
Built on principles: White Collar Factory
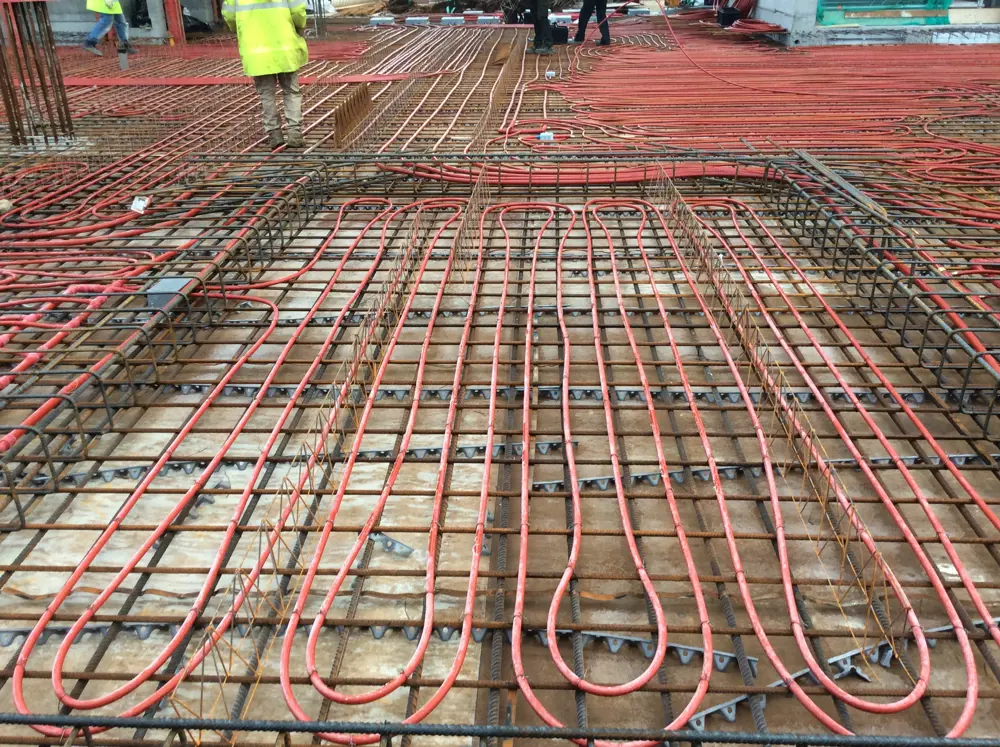
Red pipes that will carry chilled water for the concrete core cooling are laidover the mesh of reinforcing steel, before concrete is poured over both to create one of the floor slabs © Arup
It all started in 2008 with the property crash. While many construction projects stalled, property developer Derwent London decided to commission a research study into what the next generation of offices would be like and appointed three regular consultants – architect AHMM, and engineers Arup and AKT II – to do the work. The brief was simple: given an unconstrained site, what would be the ideal office building? What would it look like, how would it work and who would use it? It had to be sustainable, adaptable for changes in use, and inexpensive to build and operate.
Naturally enough, the team started with its previous experiences with Derwent in London. This had been almost exclusively in conversions of old factories, warehouses or office buildings that had reached the end of their lives, such as the Tea Building in Shoreditch (once, the Lipton Tea factory).
What would be the ideal office building? What would it look like, how would it work and who would use it?
These conversions had to accommodate the buildings’ robust frames, usually concrete columns and concrete floors, with (by modern standards) close column spacing and often low ceiling heights. The solutions for these existing buildings included flexible open-plan offices, albeit with columns; exposed services with no false ceilings; exposed interior concrete to make use of thermal mass; and as much natural ventilation as possible. The market was initially sceptical, but soon a new breed of London tenant – often young creative or technological companies – came to embrace the new approach. They did not mind the close-spaced columns or the ‘unfinished’ ceilings, and they liked the natural, more sustainable, ventilation, especially, when offered, the ability to open the windows.
These young tenants were now expanding into substantial firms, and others were beginning to catch on. The team decided that this was the future London office market. So why not, for the first time ever, design a new office building that applied the lessons learnt on converting old warehouses and factories, but that was unconstrained by the limitations of building around what was there before? The concept of the White Collar Factory was born.
This meant challenging some of the principles that often governed the London property market, in particular, the belief that the environment inside the office should be specified by the required air temperature. Comfort depends on many more things than that, including the radiant temperature of surfaces, air movement and humidity, and the team believed that achieving ‘comfort’ could be done with much less air conditioning. It also meant keeping things simple: no frills, highly adaptive, inexpensive and easy to maintain.
Foundation
🏗️ Coping with existing subterranean complexities
Almost any development in central London has to cope with existing subterranean complexities and the White Collar Factory is no exception. A stack of services run under City Road along the east side of the building and on top are twin water mains. At the middle level are twin large-bore rail tunnels driven in 1904 through London Clay and now maintained by Network Rail. A few years later another pair of rail tunnels was driven beneath, some 20 metres below ground level and at the very bottom of the London Clay, half into the Lambeth Group beneath. Below what is now the White Collar Factory, these tunnels were widened to form Old Street station, now part of London Underground’s Northern Line.
The problem for the structural engineers was twofold: simply driving new piles for the building along the eastern perimeter of the tower would hit the edge of the tube tunnels; and even with the piles relocated, it was critical to control and monitor ground movements around the tunnels. Just a small differential movement could cause the tube trains to strike the platforms of Old Street station, or worse, hit the soffit of the narrower running tunnels as they left the station.
A cautious approach was taken with the foundations. The basement excavation was dog-legged, with the deepest part of the basement furthest from the tunnels. The foundation piles were driven down to rest on the firm Thanet Sands some 30 metres below ground, with the nearest pile at least five metres clear of the nearest tunnel. This meant incorporating into the basement a massive transfer structure – effectively two very deep one-metre thick concrete beams – to take the loads from the outer columns back towards the centre and onto the piles.
Ground movement was carefully modelled for all stages of construction, and the ‘worst case’ was found to be ‘heave’ when the existing old buildings were demolished and excavation completed, when the tunnels could rise by 20 millimetres or more. But much more important than overall movement was the differential movement within the tunnel, which could affect the clearance for trains, and this required an understanding of the rigidity of the old cast-iron lining and how it would respond to movement of the ground. Actual movement was then measured during construction, and compared with the model. To the engineers’ relief, the movement at all times remained within safe limits. Rarely has real-time movement of tunnels been measured so carefully, and the data gleaned will help with the design of future buildings over London’s underground assets.
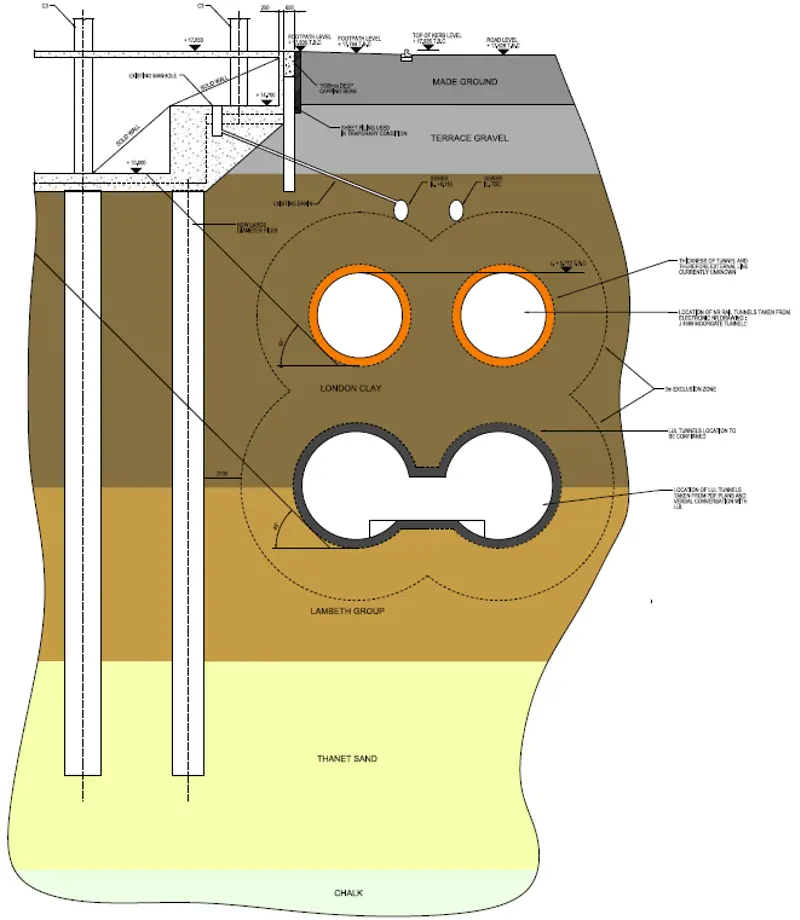
Congested services beneath the eastern edge of the White Collar Factory, with water mains (top), Network Rail tunnels (middle) and Old Street station on the London Underground (bottom), and how the basement was ‘dog-legged’ (has a sharp bend) and the loads from the perimeter columns transferred to deeppiles well away from the tunnels© AKT II
Key criteria
After several months of study, the team had established five design principles for its office of the future: high ceilings, use of thermal mass, concrete core cooling, windows that open, and flexible occupation.
Generous ceiling heights (as in old warehouses and factories) make workers feel less hemmed in, increase the penetration of natural daylight from high windows deep into the building, and improve air circulation. They can also be created by simply omitting the large false ceilings of conventional offices and leaving the services fully exposed on the ceiling, so retaining the same number of floors in a given height of building (the team retained a shallow ‘false floor’ to contain power and data cabling).
After several months of study, the team had established five design principles for its office of the future: high ceilings, use of thermal mass, concrete core cooling, windows that open, and flexible occupation
Thermal mass is the ability of a material to store heat energy. High-density materials such as concrete have high thermal mass, which can be used to help retain warmth in winter and to keep the building cool in summer. This meant building a concrete structure with sufficient mass and, equally important, with as much of the concrete’s interior surface exposed as possible. This tied in nicely with the first principle, since the absence of false ceilings allowed the soffit (underside) of the concrete slabs to be exposed.
In a modern well-insulated office in a UK climate, providing summer cooling in an efficient and sustainable way is much more challenging than heating in winter. Conventional air conditioning is energy and carbon intensive, noisy and takes up a lot of space. The White Collar Factory approach is to use passive environmental controls where possible, and a method called concrete core cooling has been introduced: chilled water pipes embedded in the reinforced concrete slabs provide radiant cooling, enhancing the natural effect of the thermal mass, and chilled water at 15°C is passed through the pipes, cooling the slab to around 20°C. The technique is used widely in Germany and Holland but less so in the UK, and never before on a London office.
Another of the maxims that the team has overturned is the belief that, to be both comfortable and energy efficient, a building must be sealed. This limits occupants’ control over their environment and their connection with the outside world, and excludes the most basic method of natural ventilation – opening a window. Calculations showed that in London weather conditions, and in conjunction with thermal mass and chilled slabs, the mechanical system could be switched off for 50% of the year and comfort provided by natural ventilation with opened windows. A traffic light system provides guidance for occupants, turning red to advise people not to open the windows when the weather is too warm or too cold.
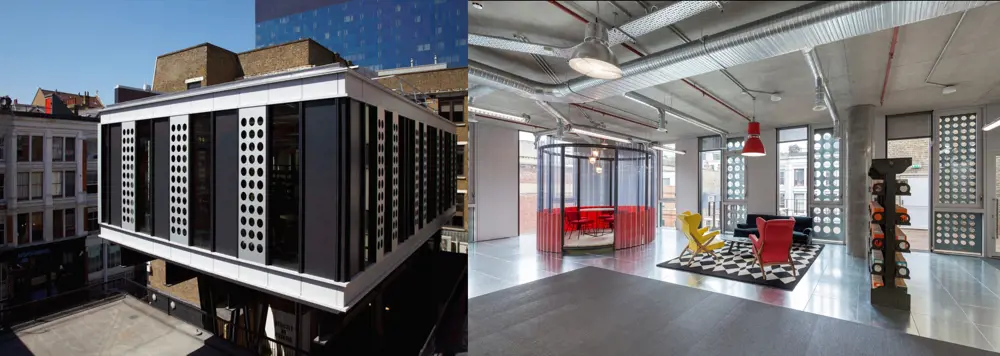
The ‘prototype’ White Collar Factory. In 2013, part of one floor perched three-storeys up in the air amid the old buildings of Old Street Yard, providing both a technical test-bed and a marketing suite. Inside shows the high ceilings with exposed services such as lighting and ventilation ductwork, and the exposed concrete surfaces to activate the thermal mass and the concrete core cooling. The façade is formed of alternating vertical strips of insulation, double-glazing and openable windows with perforated panels outside © Arup
Soundlab
🔊 From the art of modelling an auditorium to the science of replicating sound
The roots of Arup’s expertise in acoustics lie in the delicate art of designing concert halls so that they project the music in a way that delights the audience. It started with creation of the Snape Maltings for the annual Aldeburgh festival in the 1960s, led to formation of the world-leading Arup Acoustics division in the 1980s and continued with projects such as the new Glyndebourne Opera House in the 1990s. But acoustics remained more of an art than a science: since the 1950s, clients, architects and even acoustic consultants have worried about how their buildings would sound when completed. So they have had to allow lengthy periods of testing, tuning and commissioning once the building is finished, and even then, they could not be sure of a successful outcome. Even as engineers became adept at modelling the way an auditorium would reflect sound, it remained extraordinarily difficult to translate the results into anything that would indicate what the room would actually sound like.
That began to change 10 years ago with the invention of SoundLab, which uses a system of 16 loudspeakers arranged in a sphere around the listener, to replicate exactly what the music will sound like at any point in the room. SoundLab makes use of a spatial audio reproduction system called ambisonics, invented by English mathematician Michael Gerzon in the 1970s. Ambisonics is an algorithm that mimics the way that humans localise sounds in front of, behind, above and below us, in any acoustic environment, existing or yet to be built. This technology has now been combined with anechoic recordings of music (completely free of reflected sound or echoes) to simulate spatially accurate acoustic environments. Designers and musicians can change the shape or form of the room’s design, shift a balcony angle or alter the upholstery of the chairs, and compare the results. They can also make comparisons with existing halls across the world. The information is presented neutrally and quality assured to be as objective as possible. SoundLab has given designers unprecedented confidence that, when it comes to the first concert, the hall will sound as expected. Examples where it has been used include opera houses in Copenhagen and Oslo.
Now the same technology is being applied to other infrastructure and buildings, well away from the world of music. Some 25,000 people have listened to sound simulations (or ‘auralisations’ as Arup likes to call them) of the High Speed 2* rail line and were able to compare the sounds of modern high-speed trains with existing Pendolinos, at different distances and with various noise protection measures. SoundLab has also been used to reproduce the change in sound after the opening of Heathrow’s third runway and the effects of a new windfarm.
SoundLab was a natural tool for testing the principle that the windows of modern offices must be sealed shut to keep out disturbing traffic noise, particularly over noisy roundabouts such as the one at Old Street. The noise was simulated at every level over the roundabout. Results showed – and convinced letting agents and prospective tenants – that, at the higher levels of the building, the noise from open windows was all but inaudible above the normal background noise. Even at lower levels, it showed that opening the windows would be perfectly acceptable at certain times of day or for short periods.
To see SoundLab demonstrating the impact of high-speed trains on High Speed 2, visit https://www.arup.com/perspectives/soundlab
The principle of ‘flexible space’ is a response to changing office use. Tenants’ requirements are increasingly diverse, some for example requiring large open spaces and others more compartmentalised offices, and each tenant’s requirements can change over time. Large floor plates and high ceilings allow a variety of fit-outs, and quick subdivision of space if needed.
Taking these five principles further, the team established a standard column spacing of nine metres, which hit a ‘sweet spot’: any greater and the regular 300 millimetre thickness of floor slabs would have to be compromised by beams; any smaller and the columns would become intrusive and reduce flexibility. A similar compromise was reached on the façade. Conventional wisdom has it that a sustainable building requires high insulation including triple glazing, plus shading to reduce solar gain – measures that can both be costly and take up space, which reduces the office area. However, most of the benefits can be achieved with relatively simple façades by carefully balancing glazing with shade and varying the proportions depending on the orientation of the sun.
most of the benefits can be achieved with relatively simple façades by carefully balancing glazing with shade and varying the proportions depending on the orientation of the sun
All this work was translated into a ‘standard’ office design, five storeys high with a 45x45 metre floor plate, a four metre floor-to-floor height and a central services core. This was costed at a remarkably inexpensive £165 per square foot. Everything looked promising, but two major questions remained: would it work in practice, and could a conservative property market be persuaded? Derwent’s solution was simple: build a prototype that could be both a technical test-bed and a marketing suite.
In 2012, Derwent happened to be planning a development on a corner of Old Street roundabout, London’s ‘silicon roundabout’. It was decided that a small 18x18 metre section of one ‘standard’ floor would be built on the site, squeezed between the old existing buildings and perched three storeys up in the air to provide realistic exposure to sunlight. Further, a contractor (Brookfield, now Multiplex) was charged with building the prototype as if it was the ‘real thing’, providing a test of construction techniques. This also allowed for refinement of the ingredients and workmanship for achieving high-quality fair-faced concrete finishes, a notoriously difficult challenge.
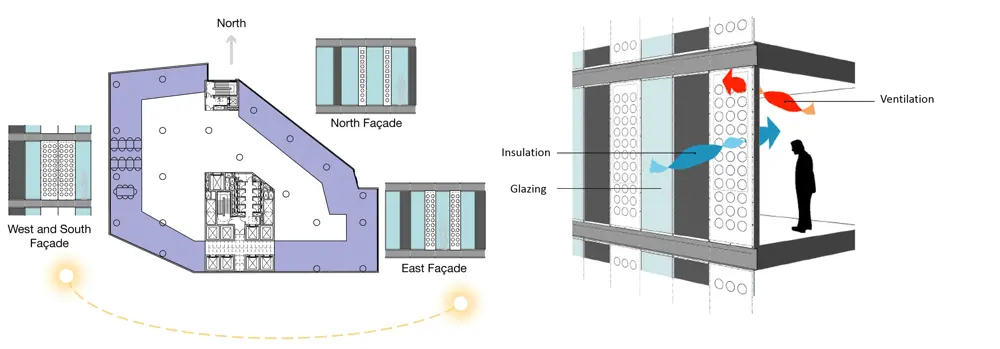
How the façade design varies according to orientation with the sun (left): more insulating panels and openable windows on the sunny south, more glazing on the north. How natural ventilation works through the openable windows behind the perforated panels, with cool air entering at lower levels and warm air escaping near the ceiling (right) © Arup
The tests, running through the particularly hot summer of 2013 and the following winter, showed that the technology worked, with close correlation between computer modelling and measurements, and allowed the design and mode of operation to be refined. The initially sceptical letting agents for the property market were gradually won over. Arup’s SoundLab, a virtual listening environment that allows clients and designers to hear the sound of existing spaces and test the sound of designs, was also used to help people understand the impact of opening windows over a noisy roundabout (see box). Meanwhile, Derwent decided to go ahead with its Old Street project, a mixeduse development including some renovated old buildings, with the White Collar Factory presiding over the northern edge, and a research project was suddenly transformed into a live design-and-construction site.
Inevitably, the ‘standard’ design had to be modified to fit the site – 16 storeys with an asymmetrical floor plan and a large basement – but all of the design principles were retained. The façade is made up of three alternating elements: full-height double-glazing, solid insulated panels, and perforated panels, which the openable windows are behind at three-metre intervals along the façade and the proportion of each element varies with orientation to the sun.
Outside air (when the windows are closed) is provided by low-pressure central air-handling units with heat recovery at roof level. Supplementary air conditioning is available to tenants to ‘top up’ the cooling on very hot days or for specific requirements. The relatively little heating required comes from conventional trench heating – simple underfloor convector units fed from gas-fired boilers by a low temperature hot-water circuit. The tower’s roof is divided between amenity space for tenants, including a running track around the perimeter, and solar thermal panels that generate electricity from solar energy, which (with the heat recovery units) fuels the hot water, including that used for the showers accompanying the 276-space cycle park in the basement.

Temperature measurements inside the prototype White Collar Factory during some of the hottest days of summer 2013, showing how the passive cooling system smoothed the peaks and troughs of outside temperatures (amber line) into a comfortable range inside © Arup
During the design stages, a case study was submitted to the government’s Technology Strategy Board (now Innovate UK) testing the building’s resilience to climate change, particularly to rising temperatures over the next 50 to 100 years. Energy and thermal comfort models were run through different scenarios, and the scope for future adaptations was tested. The results showed that with its in-built passive design measures, the building was well placed to cope. The study was turned into a Technology Strategy Board paper on best-practice design for future-proofing buildings.
[White Collar Factory is achieving] the highest possible world standards for sustainability of buildings, while the cost of construction, and the fit-out and operating costs for tenants, are substantially below the norm
Due to complete in December 2016, White Collar Factory is achieving BREEAM Outstanding and LEED (Leadership in Energy and Environmental Design) Platinum, the highest possible world standards for sustainability of buildings, while the cost of construction, and the fit-out and operating costs for tenants, are substantially below the norm. The fourth and fifth floors of the building will become the new headquarters of AKT II, a mark of the company’s confidence in what it has helped create, as well as an aid to monitoring the longer-term performance of the White Collar Factory concept.
***
This article has been adapted from "Built on principles: White Collar Factory", which originally appeared in the print edition of Ingenia 69 (December 2016).
Contributors
Hugh Ferguson
Author
Michael Stych is a Director at Arup in London and Project Leader for White Collar Factory, where he was responsible for the delivery of the building services and façade engineering, ICT and digital services, and fire, acoustics, lighting and sustainability consulting. He has over 20 years’ experience in engineering design, analysis and construction in the UK and internationally.
Rob Partridge is a Director at structural and civil engineering practice AKT II, and is responsible for leading a diverse range of projects, both in the UK and internationally.
Keep up-to-date with Ingenia for free
SubscribeRelated content
Civil & structural

Building the Shard
The Shard is one of London's most iconic buildings. The tallest in Western Europe, it was designed by Italian architect Renzo Piano and dominates the city’s skyline. Ingenia spoke to John Parker, project director for structural engineers WSP, who outlined the engineering decisions made in building the enormous steel and glass structure.

The return of arched bridges
Arch bridges are strong, durable and require little maintenance. However, very few had been built since the early 1900s until the FlexiArch was developed and launched in 2007. Now, there has been a minor renaissance for this ancient form of construction.

Creating user-friendly buildings
For Michelle McDowell, a former Business Woman of the Year, a passion for joined-up design thinking and building information modelling with a user-friendly approach has enabled her to pioneer revolutionary changes in her field.

Troja Bridge
In November 2014, one of the world’s largest network arch bridges was officially opened in Prague. The UK may soon have its first network arch bridge if the go-ahead is given for a new rail project in Manchester.
Other content from Ingenia
Quick read
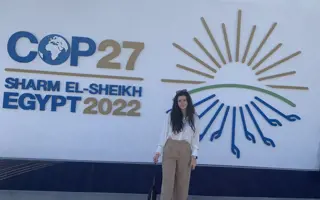
- Environment & sustainability
- Opinion
A young engineer’s perspective on the good, the bad and the ugly of COP27
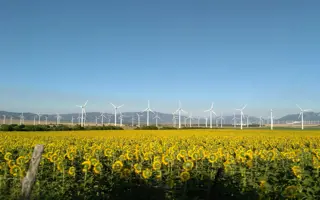
- Environment & sustainability
- Issue 95
How do we pay for net zero technologies?
Quick read
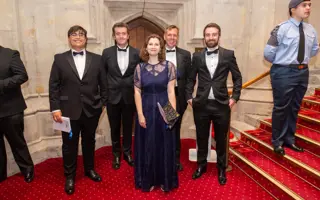
- Transport
- Mechanical
- How I got here
Electrifying trains and STEMAZING outreach
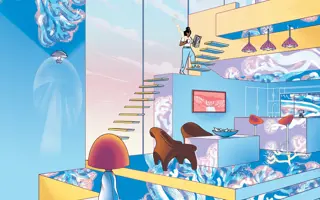
- Civil & structural
- Environment & sustainability
- Issue 95