
Against the tide
The sight of a sturdy 13-metre ocean-going craft powering its way at high speed towards a shingle beach would normally be a source of concern or even some alarm. However, if it is one of the Royal National Lifeboat Institution’s (RNLI) new Shannon-class vessels, what you’d be seeing is standard operating procedure. When it is time to bring a Shannon lifeboat home, the coxswain simply angles its bow toward the shore and opens the throttle*. To the accompaniment of a scrunching, scraping and slithering sound, the boat’s momentum carries it out of the water and up the beach to a point well clear of the waves.
While this is surely the most straightforward means imaginable of getting a boat onto dry land, the engineering that makes such a manoeuvre safe and feasible is far from elementary. Indeed, to design any feature of a lifeboat is a more than averagely exacting task; the sea and weather conditions that would prompt most similarly sized vessels to seek shelter are those in which a lifeboat may find itself being launched.
The Shannon, powered by water jets, is a product of careful thought about lifeboat design and operation. Its novel method of coming ashore is the most visible manifestation of what amounts to a minor revolution in the core business of the RNLI, part of a set of changes that encompass not only the engineering, design and operation of RNLI’s new generation of vessels, but also the organisation, location and economics of their construction.
Shannon: The technical basics
🚣♀️ The dimensions and capacity of the Shannon lifeboat
Length: 13.6 metres overall; 11.6 metres at waterline
Beam (width): 4.5 metres
Draught (depth): 1 metre
Displacement: 18 tonnes (maximum)
Maximum speed: 25 knots
Fuel capacity: 1,200 litres in each tank
Range: 250 nautical miles
Engines: 2 x 13-litre 650 hp Scania D13 engines; Twin Hamilton HJ364 water jets
Survivor capacity: six seated plus 17 standing inside, or 79 but without self-righting capacity
Slipway or beach
Some lifeboats are launched from permanent slipways; others from a beach. The choice for any particular location is determined partly by the local geography, and even more by history. If a boathouse and slipway are already in place, it would be perverse not to use them. Although the Shannon has been designed for beach launching, it can also operate from a slipway, and some already do so.
The RNLI’s need to consider a new design arises when any particular class of vessel within its fleet in has reached the end of its intended life: 25 years in the case of the Mersey, the beach-launched boat that the Shannon will eventually replace. It would have been possible to extend the life of the Mersey, but the RNLI decided that it wanted an all-weather boat capable of 25 knots, significantly higher than the Mersey’s 15–17 knots.
The RNLI’s need to consider a new design arises when any particular class of vessel within its fleet in has reached the end of its intended life
Besides wanting vessels suitable for launching and recovery on a beach, the RNLI identified a dozen or so other operational requirements when proposing the new Shannon class. These included the wind and wave heights with which the boats must be able to cope, their minimum range and duration of operation under full power, and their capacity to carry survivors and tow other vessels. Any new design seeks to improve on its predecessor, incorporate technical advances, and introduce innovations of its own. The Shannon manages to do all three.
Traditionally, RNLI has bought in boats from outside yards and modified them to its requirements, or sub-contracted the design process to others, albeit with RNLI input. For the Shannon, it judged that its own engineering team had sufficient knowledge to do the design work. The one exception, at least originally, lay in the central design feature of any new vessel: the shape (form) of its hull.
The development of the Shannon began a decade ago with an attempt to use the hull form of an existing pilot boat. The Fast Carriage Boat, or FCB 2 project as it was known, got as far as sea trials. These showed that the decision to opt for a water-jet propulsion system was fully justified, this technology offering distinct advantages over propeller-driven craft, especially when boats were making difficult manoeuvres or operating in shallow water. But the performance of the FCB hull in rough sea conditions was disappointing. In head seas (when waves or the current are running directly against a boat’s course), when travelling faster than 14 knots, there was an unacceptable amount of ‘slamming’, the term used to describe the juddering crash when a hull that has risen upwards as it moves through a wave falls back into the water.
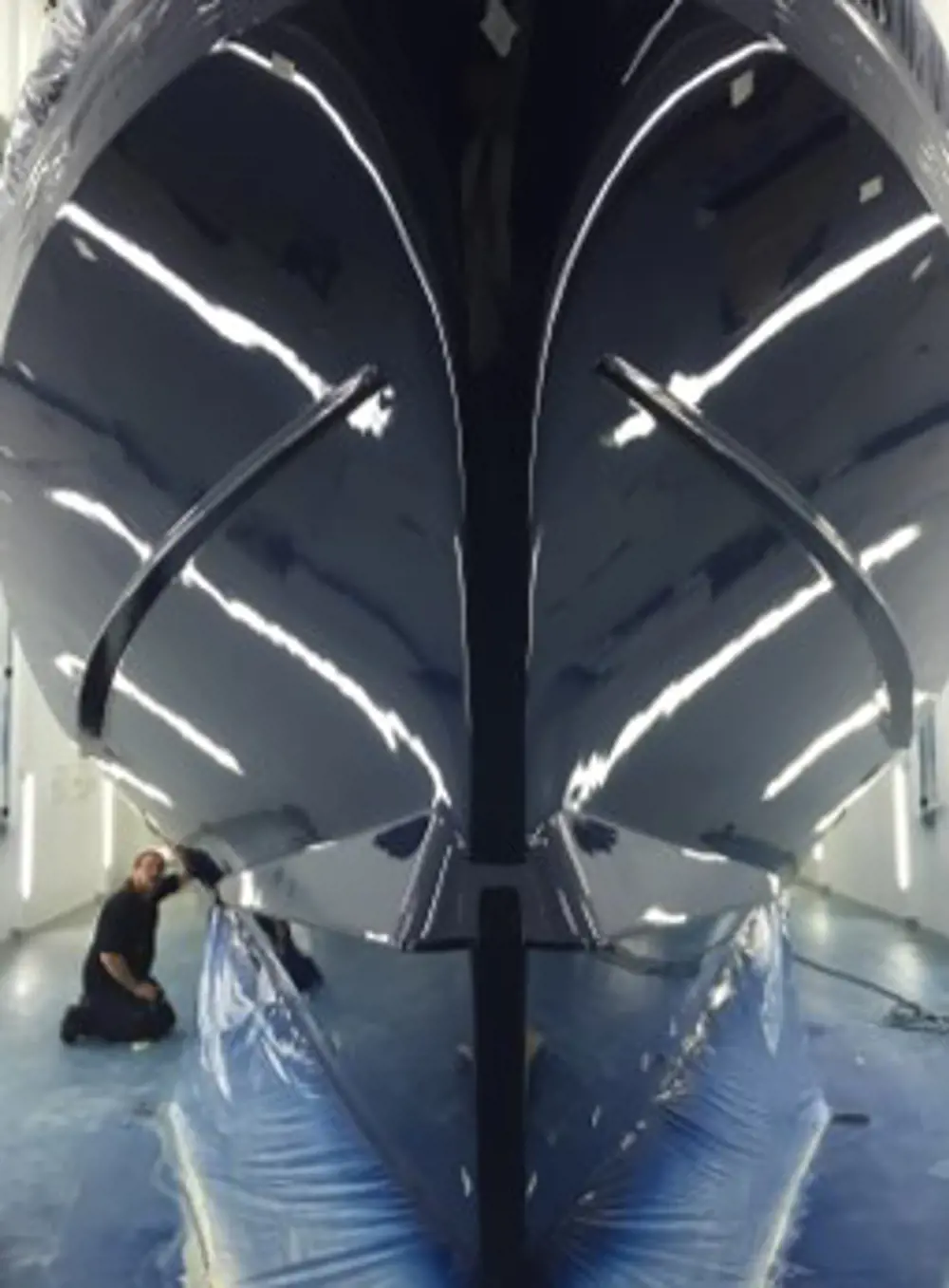
The Shannon’s hull was completely redesigned, after a competitive tendering and testing process. The shape and angle of the sides of the new hull reduce broaching when the boat is travelling in the same direction as the swell © RNLI
A new hull from scratch
The project team members decided that a completely new hull form would have to be designed, and set up a competitive tendering and testing process. At the time that this work was in progress, the team members were uncertain about the reliability of computer simulations of the anticipated performance of hull designs, particularly those expected to operate under the exceptionally challenging conditions facing lifeboats. Some virtual model testing was actually commissioned, but while the then state-of-the-art computational fluid dynamics were good for eliminating some designs, and for predicting the vertical acceleration of hull movements, work on the rolling component of their movements was less advanced. Most of the design decisions about the Shannon therefore relied on testing physical models.
It was during this period that one of RNLI’s own naval architects working on the project, Peter Eyre, decided to have a go at coming up with a new hull form in his own time. When he told colleagues what he was doing, he was invited to finish his design in office hours, and put it up to compete with the other shapes selected for testing.
To compare the hulls on the final shortlist, the team used 1.5-metre free-running models under radio control. Much of the testing was carried out in Poole Harbour where the ripples caused by force 1–2 wind conditions are equivalent to the waves confronting a full-sized hull in force 7 winds. The models carried accelerometers and other instruments able to record their motion in all dimensions as they sailed through a chosen stretch of water. By testing each model side by side with a standard hull for comparison, and so subjecting both to identical sea conditions at the same time, the team was able to measure their relative performance.
Transverse motions of the hulls when they rolled were particularly important in these tests because the crew seats developed for a previous generation of lifeboats are already good at absorbing the shock of vertical movements. Transverse movement is harder to manage and, if unchecked, can leave crews with damaged shoulders and backs. Having a hull that tracks well is also important because it minimises the amount of steering required simply to keep a vessel on course. The design team also carried out tow testing in a tank to garner more information about the performance of the hulls under specific wave conditions.
The Shannon is described as a ‘wet boat’: it tends to cut through the tops of waves rather than riding their crest, and this reduces the slamming
The result of this work was a shortlist of two, one of which was the hull design drawn up by Peter Eyre. In a final comparison this was the winner: an outcome that not only demonstrated the RNLI’s in-house expertise but also saved it money. The chosen design was a hull that is narrow at the bow but wide in the aft section, and steeper in the mid region: a shape that confers good stability and minimises slamming.
The Shannon is described as a ‘wet boat’: it tends to cut through the tops of waves rather than riding their crest, and this reduces the slamming. When the boat is travelling in the same direction as the swell, the shape and angle of the sides of the hull also reduce broaching – this being the tendency for some vessels facing severe conditions to steer by the bow and in some cases turn through 180 degrees.
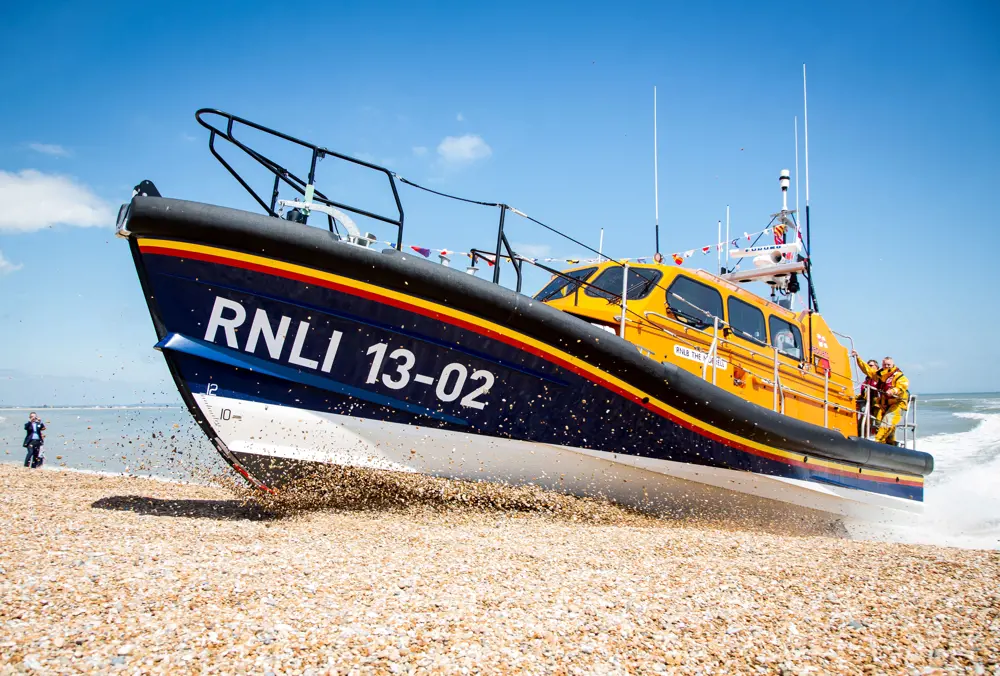
Being powered by water jets enables the Shannon to launch itself out of the sea and onto the beach easily without risking damage to a traditional rudder and screw propulsion system. The outer layer of the hull is also thicker than needed so that it is resistant to shocks and scratches © RNLI
Launch and recovery
To the outsider, if not to the crews, the Shannon’s most innovative feature is operational rather than structural: its capacity to leave the sea and return to land by beaching itself under its own power. This course of action is only possible because of engineering decisions taken during the design stage.
Conventional beach landings of the type used by lifeboats of previous classes can take up to an hour and require a fair number of helpers. The boat nudges to the beach, the land crew attach a cable and then winch it, bow first, out of the water. Well out of the water, in fact, because it has to be dragged stern first on to the tractor-hauled cradle used to transport it. This means that the boat must be sufficiently far up the beach to allow tractor and cradle to get between it and the sea. Performing these manoeuvres is time consuming, and in rough weather they can be difficult and dangerous.
the Shannon’s most innovative feature is operational rather than structural: its capacity to leave the sea and return to land by beaching itself under its own power
Beach landings of the type used by the Shannon are possible because it is powered by water jets. A conventional rudder and screw propulsion system would be, at very least, susceptible to damage. The Shannon, having hurled itself out of the sea and up the beach, can be well clear of the waves before anyone needs to approach it. Moreover, unlike its predecessors, it can be hauled bow first on to the cradle designed to hold and transport it. The cradle is attached to a new 444-horsepower tractor designed in consultation with the RNLI by the Devon-based company Supacat. Recovery time is around 15 minutes and can, in theory, be performed with as few as two people: savings that are particularly valuable when weather conditions are, as is often the case, severe.
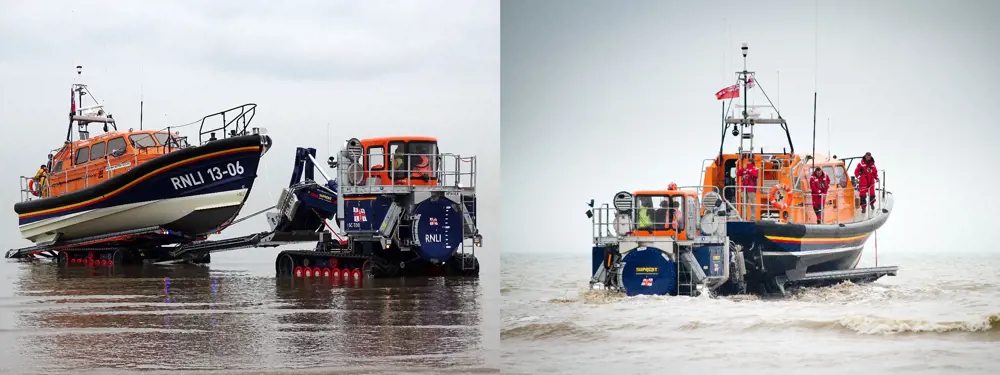
The Shannon can be recovered from the sea by the launch and recovery tractor. The boat sits on a ‘slewing ring’ that can be turned 180 degrees to relaunch the boat almost immediately © RNLI
The cradle, which also serves as a slipway for launching the boat, incorporates another innovation: a metre-wide ‘slewing ring’. In effect, the boat sits on a rotating platform that can be turned through 180 degrees. Once the vessel has been hauled on to the cradle and secured it can be turned round and, if necessary, relaunched almost immediately.
Lifeboats seldom need to be launched and recovered more than two or three times in a week, so the punishment of a beach landing is not an everyday occurrence. Even so, to cope with such a landing, the hull has to be built to withstand the initial impact and the abrading effect of sliding at speed over sand and shingle. The hull itself, 70 millimetres thick at the bottom of the boat, is a sandwich structure, composed of two layers of glass epoxy composite that are separated by a foam core. The outer layer is thicker than would be needed purely for structural purposes, the extra material giving it the required resilience to shocks and scratches. The outer surface is also covered with abrasion resistant coatings. Experience has shown that damage in these landings is minimal, and abrasion that does affect the hull surface – the loss of anti-fouling coats, for example – can be patched up in the boathouse.
The damage most likely to be sustained in beach landings is to the side keels, the two vertical fins mounted towards the rear of the boat and intended to minimise rolling when at sea. They also serve to improve the vessel’s tracking and, when beached, prevent it tilting too far on its side. If subjected to extreme force, they’re designed to peel away without damaging the underlying structure on which they are mounted. Replacement is relatively straightforward and the boat can still be operated in the meantime.
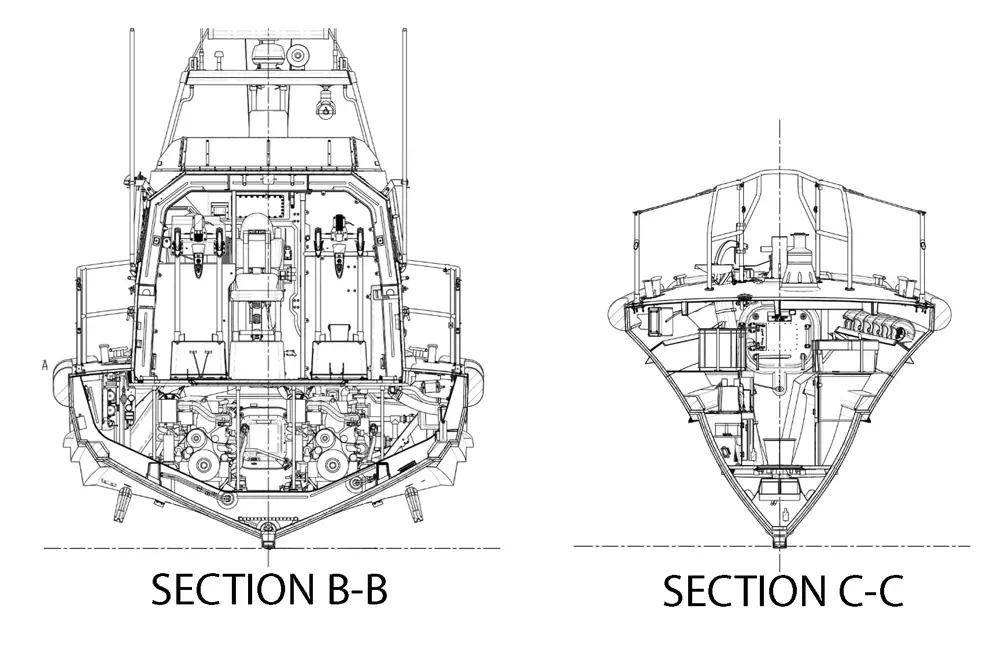
Section BB shows a cross-section of the Shannon class’s wheelhouse and engine room while section CC shows the forestore, where rescue equipment is stored. The diagram demonstrates the shape of the hull and the narrowness of the bow © RLNI
The brain of a boat
The brain of a lifeboat is its systems and information management system (SIMS). This provides access to the vessel’s intercom and other communications, displays navigational information (radar, charts, depth, speed etc), and also data about the performance of the engines and other machinery. An updated version of the system developed for an earlier class of lifeboat, the Tamar (‘Launching the Tamar’, Ingenia 33), the SIMS on a Shannon uses one screen to display all the information that a coxswain needs to operate the boat. However, the helmsman is not the only person who has access to it; screens can also be monitored and operated from the crew seats. Users are spared a cluster of different instrument faces competing for their attention, with a tracker ball they can scroll through the various screen images available to select just the information they need at any one moment.
In previous lifeboat models, the equipment required to run these systems was collected together in one place. In the Shannon it is distributed around the vessel. This has two advantages: weight is more evenly distributed and less cabling is required.
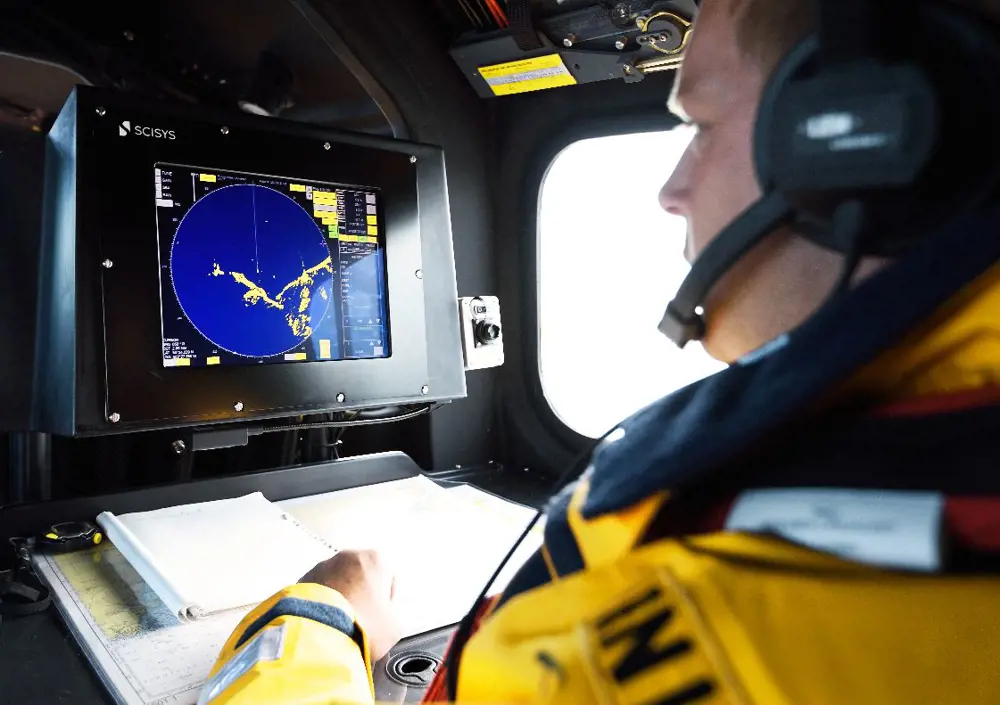
The systems and information management system provides access to the vessel’s intercom and other communications, displays navigational information such as radar, charts, depth and speed, and data about the performance of the engines and other machinery © Nigel Millard
Building the Shannon
The Shannon’s engineering and design innovations have been accompanied by equally important changes in the organisation, location and even ownership of the process of building it. RNLI’s long established practice was to have the hull and overlying wheelhouse fabricated by specialist composite manufacturers. This changed when it bought out its main suppliers, SAR Composites, and the company became an RNLI subsidiary. However, the hull and wheelhouse still went to a shipbuilder’s yard for fitting out, with the initial 12 Shannons going to Berthon in Lymington for this purpose before the RNLI decided to do the fitting out itself. But even this was not the end of the revolution.
In April 2015, RNLI formally opened its new and impressive All-Weather Lifeboat Centre. Located beside Poole Harbour, the centre comprises two large boat manufacturing and repair halls separated by a roofed area open at the sides used for storage and manoeuvring. Building this factory posed its own set of challenges because local planning regulations required the ground level of the site to be raised by a metre and half to avoid flooding. Much of the site was land reclaimed from the harbour and at risk of sinking when subjected to the new weight it was intended to carry. The site had to be compressed under a thick layer of sand – some 15,000 cubic metres in total – and left to settle for the best part of a year while water from the underlying soil was squeezed out through a large wick drain set into the sand and reaching down into the soil. The site then had to be piled and overlaid with load-transferring foundations in such a way as to distribute the weight they would eventually have to bear over as many piles as possible. An organisation accustomed to the hazards created by the marine environment had found itself having to deal with the less familiar problems posed by a terrestrial one.
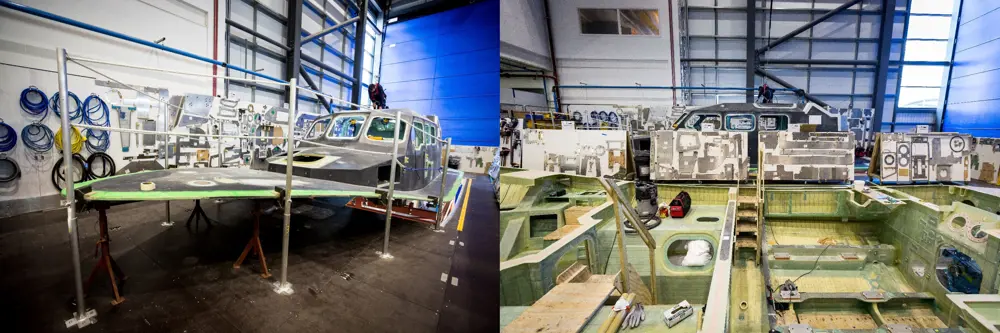
The entire construction of the Shannon takes place at the Poole All-Weather Lifeboat Centre. Each composite is created separately and joined together in aprocess that operates like a production line. A boat is completed every two months, resulting in six new boats a year © RNLI
Following the successful completion of the new centre, the RNLI moved the main manufacturing phase to the Poole factory. With the huge ovens required to bake the composites of the hulls and wheelhouses now joining the other large enclosed spaces required to paint and dry them, the entire process from start to finish is conducted on one site: another big saving to RNLI coffers. The centre operates like a production line, completing one boat every two months: a total of six per year. From start to finish the process takes about 14 months and the goal is to create a fleet of 50 Shannons.
Until recently, with orders for new boats going out to independent boat builders, there were inevitable peaks and troughs in production. Given that RNLI is a charity that relies on donations, an even flow of new boats simplifies the tasks of the fundraisers. For the coming years, they know exactly how much money will be required and when.
The future
The boats now being built should have a 50-year lifespan. As the first of them approaches the mid point of this period, it will be withdrawn for a complete refit in the Poole Centre, so marking the start of a boat-by-boat refurbishment or, depending on what new technology may have become available, an upgrade. The staff are confident that the Shannon hull will prove as serviceable during the second half of each boat’s life as they already believe it will have been during the first half. At a cost of £2.2 million each, Shannons are hardly cheap; but spreading that cost over 50 instead of 25 years represents another significant saving.
In the meantime, the staff at Poole continue to change and innovate. To allow more engineers to work more freely on the boats, for example, the two main structural components, the hull and the wheelhouse, are kept separate for as long as possible. When they are finally brought together, they are held by an improved form of bonded joint.
Another innovation is the use of composites with a lower carbon content. Any repairs that need to be made to a craft during the course of its life are quite likely to require grinding or sanding of the materials used to fabricate it. If carbon in the dust produced by this gets into the electronics it can cause shorting. This is normally avoided by protecting the electronics using polythene sheeting, or even temporarily removing sensitive equipment. However, the less carbon that is used in composites in the first place, the less the likelihood of such problems occurring.
At a cost of £2.2 million each, Shannons are hardly cheap; but spreading that cost over 50 instead of 25 years represents another significant saving
The first Shannon went into service in July 2013 and more than a dozen have now been deployed. This is the first time that the RNLI has used water-jet propulsion in a craft of this size, and the experiment seems to have paid off. Whether boats are required to crab sideways into a space or simply hold themselves accurately in one position, manoeuvrability is exceptionally good. Crews are said to be delighted with them, and have yet to report anything significant that they would like to change: a consequence, perhaps, of the input they were asked to give during the Shannon’s design phase.
Venerable institutions – a category to which the RNLI most certainly belongs – can become creatures of habit, resistant to change. Engineering as a discipline recognises no such constraints. It is surely to the credit of the RNLI that it has been able to identify what engineering has to offer and adapt accordingly.
***
*To see a Shannon lifeboat coming ashore, go to: www.youtube.com/watch?v=IBcTXJ7UGVg
This article has been adapted from "Against the tide", which originally appeared in the print edition of Ingenia 68 (September 2016).
Contributors
Geoff Watts
Author
Daniel Sharp is the Production Manager at RNLI, based at the new All-Weather Lifeboat Centre. He started work for the RNLI in 2001 as a lifeguard on the beaches of Poole during the summer while studying at university. In 2006, he took on a full-time naval architect role as part of the Shannon-class lifeboat project team, responsible for designing the Shannon class, producing the prototype and proving the design was suitable.
Keep up-to-date with Ingenia for free
SubscribeRelated content
Maritime & naval
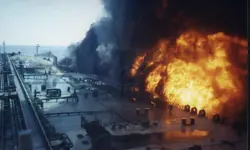
Modelling ships in danger
Stricken ships in danger of breaking up, sinking, capsizing or losing their fuel or cargo need expert help to be rescued. Lloyd’s Register’s Ship Emergency Response Service (SERS) was set up to provide this support.
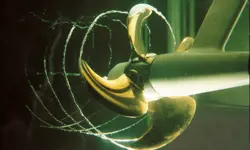
Quieter, more efficient propellers
Göran Grunditz, Manager of the Rolls-Royce Hydrodynamics Research Centre, explains the challenges when reducing noise from marine propellers for passengers onboard ships and for military vessels that seek to avoid detection, while maintaining a high thrust per input power and maximising efficiency.

Building Britain's biggest warships
The 1998 Strategic Defence Review called for the UK Armed Forces to be able to operate with more agility to confront situations on a worldwide basis and resulted in the requirement for two new Queen Elizabeth Class aircraft carriers, HMS Queen Elizabeth and HMS Prince of Wales, one of the UK's largest engineering projects.
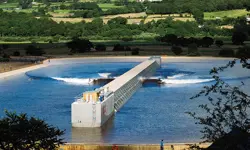
How to create the perfect wave
From small waves lapping at your feet and swells suitable for surfing to storm waves for testing structures and even tsunamis, waves of any shape and any size can now be engineered. What are the techniques and conditions needed to model waves and what makes some more powerful than others?
Other content from Ingenia
Quick read
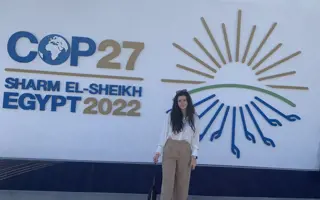
- Environment & sustainability
- Opinion
A young engineer’s perspective on the good, the bad and the ugly of COP27
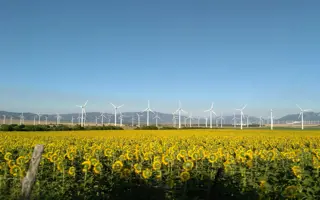
- Environment & sustainability
- Issue 95
How do we pay for net zero technologies?
Quick read
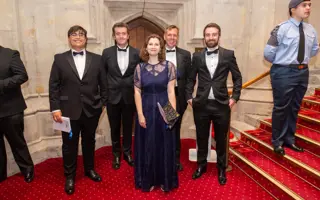
- Transport
- Mechanical
- How I got here
Electrifying trains and STEMAZING outreach
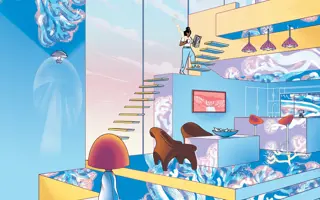
- Civil & structural
- Environment & sustainability
- Issue 95