
Bringing prehistory to life
Did you know?
- Sauropod dinosaurs had very long necks and tails, anchored by their hips, which are effectively cantilevers
- In a living dinosaur, the neck and tail would have been supported by strong ligaments running all the way along the spine
- Engineers looked to this feature of dinosaur anatomy when creating the freestanding dinosaur Fern
As museum exhibits go, it doesn’t get more iconic than Dippy. One of the most famous dinosaurs in the world, the 25-metre-long plaster cast of Diplodocus carnegii stood in London’s Natural History Museum for over a century.
When the museum sought a stunning centrepiece for its new gardens, a bronze replica of Dippy must have been a natural choice, although creating it would take some ingenuity.
The dinosaur would need to remain faithful to the beloved Dippy of old while being scientifically accurate, resist the elements and London air, and – the greatest challenge of all – stand with no visible supports. It’s something that’s never been done before.
Over the course of three years, a team of engineers, art conservators and palaeontologists collaborated to make it happen, and in July 2024, Fern was unveiled to the public. How did they do it?
A marriage of art and science
“The Natural History Museum was very clear and insistent that Dippy was the thing they wanted to recreate, not the original skeletons,” says Adam Lowe, Founder of art conservation studio Factum Arte, which the museum selected to take on the project. “The fact that the Diplodocus was a plaster cast was part of its history.”
As a start, the Natural History Museum 3D scanned every last one of Dippy’s 292 bones, which Factum Arte used as the raw material for building Fern. However, it wasn’t simply a case of immediately casting those bones in bronze – there were many steps to take first.
The team aimed to achieve a pose for the dinosaur that was not only natural and dynamic but also anatomically precise. For the latter, Factum Arte worked closely with the museum’s Professor Paul Barrett, an expert on sauropods (large four-legged dinosaurs with long necks and tails).
Dippy was first unveiled in London in 1905. Although it had been updated a few times in line with new knowledge about dinosaur anatomy and evolution – once in the 1960s to raise its neck to a horizontal position, and again in 1993 to give its tail that dramatic curve over visitors’ heads – there were further adjustments to be made.
Barrett checked each of the bone scans to ensure they aligned with current understanding. Under his guidance, the team flipped one neck vertebra, which had been upside down, adjusted the hips, corrected its slightly knocked knees, and arched the feet. “I like to think that Fern is more accurate than Dippy was,” says Lowe.
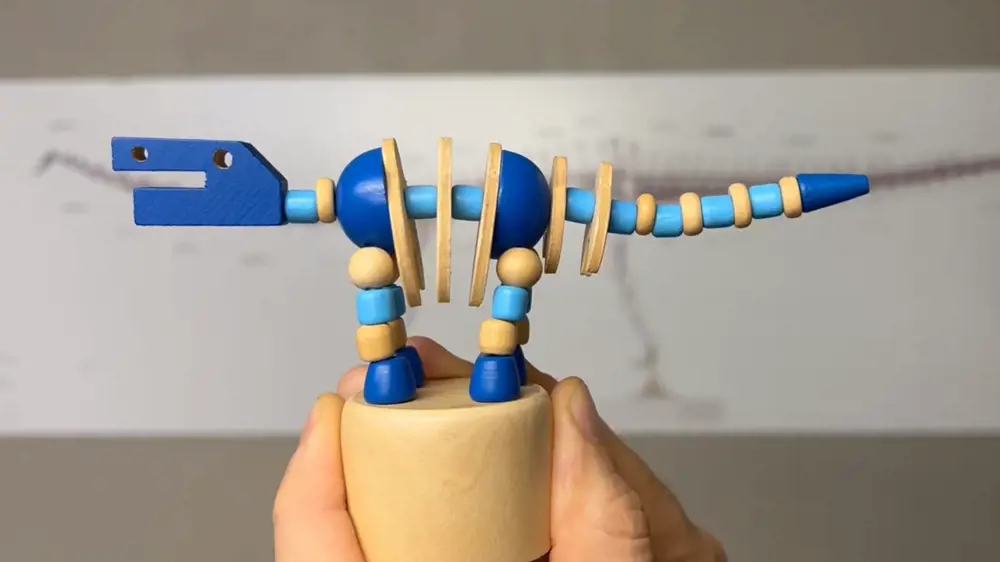
This wooden dinosaur toy is supported by cords that run through its wooden beads, just as Fern’s body is supported by a steel bar running through its spine © Structure Workshop
Engineering finds a way
As well as ensuring the structure was anatomically sound, there was the tricky job of working out how to make a skeleton stand up on its own in the absence of restraining musculature. Factum Arte brought onboard Structure Workshop to oversee the structural engineering side.
Max Clayton, an associate at Structure Workshop, says that studying the anatomy of the dinosaur was key: “It’s worth highlighting the amazing natural structure that is the real dinosaur you find after millions of years of natural selection,” he says. “Nature has come up with a lot of these solutions in a really elegant way.”
To borrow from the language of structural engineering, both Dippy’s long neck and tail are cantilevers – each is supported at only one end. In the living dinosaur, they would have been held aloft – seemingly impossibly – by strong ligaments that run all the way through the spine. These ligaments were anchored to the hip, letting the dinosaur hold its neck and tail horizontally without effort.
One of the most challenging parts of the process was thinking up a design concept to hold the structure together. Welding together the individual pieces was a no-no: “The complex biological form would have made the welding really difficult and it would be hard to actually inspect whether the welds had been done properly or not,” Clayton says. A single weld failure could be disastrous, causing the entire structure to collapse. “As engineers, we want solutions that we’re comfortable with, so we can sleep at night.”
The team had thought long and deeply about how to get the prestressed tendon system to work. The winning approach – which came to Clayton as a flash of inspiration while he was sitting in a plane on a runway, about to go on holiday – built on an earlier idea, and might now sound familiar. “It was similar to that natural solution, where all the bones are individual pieces, and they’re held aloft and held together with thin steel, we call them tendons.”
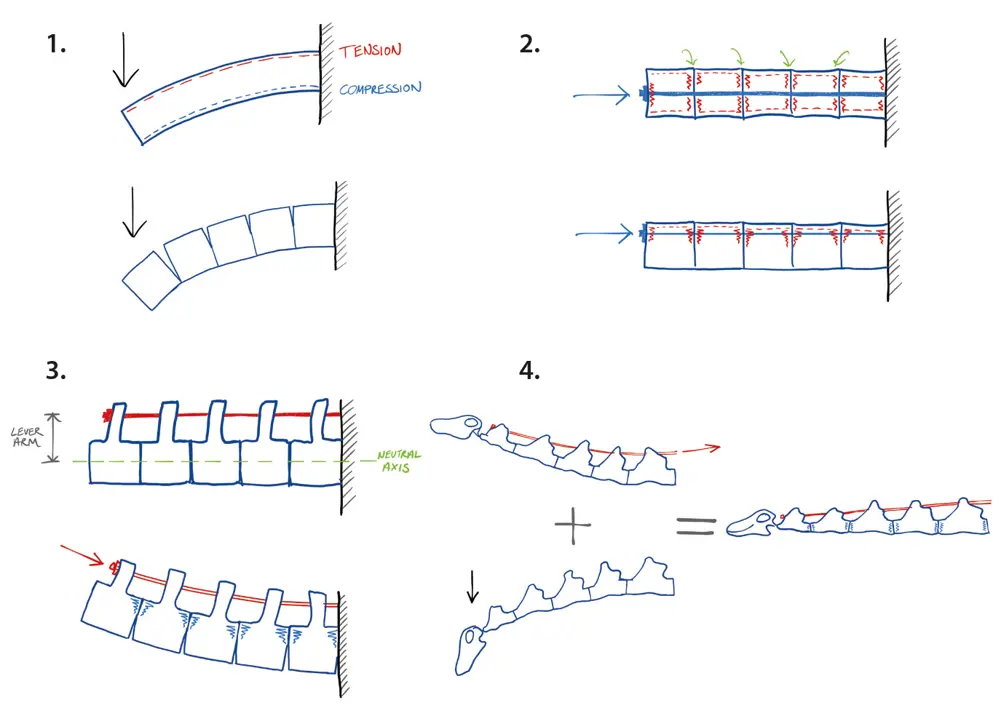
1. A continuous beam will go into tension and compression when it bends. A ‘beam’ made of separate elements cannot form tension and will simply fall apart. 2. A bar or cable under tension will pull the separate pieces together, compressing them. It is more effective if the bar is in the area at the top, where tension forms. 3. Moving the bar even higher increases its effectiveness – like a lever. It bends the beam upwards. 4. This upwards bending can be calibrated to cancel out the downwards bending due to gravity. Stresses and deflections are reduced © Structure Workshop
There are two tendons running along the length of the spine, just like those ligaments in the living dinosaur. The lower tendon runs through the centre of the vertebrae, which joins them together, while the higher one provides structural support. The bones are threaded together “like beads on a string”. (see diagram)
The main and dominant forces Fern undergoes are – unsurprisingly – because of its weight. However, there was another factor to consider: people. “It’s outside in a public setting,” Clayton says. “If someone were ever to climb up the legs and hang on the tail, you wouldn’t want it to be a danger to the public and to collapse.”
The tendons were prestressed to prepare the entire structure for the stresses it could expect throughout its lifespan (bridges undergo a similar process to prepare them for loads). In Fern, prestressing meant tensioning – stretching – the tendons. As the tendon contracts again, it pushes the bones together, compressing the bronze, which closes up the gaps.
It’s about striking a balance and optimising the level of prestress: “What we want is for the compression from our prestress to overcome any tension that would naturally form in our structure from just the bending due to external forces like gravity,” Clayton explains.
The team used a computer method called finite element analysis to predict how the structure would behave under different stresses. It used computer models from the very start of the project to test ideas and work out what structural approaches to supporting the loads would work.
Making (pre)history
The Crystal Palace dinosaurs
Just eight miles southeast from the Natural History Museum in Crystal Palace Park stand what are thought to be the world’s first ever actual-size dinosaur replicas.
Although they’re now perhaps best known for their anatomical inaccuracies, the 30 dinosaur sculptures at Crystal Palace Park, which include a squat Iguanodon and a hunchbacked Megalosaurus, were – just like Fern – based on the best palaeontological understanding of the time.
Sculptor Benjamin Waterhouse Hawkins worked closely with palaeontologists – including Richard Owen (who coined the term ‘dinosaur’, and was the driving force behind the founding of what is now the Natural History Museum) – to create the dinosaurs. He was meticulous in his work, following the literature, examining the fossils himself, and consulting with the experts when any judgements had to be made, such as about the texture of their skin or how long their toenails should be.
The form of many of the dinosaurs was extrapolated from a few bones, with familiar reptiles filling in the knowledge gaps, and so as more dinosaur skeletons emerged from the ground around the world (and crucially, more near-complete ones), the creatures of Crystal Palace, which opened to a delighted audience in 1854, fell rapidly out of date.
Now Grade I listed, the Crystal Palace dinosaurs remain largely as they were in the 1850s (though they’ve had a few facelifts over the years). Recent funding from the National Lottery to the tune of nearly £5 million will go towards the ongoing preservation of this loved relic and vivid look at the dawn of an exciting new science.
Bone by bone
While it’s the steel tendons that hold the pieces together, the bronze bones – and especially the flat bearing faces between them – also play an important structural role. These bearings undergo huge compressive forces as the tendons squeeze them together, and must be able to take yet more stress given it takes pride of place in a public space. For this reason, the bones and their bearings had to meet exacting standards. “We had to make very, very complex moulds,” Lowe says, adding that many of the casts were made at Factum.
The vertebrae had to be made in two halves, and again the team took inspiration from dinosaur anatomy. Their bones were filled with air sacs – similar to birds today – with a thin scaffolding of internal struts to prevent the bone from collapsing inwards. Fern’s bronze vertebrae are hollow, with an 8-millimetre-thick wall and strengthening fins within. “We had to bring in the internal ribbing so that they could take the compressive strength,” Lowe explains.
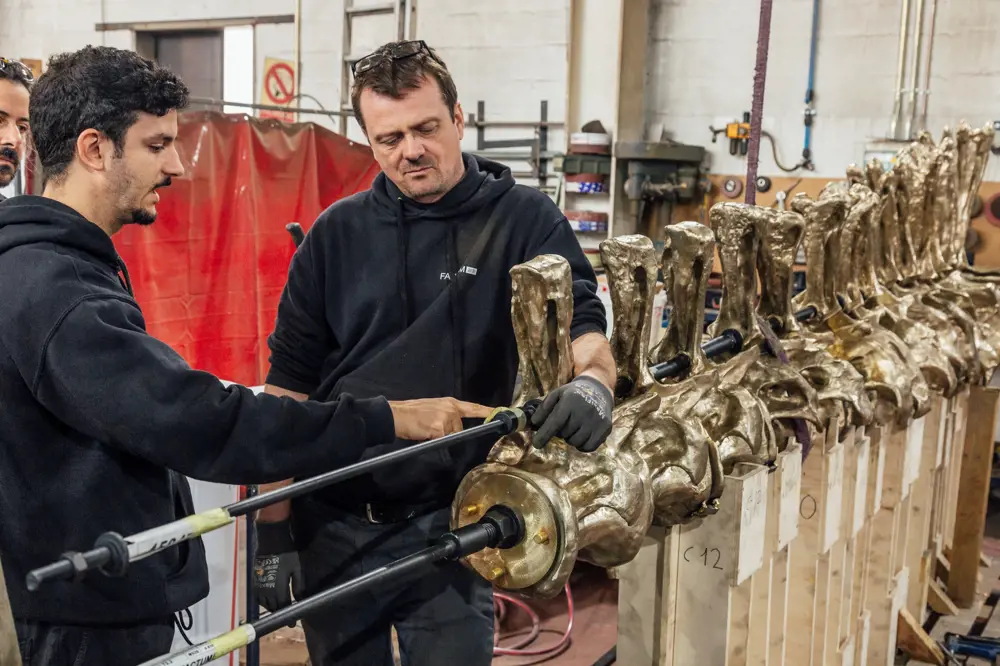
The team at Factum Arte check the vertebrae © Oak Taylor-Smith | Factum Arte
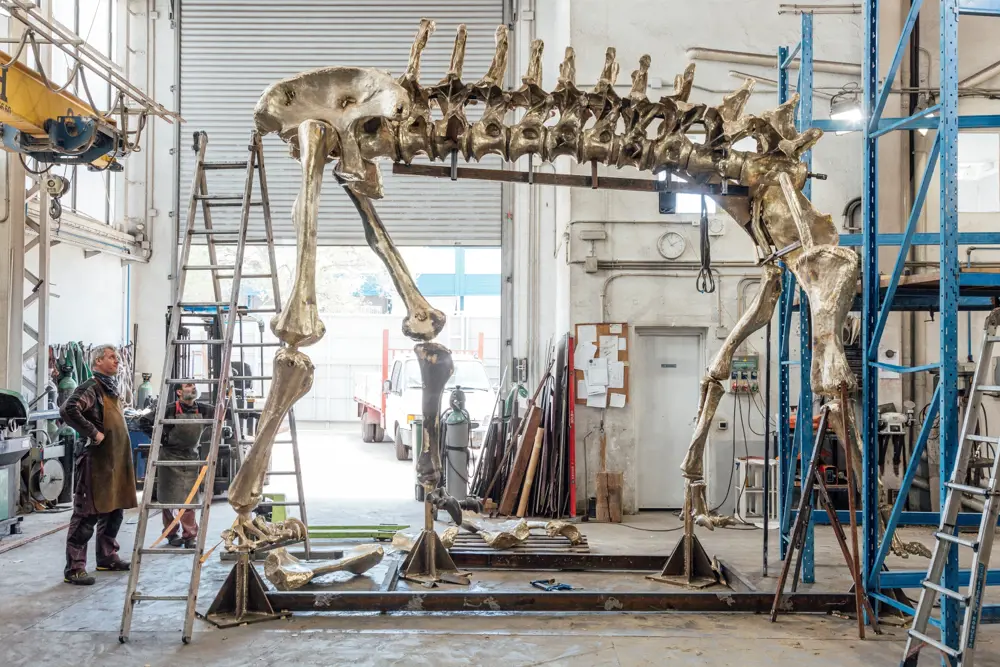
The dinosaur comes together in Madrid © Oak Taylor-Smith | Factum Arte
Successive castings, from the 3D prints on which the first moulds were based through to the ultimate bronze ‘bones’, introduced distortion. Therefore, before assembling the dinosaur Factum Arte had to compare the bronze casts to Structure Workshop’s virtual model and make final tweaks so that they would perform as expected.
Fern’s bones are cast in bronze, a material chosen for its durability, resistance to corrosion and the fact it’s very, very long-lasting. The tendons are solid, high-strength, stainless steel bars made by Sheffield-based company Macalloy. The bars curve slightly with the dinosaur’s spine, and step down in width from 20 millimetres at the base of the neck and tail, to 16 millimetres, and finally to 12 millimetres – about the width of a little finger – at the head and whip of the tail.
“The only thing that would be strong enough to hold all those forces from the great weight of the bronze neck and tail would be a really, really high spec stainless steel… that’s why we had to get specialists to make those elements,” Clayton says. “They are the key to the entire structure.”
It took about three months to assemble Fern in the Fademesa foundry in Spain. “The assembly of the dinosaur was quite awe inspiring,” Lowe says. “You’ve got all these vast bits that are being fitted together, but with incredible tolerance, very low levels of tolerance.” The pieces were tightened in place using a hydraulic jack.
After three years of collaborative effort, Fern stood for the first time. Following some final tests, and inspections by Keith Jennings, the museum’s Director of Estates, Projects and Masterplanning, and Eleanor Cornforth, a project manager involved in the gardens’ transformation and Fern, it was time to pack for London.
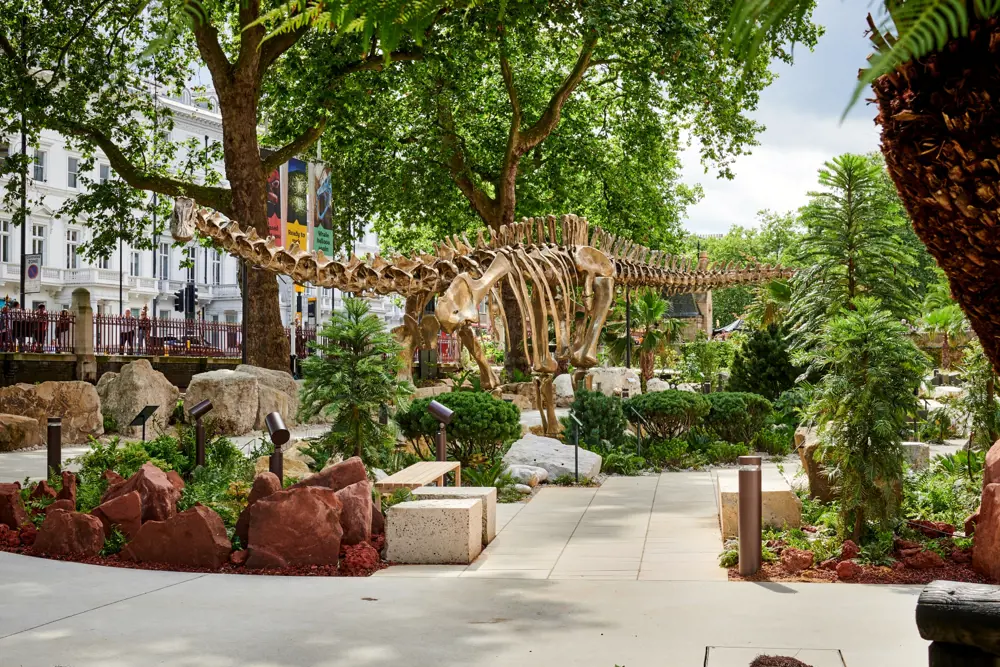
Fern’s skeleton is made of individual casts of the 292 bones that comprise Dippy, a plaster cast of several dinosaur fossils unearthed in the late 19th century © The Trustees of the Natural History Museum
Fern meets the world
One night in 2024, art handlers Mtec Fine Art installed Fern in its new home at the front of the Natural History Museum. “Fern is a masterpiece of engineering, and a true testament to the expert collaboration between the Natural History Museum, Factum Arte, Fademesa Foundry in Madrid, and Structure Workshop,” says Jennings. “Watching as Fern was put into place in the gardens and assembled in the dead of night – another technical feat of ingenuity – was an incredible scene to witness. For many, visiting Dippy in the Museum’s halls is a core memory. Now, Fern is a permanent homage that takes pride of place in our gardens, inspiring visitors to think about the world around us and its history before they even enter the galleries awaiting them inside.”
In July 2024, Fern was presented to the public for the first time and finally received its name. Its dynamic pose, courtesy of the graceful curves of the neck, back and tail, the invisible supports, as well as its garden setting, give the overall impression – 150 million years after its heyday – of a creature that lived.
The bronze of its bones has been left untreated, allowing the now burnished vertebrae to mature and darken with time. “It’s picking up its own character within the garden,” says Lowe. And Fern is expected to stand in the museum’s gardens for about 100 years.
Like Dippy before it, Fern could inspire generations to come. “I love the idea that something like 100 million children are going to pass by that dinosaur in the next decade,” Lowe says. “Even if we get just 1% being awe-struck and awe-inspired, it would be a very meaningful project.”
Clayton recalls the impression Dippy had on him as a child: “I used to go to the museum all the time as a child, and I remember being so inspired by Dippy,” he says. “To be working on this is a real dream come true.”
Contributors
Adam Lowe was trained in Fine Art at the Ruskin School of Drawing in Oxford and the Royal College of Art in London. He has been an adjunct professor of the MS in Historic Preservation at Columbia University, New York, since 2016. In 2019, Lowe became a Royal Designer for Industry, awarded by the Royal Society of Arts. He has written extensively about originality, authenticity, and preservation.
Max Clayton leads his own design team within Structure Workshop, with a focus on technical innovation, geometry and low-carbon design. In 2024 he won the Nethercot Prize for his paper on the engineering behind Fern, and his recent retrofit project, Yorkton Workshops, won Architects’ Journal’s Retrofit of the Year Award 2021.
Keep up-to-date with Ingenia for free
SubscribeRelated content
Design & manufacturing

Super cool(er)
Welsh startup Sure Chill has developed a cooler that uses the properties of water to keep its contents cool for around 10 days without electricity. This is ideal for storing items such as vaccines where electricity sources are unreliable.

R&D investment makes good business sense
In just five years, Dr Ralf Speth FREng has presided over a revolution in design and manufacturing that has helped create a new family of engines and has overhauled Jaguar Land Rover (JLR) production facilities.

Steel can arise from the ashes of coal
Thousands of people were laid off in the UK steel industry in 2015 and there are pessimistic future forecasts. Professor Sridhar Seetharaman of the Warwick Manufacturing Group argues that smaller, flexible steel mills implementing new technology would better cope with fluctuating global trends.

Integrating metrology in business and academe
Professor Jane Jiang’s interest in measuring began when she worked on a bus production line in China. She found that the best way to improve quality, consistency and productivity was through metrology, the science of measurement. Today, she runs the UK’s largest metrology research group.
Other content from Ingenia
Quick read
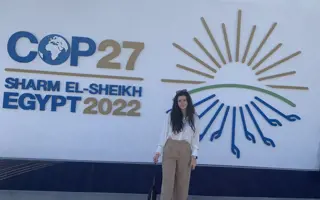
- Environment & sustainability
- Opinion
A young engineer’s perspective on the good, the bad and the ugly of COP27
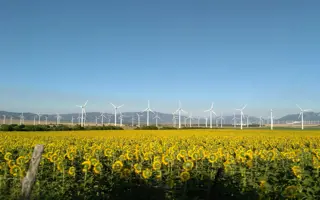
- Environment & sustainability
- Issue 95
How do we pay for net zero technologies?
Quick read
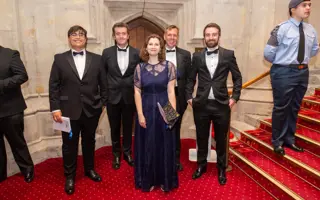
- Transport
- Mechanical
- How I got here
Electrifying trains and STEMAZING outreach
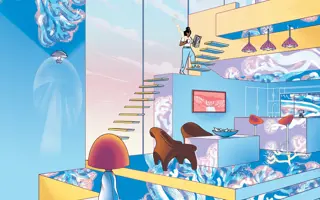
- Civil & structural
- Environment & sustainability
- Issue 95