
Compact diesel filters
This cutaway display of a 2 litre diesel engine shows the compact catalytic soot filter is so small – about 15 cm – that it can fit directly on a car engine’s turbocharger. Heat loss to the environment during normal driving and high temperature regenerations is minimised, and, during regenerations heat is released close to the trapped soot; there are no other costly components or lengthy pipes that have to be heated © Martyn Twigg
The rapid expansion of the European diesel car market has been matched with increasing regulations governing emissions of potentially harmful soot, carbon monoxide and hydrocarbons. Johnson Matthey has been leading the field in combating these emissions and were one of the 2008 MacRobert Award finalists with its compact catalytic soot filter that prevents all three pollutants from entering the environment. Dr Martyn Twigg, the company’s Chief Scientist, describes the key technical challenges that were overcome to bring this efficient and hugely successful product to market.
Decades ago, a diesel-engined car was a curiosity, but the introduction of turbo-charged high-speed direct injection engines has provided a range of technical benefits: high torque at low speed, responsiveness and power, less noise and vibration and very good fuel economy. Such clear advantages have proved popular in a fiercely competitive commercial market and have resulted in a huge increase in diesel-powered motor cars to the degree where over 50% of new European cars now have a diesel engine.
Diesel engines are fuel-efficient and produce less carbon dioxide than petrol engines but controlling their exhaust emissions has always been challenging. In the past, diesel lorries produced clouds of particulate matter in the form of black smoke when accelerating or going up hills.
Today’s diesel car engines are much more sophisticated: very-high-pressure systems enable fuel injection via several fine nozzles into the cylinders and ‘common-rail’ arrangements permit multiple, rather than single, injections of fuel.Combustion is further enhanced by boosting the amount of air available by turbocharging and through controlling the cylinder charge motion, resulting in much less particulate matter than was previously the case.
Legislation
Yet in spite of reduced emissions, concerns remain about diesel particulate matter (PM) entering the environment (see adjoining box on Particulates) and legislation is steadily driving down levels of permitted emissions. Car PM limits have decreased by more than an order of magnitude since 1983, and the PM emissions that will be permitted under the next level of European legislation – which will start to be phased in during 2009 and applied to all new models from 2010 – can only be achieved by fitting particulate filters.
Equally demanding regulations will be introduced for heavy-duty vehicles at about the same time, leading to filters being necessary on trucks and buses. Related legislation in other parts of the world will see filters fitted to diesels more widely in the not-too-distant future, and these filters will significantly contribute to improved air quality.
Particulates
Particulate matter (PM) is a by-product of engine combustion. In a diesel engine, air is compressed in the cylinders, it becomes hot; then finely atomised fuel is injected at high pressure directly into the hot gas, where it spontaneously burns to produce heat and a rapid increase in cylinder pressure.
Rapid burning leads to evaporation of the atomised fuel droplets and combustion takes place in a fuel-rich zone limited by ingress of oxygen, which in turn results in the formation of carbon from reactive intermediates. As the exhaust gas leaves the engine it cools and the high surface area of the resulting PM enables it to absorb substances present in the exhaust gas. Substances include: unburned hydrocarbons, partially combusted products, sulphur oxides, and nitrogen oxides that are formed during combustion, as well as ‘inorganic ash’ derived from lubrication oil additives used for anti-wear and anti-oxidant properties, and detergents to keep PM in suspension in the oil.
The more commonly used oil additives contain phosphorus, calcium, zinc, magnesium, and sulphur. As small amounts of oil are inevitably burned, these elements can be present in the engine’s exhaust gas and become trapped in the filter along with other inorganic matter and material from engine wear. Although the rate of ash accumulation in the filter is gradual, its presence does increase the filter’s backpressure. While not reduced by the high temperature regenerations that remove carbonaceous PM, this backpressure can be minimised by using a large filter, or ‘ashless’ lubrication oils (with reduced levels of inorganic additives), or by using filters with asymmetric channel structures that provide a larger inlet volume compared to that in the outlet side.
How the filter works
Several ceramic and sintered metal diesel particulate filters have been developed that prevent PM entering the environment. The most successful and commonly used commercially are porous ceramic wall-flow filters based on a honeycomb structure of channels. Alternate channels are plugged at one end so that the exhaust gas is forced through the channel walls, while the soot is trapped in the filter.
As particulate matter accumulates in the filter, the backpressure across it increases, which, when excessive, degrades engine performance and ultimately stops the engine from working; it is crucial that the backpressure stays within a pre-determined limit, requiring the PM to be removed from the filter. The best way of doing this is to oxidise it into carbon dioxide and water in a process called regeneration, which involves careful burning of the PM to remove it and reduce the backpressure.
Since diesel car exhaust gas temperatures rarely exceed 250°C during town driving, and diesel soot does not usually burn unless the temperature is above 550°C, an ‘active’ regeneration must be used to periodically increase the gas temperature to the higher value. This is done by late injection of fuel into the engine, even when the exhaust valves are open; some of the fuel burns and the rest is oxidised over an upstream oxidation catalyst taking the gas temperature to above 550°C.
Typically, regeneration is done every 400 to 2,000 km depending on driving conditions. While all the trapped soot is removed from the filter, which may take up to 10 minutes, the rate of particulate matter oxidation, and hence the rate of heat release and the peak temperature, is carefully controlled by the car’s onboard computer using techniques such as reducing the amount of oxygen available by throttling the engine.
Commercial filter systems
Three commercial filter systems have been developed for cars. The first – introduced in 1999 and using a base-metal fuel additive to lower PM combustion temperature – has one or more platinum-based oxidation catalysts in front of the filter to control hydrocarbon and carbon monoxide emissions during normal driving. The catalyst oxidises unburned fuel when it is injected into the engine to raise the exhaust gas temperature for controlled regeneration. It works well, although it is costly and fuel additive residues are retained in the filter as inorganic ash. This ash contributes to a gradually increasing higher backpressure across the filter.
Many cars now use the second system, which also has one or more upstream oxidation catalysts, plus catalysts in the walls of the filter to promote PM combustion, so a fuel additive is not needed.
Innovation is the catalyst
Both of these designs were unfortunately rather complex and heavy, using several units in individual housings. For third-generation developments, we realised that if sufficient appropriate catalysts could be put into the filter, separate upstream catalysts might not be needed. Also, by integrating catalysts into a single component design, it could be located close to the engine where the exhaust gas is hotter, so improving catalyst performance during normal driving as well as enhancing heat retention during regenerations.
To prove the concept of this novel ‘third-generation filter system’, we equipped cars with prototype catalytic compact filters. We used five cars fitted with various single-component designs engineered to be as close to the engine as possible.The first car ran successfully for more than 100,000 km, demonstrating the compact soot filter’s good durability. Control of hydrocarbons and carbon monoxide emissions were excellent, and regenerations were smooth and complete.
It is thermally efficient because there is only the filter to heat during regenerations, so heat losses to the environment are minimised, and the oxidation reactions used to boost the temperature actually take place in the filter, creating heat close to the trapped PM. It also has fewer components than earlier designs, so is less expensive, but the missing pieces of the jigsaw essential to realising the concept required the development of new catalysts and new manufacturing processes – and a huge amount of extended testing.
Meeting technical challenges
The first challenge surrounded catalysis and the need to meet multiple requirements. The catalyst had to remain durable in the face of severe conditions in the filter during repeated regenerations (with temperatures up to 1,000°C or more, well above the maximum for the separate oxidation catalysts used in previous systems), tolerate inorganic ash and elements from the engine trapped in the filter, and be active during low temperature town driving to remove carbon monoxide and hydrocarbon pollutants.
New formulations were developed that met all these competing demands, yet there was no process available to locate precisely the required special catalysts within the filter. With traditional emissions control catalysts, a thin layer of catalyst is applied to the channel walls of a ceramic honeycomb and the exhaust gas flows along these open channels. In a filter, the gas has to flow down the channels and through porous channel walls; catalysts cannot be applied to the surface of the channels because it would block gas flowing through the walls. Instead, catalysts must be located with precision in the channel walls, so a new manufacturing process was needed – both to place the special catalysts in specific locations in the filter walls and to place different types of catalyst in different parts of the filter.
This ‘catalyst zoning’ approach was a key to achieving further cost savings because we could place special catalysts in those areas of the filter needing it most and use less expensive catalysts, like palladium, in areas not requiring as much catalyst activity. The new robotic process we developed uses vacuum to achieve the essential precision location of catalysts in filter walls in different zones.
Compact result
This new process enables precise amounts of nano-sized catalysts on micro-sized, thermally stable materials to be placed in the filter walls at precise locations along its length. Being just a single unit, much less manufacturing energy and materials are needed than in previous designs and this, together with its optimised production, makes the Johnson Matthey Compact Catalytic Soot Filter particularly cost-effective.
It is small enough to fit directly on the turbocharger in the restricted space on the engine. In this location, heat losses are minimised, so thermal efficiency is high and all the exhaust heat is available to catalytically remove hydrocarbon and carbon monoxide pollutants while driving. High thermal efficiency also means that less fuel is used in initiating the carefully controlled periodic burning of soot trapped in the filter.
Rapid expansion
An existing pilot facility was converted to a production plant while the main plant was being designed and constructed.Increasing demand meant this first plant, which was completed in 2005, immediately went into full-scale production.Output increases were achieved in a very short timescale, and other plants were subsequently constructed in South Africa and the USA. A second plant was completed in Royston to support further market expansion.
Already, nearly two and a half million units of the compact soot filter have been manufactured in Royston and exported to Europe. Not only is this becoming a major revenue stream for Johnson Matthey, it is significantly contributing to cleaning the air we breathe.
Further reference
http://www.matthey.com/
BIOGRAPHY – Martin Twigg
Martyn Twigg is the Chief Scientist of Johnson Matthey plc. Following postdoctoral work at the University of Toronto and a fellowship at the University of Cambridge, he joined ICI in the North West of England and later moved to Billingham, where he worked on the development and manufacture of heterogeneous catalysts for the production of hydrogen, ammonia and methanol. Martyn Twigg has authored or co-authored almost 200 research papers and holds more than 50 published patent families on catalysts and catalytic processes. He co-edits the Springer book series Fundamental and Applied Catalysis.
Keep up-to-date with Ingenia for free
SubscribeOther content from Ingenia
Quick read
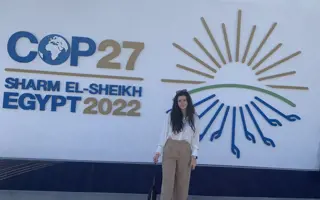
- Environment & sustainability
- Opinion
A young engineer’s perspective on the good, the bad and the ugly of COP27
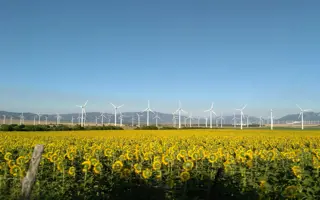
- Environment & sustainability
- Issue 95
How do we pay for net zero technologies?
Quick read
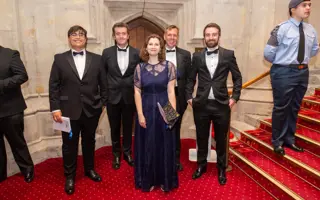
- Transport
- Mechanical
- How I got here
Electrifying trains and STEMAZING outreach
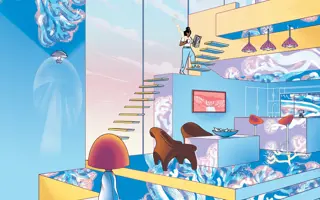
- Civil & structural
- Environment & sustainability
- Issue 95