
An aircraft like no other
For more than a century, airships of various kinds have been seeking a sustainable commercial role. So far, no venture has lasted indefinitely, but now, British company Hybrid Air Vehicles (HAV) is confident that it has found the way forward. New materials, new technologies, and most importantly, new thinking have combined to produce the newest breed of airships: a 92-metre craft called Airlander 10. Its capacity for landing anywhere without large numbers of ground staff and, if necessary, staying airborne for weeks at a time offer clear advantages in performing all sorts of tasks.
Unusually, Airlander combines the features of traditional airships with others derived from heavier-than-air machines. Not all its lift is provided by the buoyancy of the gas within its hull: up to 40% is a product of its aerodynamic shape. It is this innovation in aeronautical engineering, its hybrid status, that HAV believes will allow Airlander to rise above the weaknesses that have eventually sunk so many previous forays into this most eye-catching form of transport.
Airlander: A brief history
💸 From the million dollar defence programme to the first UK test flight
Airlander 10’s manufacturer, Hybrid Air Vehicles (HAV), was set up by Roger Munk in 2007. Its first customer was the US Army who needed an unmanned aerial surveillance craft for use in Afghanistan. The craft had to be able to fly for long periods, and at altitudes of up to 20,000 feet, out of range of local weaponry. HAV was to asked complete its part in the $500-million-dollar programme in the extraordinarily short period of 25 months. It did so, and a successful test flight of what was then called the HAV 304 took place in New Jersey, USA, on 7 August 2012. It was to be the only such outing. Defence budget cuts and the US government’s increasing determination to get out of Afghanistan led to the demise of the programme. By the time it was axed, $300 million had already been spent.
HAV saw its chance. The company had a proven craft for which the development costs had been paid, but for which the US Army no longer had a use. There being no competing bids, HAV was able to buy the craft back for a mere $301,000, virtually scrap value, and less than it cost to dismantle it, roll it up, and ship it across the Atlantic. On arrival in Cardington in December 2013, it was repaired, reassembled and reinflated. Some 500 modifications later, and with the support of private investors and grants from the UK government, Airlander 10, as it was now called, was ready for its first test flight.
Unusual design
Seen from the side, Airlander looks like most other craft of its kind. However, the view from any other angle reveals it to be quite different. It has an oval rather than round cross-section, while it resembles a pair of fat sausages pressed side to side when viewed from the front. When seen from the rear, those two sausage shapes have morphed into three. This configuration creates an aerodynamic shape and the forward movement of the craft generates lift.
It has an oval rather than round cross-section, while it resembles a pair of fat sausages pressed side to side when viewed from the front
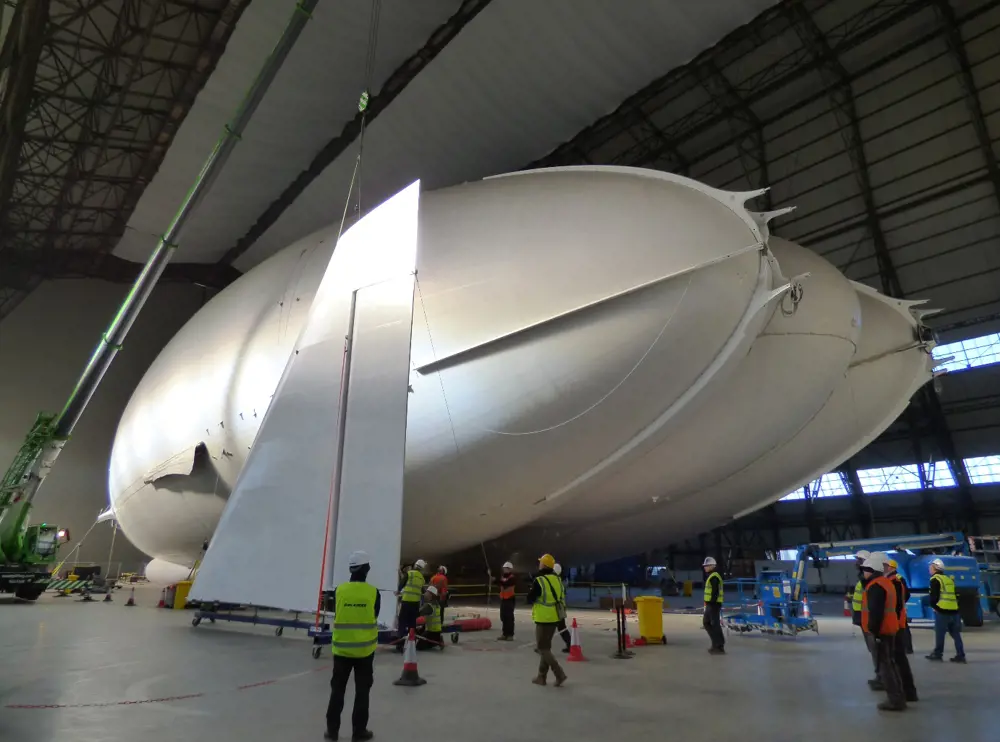
From the back, the Airlander resembles three sausages that have been squashed together, an arrangement that creates an aerodynamic shape, which is assisted by two top fins and two lower fins – one of which can be seen before it was attached to the hull © Hybrid Air Vehicles
The origins of this innovative design lie with the late Roger Munk, a British engineer born in the late 1940s, who became fascinated by airships and then set out to find a way of making them a mainstream transport system. One of Munk’s inspirations was Sir Barnes Wallis CBE FRS, who had worked on airships and headed the design team responsible for the R100, a craft that had intended to offer mail and passenger services to the countries of the British Empire but was grounded after a flight to and from Canada in the 1930s. Sir Barnes told Munk that the future success of airships would depend on overcoming a clutch of key hurdles. These ranged from the use of stronger and lighter plastics and composite materials to the introduction of more advanced flight control systems.
Over the years, Munk tackled them all. His key insight was the feature that sets Airlander apart from its predecessors: its mode of flight. While traditional airships, almost by definition, have relied on their inherent buoyancy, Airlander is slightly heavier than air and its default direction of free movement is not up but down. Only when in motion does it generate the lift it needs to start rising. Airlander combines the cost efficiency of an airship, with some of the performance virtues of an aircraft.
Airlander combines the cost efficiency of an airship, with some of the performance virtues of an aircraft
Airships by type
🛫 What are the different types of airships?
- Airships or dirigibles
Any powered aircraft that is steerable, and inflated with a gas lighter than air. - Blimp
A powered, steerable, lighter-than-air vehicle with no rigid internal structure. Its shape is a consequence of the pressurised gas within it. - Semi-rigid airship
An airship incorporating a limited rigid frame, typically a keel, to support it and distribute loads. - Rigid airship
An airship with a shape fully defined by a complete internal framework. - Hybrid airship
An airship that relies on aerodynamics as well as the gas within it to provide lift.
Unlike most of its large predecessors, Airlander has no internal framework. Its shape derives entirely from the pressure of the gas within its hull, which comprises some 7,000 square metres of fabric made up of multiple layers of three materials: Vectran, a fibre spun from a liquid crystal polymer and often used in high-performance sails; Mylar, a tough polyester film to ensure that the envelope (structure) is helium-tight; and Tedlar, a vinyl fluoride polymer with good resistance to weather and chemicals. These materials were heat-welded to form a single thin, flexible yet remarkably tough sheet. Delivered to the manufacturing site in rolls, it was cut to shape before the individual sections were assembled by heat-welding. Most existing airship hulls have been made out of polyester, which can stretch when subject to pressure, but the material used to construct the Airlander is more resilient.
Weight and strength are key factors when making the choice of any components for an airship, not just for the envelope of the hull. HAV used Forward Composites to make many of the larger components of Airlander’s rigid structures. The carbon and glass composites needed for some of the structure behave differently when pulled in different directions. This has necessitated careful structural analyses to determine how many layers of material were required at specific locations.
Its pressure, continuously monitored by instruments within the hull, is set only 0.15psi (pound-force per square inch) above atmospheric, so that any leak that might develop would be slow
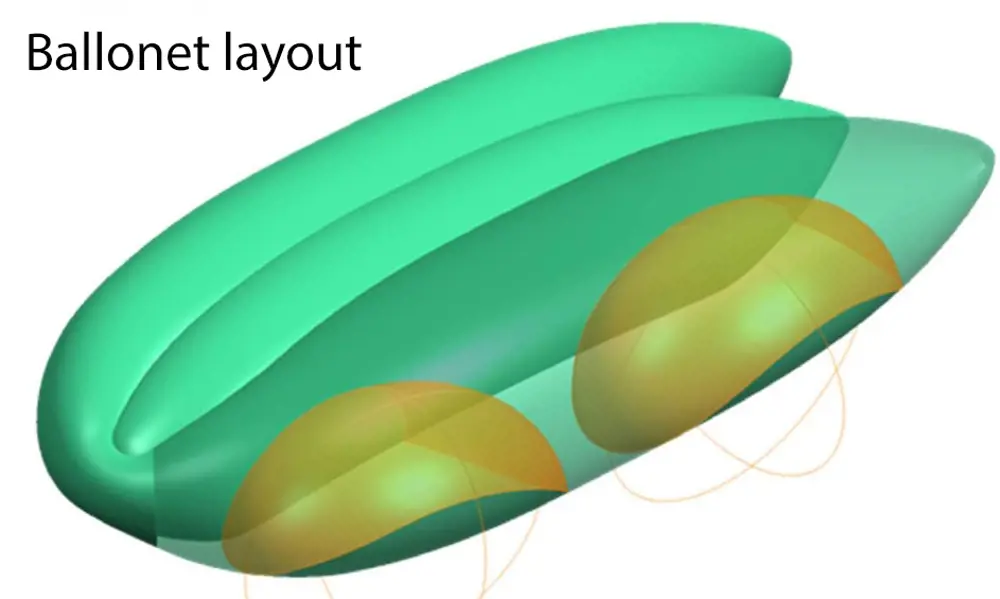
Airlander has four ballonets (seen in yellow), or air-filled balloons, within its hull. These serve to maintain the helium inthe hull at a constant pressure difference with respect to the outside air. At ground level the ballonets, which are made of the same material as the outer fabric and connected via four vents to the exterior, occupy up to a third of the volume of the craft. As the craft rises and the outside air pressure falls, the helium expands, expelling air from the ballonets, while on descent the reverse happens. The movement of air into the ballonets is aided by large fans set in the openings to the exterior © Hybrid Air Vehicles
The risks posed by a hull filled with hydrogen are obvious, so Airlander uses helium, which is an inert gas. Its pressure, continuously monitored by instruments within the hull, is set only 0.15psi (pound-force per square inch) above atmospheric, so that any leak that might develop would be slow. Moreover, the interior of the hull is divided into 15 compartments that are linked by valves that normally allow the helium to move freely between them, but can be closed if required to isolate individual sections. In contrast with the high-tech materials science that underpins the fabric of the envelope, the methods for detecting punctures in it are more traditional. One is to shine a bright light on its outer surface while observers inside the hull scrutinise its inner surface, looking out for chinks of light. Another is to spray the exterior surface with a soapy solution and look for emerging bubbles. Any repairs that are needed are fixed with a heat-welded patch.
Although it is the second most abundant element in the universe, helium is relatively rare on Earth and mostly produced by the radioactive decay of thorium and uranium. It can be found in varying amounts (from 7% down to nil) in natural gas. Although helium is a finite resource, HAV insists – in spite of occasional claims to the contrary – that we are not yet in imminent danger of running short of it.
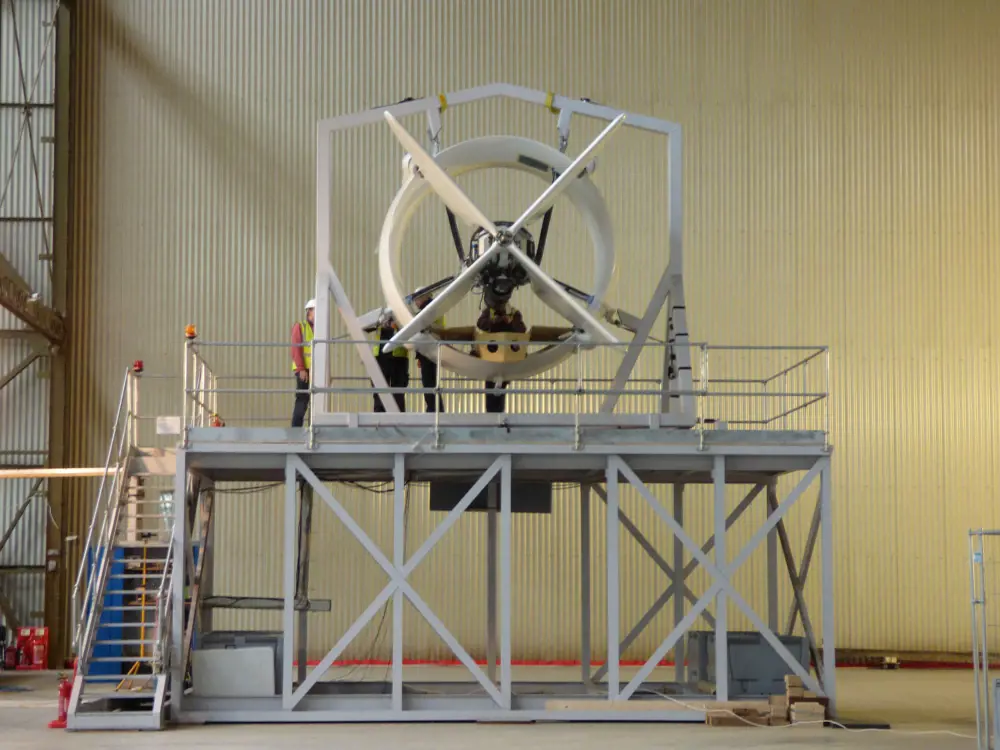
Four 325 horsepower turbocharged engines with variable pitch propellers power the Airlander. They are lighter than engines that were used for previous generations of airships and the absence of a rigid interior framework means that they need to be attached directly to the fabric structure of the craft © Hybrid Air Vehicles
The craft in flight
Airlander is powered by four 325 horsepower turbocharged engines with variable pitch propellers. These engines, which use standard aviation fuel, are lighter than those available to previous generations of airship designers. Even so, the absence of any rigid interior framework means that each must be attached directly to the fabric envelope of the craft. Close inspection of the hull next to the forward engines mounted on either side of the craft reveals virtually no sign of the local distortion to its shape that might be anticipated. The remaining two engines, each mounted on the conical rear tips of the hull, are supported by forward-running carbon composite battens, which also support the shape, attached to the fabric of the craft.
The forward engines on the current prototype Airlander can be swivelled by up to 30 degrees from a horizontal position to provide it with vectored thrust. (On later models the engines will be able to swivel through 180 degrees.) Butterfly vanes mounted behind the propellers also allow the airflow to be directed at will. Two side fins and two top fins with rudders are attached directly to the fabric of the hull, and stabilised by Parafil cables, a type of low-weight, high-tensile-strength synthetic rope that typically comprises a closely packed core of parallel polyester fibres encased in a durable black polymeric sheath.
At speeds of up to 30 knots, the craft is mostly steered by engine thrust. Above 30 knots, steering relies on the rudder and elevators on the lateral fins. The Airlander 10 is not currently intended to take off and land vertically, although the company believes it probably could and later production models will most likely include this facility.
It can carry up to 10 tonnes of cargo or passengers
Airlander 10: The basics
📏 From dimensions to engines, the specifications of the Airlander 10
- Length: 92 metres
- Width: 43.5 metres
- Height: 26 metres
- Volume of hull: 38,000 cubic metres
- Total weight: 20,000 kilograms
- Altitude: 4,880 metres
- Cruising speed: 80 knots
- Payload: 10,000 kilograms
- Range (with full load): 3,000 kilometres
- Engines: Four with 325 horsepower turbocharged V8 direct injection
Airlander’s payload module and fuel tanks are attached directly to the underside of the hull, which has a curtain of material and an array of strengthening wires connecting it to the hull’s upper surface. It can carry up to 10 tonnes of cargo or passengers, and immediately forward of where this is carried is the flight deck with seats for a pilot and co-pilot or engineer. The avionics are as advanced as those of any modern aircraft, but adapted to take account of a very different mode of flight. The central electronic control system connects with the engines, the rudder, all other mechanical components and with remote instruments and sensors via a fibre-optic cabling system. The HAV 304, which Airlander was derived from was among the first aircraft to use this ‘fly by light’ system, as it has been dubbed. Much of the seven kilometres of Airlander’s cabling runs on the craft’s outer surface, making it easier to access and maintain. When the British company (AVOptics) that manufactures the system was originally contracted to work on the airship, it found itself having to make cables ten times the length it was accustomed to.
Using a pair of skids running lengthwise beneath it, the craft can land on any surface. Pilots can practise this and other manoeuvres on the company’s custom-made flight simulator. Professional simulators for training airship pilots are, not surprisingly, pretty rare. HAV’s own simulator has undergone adaptations in which pilots found themselves teaching the simulator rather than vice-versa. The experience of a take-off is not unlike that of an ordinary aircraft but in slow motion, and as with large sea-going ships, the response to adjustments of the controls is not instantaneous.
Although Airlander can operate anywhere from the tropics to the Arctic, it is not wholly immune to weather conditions. Its 30 tonnes of weight give a stability that allows it to function even in ground winds of up to 80 knots. The absence of any rigid internal framework makes it less susceptible to the bending forces of side winds that could be a problem for previous generations of airships.
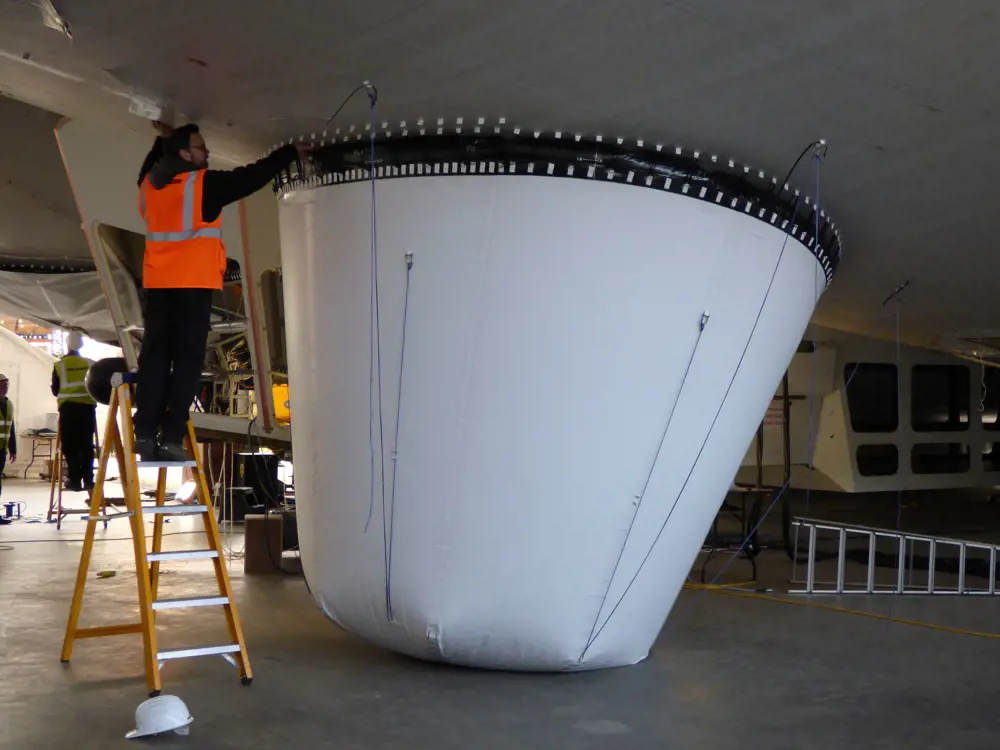
The auxiliary landing system was added to the craft following its crash. The system, a pilot-deployable two airbag landing system that acts as an extra cushion to land on, allows the aircraft to land safely at a greater range of landing angles. The airbags are over three metres in length and contain 15 cubic metres of gas (less than 0.1% of the entire hull volume) and are situated on each side of the flight deck to offer enhanced protection to the cabin and flight deck. The system uses the existing ballonet fans to inflate, and takes under 20 seconds to be ready for use © Hybrid Air Vehicles
From testing to operation
Airlander 10’s first test flight, carried out on 17 August 2016 was a complete success. Its second was less so, with the aircraft crashing into the ground as it attempted to land. The hard landing caused no harm to either member of the crew, but severely damaged the control cabin and delayed the test programme by some six months, possibly costing the company £2 million.
Fortunately, some of the testing was able to continue while repairs to the cabin were underway. Although all of Airlander’s systems continued to operate after the crash, there were lessons to be learned. HAV knows exactly how and why the accident occurred, and is confident that it will not be repeated. Either way, Airlander 10 has now been fitted with an auxiliary landing system: in essence a pair of giant air bags located slightly ahead and to either side of the flight deck. These will be routinely deployed immediately before most landings, rather as an aircraft lowers its undercarriage.
On 10 May 2017, Airlander resumed its Flight Test Programme with a successful three-hour flight. The flight test consists of three phases, during each of which Airlander flies further from its airfield and pushes its speed, altitude and endurance, among other variables, a little further each time. Flight testing will last for a number of months before a series of customer trials and demonstrations begins.
HAV believes that the biggest market will ultimately be in cargo but that may have to await the development of larger models
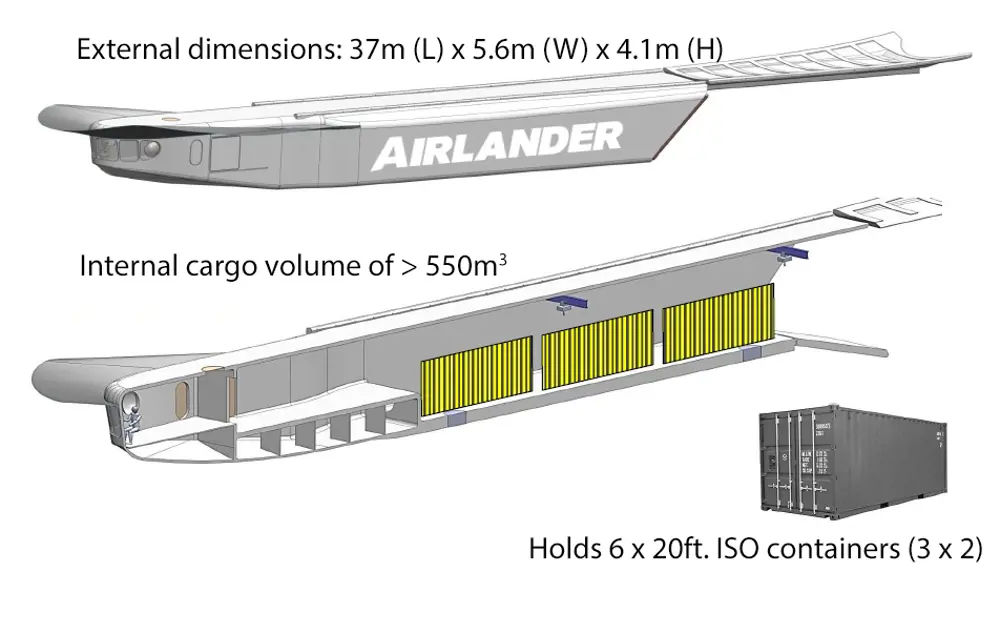
The proposed payload space of the Airlander 50, a cargo carrying aircraft that will be able to transport 50 tonnes © Hybrid Air Vehicles
Assuming that the reactivated test programme runs to time and uncovers no major problems, HAV hopes to have the first production Airlander ready for use by early 2019. It currently has over 2,000 shareholders and aims to increase investment, which is expected to happen once the aircraft is flying – an opportunity that the company has not previously had. With the aircraft flying and customer engagement driving forward, the intention is to raise £15 million to fund the early stages of production, with the aggregate level of funding required to support the move to full production at £70 million. Once production has begun, the company plans to list on the stock markets to secure the balance of funds needed.
The operation at the Airlander’s base in Cardington, Bedfordshire, is essentially an assembly process, with engines, fabric and so on brought in from elsewhere. The company anticipates being able to manufacture 12 Airlander 10s a year. It envisages them finding a role in surveillance by law enforcement agencies or the military, for oil and gas pipeline surveys, or for luxury tourism (for example, seeing the Grand Canyon from the air). However, the initial production run is expected to be focused on an endurance-optimised Airlander that will provide a platform for patrol, search, survey, communications and filming. HAV believes that the biggest market will ultimately be in cargo but that may have to await the development of larger models.
An independent study by the aerospace consultancy firm Renaissance Strategic Advisors talked of a $50 billion cargo market for airships over a 20-year period, and a need for perhaps 600 craft. It also suggested that success in the cargo field might have to await the advent of a 50 tonne payload. With this in mind, HAV already has outline plans for an Airlander able to carry a payload of 50 tonnes in the form of half a dozen 20-foot containers. However, the size of the potential market remains a matter for speculation, not least because a new combination of longer transit time but lower cost might create a case for moving certain goods – perishable foods, for example – that seldom make long journeys at present, or do so only in small quantities.
The operational efficiency of airships is indisputable
The 2016 accident: How a winch failure led to a hard landing
🪂 The second test flight coming to an undignified end
Trying to test something the size of Airlander 10 in private is impossible, so it was in front of a clutch of camera lenses that Airlander’s second test flight came to an undignified end on August 24 2016.
The culture of openness and safety that characterises the reporting and analysis of aircraft incidents applies equally to airships. A report by the Air Accident Investigations Branch, published at the beginning of March 2017, tells the story of Airlander’s accident. The test flight lasted a little over 90 minutes and was successful. It approached its mooring mast and deployed the mooring cable. Ground staff attached this to the winch intended to complete the landing operation, but the winch failed to start. The pilot decided to make another circuit while it was fixed but the lack of any pre-arranged system for dealing with the mooring cable under these circumstances left it dangling from the front of the craft.
The pilot was told that the cable was roughly 50 feet in length. In fact, it was three times as long as that, and consequently snagged some overhead wires. To avoid further mishap, the pilot was obliged to make his second approach to the landing area at well above the prescribed height. This and other circumstances led to a steeper than intended angle of descent – and a hard landing.
The operational efficiency of airships is indisputable. They require no runway and little ground infrastructure, and even without vertical lift-off can manage with a space around four times their own length. While helicopters have an operating range measured in hundreds of miles, airships can beat that by an order of magnitude. Their low fuel consumption per unit of payload gives them a carbon footprint well below that of any other powered flying machine.
Operating costs depend on the job in hand and on its location but modelling done by the company on, for example, transporting people or goods to mines in remote parts of Northern Canada suggest that the Airlander comes out at about 10% of moving equivalent loads by helicopter and is a third of the cost of using cargo aircraft. Military surveillance costs are also an order of magnitude cheaper; a task that might cost £20,000 an hour or more using a helicopter would be closer to £2,000 to £3,000 per hour using Airlander.
Commentators have so often and for so long predicted the imminent revival of the airship as a serious contender in the transport market that further prophecy would be reckless. What can be said is that present circumstances – the emphasis on fuel economy and the advent of new technologies and materials – provide a setting more favourable to success than any for half a century. If HAV cannot make a commercial success of a craft such as Airlander, it is difficult to imagine who ever will.
***
This article has been adapted from "An aircraft like no other", which originally appeared in the print edition of Ingenia 71 (June 2017).
Contributors
Geoff Watts
Author
Chris Daniels is Head of Partnerships and Communications at Hybrid Air Vehicles, and has been with the company for four years. He has a mathematics degree from the University of Oxford and an MBA from IESE Business School, Barcelona.
David Burns is Chief Test Pilot at Hybrid Air Vehicles. He has flown for Loganair, British Airways and Monarch Airways. David began flying airships with Airship Industries in the early 1980s and has worked with them and successor companies in testing, training and operations in many parts of the world.
Keep up-to-date with Ingenia for free
SubscribeRelated content
Aerospace
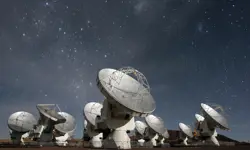
ALMA – the high altitude observatory
The Atacama Large Millimetre/submillimetre Array (ALMA) is the largest and most expensive ground-based telescope built, revolutionising our understanding of stars and planetary systems. Building it in the Atacama Desert in Chile required the ingenuity of hundreds of engineers.
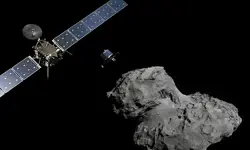
Communicating with outer space
The Royal Academy of Engineering awarded a team at BAE Systems the Major Project Award in June 2016 for their development of a powerful satellite modem system, pivotal in enabling the precise control of the pioneering Rosetta spacecraft and the first-ever soft landing of a spacecraft on a comet.
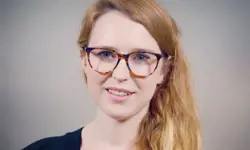
Q&A: Lucy Harden
Lucy Harden is a mechanical engineer on BAE Systems’ Digital Light Engine Head-Up Display development programme. She devises innovative solutions for pilots to display essential flight information that sits directly in their line of sight and is overlaid onto the real world.

Ready to break records
In October 2017, almost a decade of engineering development finally came to fruition when the Bloodhound Supersonic Car embarked upon its first tests at Newquay Airport. Mark Chapman, Bloodhound’s Engineering Director, spoke about how it will attempt to break the world land speed record in South Africa.
Other content from Ingenia
Quick read
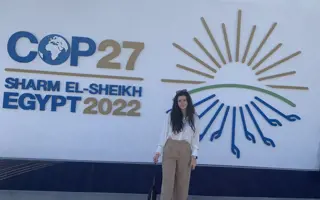
- Environment & sustainability
- Opinion
A young engineer’s perspective on the good, the bad and the ugly of COP27
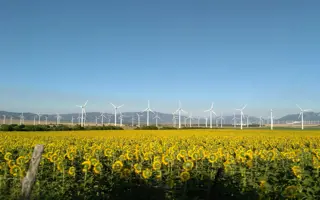
- Environment & sustainability
- Issue 95
How do we pay for net zero technologies?
Quick read
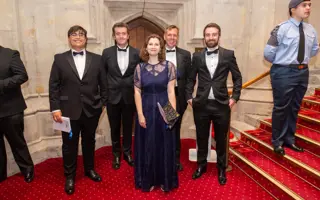
- Transport
- Mechanical
- How I got here
Electrifying trains and STEMAZING outreach
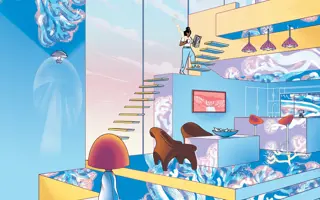
- Civil & structural
- Environment & sustainability
- Issue 95