
Could in-space manufacturing be the future for space missions?
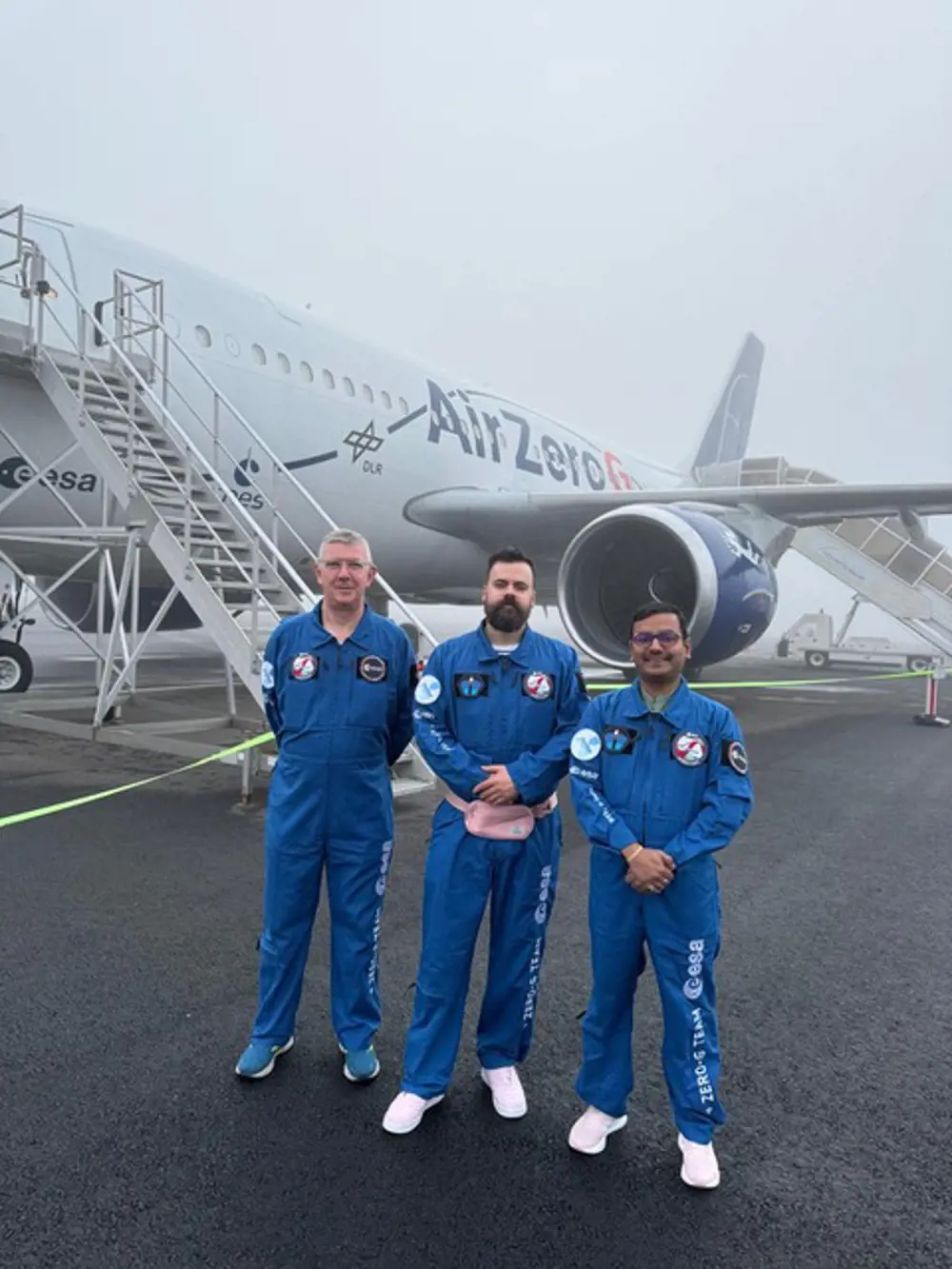
Preparing for parabolic flight: (left to right) Professor Colin McInnes FREng, Dr Gilles Bailet, and Satyam Bhatti, from the University of Glasgow's James Watt School of Engineering.
With rocket launches becoming cheaper, it’s tempting to think we can just send more hardware into orbit – but the real solution lies in creating smarter, larger, and more sustainable space ecosystems through in-space manufacturing.
Everything humanity has built so far has been constrained by Earth’s gravity. It might seem natural to build within these limits, but when we manufacture in orbit, the rules – and possibilities – completely change. In my work, I focus on 3D printing in space, which offers a radically different approach to designing and building systems for space missions.
Unconstrained by gravity
Traditionally, spacecraft must be designed to fit within the limited mass and volume of a rocket’s payload fairing, the protective cone that protects it against the pressure and heat of launching through the atmosphere. At the same time, it must also withstand the intense accelerations and vibrations of launch.
In-orbit manufacturing will allow us to bypass these constraints entirely. Instead of optimising for launch, we can optimise systems for their mission, which may last decades. Without gravity’s constraints, structures such as large antenna or radar built off-Earth could be lighter, larger, and use materials more efficiently, delivering better performance and greater capability.
Combining in-space manufacturing with recycling has transformative potential. Imagine if spacecraft were refurbished every decade: it could extend their lifespans to a century, reducing the need for new launches. This vision aligns with a more sustainable future for space exploration, where waste is repurposed, and innovation continues without adding to orbital debris. By enabling a circular economy in orbit, we can redefine the future of space engineering, ensuring resource efficiency and environmental responsibility.
Imagine if spacecraft were refurbished every decade: it could extend their lifespans to a century, reducing the need for new launches.
One of the biggest challenges we faced in our own programme of research was overcoming the limitations of existing 3D printing methods. Many types of 3D printer, including those using polymer filaments or resin, are prone to defects, failures, and inefficiency. For example, resin-based printing often traps gases that create internal defects, while filament-based systems are prone to tangling or breakage. Powder-based 3D printers, on the other hand, require complex containment systems to manage material flow, which are difficult to implement in microgravity.
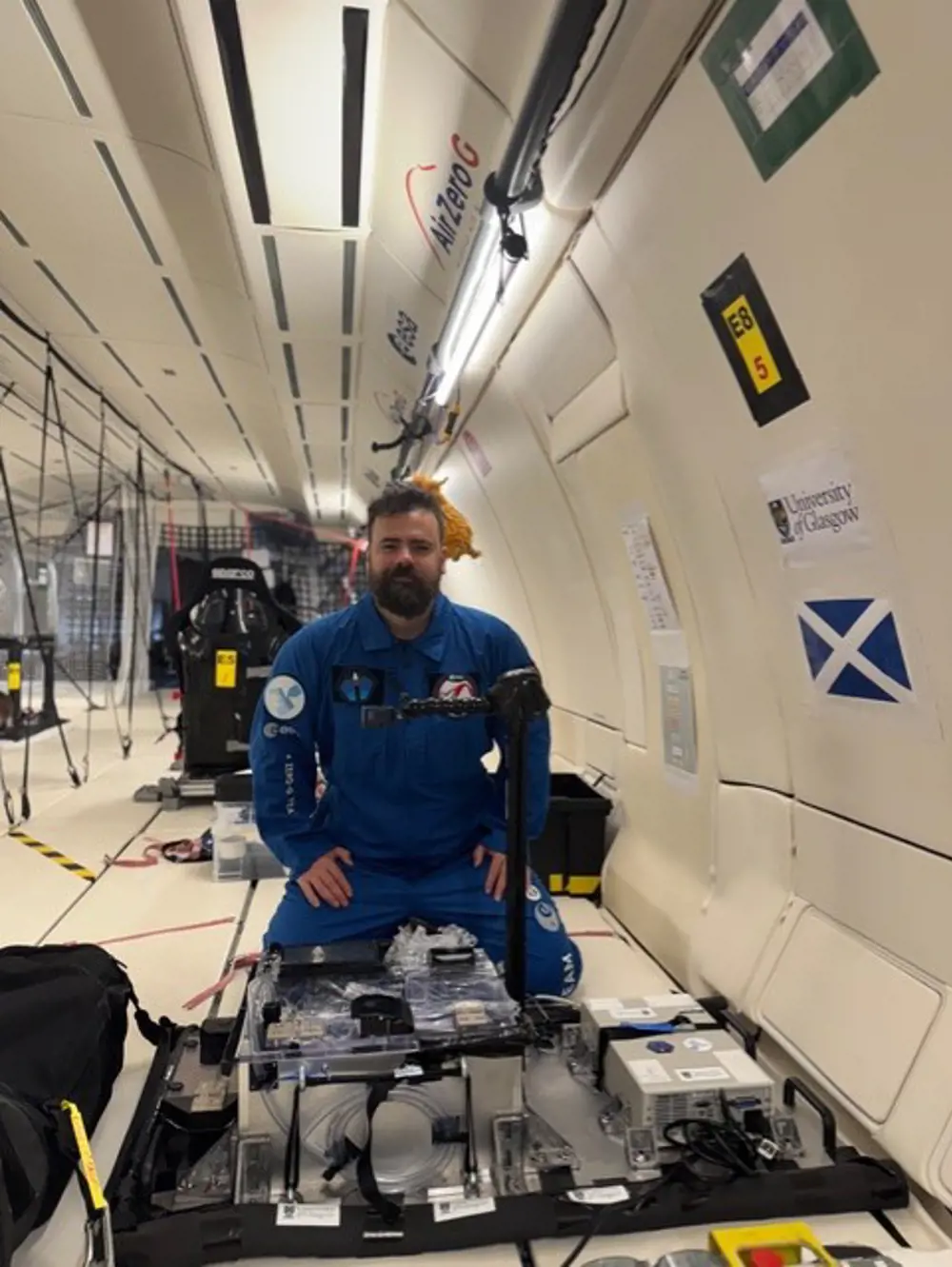
Gilles awaiting take-off on board the Air Zero G plane
To address these challenges, we have developed and patented a granular 3D printing material for microgravity. This method avoids the complexities of traditional systems by eliminating the need for spools, curing processes, and consumables. Instead, we use a purely mechanical system with anti-clogging mechanisms to transport feedstock efficiently. A second breakthrough was creating a technology that allows us to reload the 3D printer while it’s operating, eliminating interruptions and minimising failure risks.
Heightened senses: on board a parabolic flight
Testing these technologies in microgravity was a critical step in validating their potential. I’ve always been passionate about testing innovations in extreme conditions, and parabolic flight provided the perfect environment to do so.
I’ve done quite a bit of skydiving, so I thought parabolic flight would feel familiar. I couldn’t have been more wrong. Microgravity sharpens your senses, making everything feel more vivid. Astronauts training with us described how the heightened blood flow to the brain enhances perception, and I could feel it myself. Having worked on this experiment for years, I was hyper-focused during the first flights. The stakes were high, and every detail mattered. When our initial tests matched our best-case simulations, it was a massive relief.
Floating freely in microgravity, I felt a surreal connection to the physics that inspired my career. It was a reminder of why I pursued space engineering in the first place.
Floating freely in microgravity, I felt a surreal connection to the physics that inspired my career. It was a reminder of why I pursued space engineering in the first place. As the tests progressed, I began to relax, appreciating the unique sensations of weightlessness and the opportunity to witness years of hard work come to life in real time.
Building on the success of these foundational technologies, the next step is to 3D print active systems – structures embedded with electronics. This step is critical for creating spacecraft that can evolve and adapt over time. We’ll begin by testing these techniques in ultra-vacuum environments on Earth before advancing to in-flight demonstrations.
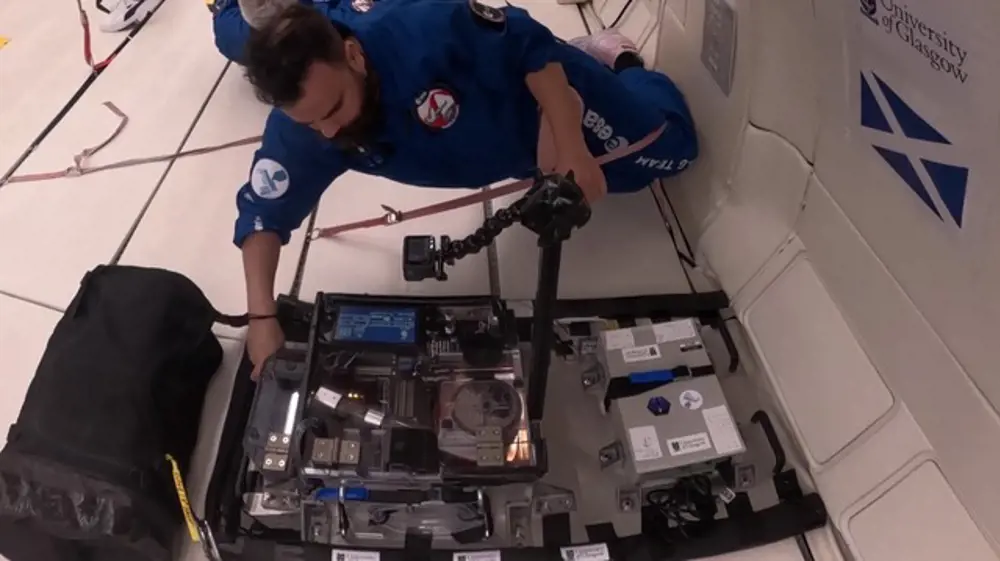
“Having worked on this experiment for years, I was hyper-focused during the first flights. The stakes were high, and every detail mattered,” says Gilles. “When our initial tests matched our best-case simulations, it was a massive relief.”
💫 The funding programmes that made these parabolic space experiments possible
Dr Gilles Bailet's in-space manufacturing programme has been supported by a Royal Academy of Engineering Chair in Emerging Technologies held by Professor Colin McInnes FREng, along with funding from a Royal Academy of Engineering Proof of Concept Award. The programme is investigating space technologies at extreme length scales – so a femto-satellite developed by Dr James Beeley was also flown as part of the experiment package.
Additional funding to support the parabolic flight from the University of Glasgow’s Glasgow Knowledge Exchange Fund and the EPSRC Impact Acceleration Account has been led by Dr Gilles Bailet. The microgravity demonstration was part of the 85th European Space Agency Parabolic Flight Campaign. Conducted in collaboration with Novespace, this saw Dr Gilles Bailet, Professor Colin McInnes, and Mr Satyam Bhatti fly in microgravity to operate the experiment. Dr James Beeley provided ground-based support at Glasgow.
A further cornerstone of our progress is the UK Space Agency’s Enabling Technology Program, led by our group in partnership with the UK Manufacturing Technology Centre, which is vital for both the technological and business sustainability of our work. This initiative not only supports the development of new materials and methods, but also ensures that safety, environmental responsibility, and economic feasibility are at the forefront. By rigorously testing materials in space-like conditions, we’re minimising risks associated with defects that could lead to structural failures or space debris. This program is paving the way for creating technologies that are not only innovative but also responsible.
Our vision is bold yet achievable: a future where in-space manufacturing transforms how we build, repair, and sustain our presence beyond Earth. This vision doesn’t just advance space exploration – it reshapes it entirely, creating opportunities for deeper interplanetary missions and fostering a sustainable presence in orbit.
***
🧬 Why we should be making cancer immunotherapy drugs in space too
Contributors
Dr Gilles Bailet is a lecturer in space technology at the University of Glasgow.
Keep up-to-date with Ingenia for free
SubscribeRelated content
Aerospace
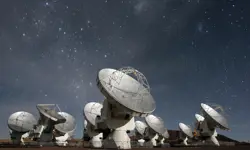
ALMA – the high altitude observatory
The Atacama Large Millimetre/submillimetre Array (ALMA) is the largest and most expensive ground-based telescope built, revolutionising our understanding of stars and planetary systems. Building it in the Atacama Desert in Chile required the ingenuity of hundreds of engineers.
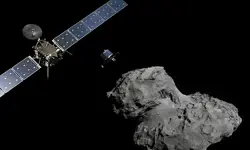
Communicating with outer space
The Royal Academy of Engineering awarded a team at BAE Systems the Major Project Award in June 2016 for their development of a powerful satellite modem system, pivotal in enabling the precise control of the pioneering Rosetta spacecraft and the first-ever soft landing of a spacecraft on a comet.
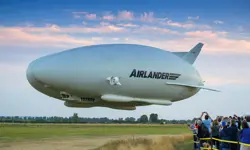
An aircraft like no other
The Airlander made headlines when it embarked on its first test flight in August 2016 as the world’s largest aircraft. Chris Daniels at Hybrid Air Vehicles Limited, and David Burns, Airlander’s Chief Test Pilot, talk about the engineering that helped it reach this stage and plans for the craft’s future.
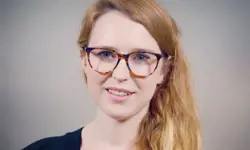
Q&A: Lucy Harden
Lucy Harden is a mechanical engineer on BAE Systems’ Digital Light Engine Head-Up Display development programme. She devises innovative solutions for pilots to display essential flight information that sits directly in their line of sight and is overlaid onto the real world.
Other content from Ingenia
Quick read
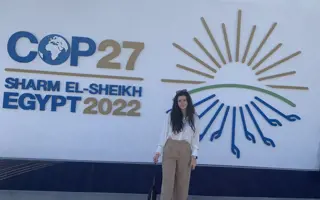
- Environment & sustainability
- Opinion
A young engineer’s perspective on the good, the bad and the ugly of COP27
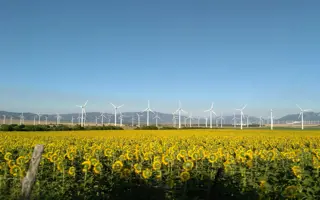
- Environment & sustainability
- Issue 95
How do we pay for net zero technologies?
Quick read
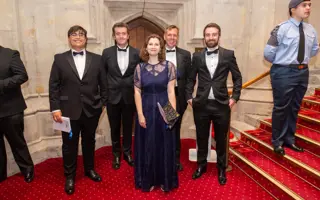
- Transport
- Mechanical
- How I got here
Electrifying trains and STEMAZING outreach
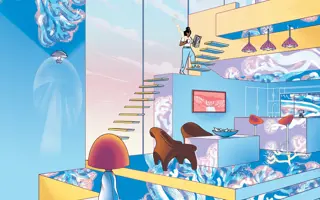
- Civil & structural
- Environment & sustainability
- Issue 95