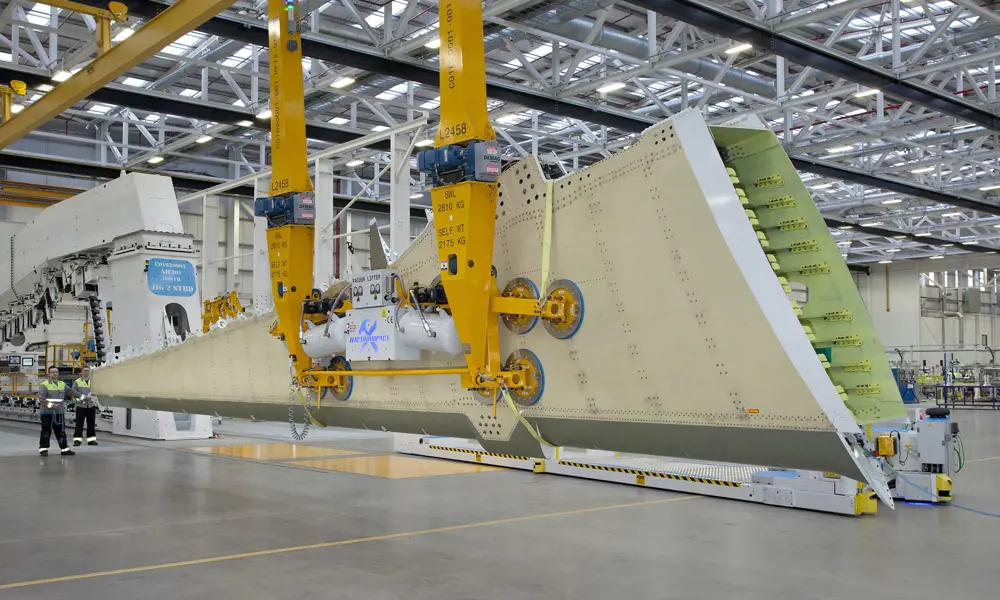
Composites take off
Truly revolutionary advanced innovations in materials technology do not come along every day. Bombardier’s composite aircraft wing is a rare example of a leap forward in materials and manufacturing engineering that has changed how this industry works. It underpins the success of the Airbus A220, which made its maiden flight in September 2013 and entered service in July 2016 as the Bombardier C Series. The plane was made to fit into the 100- to 150-seat market, which has increased in the last decade and Airbus has picked up a significant proportion of the new sales in this area. This is due in no small measure to its composite wing, with attendant reduction in assembly line costs and improved lifecycle maintenance savings.
The MacRobert Award, a rare accolade for materials and manufacturing innovation, was awarded to Bombardier for the patented resin transfer infusion (RTI) process used to make the wings. The patent protection covers the RTI process and the tooling needed to make it happen. Before this innovation, only small-scale pieces could be made by resin infusion. The Bombardier wings represent a huge jump in application as the largest and most complex structure designed using this technology.
A long track record of developing composites
Bombardier’s Belfast operation had been researching and developing composites since the 1970s. It was involved in the Next Generation Composite Wing project, a government-backed three-year programme, launched in 2008, which brought together leading aerospace companies in a £103 million research and development initiative that helped to put the UK at the forefront of the use of composites in aircraft.
Composites had already been making steady inroads into aerospace. Most composites that go into today’s aircraft programmes start with a material that arrives as a tape pre-impregnated with resin (pre-preg). This relies on curing the material under high temperature and pressure, usually in an autoclave, to bind the fibres together to create a hard and durable structure. The pre-preg material used by other large airplane manufacturers has to be stored in a deep freeze and material is wasted if left at room temperature for too long.
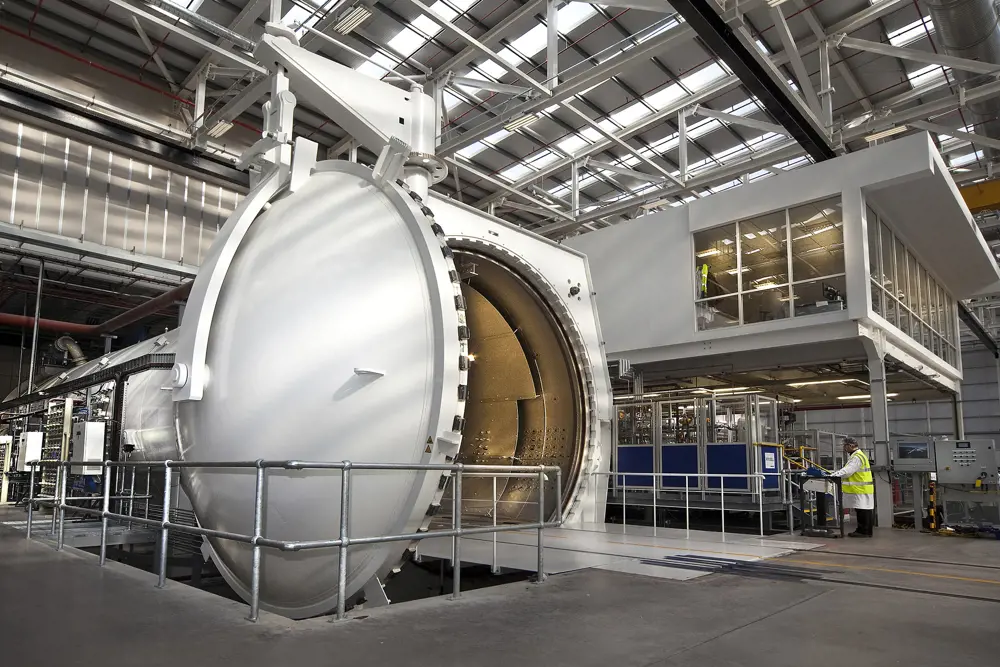
The autoclave area in the Wing Manufacturing and Assembly Facility at Bombardier Belfast where the wings are cured © Bombardier
Bombardier decided to use ‘dry’ fabrics placed in moulds to create the structure. Liquid resin is then injected into the structure before heat and pressure are used to cure the composite in the autoclave. It soon became clear that this RTI process created new possibilities. It meant that large complex structures could be manufactured as single pieces, which in turn reduced the need to make many different parts that have to be assembled with mechanical fasteners or glued together after production. This approach offered significant material savings and reduced manufacturing times.
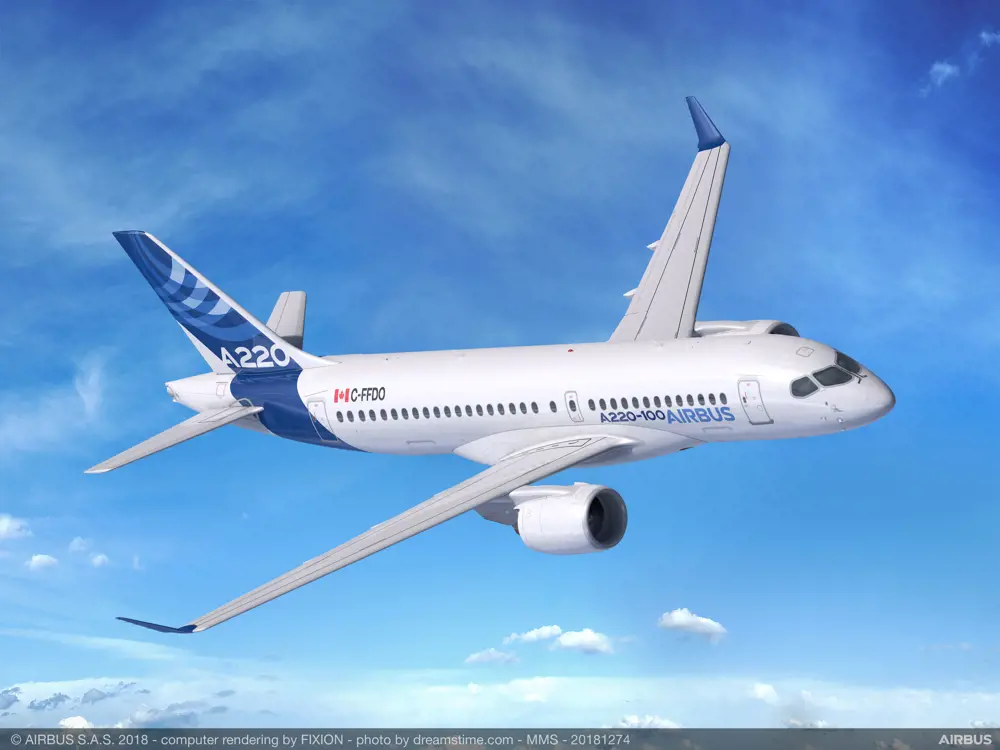
A220-100 aircraft in flight © Airbus
Extensive product testing to ensure reliability
Bombardier decided to create a composite wing as part of a development project for the Bombardier C Series of narrow-body, twin-engine, medium-range jet airliners. The CS100, (now known as the Airbus A220-100), required a 35-metre wing for its planes that would carry between 100 to 150 passengers.
Introducing a new material into something as safety-critical as aerospace needs extensive research to prove that the design, manufacturing and assembly can deliver safe and reliable components that meet all the stringent certification requirements for any new aircraft. This process involved a research and development programme that entailed thousands of individual material and component tests.
The development programme also included producing a full-scale, three-quarter span, pre-production wing. This was tested to ultimate load, replicating 150% of the most severe forces that the wing is likely to experience in service. The data collected from all the tests then fed into optimising the design of the production wings.
One of the major challenges in wing design is coping with lightning strikes. A carbon fibre structure is less conductive than aluminium, so engineers needed to address a number of challenges to receive certification, not least because it was a brand-new design. Punctures at fuel-tank boundaries and arcing from fasteners, interfaces and system installations can be prevented by designing appropriate electrical pathways and ensuring there are no gaps that create sparks. To do this, Bombardier has developed and patented high-resistance components and support brackets, which were validated through 3D computational electromagnetic modelling.
This was tested to ultimate load, replicating 150% of the most severe forces that the wing is likely to experience in service
Environmental improvements
✈️ State-of-the-art aerodynamics and recycling composite wings
The new RTI material process has led to a significant improvement in the environmental performance of aircraft of its size and range. “The composite wing enables the lightest, and most fuel-efficient aircraft in its class in the Airbus A220, contributing significantly to the reduction of CO2 from air transport,” says Parker. “While aircraft contribute only 2% of man-made CO2 to global warming today, if we do nothing, they will soon be a major contributor.” The lighter wing not only results in reduced fuel burn but in a reduction in NOx emissions because of the state-of-the-art aerodynamics.
The dry fibre used by the Belfast team can be stored at normal room temperature condition, reducing energy and wastage, unlike pre-preg material, which requires refrigeration to maintain the resin texture.
Offcuts of the pre-preg material cannot be reused and usually end up in an incinerator or as landfill. However, the dry fibre offcuts can be recycled and reused for other chopped or short fibre composite products.
It isn’t just the composite wing, however, that contributes to the Belfast facility’s ‘green’ credentials. The new wing factory includes sustainable initiatives that include recycling stations to segregate waste for reuse or recycling. The factory also employs specialised equipment to optimise energy efficiency and reduce environmental impact.
In another first, the largest rooftop solar installation in Ireland, and one of the biggest in the UK, helps to reduce the company’s reliance on fossil fuel and its energy costs. Installed in 2015, the roof of the wing manufacturing and assembly facility has 14,000 solar photovoltaic panels, generating annually approximately 2,800 megawatt hours of renewable energy for Bombardier.
Engineering new materials, and ways to work with them, is just a part of the innovation process. Engineers also have to devise new processes and approaches to manufacturing. Most commercial aircraft wings are made of aluminium alloy. They have a large number of individual parts manufactured from pieces of plate, extrusion, forgings or sheet material. These metal parts are machined and formed to the required shape. These individual parts are then put together with rivets and bolts to create the wings.
Complex fabrication and assembly processes used for turning sheets of metal into wings are no help when you want to take deliveries of fabric at one end of the production line and deliver whole wings at the other end. Bombardier set up a production and assembly line in a new 56,000 square metre facility in Belfast which was opened in 2010. This £520 million investment in the aircraft wing programme is the largest-ever, single inward investment in Northern Ireland, and one of the largest in the UK.
Under one roof it receives raw carbon-fibre material, and then handles cutting and lay-up. There then follows the RTI production system, non-destructive testing, wing assembly and testing, through to delivery of completed wings.
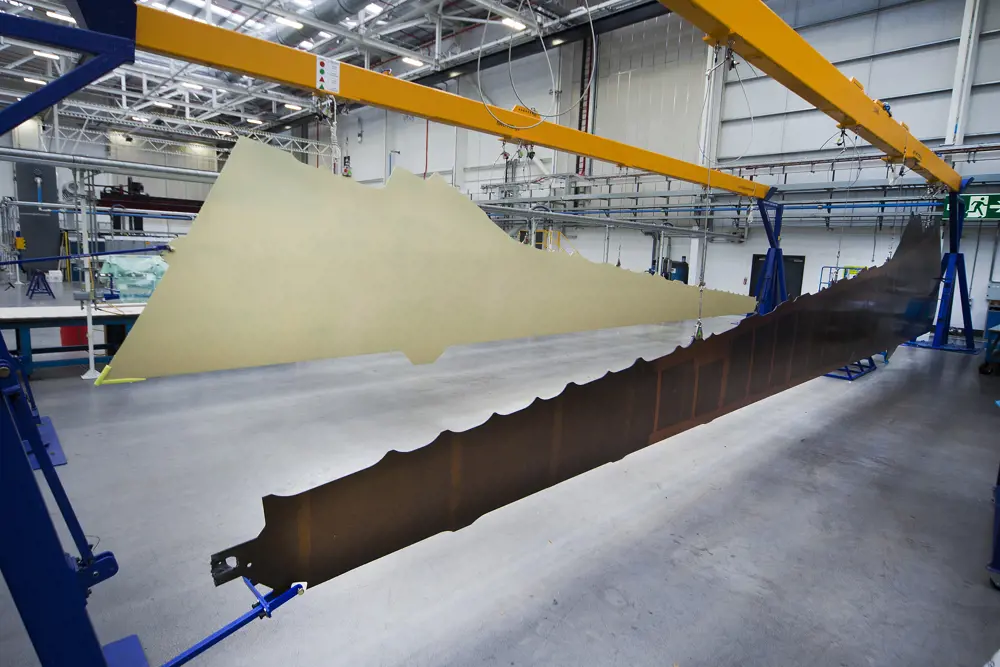
A one piece A220 wing skin produced by the RTI process © Bombardier
Increasing applications beyond wing development
The impact of Bombardier’s expertise in advanced composite components goes beyond developing and supplying wings for the Airbus A220. The company’s portfolio of composites runs to around 30 components, including nacelles (a housing that holds engines, fuel or equipment), landing gear doors, and flight control surfaces, such as flaps, ailerons, elevators and rudders. RTI composites are also used in the horizontal stabiliser for the Bombardier Global 7500 business jet.
In addition, the Belfast operation uses the process to make fan-cowl doors for the supplemental type certificate repair market – issued when Federal Aviation Administration approval has been given to modify an aeronautical product from its original design. This involves replacing the honeycomb interior of fan-cowls with a monolithic structure, resulting in a one piece, lighter and more durable component.
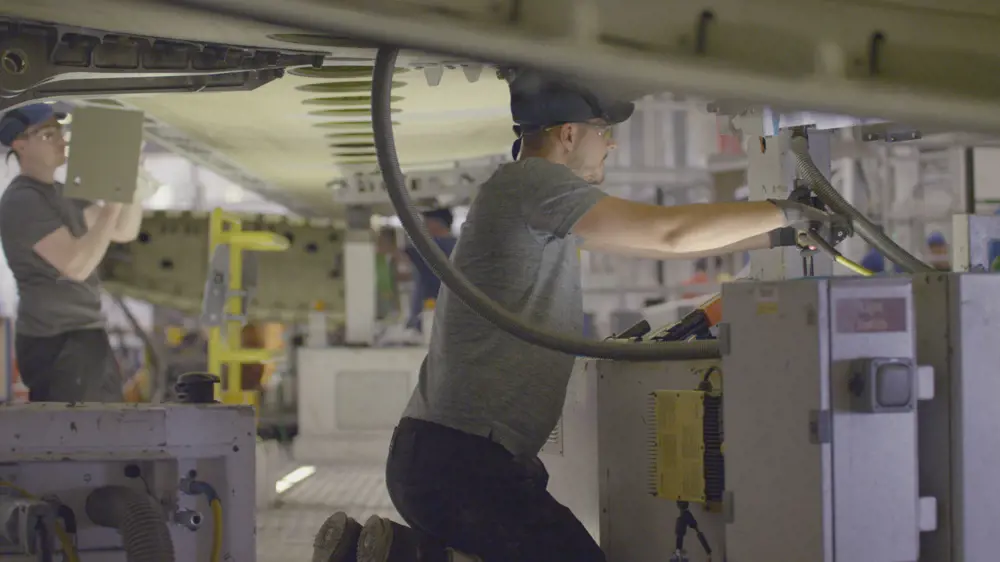
Bombardier aircraft fitters work on kitting out the wing in final assembly before despatch © Bombardier
Overall, the new wings have been a great success for Bombardier, their sales helping deliver the first company profit for five years in 2018. The company delivered more than 25 wing sets in 2018, and this is expected to increase significantly in 2019.
The Belfast facility also taps into around 200 suppliers across the UK that provide materials, systems hardware, parts, equipment and services for the wing programme, with many more throughout the whole supply chain. Bombardier’s own workforce on this wing programme will include 1,000 people at peak production and thousands more in its wider supply chain.
Bombardier’s trailblazing in the development of composites for aerospace applications has paid off both financially and with the engineering peer recognition provided by this latest award. Michael Ryan CBE FREng, Aerostructures Chief Operating Officer at Bombardier Aviation, said: “We’ve been developing our advanced composite expertise in Belfast for half a century now and it’s an immense honour to receive the gold medal in the MacRobert Award’s 50th year.”
Contributors
Michael Kenward OBE
Author
Keep up-to-date with Ingenia for free
SubscribeRelated content
Aerospace
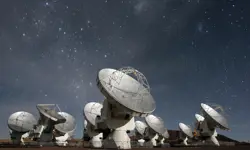
ALMA – the high altitude observatory
The Atacama Large Millimetre/submillimetre Array (ALMA) is the largest and most expensive ground-based telescope built, revolutionising our understanding of stars and planetary systems. Building it in the Atacama Desert in Chile required the ingenuity of hundreds of engineers.
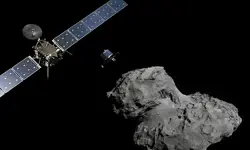
Communicating with outer space
The Royal Academy of Engineering awarded a team at BAE Systems the Major Project Award in June 2016 for their development of a powerful satellite modem system, pivotal in enabling the precise control of the pioneering Rosetta spacecraft and the first-ever soft landing of a spacecraft on a comet.
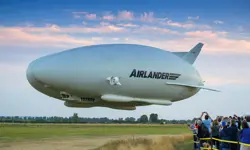
An aircraft like no other
The Airlander made headlines when it embarked on its first test flight in August 2016 as the world’s largest aircraft. Chris Daniels at Hybrid Air Vehicles Limited, and David Burns, Airlander’s Chief Test Pilot, talk about the engineering that helped it reach this stage and plans for the craft’s future.
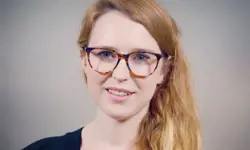
Q&A: Lucy Harden
Lucy Harden is a mechanical engineer on BAE Systems’ Digital Light Engine Head-Up Display development programme. She devises innovative solutions for pilots to display essential flight information that sits directly in their line of sight and is overlaid onto the real world.
Other content from Ingenia
Quick read
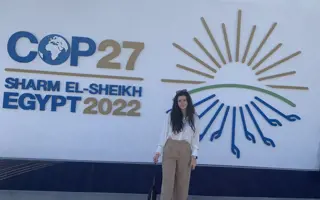
- Environment & sustainability
- Opinion
A young engineer’s perspective on the good, the bad and the ugly of COP27
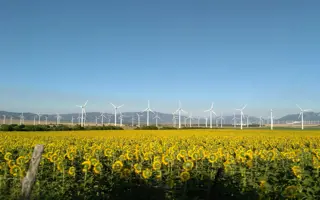
- Environment & sustainability
- Issue 95
How do we pay for net zero technologies?
Quick read
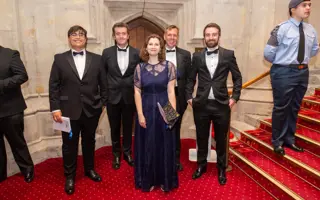
- Transport
- Mechanical
- How I got here
Electrifying trains and STEMAZING outreach
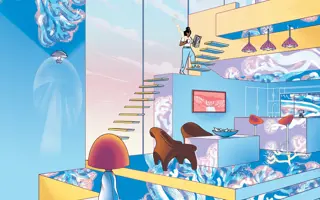
- Civil & structural
- Environment & sustainability
- Issue 95