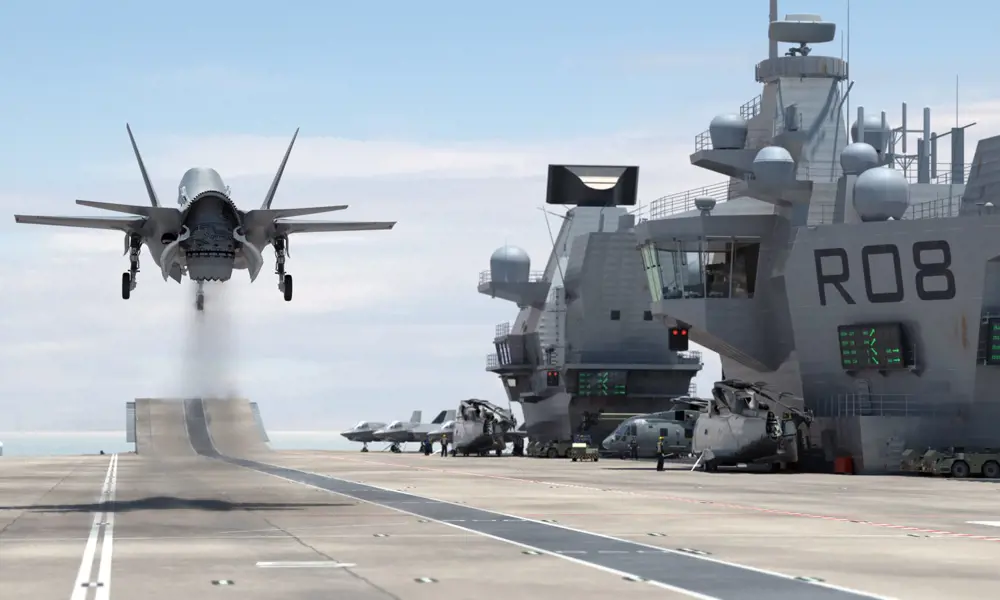
An innovative flight simulator for vertical landing
There is always great interest in the launch of new aircraft carriers, and the new Queen Elizabeth Class (QEC) vessels represent an unprecedented feat of engineering. As the largest Royal Navy warships ever constructed, each £3 billion aircraft carrier can accommodate up to 50 F-35B fighter jets, which are capable of performing vertical landings. Although the F-35B is manufactured by Lockheed Martin Aeronautics, BAE Systems assembles around 15% of every plane, from fuel systems to the rear fuselage.
BAE Systems is also one of three companies that was involved in the design and construction of each aircraft carrier, which gave it an insight into the challenges of operating aircraft from the vessels. For example, landing on a ship presents particular challenges in terms of airflow and deck motion, but the timescales for introducing the aircraft carriers into service meant that real-world testing opportunities would be limited. It was therefore necessary to create a simulator capable of accurately reflecting the complexities of a vertical landing on deck, in a variety of different weather conditions.
To achieve this objective, BAE Systems turned to a group of in-house engineers and programmers. This team needed to create a simulator that could accurately replicate the experience of landing an F-35B in fluctuating wind conditions. It did this by precisely modelling the vortices and turbulence generated as wind hits the 280-metre-long aircraft carrier and is forced upwards over the flight deck. With each F-35B worth $122 million, potential issues had to be resolved in laboratory conditions.
An evolving system
Dr Steve Hodge is the Senior Simulation Engineer at BAE Systems, with responsibility for developing the air-wake model used in the F-35/QEC simulator. His involvement with the simulator began in the early Noughties, when the UK government decided to proceed with the proposed Aircraft Carrier Alliance (the partnership between BAE Systems, Thales UK, Babcock and the Ministry of Defence that is delivering the aircraft carriers) to develop HMS Queen Elizabeth and HMS Prince of Wales. Since then, Dr Hodge’s team has consistently advanced the boundaries of computer modelling and simulation models, including a world first in air-wake modelling.
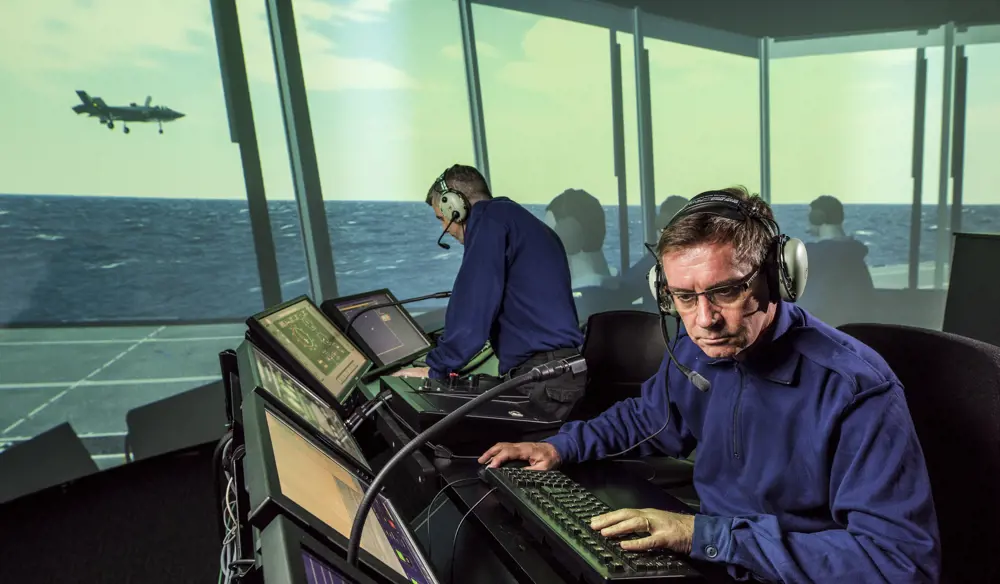
As well as allowing pilots to practise flying, the simulator includes a full representation of the ship’s flying control tower (FLYCO), where the landing signal officer onboard the carrier plays an important role in controlling aviation operations © BAE Systems
Dr Hodge explains that there are two parts to the F-35/QEC aircraft carrier integration simulator that his team has developed: “There’s the actual piloted simulator with a cockpit the pilot gets into, but there’s also the FLYCO [flying control tower] simulator. That’s on the aft island of the aircraft carrier, where the flying control team sits, including the landing signal officer. We realised as time went on the importance of integrating the landing signal officers and the FLYCO team into our simulations.” The simulator is now in its second iteration. Having started off with a hydraulic motion platform, it now has a fully representative cockpit with an electric motion system, high-resolution screens and a replica of the FLYCO environment next door, from where the landing signal officer can communicate with the pilot in real time.
According to Dr Hodge, the retrospective introduction of FLYCO is only one aspect of a gradually evolving brief: “We’ve worked throughout the whole QEC development cycle, so the focus of the simulator has changed. When I first got involved, it was more about helping to develop the visual landing aids and the flight deck markings on the carrier. Then we started putting more fidelity into the aircraft model, so we integrated a high-fidelity model of the F-35, which we developed with our partners at Lockheed. We integrated that with our models of the carrier and started to use it not only for the visual landing aids, but also for developing landing techniques such as the shipborne rolling vertical landing. We’ve evolved not just to cover the design of the ship but also the design of the aircraft.” This has included supporting preparations for first of class flight trials, which are due to commence later in the year. This simulator will allow flight test engineers to test in different conditions, so that they can make the most of the time they have during the real first of class flight trials onboard the ship.
Recreating air force
A hugely significant – and world-leading – advance was made in terms of integrating air-wake modelling into the F-35B flight simulator. “If you imagine the air flowing over the sea,” Dr Hodge explains, “it starts to create vortices and turbulence whenever it hits the ship. The angle the wind hits the ship at creates different patterns of airflow over the deck and around the ship. The pilot has to fly through the turbulent air wake behind the carrier in order to land on it, so it’s been really important to model that ship air wake in order to make the simulator as realistic as possible.” Sponsored PhD students at the University of Liverpool have been looking at advanced computational techniques to model the air wake, before integrating their findings into the simulation using high-performance computers: “The machine we use for that needs a lot of processors and memory to hold all the air-wake data, before mapping it onto a grid to apply it to the aircraft as it flies through the air wake. We’ve got a machine with one terabyte of data and 64 processors to model the air wake in real time.”
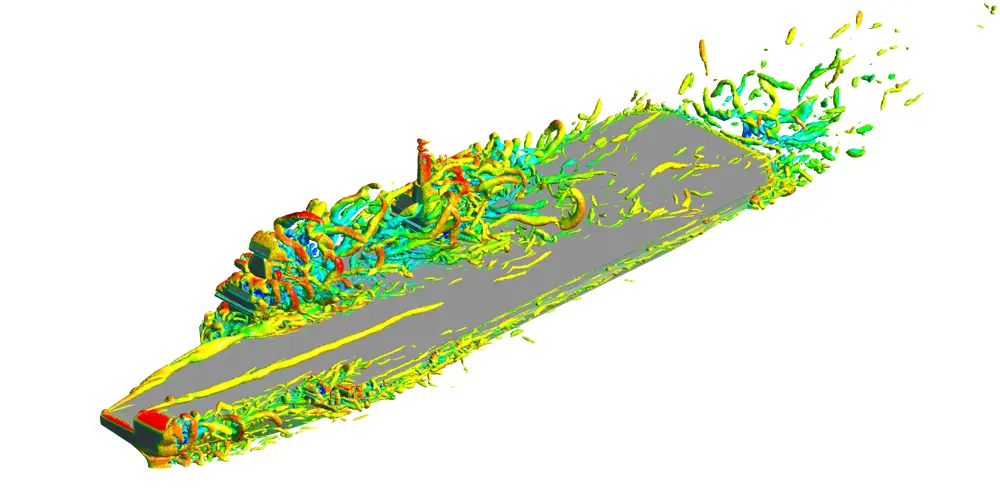
A visualisation of vortices being shed from the superstructure as wind flows around the aircraft carrier, modelled using computational fluid dynamics. This is an example of the air-wake models being integrated into the F-35/QEC integration simulator © University of Liverpool
This sort of processing has taken the team into unchartered territory, according to Dr Hodge. “Elements have been done in the US, but there hasn’t been a place where it’s been done on this scale – and there hasn’t been a situation where everything’s been brought together. You might have someone who’s done air-wake modelling, and there are plenty of aircraft flight simulators out there, but there’s no other simulator in the world where you can fly the F-35 to the aircraft carrier, stand inside the FLYCO simulator and see it land while interacting with the pilot. This is the only place where the air wake and ship motion are modelled and the simulator accurately reflects the aircraft handling qualities and the airflow around the ship. There’s nowhere else all these models have been put together and integrated into one place in such high fidelity.”
This is the only place where the air wake and ship motion are modelled and the simulator accurately reflects the aircraft handling qualities and the airflow around the ship
Wind breakers
The computational analysis required to accomplish this in an engineering simulator is also innovative. “We can basically scale up the wind models to represent different wind strengths,” Dr Hodge says, “but when it comes to different wind directions, you don’t have any choice but to compute the air wake. As the wind goes up in magnitude, the flow pattern doesn’t really change a great deal apart from the vectors getting scaled up slightly because of the wind speed. However, as you change the direction that the wind hits the island of the ship, then the patterns of flow over the deck change dramatically, so we needed to do the computations for each wind direction. We’ve got a database of wind directions going all round the ship. Each one takes about two or three weeks to process on a high-performance computing cluster, and then we extract the data in real time. The computation is quite an important process; it’s not just calculating one solution, but multiple time steps. We end up with 30 or 40 seconds of flow data we can replay in the simulator.”
To confirm the air-wake model was delivering accurate results, Dr Hodge and his team validated it in a water tunnel at the University of Liverpool using a 3D-printed 1:200 scale model of the aircraft carrier. The team used water instead of air to create a ‘wet’ wind tunnel, which allowed it to submerge the model of the carrier in a tank and then blow water over it. The team then used anemometers to measure the air speed over the ship at different points. This was still an aerodynamic test rather than a hydrodynamic one, substituting air for water, and comparing the results with anemometer surveys of the newly-constructed HMS Queen Elizabeth.
We’ve got a database of wind directions going all round the ship. Each one takes about two or three weeks to process on a high-performance computing cluster, and then we extract the data in real time
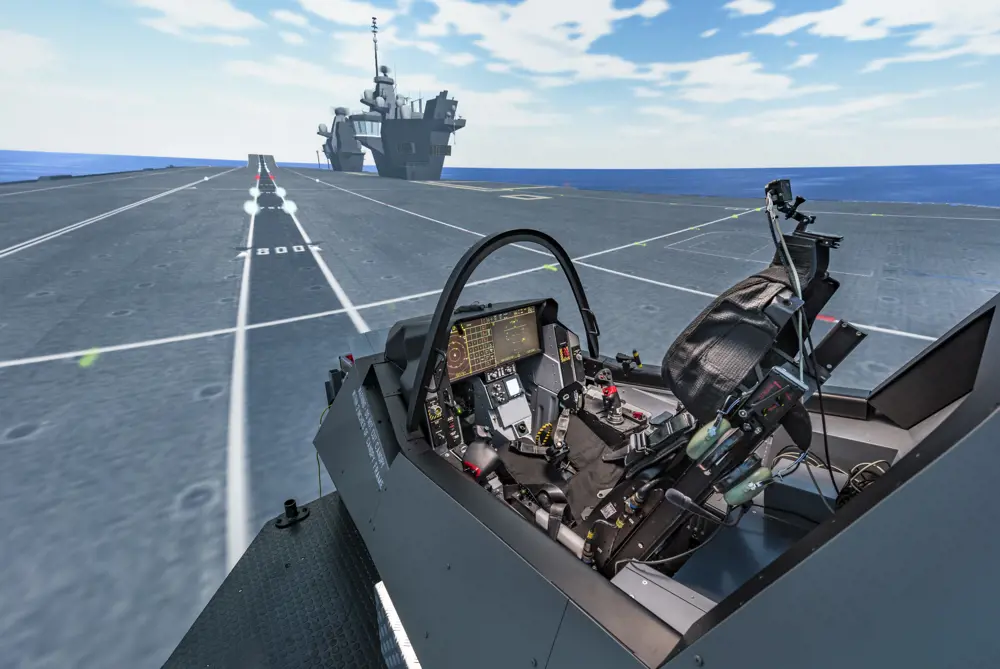
The fully immersive simulator has a cockpit moved by an electric motion platform. Highly specialised engineering data was fed into the simulator to replicate the disturbances that an aircraft would experience, meaning that when a pilot lands an F-35 in the simulator, they feel the motions that they would feel in real life © BAE Systems
The F-35 simulator includes a dome with 16 high-resolution projectors in the piloted simulator. It includes a faithful reproduction of an F-35 cockpit, mounted on a cutting-edge and highly responsive electric motion platform that is capable of moving in six axes. It also offers more sensory input and a greater sense of immersion than other simulators. From the simulator’s cockpit seat within the dome, pilots can feel the external forces of the air wake, while the projectors create a fully immersive wraparound view of the aircraft carrier and the sea surface.
So far, the simulator has been extensively used by the F-35 Integrated Test Force, which includes pilots from the RAF and Royal Navy, the US Navy and US Marines. These pilots are experienced in ship landings, but future F-35B pilots have also been practising the challenges of landing at sea. Feedback on the simulator has been extremely positive, according to Dr Hodge: “It’s fully immersive and the pilots are very complimentary. They say the motion and high wind conditions give them the sense of stress that other simulators don’t. Beyond that, the flight test team is taking notes on test landings, to help determine what to look for when real flight testing begins later this year.” That should enable them to optimise available time aboard the ship, focusing their attention on other elements of the F-35’s performance.
Such has been the complexity of Dr Hodge’s work that he has used it as the basis of a company-funded PhD. In 2010, his work on ship/air integration using simulation saw him graduate with a doctorate, reflecting the challenges of accurately modelling both the aircraft and its carrier. He concludes by acknowledging the remarkable advances in computing power that have made the current F-35/QEC simulator possible: “If someone had shown me this simulator when I first started modelling the aircraft carrier 18 years ago
I would have been astounded. It’s amazing what we can do now compared to what we could achieve in those days, and it’s just getting better all the time with computing power, digital projectors and other advances. It makes you wonder what we’ll be able to accomplish in 20 years’ time.”
Regardless of how technology evolves in the coming years, the research conducted for the aircraft carriers and F-35B will contribute to future knowledge of air-wake modelling, across other platforms and simulators.
***
This article has been adapted from "Flying without wings", which originally appeared in the print edition of Ingenia 76 (September 2018).
Contributors
Neil Cumins
Author
Dr Steve Hodge is Senior Simulation Engineer at BAE Systems. He has worked in the company’s simulation department for 20 years, having previously worked on the Hawk and Harrier fighter aircraft.
Keep up-to-date with Ingenia for free
SubscribeRelated content
Aerospace
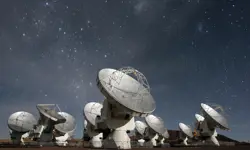
ALMA – the high altitude observatory
The Atacama Large Millimetre/submillimetre Array (ALMA) is the largest and most expensive ground-based telescope built, revolutionising our understanding of stars and planetary systems. Building it in the Atacama Desert in Chile required the ingenuity of hundreds of engineers.
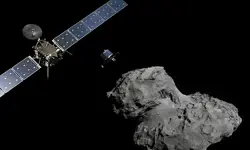
Communicating with outer space
The Royal Academy of Engineering awarded a team at BAE Systems the Major Project Award in June 2016 for their development of a powerful satellite modem system, pivotal in enabling the precise control of the pioneering Rosetta spacecraft and the first-ever soft landing of a spacecraft on a comet.
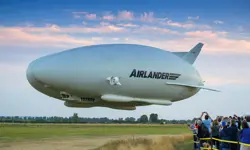
An aircraft like no other
The Airlander made headlines when it embarked on its first test flight in August 2016 as the world’s largest aircraft. Chris Daniels at Hybrid Air Vehicles Limited, and David Burns, Airlander’s Chief Test Pilot, talk about the engineering that helped it reach this stage and plans for the craft’s future.
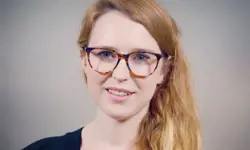
Q&A: Lucy Harden
Lucy Harden is a mechanical engineer on BAE Systems’ Digital Light Engine Head-Up Display development programme. She devises innovative solutions for pilots to display essential flight information that sits directly in their line of sight and is overlaid onto the real world.
Other content from Ingenia
Quick read
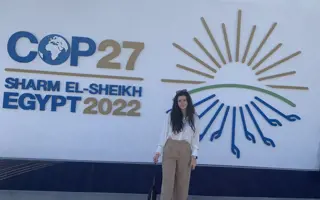
- Environment & sustainability
- Opinion
A young engineer’s perspective on the good, the bad and the ugly of COP27
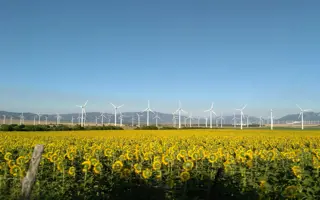
- Environment & sustainability
- Issue 95
How do we pay for net zero technologies?
Quick read
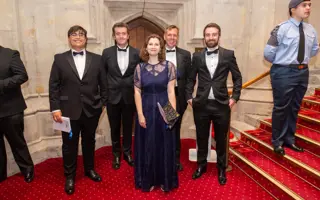
- Transport
- Mechanical
- How I got here
Electrifying trains and STEMAZING outreach
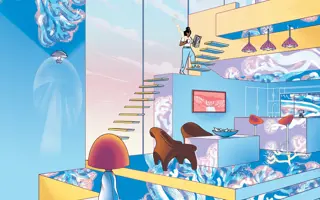
- Civil & structural
- Environment & sustainability
- Issue 95