Going vertical – developing a short take-off, vertical landing system
Developing a short take-off, vertical landing system
Rolls-Royce earned its fundamental role in developing the Joint Strike Fighter – the world's largest fighter aircraft programme – through its expertise in the area of vertical lift propulsion systems, pioneered with the unique Harrier. Hutchinson reports on the heritage of 'V/STOL' flight, the Harrier's propulsion challenges and, in more detail, the engineering challenges that have been experienced in developing an effective propulsion system for a supersonic V/STOL fighter for the 21st century.
Rolls-Royce, the company responsible for the unique propulsion system that enables the Harrier to rise or descend vertically, is developing the next generation of vertical lift. Sir Stanley Hooker would be delighted and inspired by what is happening today just yards from his former office in a factory in Bristol.
Hooker was the engineer at the heart of inspired designs such as the Olympus (culminating in the engine for Concorde) and, significantly, the Pegasus (powerplant of the Harrier family of Vertical/Short Take-Off and Landing (V/STOL) aircraft). Hooker recognised the far-reaching potential of the concept brought to him by Marcel Wibault, a veteran French aircraft designer. Wibault’s design for a vertical take-off and landing aircraft featured a single engine driving four centrifugal compressors arranged in a square around the aircraft’s centre of gravity. The compressors could be rotated to vector the thrust 90 degrees vertically down (for lift) and to rearwards (for forward flight).
The Bristol team established that Wibault’s system of compressors would prove too heavy and complex for flight. They came up with an inspired improvement – to replace the separate centrifugal compressors with bypass flow from a single large LP compressor and redirect both this flow and the hot jet efflux. This harnessed Wibault’s elegant solution of ensuring that the lift forces are exerted through the aircraft’s centre of gravity in one highly practical stroke.
This proved a key step towards achieving, at last, a practical V/STOL vehicle. Before this breakthrough, almost two decades of trial and error had failed to achieve practical short or vertical take-off and landing success, in spite of extensive and costly research and development programmes on both sides of the Atlantic.
In the United States, vertical take-off and landing (VTOL) grabbed public attention through pioneering ‘vertical riser’ fighters launched by Lockheed and Convair in 1954. In spite of their promise they ran into technical problems and both were grounded by 1956 – but their developers learned much. By 1960 nearly 20 different types of piloted VTOL aircraft had flown, some simple ‘flying platforms’, others complex machines such as the UK’s Fairey Rotodyne transport, a compound autogyro.
Some experimental types were equipped with Rolls-Royce power units, such as the Bell X-14 with two Armstrong Siddeley (later Rolls-Royce) Viper turbojets slung under its nose, exhausting through vane cascades. This was the first aircraft to use jet exhaust vectoring to achieve VTOL flight. During a remarkable 20-year flying career, the X-14 contributed significantly to the development of VTOL flying techniques and control systems.
By 1960, Wibault’s concept in the workable shape of the BS53 (later Pegasus) had emerged in the new Hawker P.1127, designed by the Hawker Aircraft Company (led by Sydney Camm) around the new engine. Hooker and his team used an existing engine (the Orpheus) as the core of the BS53. It proved the ideal architecture for the new powerplant as it featured a hollow central shaft of sufficient internal diameter to accommodate a second, contra-rotating shaft to drive the additional compressor. Critically, the new engine’s contra-rotating shafts virtually eliminated gyroscopic effects. This initial prototype of today’s Harrier combat aircraft emerged to herald the arrival of the western world’s only operational V/STOL aircraft in front-line service today, operating in a variety of combat roles with armed forces in the United States, the UK and other nations worldwide. Within the tight constraints of the original engine’s dimensional ‘envelope’, the Pegasus has grown in power from 11,000 lbf of thrust to 23,800 lbf in its latest configuration.
The Rolls-Royce LiftSystem®
The Pegasus captured the full potential of what brilliant mathematician and aeronautics expert Theodor von Karman termed ‘vectored thrust’. Today, more than four decades later, vectored thrust is again being exploited by engineers at Bristol. This time, the promise is encapsulated in a ‘cutting edge’ technology package named the Rolls-Royce LiftSystem®, for which Rolls-Royce is subcontracted to Pratt & Whitney as a member of the F135 STOVL Propulsion System team. This is a major advance in technology with a key role to play in an aircraft family that will dominate the future combat aircraft market.
The Joint Strike Fighter (JSF), the biggest-ever US Department of Defense acquisition programme, is set to benefit from this technology. JSF comprises three carefully-tailored aircraft within one core design to ensure effective multi-role capability – and crucially, affordability. These are a conventional take-off and landing version (CTOL), a carrier version (CV) with a larger wing and other modifications for service at sea, and a Short Take-Off Vertical Landing (STOVL) version. Initial procurement plans for the latter alone amount to approximately 750 aircraft, with some 600 for the United States Marine Corps, up to 150 for the UK and further export orders anticipated.
The Rolls-Royce LiftSystem® creates a STOVL-capable aircraft without the need for significant changes or compromises to the highly effective JSF multi-role combat aircraft. The system comprises the Rolls-Royce LiftFan®, mechanically driven from a conventional gas turbine and supplying vertical lift from the forward part of the aircraft, and a rear-mounted jet pipe from the main engine that can vector thrust from horizontal to vertical. Roll control is achieved by using thrust nozzles on ducts (‘roll posts’) extending laterally from the main engine.
Why change from the soundly successful ‘four-poster’ vectored-thrust layout of the Pegasus for the Harrier?
The Harrier, for all its unique operational qualities, still has the inevitable limitations that come with its type of powerplant. Its large intake and lack of reheat dictate subsonic operation, while its payload/range, although much improved in the past 20 years, is still short of conventional combat aircraft. In particular, its ability to bring back expensive, modern, smart munitions in battle is limited whenever a vertical landing is required – on board a carrier, for example.
Ever since the Harrier entered service in the United States and Britain back in the late 1960s, aerospace organisations have searched for a next-generation concept that could replace the Harrier family with an even better aircraft, capable of supersonic flight while retaining the key ability of vertical operations. Following a series of aborted programmes and studies in both the US and the UK, the US Defense Advanced Research Projects Agency (DARPA) launched the Advanced Short Take-off and Vertical Land (ASTOVL) project. This considered a wide range of aircraft concepts including several using one or more fans driven by the main propulsion engine to augment vertical thrust.
The UK joined the project in 1993 for its second phase. At this stage, concepts to be studied further were narrowed by competition to the two funded for a large-scale powered model trial programme. These focused on the Lockheed Martin/Allison shaftdriven lift fan and the McDonnell Douglas gas-powered lift fan. Each featured a single fan behind the pilot to provide forward vertical thrust, with the main engine thrust vectorable through 90 degrees for either vertical or horizontal thrust.
The Lockheed Martin design favoured driving the lift fan through a shaft from the main engine and gearbox while in vertical mode. The rival McDonnell Douglas model drove its lift fan by passing exhaust gases from the main engine forward to the fan along ducts. Both aircraft represented highly innovative applications for STOVL concepts, recognising that significant thrust augmentation could be achieved at low forward speed by increasing the bypass ratio through a secondary lift system. In addition, Boeing developed a next-generation version of the Harrier’s direct lift approach and also joined the competition. Before long, McDonnell Douglas dropped its ‘gas fan’ approach and switched to a concept with a separate, vertically-mounted lift engine for additional vertical thrust.
By 1995, both Lockheed Martin and Boeing had made excellent progress and were selected to continue (as ASTOVL eventually evolved into Joint Strike Fighter). The DOD, in fact, added the requirement for CTOL and carrier versions of the same aircraft to be developed with minimum change from the STOVL version needed by the US and UK. Ironically, the unsuccessful contender, McDonnell Douglas, which of course was subsequently acquired by Boeing, had originally offered a direct lift system of its own but had dropped that in favour of the gas driven fan. Meanwhile, Rolls-Royce had acquired Allison and were now responsible for the LiftFan used on the Lockheed aircraft.
Finally, a competitive fly-off saw the Lockheed Martin X-35 with its Rolls- Royce LiftSystem® matched against Boeing’s X-32 (with direct lift and again with Rolls-Royce providing the major lift components) in a game of high stakes: the JSF contract itself. After extensive flight trials, the Lockheed Martin shaftdriven lift fan aircraft concept was selected – a concept still clearly recognisable from the early drawings of 1993 and before. Rolls-Royce was selected to provide the innovative LiftFan, the 3 Bearing Swivel Module and the roll-posts, which together deliver JSF’s unique STOVL capability.
The engineering challenges
The Rolls-Royce LiftSystem®, using energy provided by the aircraft’s single main engine, provides what for so long has proved unachievable: vertical lift and supersonic capability in one package. It attains this unmatched ability by assisting the extraction of some 40,000 lbf of vertical thrust from the conventional main engine, which can produce only 30,000 lbf of horizontal thrust in its normal mode. This remarkable feat is achieved by the use of a separate, mechanically driven vertical fan that is powered by the LP turbine of the prime engine. The extra mechanical power is made available by opening up the final nozzle on the main engine at the same time as directing its efflux vertically by means of the Rolls-Royce 3 Bearing Swivel Module. The system thus effectively increases the bypass ratio of the main engine through the induction of higher airflow by the LiftFan with not only higher airflow, but higher airflow with the ideal characteristics for vertical flight (high mass flow and low jet velocity). This is truly a revolutionary step that redefines the relationship between horizontal thrust and vertical lift, and produces significant increases in performance, efficiency and safety.
At last, the inherently conflicting requirements of high speed, range, manoeuvrability, payload and vertical take-off and/or landing have been reconciled. This technology maximises vertical lift by the elegant integration of a deceptively simple engine-driven LiftFan with an enabling engine powerful enough to achieve a 1.5:1 lift-to-thrust ratio. All previous attempts over the years were restrained by the 1:1 lift-to-thrust constraint inherent in direct lift systems, leaving little margin for fuel and payload.
This novel concept permits the main engine to be optimised for conventional flight, uncompromised by its STOVL capability. The LiftFan augments vertical flight just as the afterburner augments high-speed performance.
None of this, naturally, makes for easy engineering. The modern designers are faced with the same four crucial technical targets that faced Hooker – minimising weight and size, and maximising durability and functionality. Plus, most crucially of all in this cost-driven era, they have to focus on affordability.
The LiftFan provides many particularly interesting challenges. Examples of technologies that are under development are hollow-bladed blisks (a bladed disk or ‘blisk’ achieved by super-plastic forming of the blades and linear friction welding to the blisk hub); organic matrix composites for the interstage vanes; a clutch mechanism with the ability to transfer 29,000 shaft horsepower without chatter or wear while ensuring high life; and a gearbox design with a 30:1 horsepower-to-weight ratio, able to operate with interruptions to its oil supply of up to a minute – and all these have to be achieved within tight budgets and timescales.
Exciting engineering derives, too, from the fact that the LiftFan must be capable of functioning safely in the 250- knot crosswind, which occurs at its intake when the aircraft starts to migrate from forward flight to the hover. The scale of this challenge can be appreciated by recognising that conventional military and civil intakes normally operate with a maximum crosswind of only 30 knots; plus the fact that the intake of the LiftFan is only some 0.2 metres, compared with more than 1 metre in civil applications.
These challenges have led to the development in the UK of a world-leading, aero-mechanical analytical capability that now enables the prediction of vibration amplitudes more accurately than ever before, while three-dimensional analysis techniques yield an understanding of the blade distortion following a 1.5 lb bird strike.
Formula One gearboxes lead blissfully relaxed lives compared with the LiftFan™ gearbox, which takes 29,000 hp from the main engine and transfers it through a right angle to drive the LiftFan rotor.
Formula One would also appreciate the LiftSystem clutch, which uses dryplate carbon–carbon technology originally derived from aircraft brakes and a unique closed-loop clutching system for precise, smooth and rapid power transmission to the LiftFan – while achieving the required high durability.
Another unique contributor to the Rolls-Royce LiftSystem® is the 3 Bearing Swivel Module, the rear-mounted ‘jet pipe’ that vectors thrust through 90 degrees in little more than two seconds. This core element of the supersonic JSF also articulates laterally, thus simultaneously providing yaw capability. As one of the two main ‘thrust pillars’ on which the aircraft rides in STOVL mode, this duct has both to support the final hot nozzle and transmit its thrust loads back to the engine mounts. Engineers have invented a new word – fueldraulics – to define the power system of the module’s actuators, which exploit fuel (pressurised to 3500 lbf/in2), rather than hydraulic fluid, to reduce weight and complexity. One actuator will actually ‘travel’ with the swivel nozzle, moving through 90 degrees in a less than perfect environment of intense heat and vibration.
Economic constraints
All of this exciting engineering is happening within a carefully controlled programme management package that maintains constant sight of the key driver behind the entire Joint Strike Fighter programme – affordability. Turning back to basics, JSF is intended to provide a cost-effective, highly flexible and overpoweringly effective defence element quickly and easily wherever in the world it may be needed. Life cycle costs are thus crucial. So the principles of ‘cost as an independent variable’ have been engineered into the entire JSF programme from the outset. This means development, product and life cycle costs have the same status as capability and performance to ensure the customer gets best value for money.
Benefits to the UK
Not least, the Rolls-Royce LiftSystem® has created top quality engineering and manufacturing jobs in UK industry now and for many years to come, while ensuring that the UK has access to the latest defence capabilities and technologies.
When the first JSF STOVL variant takes to the air, it will not simply be by far the most capable combat aircraft of its kind yet to fly, but the embodiment of a uniquely positive, creative and effective US–UK partnership in which everyone gains. For Rolls-Royce, with its long-term experience of working with overseas aerospace organisations, JSF marks another major step forward not only in its global reach but also in its engineering excellence, extending still further the flight-path so successfully pioneered more than four decades ago by Sir Stanley Hooker and his STOVL champions.
John Hutchinson
Freelance Writer
John Hutchinson is a writer and PR consultant based in the UK. His background includes writing and media relations work within the aerospace industry spanning some three decades and today his activities focus also on sectors including technology, transport, education and the environment, frequently highlighting developments that bring multinational benefits through advances in European collaboration.
Keep up-to-date with Ingenia for free
SubscribeOther content from Ingenia
Quick read
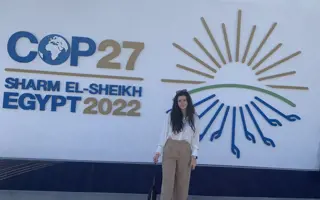
- Environment & sustainability
- Opinion
A young engineer’s perspective on the good, the bad and the ugly of COP27
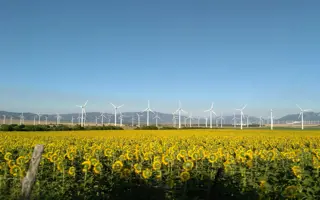
- Environment & sustainability
- Issue 95
How do we pay for net zero technologies?
Quick read
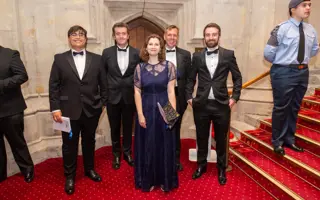
- Transport
- Mechanical
- How I got here
Electrifying trains and STEMAZING outreach
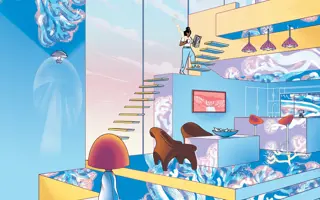
- Civil & structural
- Environment & sustainability
- Issue 95