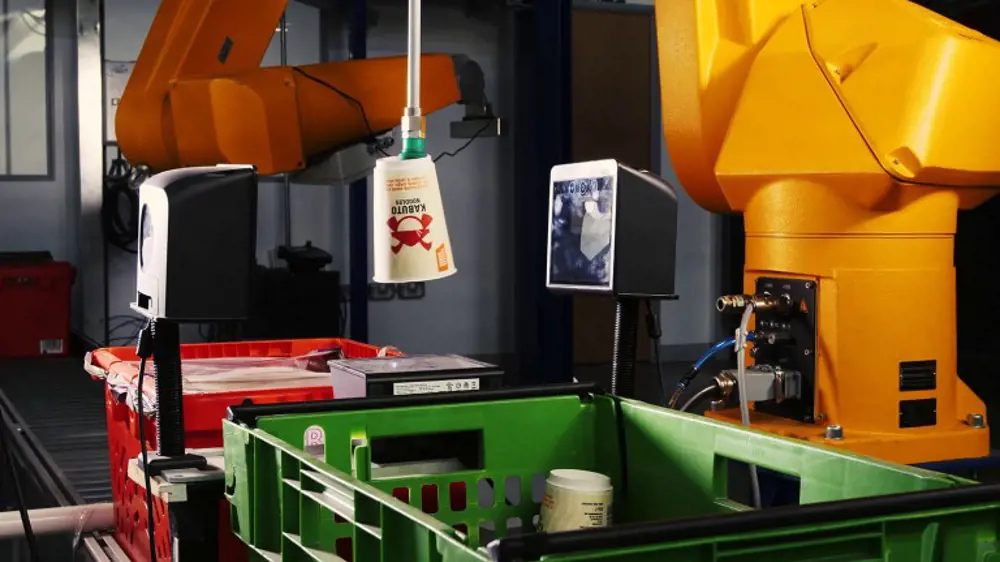
Ocado’s robotic picking system uses a suction cup attached to an articulated arm. This is guided by a computerised 3D vision system that calculates grasping points on an object regardless of its shape and deformability © Ocado
Getting a grip on things
One of the biggest challenges facing robots in a facility like Erith is the sheer variety of product sizes, shapes, weights and materials. While pre-packaged goods may offer predictable sizes and weights, a fragile foil-wrapped Easter egg will require very different handling from a bottle of wine or a bag of frozen vegetables. The robots also have to contend with infinite variations in fresh produce – no two fruits or vegetables will be exactly alike. Until now, this has required humans to complete the final stages of order packing. That represents another obstacle on the road to full automation, which Ocado has been attempting to overcome for years.
One of the biggest challenges facing robots in a facility like Erith is the sheer variety of product sizes, shapes, weights and materials
“Specific items need different grippers and varying strategies for grasping them,” Paul admits. From babyhood, humans learn strategies for picking things up. “For example, if you’re going to insert a bottle into a wine rack, you instinctively know to hold it by the neck so your hand won’t be in the way, and you anticipate the forces that will be required to carry the bottle. If you want to pick a piece of paper off a table, you’d probably slide it to the edge, rather than crumple it.”
“These strategies are instinctual to humans, but robots have to either be taught them or be allowed to learn them. Initially, we will start allowing robots to pick items using a simple suction gripper, while we continue to work on more advanced grippers that mimic the capabilities of human hands.” These artificial limbs use the principle of environmental constraint exploitation to create an orchestrated interaction between the robot, the object and the environment. Modelled on the way humans use their hands, a 3D camera identifies opportunities for environmental manipulation. A robotic hand then sequentially closes its ‘fingers’ around the object, adapting to the shape it needs to pick the item up without applying too much force. Once this has been refined to the point where items aren’t dropped or damaged, one of the few remaining human elements of the Erith warehouse could be eliminated.
Bots and dashes- Erith's data lakes
🗃️ Processing four terabytes of data per swarm per day
Each robot at Erith generates a significant amount of data, which requires processing to be useful in terms of future planning or refining the existing system. The computational power required to process this constantly evolving data stream is enormous. The bots generate about 5,000 data points, a thousand times per second. That’s one gigabyte of data per bot per day, or a total of four terabytes per swarm per day.
The data is processed in various ways; for instance, half a petabyte of raw batch and streaming data is supplied to Google’s BigQuery analytics platform for customised analysis.
The bot controller software is capable of completing three million routing calculations per second. Along with operational and sensor data from the bots, this is streamed to a data lake in the cloud. A machine learning system conducts analytics for monitoring, oversight and predictive maintenance.
Ocado is in the process of rolling out new software at Erith, which will see around two billion messages a day being sent and received. The bot controller software has been christened Dash, and is capable of completing three million routing calculations per second. However, this isn’t as memory-intensive as might be expected, only requiring around 50 GB of space to complete its calculations.
A sign of things to come?
As Ocado improves its algorithms and optimises the efficiency of its robots through simulation learning, each new fulfilment centre operates more effectively than its predecessors.
Following a three-year construction and fit-out period, it took Erith’s army of robots just 14 weeks to achieve the same level of throughput as the previous CFC had achieved over its first 15 months of operation.
Erith was the world’s largest automated warehouse for online grocery retail when it opened last year. However, the technology underpinning it is likely to populate far larger warehouses overseas as foreign consumers embrace the relative simplicity of ordering groceries online. Indeed, there may come a time when customers might not have to order groceries at all. AI and machine learning could ensure items are delivered to individual households as and when they’re needed, without any customer involvement at all.
***
This article has been adapted from "Hives of activity", which originally appeared in the print edition of Ingenia 80 (September 2020).
Contributors
Paul Clarke CBE is an independent advisor, working on a portfolio of government, industry and start-up advisory roles. At the time of writing Paul was the Chief Technology Officer at Ocado. He joined the company in 2006, initially working on warehouse control systems before joining the team designing Ocado’s next highly automated fulfilment centre. Since taking on the role of CTO in early 2012, Paul has focused on growing Ocado Technology to over 1,300 engineers and on the research that will future-proof the Ocado business.
Keep up-to-date with Ingenia for free
SubscribeRelated content
Technology & robotics

When will cars drive themselves?
There are many claims made about the progress of autonomous vehicles and their imminent arrival on UK roads. What progress has been made and how have measures that have already been implemented increased automation?

Autonomous systems
The Royal Academy of Engineering hosted an event on Innovation in Autonomous Systems, focusing on the potential of autonomous systems to transform industry and business and the evolving relationship between people and technology.

Hydroacoustics
Useful for scientists, search and rescue operations and military forces, the size, range and orientation of an object underneath the surface of the sea can be determined by active and passive sonar devices. Find out how they are used to generate information about underwater objects.

Instilling robots with lifelong learning
In the basement of an ageing red-brick Oxford college, a team of engineers is changing the shape of robot autonomy. Professor Paul Newman FREng explained to Michael Kenward how he came to lead the Oxford Mobile Robotics Group and why the time is right for a revolution in autonomous technologies.
Other content from Ingenia
Quick read
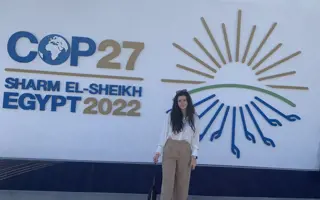
- Environment & sustainability
- Opinion
A young engineer’s perspective on the good, the bad and the ugly of COP27
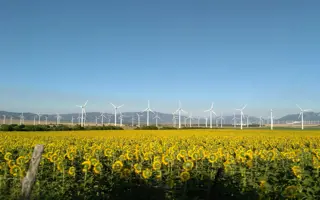
- Environment & sustainability
- Issue 95
How do we pay for net zero technologies?
Quick read
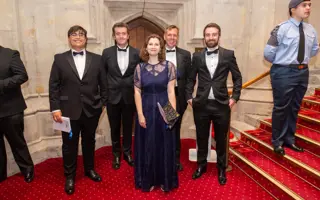
- Transport
- Mechanical
- How I got here
Electrifying trains and STEMAZING outreach
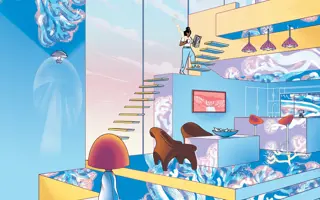
- Civil & structural
- Environment & sustainability
- Issue 95