
Designing and manufacturing world-class engines
Jaguar Land Rover is the UK’s largest automotive manufacturer, with a history going back almost 70 years. The company has been named as a finalist for the 2016 MacRobert Award in recognition of the worldclass innovation behind the most significant decision the company has ever made: to design and manufacture its own engines for the first time in a generation.
In 2011, it was announced that Jaguar Land Rover would invest £1.5 billion a year for the next five years in new product development. The design, development and creation of a new family of Ingenium engines supports the company’s aim to be completely self-sufficient in the design and manufacture of all engines by 2020. Starting with little more than a blank sheet of paper and an empty field, the Jaguar Land Rover team has developed an entire suite of world-leading Ingenium engines that meet the growing demand for lower fuel consumption and cost of ownership, without compromising vehicle performance and driver experience, and delivering commercial robustness for the company now and into the future. The first diesel Ingenium engine was launched in January 2015, and the petrol engine is due to launch later this year.
Innovation
The Ingenium engines are the result of almost 200 innovative ideas, which led to more than 100 new patent applications. These were combined to deliver significant emissions and weight reductions alongside improved performance and fuel economy. A key aspect of this was to deliver the lowest engine friction, using the latest engine system technologies. Despite adding features and increasing power output, Ingenium engines weigh up to 40 kg less than other equivalent engines.
In order to build the Ingenium engines, Jaguar Land Rover built an entire manufacturing facility from scratch, which presented an opportunity to create a world-class manufacturing environment
In order to build the Ingenium engines, Jaguar Land Rover built an entire manufacturing facility from scratch, which presented an opportunity to create a world-class manufacturing environment. In 2012, building work started on the £500 million, 98,000 m2 state-of-the-art Engine Manufacturing Centre (EMC) just outside Wolverhampton, and work is currently underway on an 85,000 m2 expansion worth in excess of £450 million. The EMC also has impressive green credentials with one of the largest solar panel roofs in the UK, which can generate up to 30% of the site’s electricity needs.
Benefit to society
Filling a brand new factory with skilled staff presented its own challenge, and Jaguar Land Rover took a new approach to creating job opportunities and upskilling the local community. Every EMC employee undertakes an intensive two-week immersive training programme called the Powertrain Way, which has successfully introduced bus drivers, bricklayers and beauticians to new careers in engineering. Wolverhampton has the second highest unemployment rate in the UK, and the EMC is already providing a large number of opportunities in the region. The facility opened in 2014 and already has almost 1,000 employees, with a further 5,500 in the supply chain. More than 40 people have enrolled on an apprenticeship programme, and last year Jaguar Land Rover opened an Education Business Partnership Centre working with local schools to encourage children to pursue STEM subjects.
For more information, visit Jaguar Land Rover
***
Other publications relating to Jaguar Land Rover include 'Driven to an electrifying future', Ingenia 79 and 'Charging into the future', Ingenia 85.
This article has been adapted from "Designing and manufacturing world class engines, Jaguar Land Rover", which originally appeared in the print edition of Ingenia 67 (June 2016).
Keep up-to-date with Ingenia for free
SubscribeRelated content
Mechanical

When will cars drive themselves?
There are many claims made about the progress of autonomous vehicles and their imminent arrival on UK roads. What progress has been made and how have measures that have already been implemented increased automation?

R&D investment makes good business sense
In just five years, Dr Ralf Speth FREng has presided over a revolution in design and manufacturing that has helped create a new family of engines and has overhauled Jaguar Land Rover (JLR) production facilities.

Bikes help improve skills and attitude
The Archway Project is an independently-funded scheme that is expanding its engineering-based programmes by providing BTEC certificates and diplomas. John Milton, the director of the project, explains what the charity does to help reduce anti-social behaviour and improve employment prospects.

High speed evolution
In December 2010, Eurostar International Ltd awarded a contract for 10 new high speed trains to Siemens. The company has used a system developed over decades to maximise the performance and passenger-carrying ability of its 320km/h trains.
Other content from Ingenia
Quick read
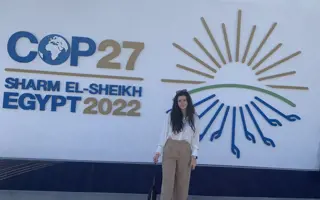
- Environment & sustainability
- Opinion
A young engineer’s perspective on the good, the bad and the ugly of COP27
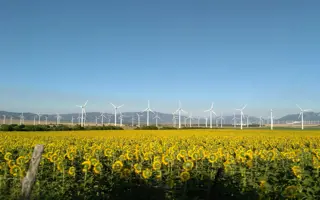
- Environment & sustainability
- Issue 95
How do we pay for net zero technologies?
Quick read
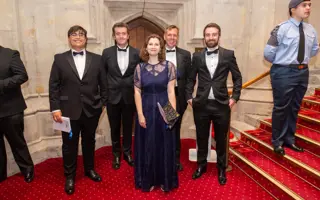
- Transport
- Mechanical
- How I got here
Electrifying trains and STEMAZING outreach
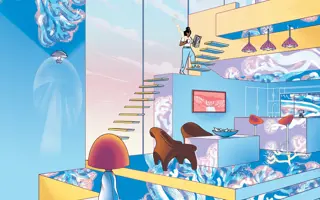
- Civil & structural
- Environment & sustainability
- Issue 95