
Digital hydraulics for wind energy and beyond
When the wave energy research group led by Professor Stephen Salter FRSE at the University of Edinburgh first started developing hydraulic systems, it faced an uphill struggle. As he wrote at the time: “The reputation that high-pressure oil has in 1984 is very like the reputation that electronics had in 1944. It is used with reluctant suspicion for jobs that cannot be done in any other way. It is thought to be expensive, complicated, temperamental, unreliable and inefficient. It is blamed for everything that goes wrong.” Now, three decades later, the technology that they were researching not only plays an important part in the world’s largest floating wind turbine – it has won the Royal Academy of Engineering 2015 MacRobert Award.
The award went to Artemis Intelligent Power, the company that Salter set up with his colleague Professor Win Rampen FREng in 1994 to commercialise their university research on Digital Displacement® (DD) transmission. In particular, the prize recognised the use of digitally controlled hydraulics in wind turbines. DD transmission, said the announcement that accompanied the award, “has the potential to transform the viability of offshore wind power and low carbon transportation”.
the prize recognised the use of digitally controlled hydraulics in wind turbines
Wind turbines are just one application looking to expand capacity as manufacturers move to build larger devices. Mitsubishi, which now owns Artemis, has already tested a 7MW wind turbine with DD transmission in Scotland and recently launched the world’s largest offshore floating wind turbine. This second 7MW wind-turbine is due to operate off the coast of Fukushima in Japan. DD hydraulic machines, pumps and motors, and pump-motors that can perform both roles, are also key components in new systems for flywheel energy storage and regenerative braking in buses and trains as well as industrial processes. There are also hopes that the technology will return to its origins, as a way of helping to capture wave energy.
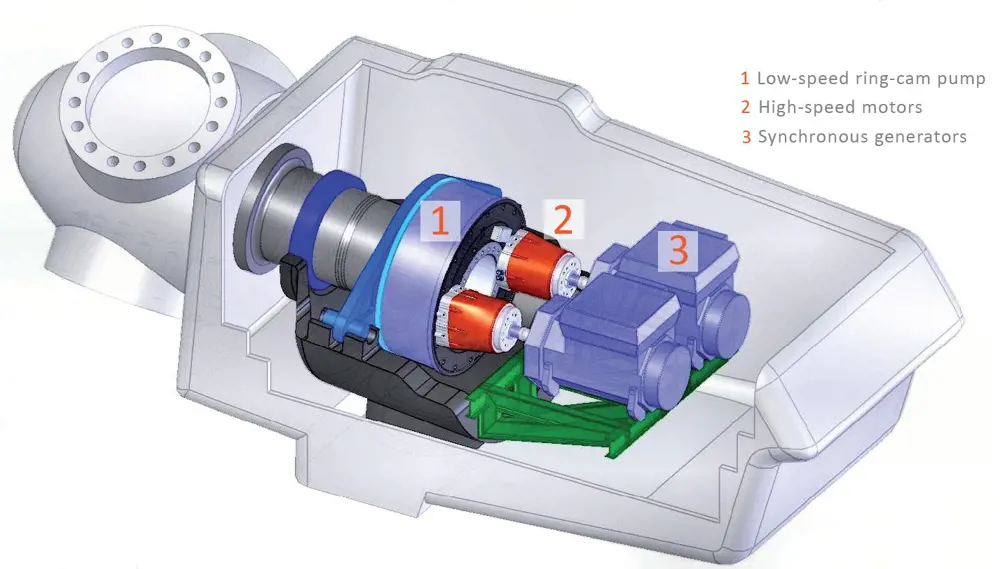
A simplified drawing of the wind-turbine transmission. Inside the Digital Displacement® pump and motors. Computer-driven valve communication replaces traditional mechanical control of oil flow
Replacing the gearbox
Professors Salter and Rampen set up Artemis Intelligent Power as a spinout from their university research into hydraulic transmissions for wave energy. Salter first came up with the idea of a very large slow-speed ring-cam pump, while Rampen later realised that the same concept could also work in a high-speed motor such as would be needed to drive a generator. Putting the two together led to an infinitely variable speed hydraulic system, with a pumped fluid carrying energy from place to place rather than a fixed-speed mechanical gearbox.
Hydraulic systems may have been “blamed for everything that goes wrong,” in the past, but thanks to their ability to deliver power to devices in awkward places, they have had a long history of use in heavy machinery. Here, for example, in a digger on a construction site, pressurised fluid delivers power from a diesel engine to the tools and wheels.
DD technology replaces the conventional analogue mechanisms of hydraulic machines with a completely digital control method. The multiple working chambers of the machine each have solenoid-operated valves that are controlled by an embedded computer synchronised to the rotation of the shaft. A computer provides real-time control of every working stroke of the machine.
DD technology replaces the conventional analogue mechanisms of hydraulic machines with a completely digital control method
The advantage of hydraulic systems is that they outperform electric motors in terms of weight and cost. The power density, the power produced per kilogramme of hardware, in a hydraulic machine is typically at least three times higher than in electric motors. But traditional hydraulic pumps and motors are noisy and inefficient. DD deals with these drawbacks by bringing electronic control to hydraulics. Traditionally, hydraulic pumps and motors relied on the mechanical control of valves to switch a flow of oil between high pressure and low pressure manifolds in pumps, motors and transmission systems. In Artemis’s DD systems, electronically switched poppet valves control the flow of oil, on an ‘as-needed’ stroke-by-stroke basis, into and out of the chambers of pumps and motors.
It was not until the late 1990s that enough people accepted the viability of the technology, allowing the business to grow and take on staff. Dr Niall Caldwell came on board in 1999, when he joined the two mechanical engineers, Win Rampen FREng and Uwe Stein, and Jon Almond, an electronics engineer, to become the resident expert on control systems and simulation. As the company grew, and expanded its staff and facilities so that it could tackle more ambitious challenges, it began to think of developing systems for wind turbines, the subject of Stephen Salter and Matthew Rea’s seminal paper, Hydraulics for wind (1984).
The advantage of hydraulic systems is that they outperform electric motors in terms of weight and cost
Back in the 1980s, wind turbines mostly delivered peak powers of around a few hundred kilowatts. By 2009, when Artemis turned to wind turbines, their output had broken through the megawatt barrier. In a project funded by, among others, the Carbon Trust, Artemis developed a hydraulic transmission system for a 1.5 MW wind turbine.
Artemis’s project showed that, compared to the usual gearbox, a DD hydraulic transmission could reduce the weight of the transmission that has to be supported in the nacelle at the top of the structure and eliminate the costly electronic power converter that virtually all wind – turbines use to make their electricity ‘grid-friendly’. It also allowed the use of two generators instead of one so that either could be switched off – saving energy – in light and moderate winds.
There is nothing new about the idea of using hydraulic transmissions in wind turbines, but conventional hydraulics were simply too inefficient for Artemis to seriously consider them. The development of DD transmissions with efficiencies comparable to those of gearboxes changed this.
Mitsubishi Heavy Industries Ltd (MHI) heard about the company’s work on the use of hydraulic systems in renewable energy at this time. The Japanese company, which had worked on wind turbines since 1980 and has sold more than 4,000 turbines, was looking for a new technology for the transmission for offshore wind turbines. It wanted to build wind turbines that were approaching the limits of mechanical gearboxes.
After analysing the prototype 1.5 MW wind transmission in the Artemis lab, MHI acquired the company in 2010 as part of its proposed £100 million R&D investment in the Scottish offshore renewables industry. They then jointly built a 2.4 MW transmission to retrofit into an existing in-house turbine in Yokohama and, in rapid succession, the 7MW wind turbine which is now installed at the Hunterston offshore wind turbine test facility in Scotland. While this is being put through an initial test programme, a second 7 MW turbine, the world’s largest floating wind turbine, has been installed 20 km off the coast of Fukushima Prefecture in Japan.
On the buses
🚌 Turning 12-year-old city buses into hybrid vehicles
Artemis has worked with the manufacturing company Alexander Dennis, which makes buses, and a local operator, Lothian Buses, to turn a 12-year-old city bus into a hybrid vehicle. For the demonstration, Artemis set out to develop a DD hydraulic system that could be retrofitted to existing vehicles. The demonstration bus showed that a DD system could save up to 25% of the fuel consumption of a typical urban bus.
Battery hybrids combine a mechanical transmission with electric motors. The power comes from batteries and the engine. The hybrid captures braking energy to recharge the batteries.
In hydraulic hybrids, the energy store usually takes the form of a gas accumulator, a pressure vessel containing a bladder pre-charged with nitrogen gas that provides a spring-like store for high-pressure oil. While accumulators cannot match batteries for long-term energy storage, they are much quicker at charging and discharging. Electric hybrids typically cannot recharge batteries quickly enough to recover all of the energy that could be captured during braking.
The project showed that hydraulic hybrids beat batteries in terms of the payback time, how long it takes for the energy savings to recoup the extra cost, by a large margin. Battery hybrid buses currently cost at least 50% more than conventional diesel vehicles and operators cannot afford to run them without subsidies.
Battery hybrids are expensive because they need ‘exotic’ and hard-to-dispose-of materials, such as rare-earth magnets and lithium, whereas hydraulic pumps and motors are essentially made of steel – one of the most widely recycled materials. The charging and discharging of hybrid batteries has to be managed as shown up by widely reported problems with the new London buses. Typical paybacks are more than 15 years, while diesel-hydraulic hybrid buses could recoup the extra cost in two or three years.
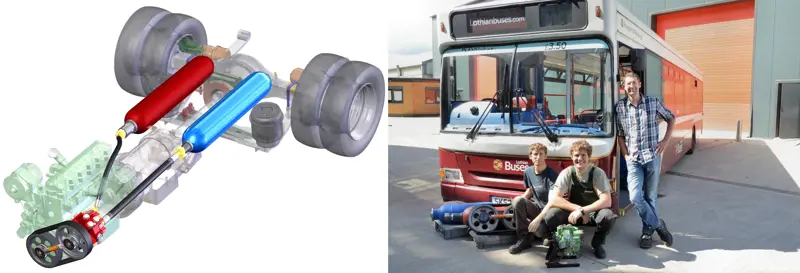
The green pump-motor in the foreground enables the hydraulic hybrid to save fuel. Following successful trials, Artemis is seeking partners to help exploit this application
Energy Efficiency
When Artemis opened for business in the 1990s, hydraulic equipment had yet to join the ‘digital revolution’. This limited efficiency, especially when not working at full load. One conventional hydraulic machine that Artemis uses to benchmark its own systems can reach an efficiency of around 86% at full load, but run this machine at a load of around 30% and the pump’s overall efficiency drops to around 60%. Even when it is idling with no load, a conventional hydraulic pump like this can consume 10% or more of its full-load power. The corresponding idling losses for a DD machine are about 1% of full-load power.
Electronic control makes DD machines more efficient when there is no load. Idling cylinders are not pressurised, so ‘leakage flows’, which are a necessary part of machine design, are small and waste very little energy. This allows systems to operate at high efficiency even down to small fractions of full power. This is important in many applications of hydraulic systems, such as injection moulding machines, which operate a duty cycle with short bursts of activity followed by idle periods. Under such circumstances, DD systems have about a quarter of the energy loss of purely mechanical systems.
One advantage of this energy saving is that hydraulic pumps and motors generate less waste heat, sometimes eliminating the need for a cooling system. DD machines are also quieter in operation. Indeed, one machine was so quiet that the customer, used to a constant racket from hydraulic machinery, complained that it was not working.
DD doesn’t just save energy and reduce noise, it gives operators more control over machinery, by responding about five times faster than conventional machines. That response can be controlled more accurately than conventional hydraulic systems, which rely on add-on servo-mechanisms rather than the inherent digital control that is a part of the system.
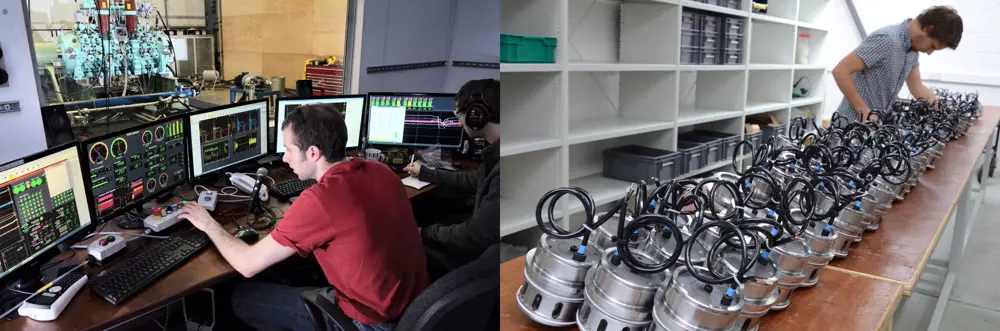
Artemis mechanical engineers testing a 3.5 MW digital displacement motor (Left). Computer-controlled valves are at the heart of all Artemis hydraulic machines (Right). This batch will be installed in a Digital Displacement® wind-turbine transmission
Artemis launched digital control at just the right time. Customers were becoming increasingly comfortable with electronic fuel systems for petrol and diesel engines in cars, for example. Working at first with makers of off-road vehicles, the small team at Artemis began developing a sequence of larger and larger systems. It was not long before they reached 50kW. Then, in 2008, in a demonstration with a BMW car, Artemis developed a 200kW series-hybrid transmission. The hydraulic system recovered energy when the vehicle braked, and optimised the engine speed and switched the engine off when it was not needed. The project showed that the hydraulic system could save around half of the fuel normally used in an urban driving cycle, with a similar cut in CO₂ emissions.
The power output of hydraulic systems has continued to grow, along with the applications of the technology. For example, after cars, Artemis moved on to buses, in a project that involved turning a 12-year-old city bus into a hydraulic hybrid – see The power output of hydraulic systems has continued to grow, along with the applications of the technology. For example, after cars, Artemis moved on to buses, in a project that involved turning a 12-year old city bus into a hydraulic hybrid – see On the buses.
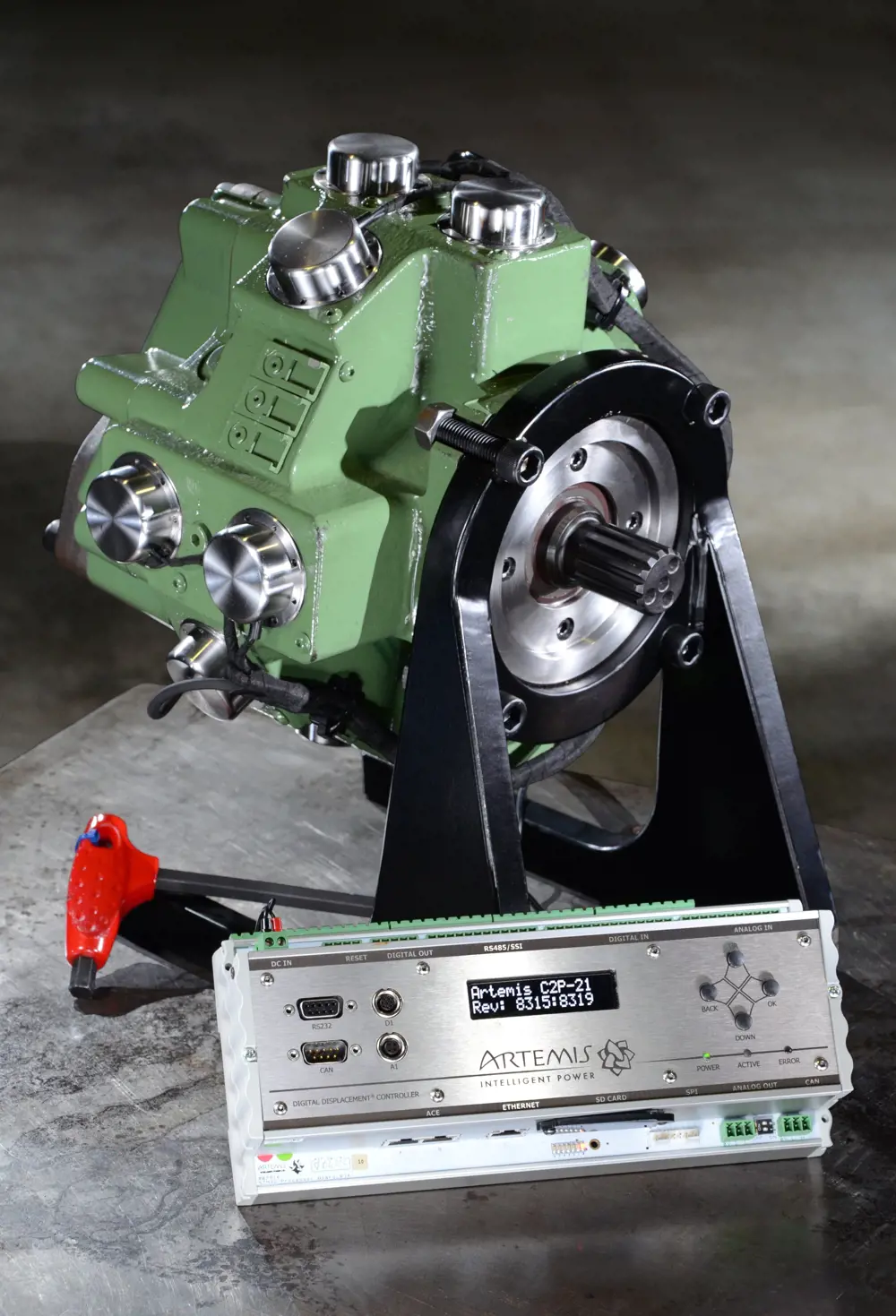
The Artemis ‘E-dyn 96’ industrial pump, shown here with its computer control unit, is designed to cut energy costs in manufacturing processes such as injection moulding
Further applications
The lower cost and ability to retrofit DD hydraulics into conventional systems is also behind a project to investigate regenerative braking in trains. As part of a competition, Accelerating Innovation in Rail, funded by Innovate UK. Artemis is working with the engineering consultancy Ricardo and train maker Bombardier on a hybrid rail vehicle.
This project combines Artemis’ DD hydraulic pump-motor transmission and Ricardo’s flywheel energy storage system. In this case, the goal is to improve the transmission system as well as to recover braking energy. Conventional diesel commuter trains dissipate about 35% of their overall mechanical engine energy as heat through braking, while the transmission can waste up to a further 30%. Hydraulic transmission and energy storage can tackle both losses.
The DDFlyTrain project has already shown that the technology could deliver a return on investment in less than five years. Other benefits could include reduced wear, as the flywheel takes much of the strain off the brakes. The hydraulic system is also good at returning stored energy and reducing the load on the diesel engine, so there could also be less pollution, noise and vibration as trains pull out of stations. DD hydraulic trains may not sever the link between oil and transport, but, as Caldwell puts it, thanks to the limited economic case for electrification in the UK, diesel trains will be around for some time, so they might as well be 30% more efficient.
Artemis’ steady move up the size scale and into new markets owes much to the company’s commercial strategy over its 20 years in business. The company started small, working in an old cabin that also housed Salter’s wave energy group. Rather than take on venture capital, the founders decided to retain control of the business and to fund growth through income. It has a growing patent portfolio, which currently stands at some 120 patent families. Mitsubishi has filed almost as many again over the past five years, which has opened the door to consulting work and licensing deals. That income has helped to unlock matching funding from the Carbon Trust, Energy Saving Trust, DECC, Innovate UK and the Scottish government.
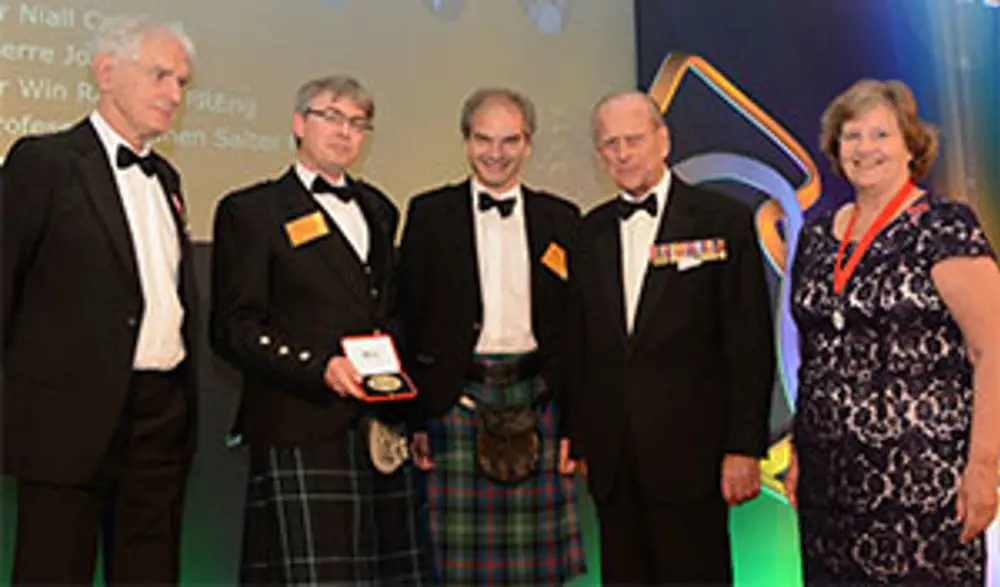
The MacRobert Award was presented to the Artemis team by the Duke of Edinburgh at the Royal Academy of Engineering’s awards evening on 16 July 2015. From left to right: Professor Stephen Salter FRSE, Dr Niall Caldwell, Professor Win Rampen FREng, HRH Prince Philip, Professor Dame Ann Dowling DBE FREng FRS
Business model
The company’s business model meant that it worked with leading global companies, including Sauer-Danfoss, Bosch Rexroth and Mitsubishi. Together they develop DD systems and power transmissions for a growing range of energy-saving applications.
Artemis’ ability to persuade such businesses to even look at DD technology impressed Nick Cooper FREng, a MacRobert judge and a mechanical engineer. The Artemis drive may be “both an incredible piece of invention and a brilliant piece of detailed engineering design” but ideas that overturn established models can face an uphill struggle for acceptance. “Without being too blunt, nobody in their right mind would give it a second look, and as such the story of Artemis is about technical excellence, but is also a tale of faith, determination and belief in the invention and its viability.”
Artemis has continued to grow under its new owners. It now has a staff of around 50 people, most of them qualified engineers. While MHI concentrates on the use of DD hydraulics in wind turbines, Artemis continues to develop the technology for other systems. It has now built up Artemis Manufacturing Group, which can manufacture the mechanical and electronic systems for DD hydraulics. As Caldwell describes it, this ISO 9001 standard facility gives the company the ability to supply small-scale production quantities of equipment for pilot trials and to get the ball rolling with OEM customers.
Caldwell sees the relationship between MHI and Artemis as being mutually beneficial. “We have found that Mitsubishi has a very impressive culture including Monozukuri, which is ‘the art, science and craft of making things’.” Now that Artemis has helped MHI achieve a 7MW system, perhaps, armed with the prestige of the MacRobert Award, the company can take a shot at Salter’s 30-year old ambition of building a 30 MW wind turbine.
***
Michael Kenward OBE would like to thank Jamie Taylor, Senior Project Manager at Artemis, for his help in the preparation of this article.
This article has been adapted from "Bringing electronic control to hydraulics", which originally appeared in the print edition of Ingenia 64 (September 2015).
Contributors
Michael Kenward OBE
Author
Dr Niall Caldwell was the Managing Director of Artemis at the time of publication and is currently the Senior Director of Research and Development at Digital Displacement. He is an inventor with over 50 patents and joined Artemis in 1999. As Technical Director, he led the team which developed the control systems for the company’s hydraulic hybrid systems, including a series-hybrid BMW saloon demonstrator. Following the acquisition by MHI in 2010, he led the development of the control system of the 7MW offshore wind hydraulic transmission, and took over as Managing Director in 2013.
Keep up-to-date with Ingenia for free
SubscribeRelated content
Energy

Algae-powered architecture
An apartment block in Hamburg in Germany has been built that uses microalgae placed within its façade to generate heat and biomass. Jan Wurm, an associate director at Arup, was one of the chief designers of the energy system. He talked about the concept, execution and results from the world’s first photobioreactor.

New energy pioneers
London-based BBOXX supplies solar-powered battery boxes to customers in developing countries. Their remote monitoring and battery management system was one of the winners of the 2015 Bloomberg New Energy Finance Award.
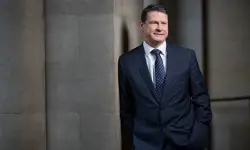
Energy with connections
When Steve Holliday FREng moved from the oil industry into energy distribution, the sector was seen as staid. In reality, during his years at National Grid, the sector became increasingly important as the need to tackle climate change led to a transformation in the UK’s energy mix.
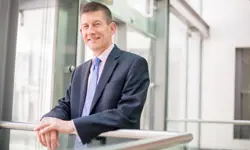
Building a sustainable career
Dr Shaun Fitzgerald FREng has moved between academia, strategic consulting and running his own business, and is now the new Director of the Royal Institution. A career that started in geothermal energy research moved to natural ventilation in buildings, leading to a business that has changed the nature of building design.
Other content from Ingenia
Quick read
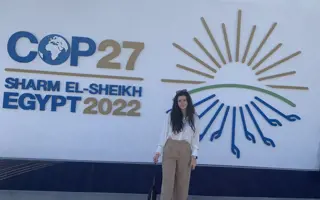
- Environment & sustainability
- Opinion
A young engineer’s perspective on the good, the bad and the ugly of COP27
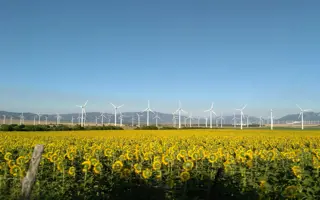
- Environment & sustainability
- Issue 95
How do we pay for net zero technologies?
Quick read
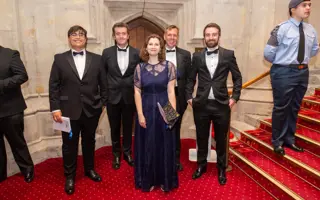
- Transport
- Mechanical
- How I got here
Electrifying trains and STEMAZING outreach
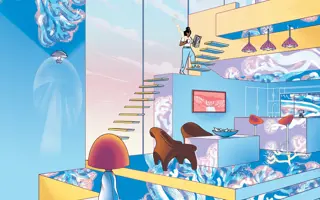
- Civil & structural
- Environment & sustainability
- Issue 95