Applied origami
With mathematical modelling and new software based on the properties of folded paper, origami is finding applications in surface design, collapsible and deployable structures, robotics and medicine. Manisha Lalloo looks at how engineers have discovered new uses for the Japanese art of folding paper.

Shannon Zirbel, a PhD student in mechanical engineering at Brigham Young University, Utah, unfolds a solar panel array prototype that was designed using the principles of origami. She worked on this project with Brian Trease at NASA’s Jet Propulsion Laboratory, Pasadena. See opposite for the folded version of thestructure © Mark Philbrick/BYU Photo
Origami, from ‘oru’, meaning ‘fold’ and ‘kami’, meaning `paper’, is an ancient Japanese art form that can be traced back to the 17th century. Usually bringing to mind images of paper cranes, at first glance the discipline seems to hold little or no link to that of engineering. However, there is a rich tradition of engineers translating the concepts of paper folding to their work.
EARLY APPLICATIONS
Origami provides an elegant mechanism to package large objects into smaller spaces, an application that engineers have taken advantage of, especially in space. In missions to outer space, large objects need to be transported in narrow rockets before being unfolded to their full dimensions while in orbit.
The first origami to be activated in this way was for a solar array in a Japanese research vessel launched in 1995. The solar array was folded using a pattern developed by and named after structural engineer Koryo Miura, a professor at Tokyo University, which packaged it as a compact parallelogram for its flight into space. Miura-ori is an example of rigid origami, where a material only bends at pre-specified fold lines, for example, a metal sheet connected by a series of hinges – see MIURA-ORI
Miura-ori is a widely used fold to pack flat sheets into a smaller space. Formed of a grid of packed parallelograms, Miura-ori is an example of an origami tessellation as well as being a form of rigid origami, as each parallelogram remains flat upon folding and unfolding. Originally developed for use in solar arrays, Miura-ori has since found a variety of everyday uses, such as map folding, and its final compact shape is limited only by the thickness of the sheet material.
Miura-ori has also found useful application for engineers looking to creating new mechanical metamaterials with unusual properties. The Poisson’s ratio of a material describes the ratio of the relative contraction strain normal to the applied load to the relative extension strain in the direction of the applied load. Most materials, for example, an elastic band, when stretched in one direction will compress in the other two directions perpendicular to the direction of expansion. However, a material with a negative Poisson’s ratio becomes larger in the other two dimensions when stretched. The Miura-ori fold is a simple example of this, demonstrating a positive Poisson’s ratio in one pair of directions but a negative Poisson’s ratio in a second pair.
Researchers have also discovered that adding defects to a Miura-ori sheet can increase stiffness of the material. So-called pop-through defects can be introduced by inverting the folds around a single parallelogram, conferring stiffness to the structure. Adding more defects can increase this effect further, giving a degree of tuneability to the overall stiffness of the material. As the defects are a stable alternative state for the structure, in principle, engineers could switch between structural forms upon activation by an external force, creating a material that could be stiff or flexible depending on conditions.

Miura-ori folded

Miura-ori pop

Miura-ori squeezed
-
Download a printable Miura-ori fold pattern
(270KB)
In 1990, Professor Sergio Pellegrino FREng founded the Deployable Structures Laboratory at The University of Cambridge to develop new, generic solutions and better understand the behaviour of existing deployable structures. Among its work was a deployable antenna, developed with engineer Dr Simon Guest, which achieved folding of a curved rigid surface. The antenna – called the Solid Surface Deployable Antenna – was split into wings with each wing subdivided into panels, which are connected by revolute joints. A wrapping fold pattern then wrapped the wings around a central hub.
Origami is also being used to fold other devices such as telescopes and booms. This summer, NASA’s Jet Propulsion Laboratory reported on a new project in collaboration with researchers from Brigham Young University and origami expert and physicist Robert J Lang to develop a solar sail that can fold up as small as nearly nine feet in diameter from an unfolded diameter of 82 feet.
APPLYING ORIGAMI
In the 1980s and 1990s, patterns from the world of origami started to be used in formal engineering contexts. However, while not specifically referred to as origami, the application of folding in engineering began much earlier. For example, in the 1950s, an origami pattern, later named the Yoshimura buckling pattern after the scientist that identified it, was discovered in cylindrical tubes as they buckled.
The recent rise in engineering-origami applications is largely a result of the application of mathematics to the craft. Although popularly seen as a creative art form, at the heart of origami is a set of mathematical rules that can be used to describe desired shapes and forms – FOUR LAWS OF FLAT-FOLDING
Mathematically modelling an origami shape becomes progressively harder the more complex that shape becomes. An example of a simple model would be flat-folded origami, where the final folded object is essentially still two-dimensional. At this stage of complexity, the crease pattern for a folded object must satisfy the following four laws illustrated here for the design New Flapping Bird, by Samuel L. Randlett:




1 A crease pattern can be coloured with only two colours without ever having the same colour meeting along an edge.
2 At any interior vertex the number of mountain folds (folds coming out of the plane) minus the number of valley folds (folds going into the plane) always differs by two.
3 Alternate angles around any interior vertex sum to a straight line.
4 No matter how you stack folds and sheets, a sheet can never penetrate a fold; a fold can also never penetrate a fold.
In the 1990s, Dr Robert J Lang, a physicist and early pioneer of applying engineering principles to origami, developed a computational program that could design origami bases for flat-folded structures. The resulting program, called TreeMaker, was one of the earliest crease pattern generators and could be used to create a variety of flat-folded objects which could subsequently be shaped into fuller 3D shapes.
As engineers better understand the laws that govern origami, they are better able to predict and design desired folded shapes and structures.
Engineers have used these mathematical rules to develop a number of computer programs to simulate complex folding patterns. Each computational program focuses on a different problem – some solve problems for flat-folded structures, while others look at 3D or curved structures.
One application where origami modelling is making a real difference is in car airbags. When designing airbags, engineers use a mixture of simulation and experiment to save on the number of real life crash tests that need to be carried out. To simulate airbag deployment, engineers use finite element analysis— dividing the surface of the airbag into hundreds of small triangular sections, and then calculating their position and orientation as the airbag inflates. Finite element analysis requires complex modelling, taking into account material properties of the airbag and the thermodynamics of the system.
However, before such deployment simulations can be run, the airbag’s folded-up starting point must be known, and optimised. Given that a folded-up airbag is essentially a flat-folded structure, origami algorithms have been applied to determine the airbag’s starting state. German company EASi Engineering, which develops airbags for Mercedes-Benz, uses software based on one of Dr Lang’s algorithms to determine the creases that are needed to transform one flat-folded shape into another.
Given that 25% of all metal production is sheet metal, origami folding provides a potentially very efficient form of manufacture for the future – see ROBOFOLD

RoboFold worked with Zaha Hadid architects to create a sculpture for the 2012 Venice Architecture Biennale. Called Arum, the sculpture is made fromsheets of bent aluminium. Photo: Iwan Baan
A company pioneering metal folding is RoboFold, a UK start-up based in London. Founded by designer Gregory Epps, the company specialises in folding sheets of metal into desired structures using industrial robots usually seen on car manufacturing lines. The company has developed a suite of software that can transform the practice of folding paper by hand into an industrial process of folding metal with robots.
RoboFold works mainly in the architecture and design space, manufacturing one-off aluminum pieces that are used in structures such as furniture and facades. In 2012, the company worked with Zaha Hadid Architects to create a sculpture for the Venice Architecture Biennale.
For each piece, the design is initially scoped out in practice with paper before moving onto computer simulations using bespoke plug-ins running on the popular Rhino and Grasshopper CAD platforms. A flat cutting pattern is created, which is scored and cut onto a metal sheet by a CNC router before the structure is folded into shape by robots programmed to carry out that particular process.
Manufacturing by folding relies heavily on software, rather than hardware, to create folding patterns and animations. Therefore the speed of manufacture is comparable to mass production, but also has the benefit of being able to update designs, or make one-off pieces quickly and cheaply simply by changing the underlying software code.
However, creating structures with the technique of curved folding requires a different manufacturing mindset– manufacturers are used to designing with the limitations of tooling rather than folding, and certain geometries are simply not possible using a folding process. Robofold, for example, takes this into account by manufacturing directly from design data.
The Institute of Aircraft Design in Stuttgart, Germany is at the forefront of origami manufacturing. They have created a machine that can produce accurate, precise origami structures. The origami cores can be manufactured from a variety of different materials and are intended to be used in aerospace applications, where lightweight structures are essential.
SELF-FOLDING
Self-folding is an active field of research with engineers employing a number of strategies to activate folding in materials. By using self-folding materials, engineers can eliminate the need for external actuation – by either humans or robots. Self-folding opens the possibility of creating complicated folding patterns with tens or hundreds of folds that can be initiated at the same time as well as applied to structures at a very small scale.

Researchers at MIT and Harvard have developed a self-folding robot that can self-fold and crawl away on the addition of a battery. The research demonstrates the expanding area of self-folding that can be used to create devices which are too complicated or too small to fold manually – see www.youtube.com/watch?v=Z-zule67nL8 © Harvard’s Wyss Institute
Fold lines can easily be printed onto sheet material, using inexpensive and commercial techniques such as screen or inkjet printing to change its properties and induce folding. For example, researchers at North Carolina State University have printed black ink onto sheets of optically transparent, pre-strained polystyrene to create a crease pattern that could be activated by light. When heated by a source such as an infrared lamp, the black ink causes printed regions to absorb more energy, heating the underlying polymer to temperatures above its glass transition temperature. These printed ‘fold lines’ are then relaxed and shrunk, acting as hinges to fold the sheet into a three-dimensional shape. By varying the width of the lines, engineers could change the final angle of the hinge, allowing the creation of a variety of objects, such as cubes or pyramids, without ever having to physically touch the material.
Taking this idea a step further is a group at Harvard and MIT who have created an origami robot that can self-fold and crawl away with the addition of a battery. This work took advantage of the properties of shape memory alloys to form a composite polystyrene and paper base sheet onto which engineers attached two motors, two batteries and a microcontroller, as well as predetermined hinges.
After a timed delay of 10 seconds, electrical currents heat the shape memory alloy layer, causing it to fold into a 3D structure in four minutes. When cooled, the shape memory alloy stiffens, locking the fully assembled robot structure in place, and the microcontroller signals the robot to crawl away at a speed of about 160 m per hour. This technique could be used to create devices that can self-deploy in extreme environments such as space, or be adapted to initiate from differed triggers such as heat or pressure from the surrounding environment.
LIMITATIONS
Many origami designs begin with crease patterns on a sheet of paper – a blueprint for the design, printed as a series of lines on a flat sheet indicating where folds need to be made. By drawing on origami’s underlying mathematical laws, engineers can create crease patterns on demand. However, the mathematical models available to describe structures are approximations of real life, and engineers need to be aware of the limits and assumptions built into such models.
One such assumption is the use of zero-thickness material – the idea that the material to be folded is so thin that its thickness can be ignored. While this works well for paper or even very thin plastic or metal, in mechanical structures such as solar arrays, the significant thickness of the panels needs to be taken into account in the engineering model. A second assumption gives rise to the ability of the paper (or folding material) to be able to intersect itself – a situation that could not happen in real life without performing a cut on the sheet.
Such assumptions are necessary to simplify origami problems into ones that can be easily solved mathematically. Research carried out in the 1990s showed that, in some cases, introducing a requirement to avoid self-intersection results in a problem belonging to class NP-hard, the hardest type of problem to solve in computational complexity theory. As such, this has given rise to a rich area of research for engineers, who are trying to describe the laws that can model such situations, including how to account for curved folds or plastic deformation.
CONTINUING RESEARCH
Today the research into origami applications in engineering has become widespread with engineers researching ways to use origami to give materials additional properties, such as high-energy absorption or added stiffness.

By introducing pre-folds, engineers can guide structures towards highly energy-absorbing modes, such as in this laboratory model of a crash box for use behind the front bumper of a car. On failure, the crash box crumples, transmitting little energy to the remainder of the car. This reduces impact to the vehicle’s body – and its contents – in the event of a collision © University of Oxford
Honeycomb structures are widely used in aerospace and aeronautic applications, such as in aircraft wings. Origami offers engineers an alternative lightweight structure, with a variety of patterns to choose from with plenty of design parameters that can be tailored to provide desired behaviours.
Replacing honeycombs with origami could be used to design better, more impact-absorbing crash boxes. Crash boxes, found behind the front bumper of a car, minimise the impact to a car’s body in the event of a crash. Origami can be used to create highly energy-absorbing structures, by using pre-creases to guide structures to certain failure modes.
In the early 2000s, researchers led by Professor Zhong You at the University of Oxford used origami to develop a new kind of aortic heart stent for treating aneurysms. Based on an origami water bomb, the stent could be made out of biocompatible material, folded down to a small diameter before being threaded into the target vessel and subsequently expanded to improve blood flow.
Engineers are also interested in the application of origami to change a material’s mechanical properties. Mechanical metamaterials are artificial structures whose mechanical properties are defined by their structure rather than their composition. By introducing fold patterns into materials, engineers have found a way to create tuneable materials with novel properties, such as enhanced stiffness or a negative Poisson’s ratio.
In 2012, the US National Science Foundation awarded a total of $26 million to 13 separate projects researching origami design to aid in the integration of self-assembling systems. The use of origami in engineering is a rich and burgeoning research area and work continues in fields as diverse as computational simulations, energy-absorbing structures, mechanical metamaterials, self-folding devices and the application of origami in manufacturing. With interest in the field increasing and the sheer number of origami patterns available to investigate, it is likely there are still many more applications of origami in engineering to come.
The author interviewed Dr Robert J Lang, physicist and early pioneer of applying origami to engineering; Professor Zhong You at the Department of Engineering Science, University of Oxford and Gregory Epps, founder of RoboFold, for this article.
Keep up-to-date with Ingenia for free
SubscribeOther content from Ingenia
Quick read
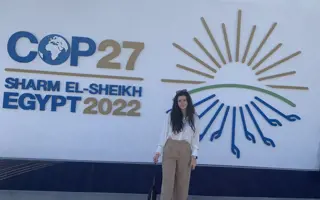
- Environment & sustainability
- Opinion
A young engineer’s perspective on the good, the bad and the ugly of COP27
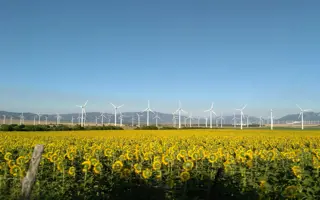
- Environment & sustainability
- Issue 95
How do we pay for net zero technologies?
Quick read
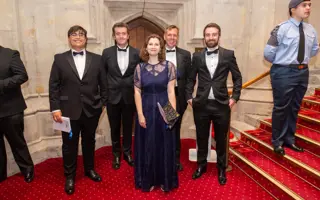
- Transport
- Mechanical
- How I got here
Electrifying trains and STEMAZING outreach
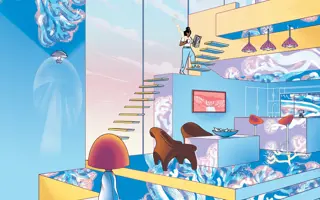
- Civil & structural
- Environment & sustainability
- Issue 95