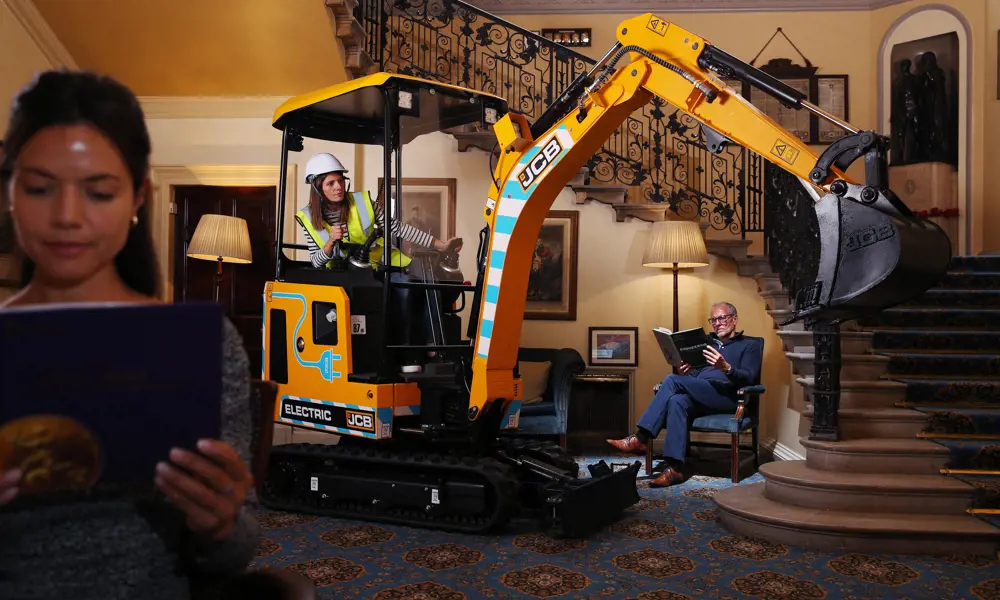
Groundbreaking digging
For over a century, oil has provided the fuel for most of the world’s transportation. The dominance achieved by petrol and diesel seemed unassailable in the 20th century, even during the 1970s Arab oil embargo and the fuel strike of 2000.
Yet electricity has always been a viable alternative in terms of propulsion. The first electric car was developed in America in 1890, while post-war Britain echoed to the whine of electric milk floats. Sir Clive Sinclair’s C5 was decades ahead of personal transportation solutions like the Segway, and over a third of the UK’s rail network is already electrified.
The electric excavator paving the way to zero carbon
With climate change one of the stories dominating the headlines before COVID-19, the necessity of moving away from fossil fuels has been acknowledged even by the internal combustion engine’s most loyal supporters. When construction equipment manufacturer JCB set out on the road to zero carbon, it was obvious that new propulsion systems would be required for its range of diesel-powered machines. Heavy machinery such as 20-tonne excavators can run on battery power, but it would be expensive to purchase and time consuming to charge, so smaller machines are much better suited. So began a multi-layered research programme, attempting to develop hydrogen solutions for larger machines while creating electric alternatives to the diesel engines fitted in the company’s smaller products.
The result is the world’s first fully electric mini excavator – the 19C-1E. Visually identical to the diesel-powered 19C-1, this 1,787-kilogram machine will eventually form part of a family of vehicles sharing the same groundbreaking power source. Such is the 19C-1E’s engineering excellence, it won the Royal Academy of Engineering’s 2020 MacRobert Award, supported by the Worshipful Company of Engineers. This award acknowledges the engineering challenges involved (and solved) in creating a construction machine capable of travelling through a library without shaking the paperbacks off their shelves.
Battery design and sourcing
The first thing to note about the electric mini-digger is its similarity to the standard 19C-1 diesel model, as JCB’s Chief Innovation Officer Tim Burnhope explains. “It uses the same bodywork, but we designed it so the diesel engine could be replaced with the battery and motor. It’s the same weight, so you can tow it on the same trailer. All the access points on the bodywork are identical, with a charging point where you normally put the diesel fuel in. To a customer it feels the same, and the only real difference to the operator is that the fuel gauge has been replaced with a battery level gauge.” Essentially, the electric motor and batteries slot into the diesel housing and the 19C-1E is otherwise identical to the 19C-1 diesel model.
Essentially, the electric motor and batteries slot into the diesel housing and the 19C-1E is otherwise identical to the 19C-1 diesel model.
Sourcing suitable batteries was central to this project’s viability, and the automotive sector provided inspiration. JCB’s Director of Advanced Engineering Bob Womersley quickly recognised the advantages offered by the Sunderland-built Nissan LEAF’s lithium-ion cells: “When we were introducing our machine into the market, we had to have absolute confidence in its robustness. The LEAF batteries use pouch cells, rather than cylindrical cells like the Tesla range – these have many electrical joints in the battery configuration. The robustness requirement that is unique to off-highway equipment steered us in the direction of pouch cells.”
Densely stacked in space-efficient rows, pouch cells are encased in robust bags that protect their contents. This addresses one of the biggest challenges facing any electric powerplant used in industrial machines. “Track laying machinery has no suspension,” Bob says, “so it shakes the machine extraordinarily over rocky or uneven terrain. Machines can encounter well over 15 G, substantially higher than you’d see in a passenger car, so any tiny weakness is exposed in a digger application.” These G forces (acceleration) also affected the design and manufacturing of the 19C-1E’s electric motors, which have resin-encased windings to reduce vibration sensitivity. The motor connects directly to the hydraulic pump without requiring a flexible coupling, helping to reduce the transport weight.
Machines can encounter well over 15 G, substantially higher than you’d see in a passenger car, so any tiny weakness is exposed in a digger application
The pouch cells are assembled into 5 kWh battery packs, and the 19C-1E can currently be purchased with four packs. Each one weighs 35 kilograms, although the machine is only 3 kilograms heavier than its diesel counterpart. Compensatory weight savings include the absence of a radiator, no coolant liquid or engine oil, and of course no need for a heavy diesel engine.
How the electric digger delivers comparable power to its diesel counterpart
With two patents pending on the electric powertrain, a 48 V electrical system delivers instant torque (a measure of the force that can cause an object to rotate about an axis) from the electric motor to the load-sensing hydraulic system. When not in use, the motor drops to an idle speed of just 150 rpm (rotations per minute) to optimise battery life. The motor only needs to idle in order for the hydraulic pump to be on standby at very low speed for instantaneous acceptance of load as the operator demands. Instant torque is available for operation at either 1,200, 1,600 or 1,800 rpm, while it’s also possible to increase power to 2,300 rpm for rapid relocation between sites.
“The low idle speed runs considerably slower than a diesel engine,” explains Bob, “and the torque characteristic of the motor means it can deliver the power at a much lower speed. We have a device in the control software that we call auto kick-up, which is the opposite of auto idle. This encourages the operator to work on the lowest set point on the motor speed, but when they really need high power during machine operation, the software has an auto kick-up function that means they aren’t tempted to use more motor speed than necessary. Because the machine is very quiet, the operator is not aware of its operating speed, and the seamless delivery of power means they wouldn’t have an awareness that these efficiency measures are going on.”
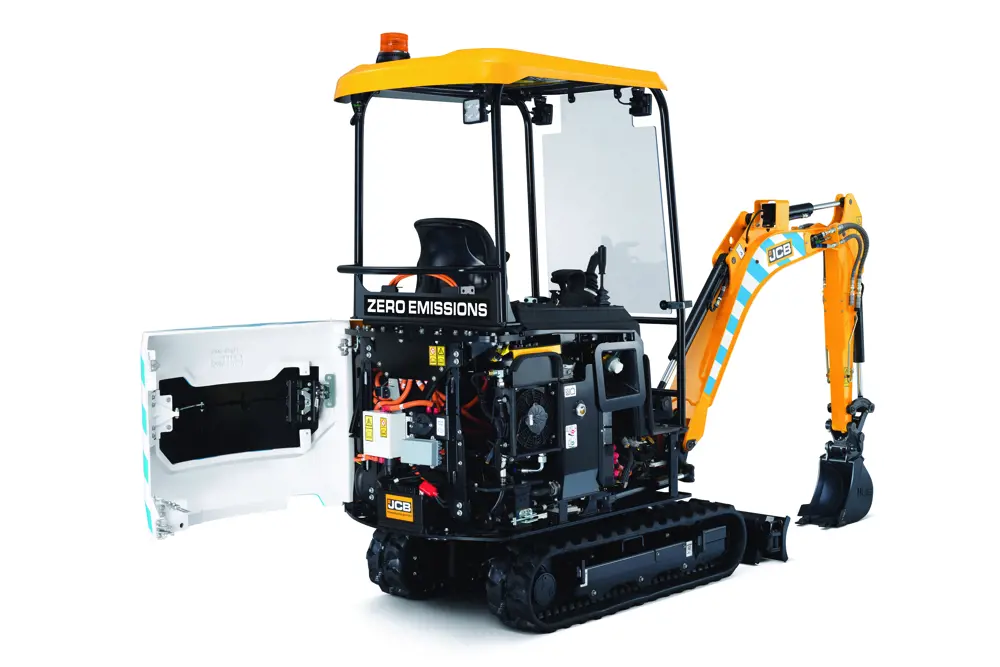
The 19C-1E with side covers removed shows the electrical components packaged tightly within the space of the original diesel engine © JCB
Interestingly, the auto kick-up technology had been developed previously but never made it into a production machine. “We had trialled the auto kick-up as part of our machine efficiency systems,” says Bob, “so it was shelf engineered but not fully refined. In fairness, it works better with an electric motor than with a diesel engine because of how inconspicuous it is and how quickly the motor can react to it. We refined other systems as they were tested – we changed the hydraulic circuit to minimise the pumping losses, and ran the motor slower so the pump was running at a greater displacement than it would on the diesel machine.”
“One of the crucial testing stages was actually giving it to customers,” admits Tim. “We got it out on site to make sure we could learn from customers very early on. That allowed us to gain knowledge and prove the concept, and I think there was a lot of surprise when we started rolling out models to test. Customers didn’t expect electric to offer the same performance level as diesel. For some reason, they expected it not to deliver the same power as the diesel model and that the machine would lose power under load. They were shocked to realise just how powerful it was.” Yet the 19C-1E’s performance figures are comparable to the diesel model across the board, providing a maximum digging depth of 2,891 millimetres with the largest 1,344-millimetre dipper arm fitted.
They were shocked to realise just how powerful it was
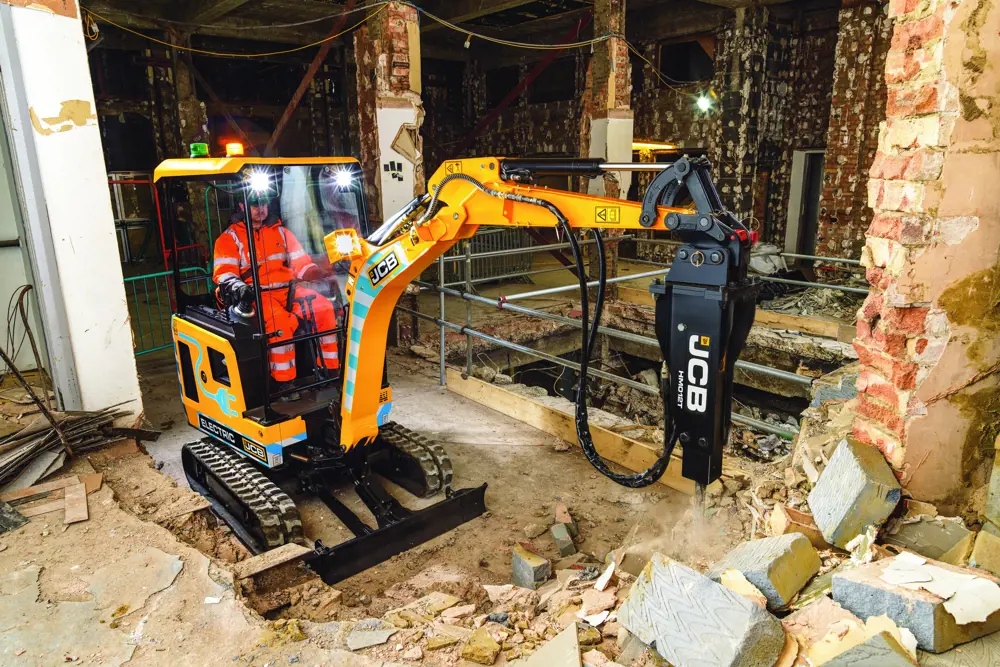
The 19C-1E can easily and safely carry out internal works, as it produces no fumes, has no tethering cables and creates no engine noise © JCB
The benefits of electric models: internal works and quietness
Another crucial piece of research was the accumulated telemetry data gathered from diesel machines throughout the last decade using JCB’s LiveLink system, including average run times and load on equipment. The JCB team noted with surprise that many electric test models were being used for longer periods each day than their diesel counterparts, possibly because of a combination of lower operator fatigue and quieter operation permitting use outside of normal working hours.
The absence of fumes or tethering cables means internal works such as foundation excavations can be carried out safely, and the lack of engine noise enables operators to talk to people outside the vehicle even while it’s in use. Indeed, one of the greatest benefits of electric power is its quietness compared to internal combustion. The 19C-1E emits remarkably less noise compared to its diesel counterpart, with almost no powertrain noise, low vibration and no diesel fumes. This makes long periods at the 19C-1E’s controls more comfortable, as well as enabling it to work in busy urban environments without disrupting nearby homes and workplaces.
one of the greatest benefits of electric power is its quietness compared to internal combustion
The battery life and charge of the JCB
During a 10-month period of the development process, the JCB team quadrupled the battery’s run time, giving it the capacity to complete a full day’s shift on site. Onboard telematics, a standard feature on all JCB machines, yielded valuable background information, especially while the 19C-1E was being tested in JCB’s proving ground – a large quarry adjacent to the factory, where even JCB’s heaviest equipment including the X-Series excavators are tested. Despite being dwarfed by its surroundings, the 19C-1E proved capable of operating at a wide range of temperatures and maintaining performance throughout the charging cycle.
Charging can be carried out using a standard three-pin mains plug, taking eight hours at 230 V. However, many industrial clients will have access to three-phase power at 415 V, which is capable of fully replenishing the batteries in just over two hours. The modular design of both the batteries and electric motor will support their incorporation into many other products within the JCB range, while the same production line is currently fitting electric and diesel motors into the otherwise identical 19C-1 bodies.
The consumer market of the electric mini-digger
The 19C-1E is a domestic success story, with a proprietary electric propulsion system developed and supported by a UK-centric supply chain including battery and motor manufacturers. “We’ve been pleasantly surprised by the way UK agencies now have the foundation for developing electric vehicles,” Bob acknowledges. “The universities have specialist equipment to test batteries, and we did a shaking test extensively on battery packs because there are safety considerations regarding fire risks. That testing infrastructure now exists in the UK, which has been really advantageous for us.”
Since its launch, the 19C-1E’s sales have more than quadrupled initial estimates, with exports to 32 countries. This is an entirely new market, and despite a higher retail price resulting from the cost of battery production, the electric mini-digger has a lower cost of ownership than its diesel sibling thanks to minimal maintenance and the ability to complete work that would have otherwise been carried out by hand or with the support of expensive fume extraction. Bob cites an example of a contractor trialling the 19C-1E on behalf of a utility company: “It was quite a delicate assignment, because when it comes to working beside a water main, you usually need to finish off with a spade. Without engine noise to distract him, the operator could hear the teeth touching the cast iron water valve. He was very surprised!”
Indeed, consumer scepticism is one of the few challenges facing JCB as it rolls out this new technology. The utilities contractor was initially doubtful about the electric digger’s potential, and similar concerns are shared among other prospective clients. “There isn’t a conscious resistance among customers,” Tim says, “just nervousness. Any innovation needs leaders and ambassadors to start removing the blocks to its adoption. We need more hire companies to take the product so people can try it without capital commitment. Good news travels fast, and once people experience it, they get more confident and tell others.”
“We’ve set the benchmark for volume-produced electric construction equipment,” says Bob, “and in the process, we’ve crossed a threshold of understanding on electric propulsion. We understand batteries, we understand electric motors, we understand the control system and the electrical architecture to deliver the power. It’s almost like we’ve come of age, and we can see the route to capitalise on it.”
Tim concurs: “We’ve got an electric machine solution, with a modular battery system and motors that can be rolled out across many products in our range. We have the infrastructure to go up through the weight classes with electric products. Imagine if you buy several different products at the same time, and they all have the same technology. It’ll all be interchangeable.” At the current rate of progress, it won’t be long until we see many more electric-powered construction machines on sites across the world.
***
This article has been adapted from "Groundbreaking digging", which originally appeared in the print edition of Ingenia 84 (September 2020).
Contributors
Neil Cumins
Author
Tim Burnhope FREng has he held numerous roles at JCB including Group Managing Director of Product Development, MD of JCB Sales, Director of European Sales, and MD of both the Loadall and Backhoe Loader Business Units. At the time of writing he was the Chief Innovation and Growth Officer for JCB and is currently Group Director for Special Projects.
Bob Womersley is Director of Advanced Engineering at JCB. He joined JCB in 1982 as a development engineer on JCB’s first production transmission, and his positions at the company have included Chief Engineer, Engines, and Director of Hybrid programmes. As Advanced Engineering Director, he has led JCB’s strategy on machine electrification and advanced propulsion.
Keep up-to-date with Ingenia for free
SubscribeRelated content
Environment & sustainability
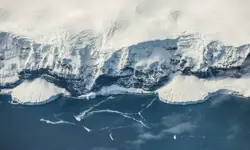
The extreme engineering behind life on an Antarctic station
Antarctica is one of the most challenging environments on the planet, but of enormous scientific importance to humanity. Technology and engineering is essential to enable the British Antarctic Survey's researchers to pursue their science effectively in this awe-inspiring landscape.

Recycling household waste
The percentage of waste recycled in the UK has risen rapidly over the past 20 years, thanks to breakthroughs in the way waste is processed. Find out about what happens to household waste and recent technological developments in the UK.

Upgrade existing buildings to reduce emissions
Much of the UK’s existing buildings predate modern energy standards. Patrick Bellew of Atelier Ten, a company that pioneered environmental innovations, suggests that a National Infrastructure Project is needed to tackle waste and inefficiency.

An appetite for oil
The Gobbler boat’s compact and lightweight dimensions coupled with complex oil-skimming technology provide a safer and more effective way of containing and cleaning up oil spills, both in harbour and at sea.
Other content from Ingenia
Quick read
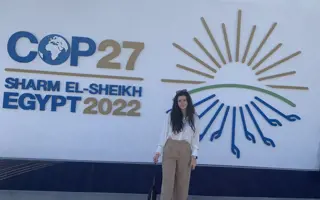
- Environment & sustainability
- Opinion
A young engineer’s perspective on the good, the bad and the ugly of COP27
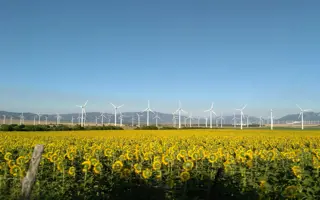
- Environment & sustainability
- Issue 95
How do we pay for net zero technologies?
Quick read
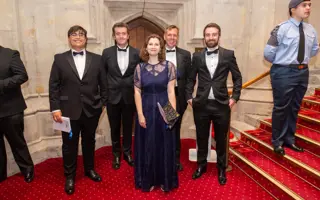
- Transport
- Mechanical
- How I got here
Electrifying trains and STEMAZING outreach
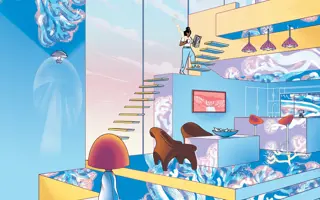
- Civil & structural
- Environment & sustainability
- Issue 95