
The technology that helped Team GB's cyclists go for gold in Rio 2016
After the 2016 Summer Olympics in Rio de Janiero, Brazil, the British Cycling team returned to the UK having won 12 medals – six of which were gold. The team once again dominated the Olympic sport and the press speculated about what had led to its success, suspecting secret skinsuits and aerodynamic paint, among other things.
The press was right to wonder if engineering had made a significant impact. Professor Tony Purnell, Head of Technical Development at British Cycling, points out the striking difference in the way the 1,500-metre record for running and the four-kilometre team pursuit cycling world record have changed over the last 30 years. Both events are nominally around four minutes, but the 1,500-metre record has hardly changed, while the cycling time has dropped by some 13 seconds. Calculations that Professor Purnell made revealed a need for some 15% improvement in power or about 17% less aerodynamic, rolling and friction drag reduction to improve on this time. A combination of factors led to the success of the British Cycling team in Rio, but it is clear that engineering played a key role.
Funding research
British Cycling receives a grant from the National Lottery (it received £30 million in the four years leading up to Rio) and a portion of this is invested in research and development led by Professor Purnell.
Following a career in technical development for Formula One, Professor Purnell joined British Cycling in 2013 with a job to “employ technology in any way I can to make the Olympians faster”. With improvements being made not only by Team GB, but by other countries’ teams as well, to record the fastest possible times, the focus was on marginal gains that could be made to improve performance. “Some of the races are very close and if you can make the slightest difference to push your rider in front, it can be the difference between gold and silver,” Professor Purnell explains.
Some of the races are very close and if you can make the slightest difference to push your rider in front, it can be the difference between gold and silver
Before focusing on the areas where these gains could be made, Professor Purnell used mathematical modelling to work out how a 1% improvement would affect the changeable variables:
- rider power
- total mass
- frontal area
- coefficient of drag
- coefficient of rolling resistance
- inertia of wheel
- drivetrain efficiency.
Within these variables, Professor Purnell and his team decided to focus their research on frontal area, coefficient of drag and drivetrain efficiency as these were the areas where a small increase in percentage could make the biggest gains in speed.
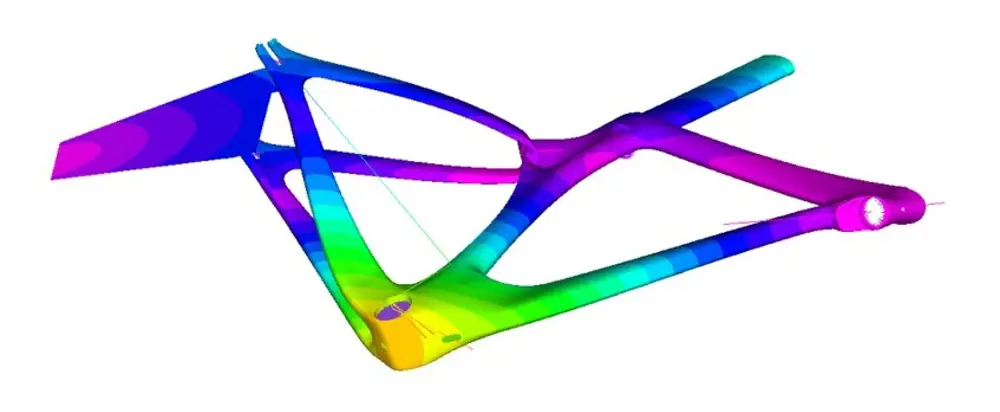
A finite element analysis (FEA) process was used to aid development of the T5GB frame. The T5GB achieves part of its performance benefit by having a shape that reduces aerodynamic drag. However, this reduction runs counter to the need to have frames that are structurally optimised for high stiffness and low weight. One of the advantages of the T5GB is that it incorporates those two contradicting requirements. This balance was achieved by using technical expertise and experience from motorsport and similar high-tech/fast-paced industries to engineer the optimal frame in a rapid timescale © Lentus Composites and Cervélo
In preparation for London 2012, the team of engineers working with British Cycling (known as the ‘Secret Squirrel Club’) had made a lot of progress and modified the obvious engineering on the bikes but more research was needed in order for it to continue. Professor Purnell realised that funding would not stretch to research and to build a new bike so, as a Visiting Professor at the University of Cambridge, he decided to “shamelessly exploit the ability and enthusiasm of Cambridge students” to carry out research. A group of engineering students, studying Master’s, PhDs and carrying out postdoctoral research, worked on projects that included turning the velodrome into a wind tunnel, measuring rolling resistance, optimising the changeover timing of the team pursuit, aerodynamic handlebars, testing the stiffness of the bike frames and investigating whether cyclists should shave their legs. “The students were really good at investigating whims,’ explains Professor Purnell, “and once we were fairly confident we could make a gain, we then went to consultancy services.”
The students were really good at investigating whims and once we were fairly confident we could make a gain, we then went to consultancy services
How engineering helped
🚲 The engineering gain that helped Britain win in the final
The most visible technology improvement delivered by the research was the Cervélo T5GB track bike. While people may have looked at the equipment and expected to see something dramatically different, in reality the devil was in the detail. The prototype of the new bike was made from 3D-printed plastic and tested in a wind tunnel. The figures were very encouraging from the start, reflecting Cervélo’s long specialisation in aerodynamics. When built up into a complete bike without a rider, it produced over 10% less drag when tested back to back. Further tests added a pedalling rider adopting the sort of position that an Olympic rider would take in the various events. This showed a solid gain in excess of 1%, which was seen immediately when the bike started to undergo track tests. “People forget that wind tunnel testing is a simulation, not the real thing, so the track testing programme was important to us as it gave concrete evidence for performance gains or losses,” adds Professor Purnell. The track tests confirmed the observations of the previous experiments. “One percent does not sound that much, but when one feeds this into British Cycling’s computer simulations it gives the team pursuit about 0.8 seconds gain over the four minutes or so of the event. That is around a 15 metre gain, which funnily enough is about how much the British men beat the Australians by in the final.”
A new frame
The most visible outcome of this research was the development of a new bike frame by racing and track cycle specialist Cervélo, which was supported in the engineering and manufacturing of the new frame structure by Oxford-based engineering firm Lentus Composites. Development of the frame began 18 months before Rio and it was the ability of the British company to develop parts at a high quality and such a rapid speed that made the project possible in such a short space of time.
The British Cycling team had previously used the UKSI frame in the Beijing and London Olympic Games; however, for the Rio Games, Cervélo had designed a new shape – the T5GB, which was more aerodynamic than the UKSI. Lentus Composites’ task was to manufacture this new frame but ensure that it matched the stiffness and lightness of the previous bike, and passed all of the International Cycling Union’s (UCI) stringent safety and strength tests. A carbon-fibre reinforced polymer composite frame, the T5GB is made from a mixture of several different kinds of carbon that offered certain properties in terms of either stiffness, weight, or toughness, materials that offer properties that exceed high-performance steel, but at a fifth of its weight. The frame was first built as a 3D finite element analysis (FEA) mesh and simulated more than 50 times to optimise stiffness, weight and safety. Specialist software was used to cover the mesh in plies of composite (moulded layers), allowing the bike to be built in a virtual environment and put through the same stiffness tests as the real frames would be. While this was ongoing, a number of development bikes were built and tested to validate the FEA process.

Left: Engineers place computer-cut plies into the mould tooling, based on the design that was developed through the FEA process. The placement of these plies is critical to achieving the desired frame stiffness and strength, so they have detailed instructions and diagrams to help. Right: An engineer tests the finished frame for stiffness at Lentus Composites. Multiple stiffness tests were carried out using methods that were developed by Cervélo, based on its knowledge of how frame stiffness relates to bike performance and rider feel. The test demonstrates that the T5GB will behave and handle in the way Cervélo intended © Lentus Composites and Cervélo
Using the same software, the engineers were able to generate the two-dimensional ply shapes needed to cut out the materials at a later stage and model how the fibres would lay in the final frame, an important aspect that was key to the resultant performance. When it came to manufacture, the engineers were faced with 120 flat shapes of all different sizes and materials that needed to be laid onto the frame in the correct order and location to generate the required properties. Once that was complete, the bikes were covered in a paint that was lighter than clear lacquer. The paint, and the process of applying it, was specially developed by a separate firm for use in ultra-lightweight liveries on composite materials. Its use on the T5GB was the world’s first application of the technology.
The computer-aided engineering process was integral to the overall design and allowed Cervélo and Lentus Composites to deliver a bike that worked the way British Cycling needed it to in the time available, rather than having to build and test multiple frames.
As well as the changes that were made to the bike frame, the team focused on coefficient of drag by making improvements to the handlebars, shoes and skinsuits – “just about anything that could give us an advantage,” Professor Purnell adds. This included a focus on riders refining their positions to gain aerodynamic advantages.
Quite close to the games, we began to doubt some tyres that had been ordered so a couple of students spent two days testing them on a rolling rig in the lab. They fell to pieces rather too quickly so we had to change them at the last minute
All of the changes and improvements made were rigorously tested before being implemented and Professor Purnell is keen to point out that there was a big emphasis on evidence-based decision making. “Quite close to the games, we began to doubt some tyres that had been ordered so a couple of students spent two days testing them on a rolling rig in the lab,” he explains. “They fell to pieces rather too quickly so we had to change them at the last minute. If that testing had not have happened, we may have gone to Rio with the wrong tyres.”
Teamwork
Approaching Rio, the velodrome at British Cycling’s training facility was covered in instruments and cameras so that the technical team could arm the coaches and riders with hard facts and evidence rather than opinion. There was always the worry that the coaches and riders would think of Professor Purnell’s team as “hair-brained boffins who weren’t going to deliver anything”, so it was gratifying to first see the women’s team pursuit and then the whole squad embrace the approach to help improve their times.
Undoubtedly, the work of the technical team and the coaches and riders paid off. The women’s team pursuit first broke the world record in the qualifying rounds for the World Cup in Manchester in 2013 with 4:23.910, and continued to break them until setting a new world record of 4:10.236 in the finals at the Rio Games in 2016 – winning gold, of course.
However, the team’s work did not end with Rio. As Tony says: “Is there more to come? We’ll have to wait until the Tokyo games to answer that.”
***
This article has been adapted from "Going for gold", which originally appeared in the print edition of Ingenia 70 (March 2017).
Contributors
Professor Tony Purnell is a Visiting Professor at the Cambridge University Engineering Department and is also part of a research group exploring pathways to reducing greenhouse gas emissions in the aviation industry. At the time of publication, he was Head of Technical Development at British Cycling and before this, he spent more than 10 years working in Formula One.
Graeme Hyson is a Senior Lead Development Engineer at YASA, working in YASA's New Technology department leading the development of future motors. At the time of publication, he was Lead Engineer at Lentus Composites, an engineering-led manufacturer of composite products, assemblies and systems for a range of industry sectors. Graeme presented the frame engineering process at the talk.
Keep up-to-date with Ingenia for free
SubscribeRelated content
Sports & leisure
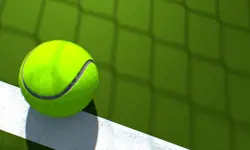
How technology enhances the Wimbledon tennis experience
The All England Lawn Tennis and Croquet Club (AELTC) and IBM worked closely together since 1990 to harness innovative technology to transform The Championships into one of the most popular and technically advanced events on the international sports calendar.

Noise-cancelling headphones
Used by plane and train passengers wanting to listen to radio, music or film without hearing background noises, active noise-cancelling (ANC) headphones are able to prevent outside noise from leaking through to the inside of headphones.
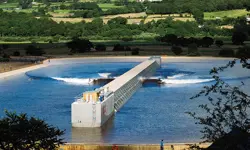
How to create the perfect wave
From small waves lapping at your feet and swells suitable for surfing to storm waves for testing structures and even tsunamis, waves of any shape and any size can now be engineered. What are the techniques and conditions needed to model waves and what makes some more powerful than others?

A formula for success
Over the past 30 years, Paddy Lowe FREng has seen Formula One motor racing grow from small teams to a billion pound enterprise at the forefront of technology. He has introduced active suspension, hybrid engines and other key technologies that have changed the profile of motor racing.
Other content from Ingenia
Quick read
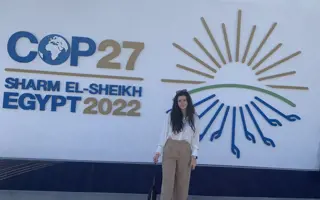
- Environment & sustainability
- Opinion
A young engineer’s perspective on the good, the bad and the ugly of COP27
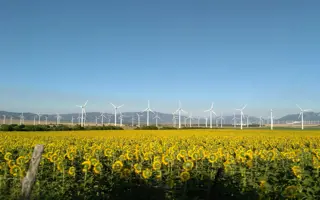
- Environment & sustainability
- Issue 95
How do we pay for net zero technologies?
Quick read
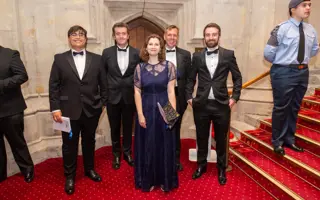
- Transport
- Mechanical
- How I got here
Electrifying trains and STEMAZING outreach
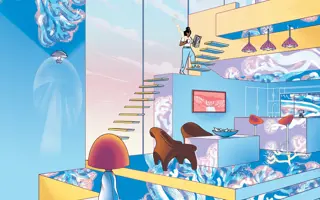
- Civil & structural
- Environment & sustainability
- Issue 95