
An Airship Renaissance?
A Hybrid Air Vehicles scale demonstrator proving the take-off and landing properties of its hybrid airship design
Numerous projects to develop airships have faltered because of technical and economic difficulties. Today, a team of British engineers is building a hybrid airship that looks set to succeed where others have failed. Dr Rebecca Pool, a freelance technical writer, finds out how the designs of airship innovator Roger Munk are now being used to build commercially viable airships.
After a century of mixed fortunes, the airship finally looks to have developed into a craft that can be a commercial success. Contractor Northrop Grumman commissioned a new breed of military surveillance airship for the US Department of Defense. This was designed by UK-based airship developer Hybrid Air Vehicles, and will soon start patrolling Afghanistan airspace. Known as a long-endurance multi-intelligence vehicle (LEMV), it is designed to sustain altitudes of 6,000 m for a three-week period, and will operate within national and international airspace.
The LEMV design is produced by a team of Cranfield-based UK designers. Their airship business had already developed a heavy-lift version of this design that can lift 50-tonne loads from surfaces including land, snow and ice, and water. Canadian operator Discovery Air signed an agreement for several such heavy-lift vehicles in 2011 and construction is scheduled for 2012 with take-off planned for 2015. So why are these hybrid airships succeeding when so many before have failed?
The differences
The so-called hybrid aircraft/airship – part-aircraft, part-airship – was conceived by the late airship pioneer and founder of Hybrid Air Vehicles, Roger Munk. Hybrid airships differ in several fundamental ways from the first wave of airships. First, and importantly, they are inflated with inert helium and air at just above atmospheric pressure instead of highly flammable hydrogen, the gas that contributed to the Hindenburg tragedy of the 1930s. Also designed without an internal frame, much of the modern airship’s lift is generated by the buoyancy provided by helium.

Ducted propellers being tested. These can be rotated to provide vectored thrust
In addition, the hybrid airships also have a new wing-shaped hull designed to develop aerodynamic lift as the craft is driven, and guided, through the air by its four ducted propulsors. These propulsors are in fact four engines, with vane actuation to provide vectored thrust to control the attitude and angular velocity – or manoeuvrability – of the vehicle.
For the heavy-lift version, more powerful propulsors can also provide upward thrust for vertical take-off and landing. The more powerful engines also enable the craft to lift and carry up to 50 tonnes.
Finally, unlike its predecessors, this generation of airship has an inflatable landing system, known as an Air Cushion Landing System, which is used for landing, taking off and manoeuvres on the ground. Unlike their conventional predecessors, Hybrid airships need no large ground crews to secure them with tethers on landing. So how have engineers moved from yesterday’s blimps to today’s aircraft?
In the beginning
The 20th century brought a golden age of airships. In June 1898, Count Ferdinand von Zeppelin began construction of the world’s first rigid airship to take flight, the LZ-1. With a 130 m rigid metal frame covered in rubberised cotton fabric, the structure housed gas bags that contained around 11,200 m³ of hydrogen. The airship was powered by two four-cylinder water-cooled Daimler gasoline engines producing 10 kW each.
Over the next 15 years, Zeppelin airships were built with sturdier frames, streamlined hulls, more powerful engines and aerodynamic features, such as cruciform fins, to boost stability. Now some 200 m long, and able to cruise at 140 km/h for around 12 hours, these vessels as well as US Navy and British Army versions played a crucial role in World War One and led to the development of the Hindenburg and Graf Zeppelin giants. Each of these vessels was 250 m long and intended to ferry at least 120people around the world. However, the 1938 Hindenburg tragedy, in which 13 of 36passengers and 22 of 61 crew members died, signalled the end of the airship heyday.
Helium takes over
After a long hiatus, the 1970s brought renewed interest in the airship, instigated by the design of a massive, non-rigid, helium-filled airship to transport gas, as part of the Shell Gas Transportation project. Although this airship never got off the drawing board, project leader and marine engineer Roger Munk realised he could design a new type of airship that could lift heavy loads in the same way as aeroplanes and helicopters, and be controlled much better in the air and on the ground than past airships.
Instead of being assembled with the heavy, internal framework that characterised the Zeppelins, he could see the advantage of pumping up the vessel with lighter-than-air helium. The gas pressure would maintain the vessel’s shape and also provide it with most of its lift.
In addition, he would design a novel shape to optimise aerodynamic lift and at the same time integrate engines that provide extra power. These engines would improve manoeuvrability on land and in the air as well as increase the vessel’s lifting capacity.
Munk built his first non-rigid airship prototype in 1979, which at 50 m long and containing 5,130 m3of helium was small by Zeppelin standards. The propulsion system contained vectored thrust engines: Porsche engines driving ducted fans tilted to drive the airship upwards or downwards. Propulsion ducts also allowed these units to move through 210°, allowing full manoeuvrability of the vessel in the air. Importantly, the ducts also helped to improve ground handling, even during winds, reducing the need for large ground crews.
The airship’s envelope was fabricated with a tough, single-ply polyester coated with titanium dioxide-doped polyurethane. Meanwhile, a large Kevlar gondola sited on the underside of the airship was built to carry nine passengers and two crew. This hung from the top of the envelope via a system of 14 Kevlar cables, with the load spread along four arched parabolic load curtains bonded to the top of
the envelope.
Later versions had a 30% bigger envelope, increasing lift by 50%. This, coupled with the use of twin Porsche 930/67 turbo-charged engines giving 220 kW each, meant that heavier weights – up to 18 passengers – could now be carried.
Despite the design breakthroughs, only six vessels were built during the 1980s, to be used mainly for advertising purposes. However, these airships formed the basis of Munk’s future designs. In June 1987, he won a major $170million US Navy Airship contract with its joint venture partner, Westinghouse, to build a half-size model of his Sentinel5000, which at 68 m long was 9 m longer than his first prototype.
The new airship took off in 1991, and was the largest airship in the world at the time, but disaster struck in 1995 when a hangar fire destroyed the airship and nearly all of Munk’s company assets, ending the Navy Airship programme.
Undeterred, Munk continued to develop lifting hull concepts for airships that could be operated remotely, leading to three further airship designs. The first was the StratSat, designed to operate at 18,000 m for up to five years, fuelled by a diesel- and solar-powered propulsion system. A prototype was built and flown in 2002. The second, the AT-10, a five-seat, diesel powered non-rigid airship was designed in 1997 and built for a customer in the Far East.
His third concept was the hybrid airship. This was designed with a novel three-lobe hull to maximise aerodynamic lift as well as a hovercraft cushion system to help the vessel land and take off and ensure that it could be controlled on the ground. Munk died from a heart attack (aged 62) in 2010, just months before the US Military awarded his company a contract for a surveillance hybrid. Canada’s Discovery Air commissioned his company to build the hybrid Heavy Lift vehicles in the autumn of 2011.
The airship today
The first contract from the US military for a surveillance hybrid airship follows a decade of operations in Afghanistan and Iraq. In these countries, armed forces have relied on the use of unmanned aircraft – typically fixed-wing craft – but now need vehicles that can remain in the air for much longer. At the same time, the Department of Defense has expressed an interest in using the same unmanned vehicles to carry cargo – this has opened the way for the hybrid airship/aircraft.
Like conventional airships, hybrid versions can take off and land at non-airport bases without the need for a landing strip, a major advantage to the military. But these part-airship part-aircraft vessels have additional benefits.
Munk designed his hybrid airships with an elliptical cross-section and cambered longitudinal shape. This wing-shaped body produces far more dynamic lift than the early cigar-shaped airship designs. This new design, with its combination of buoyant lift from helium, aerodynamic lift from the vessel shape and vectored thrust, can transport heavier loads for a given volume of helium than conventional airships which rely on buoyancy alone. What’s more, this triple lift combination also makes hybrid versions easier to control in turbulence and wind with its bow thruster providing additional control. The hybrid airship can take-off in winds of up to 75 km/h.
These features will be put to use soon, when Hybrid Air Vehicles completes its $517million US army contract, won in partnership with US defence contractor Northrop Grumman. The surveillance LEMV has four vectored thrust engines; two at the front and two towards the rear of the hull. Once on station at its cruising height, the vehicle will operate so as to minimise fuel consumption to around 17 litres per hour, thus enabling the vehicle to stay aloft for up to 21 days.
Construction details
Materials have moved on since the 1980s and the Hybrid Air Vehicles heavy lift vessel’s hull is now fabricated with a light, three-layer composite material electronically welded together to provide strength, UV and weather protection and to retain the gas.
The payload module will be built on the centre line beneath the airship and will comprise a flight deck to house the pilot station and controls (for the manned version), flight control system and payload compartment as well as the vessel’s fuel tanks.
Gas aside, and in line with Munk’s original concepts, there is very little structure inside the vessel. As with past non-rigid airships, internal diaphragms support its shape while a parabolic suspension system of Kevlar cables hangs from the top of the vessel and is attached to the payload module to support and distribute its load across the airship hull. Airbags or ballonets within the hull control pressure; as the vessel rises, the helium inside the hull expands and air is pushed out of the ballonets; four small motors re-inflate each of the ballonets as the vehicle descends.
The first surveillance hybrid airship is nearing completion and is due to be operational in Afghanistan by the end of 2012.
Load carriers
As the US Army puts the surveillance hybrid airship through its paces, Hybrid Air Vehicles will start building the first heavy-lift vehicle for Discovery Air. With its streamlined shape, buoyancy and powerful engines, this hybrid airship can carry up to 50 tonnes over 4,000 km, approximating to the payload and distances offered by today’s fixed-wing military aircraft. Clearly, the airships travel at much lower speeds – top cruising speed is 200 km/h compared to an aircraft’s 800 km/h – but as with surveillance versions, these craft do not need airstrips for take-off or landing. What’s more, these vessels can save up to 60% of the fuel that would be consumed by an equivalent fixed-wing air transport because around 60% of their lift is generated by the helium.
The heavy-lift airship design is similar in shape to the surveillance ship but instead of the four lower power engines, this version has four much more powerful gas turbine engines – see Specifications of the Hybrid Air Vehicles airships. The payload module is larger with two pilot stations and a bigger payload bay.

A Hybrid Air Vehicles scale demonstrator was used to prove its patented air cushion landing system which also gives the vehicle hovercraft like properties which enable it to take off, land and manoeuvre on water as well as on ground – or any other moderately flat surface
Whereas the surveillance airship has light pneumatic tubes on the underside of the outer hulls to provide stability on land, the heavy-lift version has ‘hover-pads’, which are inflated or deflated with four separate power units. These enable vertical take-off and landing for payloads of up to 20 tonnes (above this, the airship needs to take off with some forward motion). On landing, air is blown downwards, landing the vessel gently, at which point air is then drawn back up the pads so that they act as suction anchors fixing the airship firmly to the ground.
Vertical take-off and landing in a range of terrain, coupled with massive fuel savings, make the vessel appealing to a variety of industries. The recent Discovery Air deal will see airships carrying cargo for the mining industry to remote regions of the Arctic where roads and infrastructure have not yet been built. And as oil and gas exploration progresses to ever more remote regions and further out to sea, the need for a vessel that can transfer equipment and people to rough terrain or offshore platforms will only increase. With this in mind, Hybrid Air Vehicles has laid out plans to scale up its airship in stages and use more powerful engines to increase payload capacity first to 200 tonnes, and then eventually to 1,000 tonnes.
The next Golden Age?
Just as the Zeppelins carried tourists across the Atlantic in the 1930s, the hybrid airship could eventually double as a cruise ship. Enthusiasts suggest converting a payload module to a passenger cabin that could house 300 passengers on a 48-hour luxury flight across the Atlantic. While a lot slower than today’s transatlantic flights, the airship crossing would use only one fifth of the fuel consumed by a conventional aeroplane. Furthermore, passengers could board in a London park instead of driving out to an airport.
If luxury passenger transit sounds ambitious, a European Commission project has even greater hopes for the technology. Engineers and researchers from the EU, Russia and Uruguay are designing a more efficient cargo transport system, the Multi-body Advanced Airship for Transport, which is in effect a mobile flying logistic centre.
Instead of using thousands of planes and ships to transport millions of tonnes of goods every year, the researchers are investigating the idea of a massive airship that would cruise at around 200 km/h, 15 km high, on a fixed route. Smaller, feeder airships would dock onto the larger vessel, depositing goods and passengers for later collection and delivery by an earthbound airship. Importantly, the system would be powered by photovoltaic cells (PVs) by day (the PVs would also produce hydrogen and oxygen) and hydrogen fuel cells by night, leaving no trail of carbon dioxide emissions.
The project started in November 2011, with engineers initially looking at key aspects such as the best architecture for its airships and the easiest procedure for docking operations. Even if this research proves successful, such a transport system will take decades to realise.
In the meantime, Hybrid Air Vehicles intends to ramp up production of its current designs to tens of units a year within a few years. Whether high-flying, multi-body airships ever get beyond the research stage or not, we can now say with some confidence that deployment of Munk’s hybrid concept is now very close to commercial reality.
Keep up-to-date with Ingenia for free
SubscribeOther content from Ingenia
Quick read
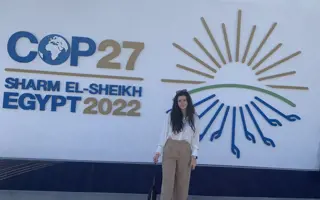
- Environment & sustainability
- Opinion
A young engineer’s perspective on the good, the bad and the ugly of COP27
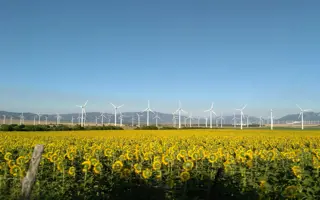
- Environment & sustainability
- Issue 95
How do we pay for net zero technologies?
Quick read
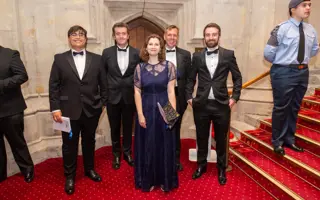
- Transport
- Mechanical
- How I got here
Electrifying trains and STEMAZING outreach
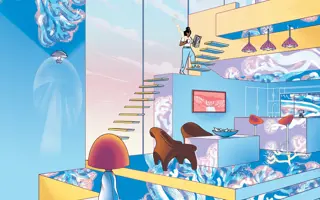
- Civil & structural
- Environment & sustainability
- Issue 95