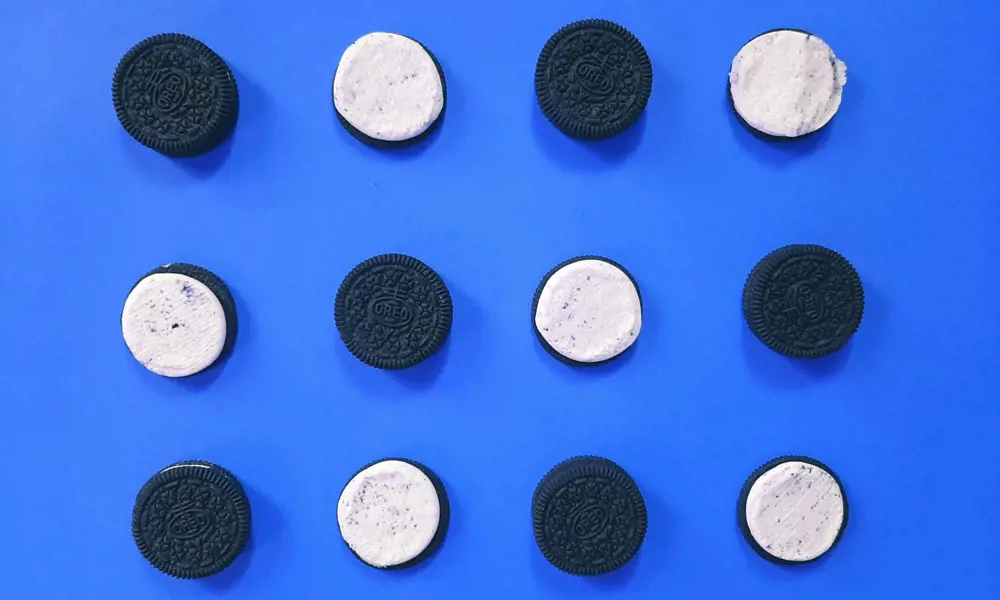
Better batteries, crunchier biscuits: prize-winning startup Polaron solves material problems
When Dr Isaac Squires, Dr Steve Kench and Dr Sam Cooper set out to develop AI tools for making better batteries, they probably didn’t expect that the same tools might one day help fine-tune the texture of Oreos.
It turns out for battery performance, and the crunch of the iconic sandwich biscuit, the devil is in the detail. If you looked at a battery under a powerful microscope, you’d see a complex landscape of particles and pores. The way these grains are organised directly impacts how much energy they store, how fast we can charge them, and how quickly they degrade.
Now at startup Polaron, the team has developed AI models with which battery designers can explore thousands of material designs in a day. By analysing and optimising the microscale structure of electrodes and other components, Polaron’s AI is helping manufacturers build batteries that last longer, charge faster and degrade more slowly.

Left to right: Steve Kench, Isaac Squires and Sam Cooper © Polaron
In March this year, Polaron won the first ever Manchester Prize for its technology. Led by the Department for Science, Innovation and Technology and Challenge Works, the prize rewards British-led AI breakthroughs for public good. Indeed, batteries (and biscuits) aside, Polaron’s technology could help develop improved pill coatings for drug delivery, bone implants, alloys for jet engines and composites for wind turbines.
Taking generative AI to battery materials
In 2021, Squires and Kench were PhD students in Sam Cooper’s lab at Imperial College’s Dyson School of Design Engineering. As Squires explains, the research group spied an opportunity for the generative AI tools starting to emerge from big tech companies. Instead of “auto-completing emails and generating pictures of unicorns on the Moon”, they figured these tools might be able to help solve the problems with battery materials.
After three years working on research, they realised that the AI models they were developing could address “not just an interesting scientific problem, but an industrially relevant engineering and manufacturing problem,” says Squires. This led them to form Polaron.
The research group spied an opportunity for the generative AI tools starting to emerge from big tech companies. Instead of “auto-completing emails and generating pictures of unicorns on the Moon”, they figured these tools might be able to help solve the problems with battery materials.
Most lithium-ion batteries are made of a solid, sponge-like material, immersed in a liquid electrolyte. When the battery discharges, lithium ions work their way through tiny pores from the anode to the cathode, delivering energy. When it charges, the ions flow back to the anode, storing energy.
If the structure is dense, with fewer pores, it’s more difficult for the ions to flow across it, making fast charging more difficult. The flipside to this is a higher energy density – meaning it can store more energy overall. Bigger pores allow the ions to flow through more easily, but at the cost of lower energy density.
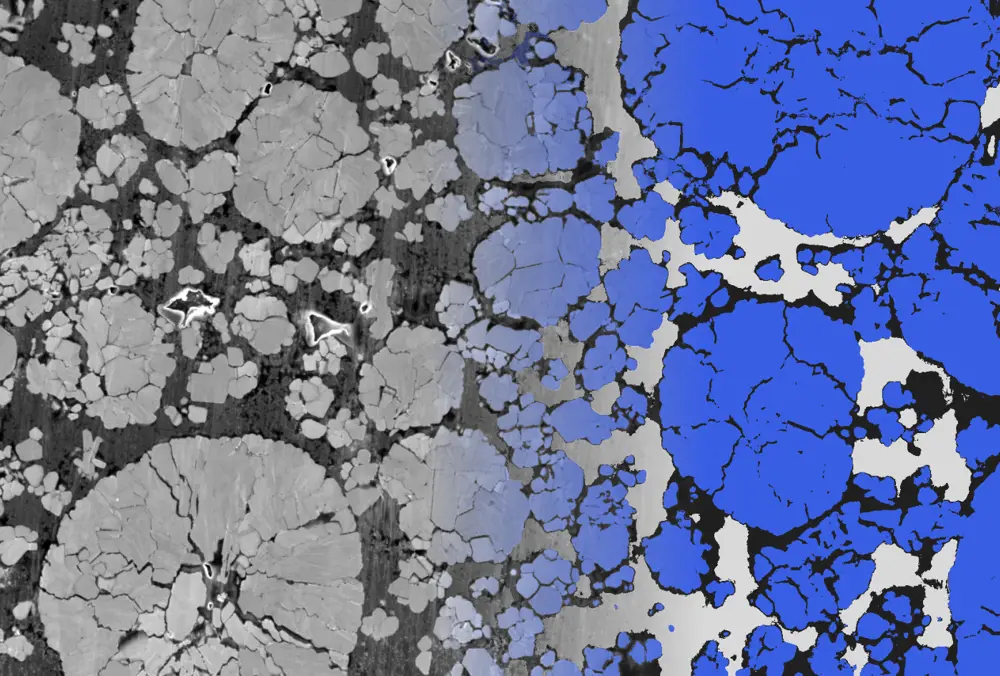
Microscope image of a nickel-cobalt-manganese oxide battery electrode © NREL, adapted by Polaron.
Sometimes trade-offs are acceptable. Take a power tool: you need it to operate at a high power, so the energy comes out very quickly. You probably don’t care as much about needing to store a lot of energy because they tend to be easy to charge. But mostly, battery makers are aiming for the best of both worlds. “We want as much energy as we can and to charge as quickly as we can,” says Squires.
To get there, manufacturers tweak battery design at multiple levels, including the pack, the module, and the material microstructure. The last part is where Polaron comes in. “Doing that design is really hard and really slow at the moment,” says Squires. Polaron aims to cut down “years and years of trial and error” to days.
Ready for the closeup
Simply put, making battery electrodes involves mixing lithium-containing powders into a porridge-like consistency. This concoction is coated onto a metal foil, dried, crushed, rolled up and put into a can. Each of these different steps affects how the battery looks under a microscope.
Polaron’s generative AI model analyses microscope images, learning features associated with particular behaviours and properties. This can be extended to learn the relationship between the structure, and the process – how the battery was made - enabling engineers to rapidly identify manufacturing parameters that will produce the optimum electrode material.
While it’s a form of generative AI, it’s a very different type of model from the latest ChatGPT, explains Squires. To spit out semi-recognisable Studio Ghibli-style images of everyone and their favourite memes, the model doesn’t have to be that accurate, but has to be very multi-purpose. More rigour is needed for AI to work for materials science. Errors need to be incredibly small for Polaron’s technique to be meaningful – especially in manufacturing processes. “If you don’t get it exactly right, it’s pointless,” says Squires.
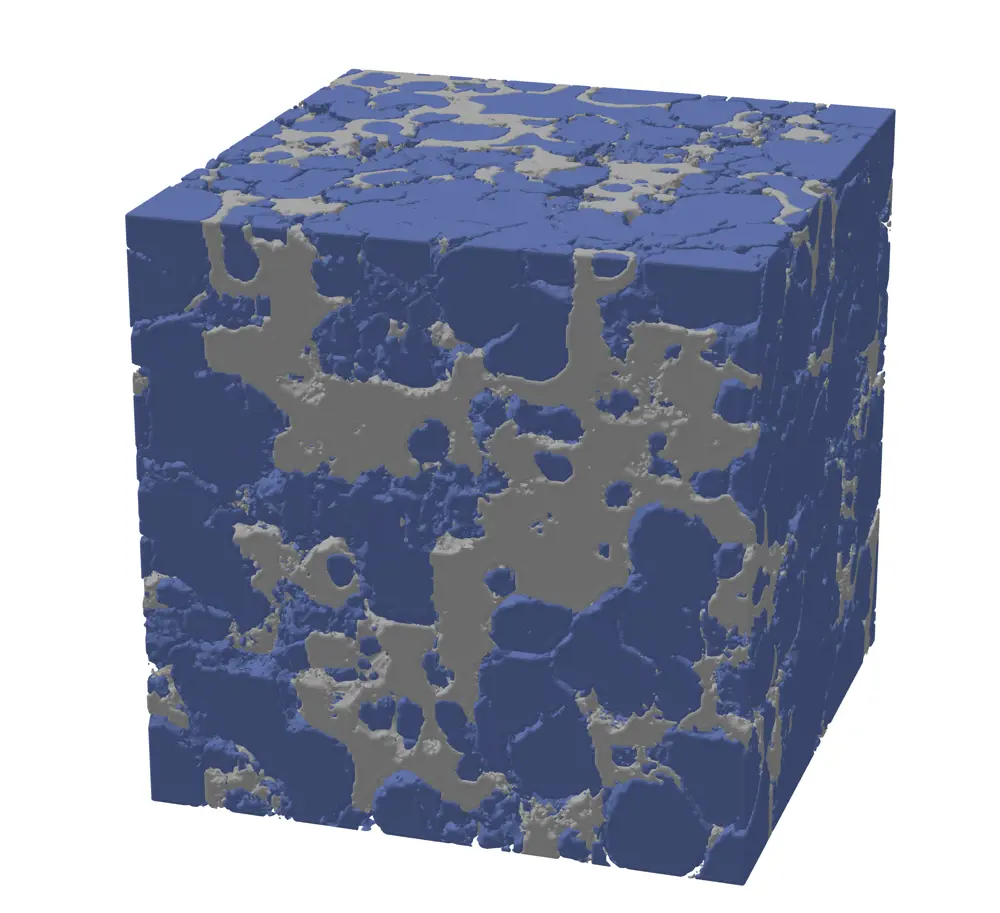
A cathode model in 3D © NREL, adapted by Polaron.
This is because the relationship between the way that we make materials and how they behave is “very specialised and very localised,” Squires explains. “If you have a factory in Atlanta, making a specific material, and you have the same factory – carbon copy – and you put it in Slovakia, you'll need to adapt the process.”
This means models have to be more specialised. Instead of learning from vast swathes of the internet, Polaron’s model is trained specially for each customer, on small sets of their own microscope images.
To get these images, the customer slices into their electrode material with a beam of ions, to create a super-flat surface. But because battery processes happen in 3D, one of the really innovative things about Polaron’s technology is a step that takes that 2D image and constructs a 3D model. From there, the AI can generate new material designs in seconds – allowing battery engineers to explore thousands of different variations in a day.
And it works: Polaron’s research shows its model can boost battery energy density by more than 10%. Unsurprisingly, the company has had a lot of interest from battery companies.
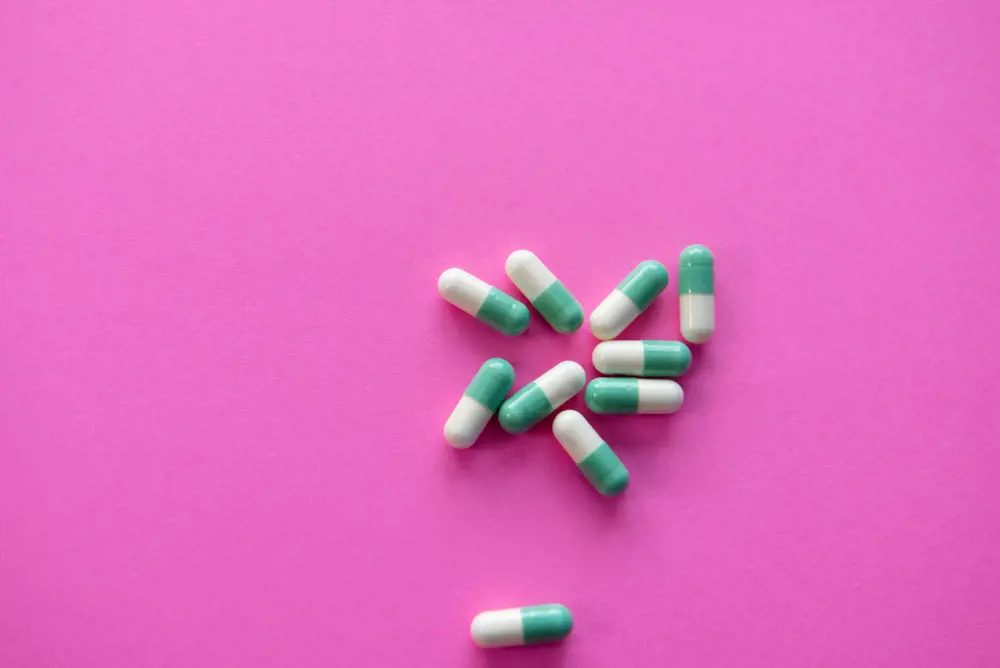
For pharmaceuticals, Polaron's technology could affect drug delivery as the microstructure of pill coatings directly affects how the active compound is released © Unsplash / Christina Victoria Craft
It’s gone further than the team expected. “People are using it for things we’d never even thought of,” says Squires. Beyond batteries, the technology is being applied to fuel cell materials, alloys for bone implants and jet engine turbine blades, and composites for wind energy.
One of the more unexpected requests is coming from the pharmaceutical industry. Most pills are coated, to mask a drug’s unpleasant taste, control release, or protect it. The microstructure of the coating affects the way it dissolves and how medicine is delivered. Then of course, there’s Oreos. “I’ve been on the phone with an Oreos manufacturer before, and they say that the porous microstructure of Oreos affects the texture,” says Squires.
With the Manchester Prize under their belts and interest from all sides, the next priority is to scale up and get hiring. “We want to build on this early momentum in the battery materials space,” says Squires. And who knows, maybe an even crunchier Oreo is on the cards.
***
More in AI:
🎨 Can AI boost human creativity?
❄️ AI shakes up the world of weather forecasting at Google DeepMind
❌ The PhD student fighting AI harms and deepfakes
Contributors
Florence Downs
Author
Keep up-to-date with Ingenia for free
SubscribeRelated content
Environment & sustainability
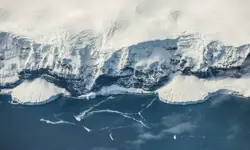
The extreme engineering behind life on an Antarctic station
Antarctica is one of the most challenging environments on the planet, but of enormous scientific importance to humanity. Technology and engineering is essential to enable the British Antarctic Survey's researchers to pursue their science effectively in this awe-inspiring landscape.

Recycling household waste
The percentage of waste recycled in the UK has risen rapidly over the past 20 years, thanks to breakthroughs in the way waste is processed. Find out about what happens to household waste and recent technological developments in the UK.

Upgrade existing buildings to reduce emissions
Much of the UK’s existing buildings predate modern energy standards. Patrick Bellew of Atelier Ten, a company that pioneered environmental innovations, suggests that a National Infrastructure Project is needed to tackle waste and inefficiency.

An appetite for oil
The Gobbler boat’s compact and lightweight dimensions coupled with complex oil-skimming technology provide a safer and more effective way of containing and cleaning up oil spills, both in harbour and at sea.
Other content from Ingenia
Quick read
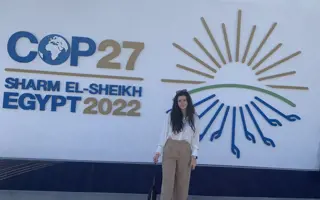
- Environment & sustainability
- Opinion
A young engineer’s perspective on the good, the bad and the ugly of COP27
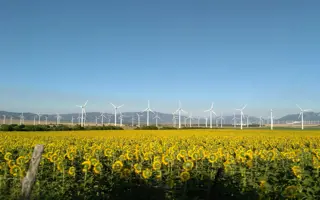
- Environment & sustainability
- Issue 95
How do we pay for net zero technologies?
Quick read
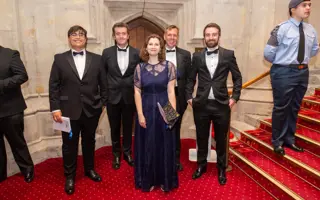
- Transport
- Mechanical
- How I got here
Electrifying trains and STEMAZING outreach
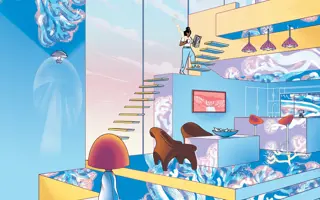
- Civil & structural
- Environment & sustainability
- Issue 95