Additive manufacturing and 3D printing

Dental frameworks. Laser melting is an AM process that uses high-power lasers to fuse together successive thin layers of powdered metal, 0.03 mm thick. The dental frameworks are created from powdered cobalt chrome and when every layer has been built up, the solid copings and dental bridge frameworks are then removed from the machine, sand blasted, polished, inspected and ultrasonically cleaned © Renishaw
It may be some time before every home has its own 3D printer making spare parts for a broken vacuum cleaner, but additive manufacturing and 3D printing are already freeing designers and manufacturers from some of the restrictions imposed by existing production technologies. With excitable media coverage often overstating the current capabilities of additive manufacturing, Ingenia asked Professor Richard Hague, of the University of Nottingham, and Dr Phil Reeves of Econolyst Ltd to describe the present state of the technology, its future potential and the engineering challenges that still need to be overcome.
Hardly a day goes by without a media mention of additive manufacturing or 3D printing and how it will transform industry as we know it. The coverage claims that it will not be long before we all become ‘makers’, designing devices on our computers or ‘downloading’ them over the internet for production on a local printer. In truth, the concept of fabricating products layer by layer has been around for over 25 years within industry, with this method being used to test designs by ‘rapid prototyping’ prior to full-scale production. However, it is only within the last decade that industrial applications have been identified where this layered manufacturing approach can also be used for the production of end-use parts.
AM OR 3D PRINTING?
While some people use these terms interchangeably, they actually represent different ends of a common technological spectrum. Additive manufacturing (AM) is ostensibly an industrial process, undertaken using high capital cost technology, often within an established supply chain, or offered as a managed service by a specialist part supplier. 3D printing, on the other hand, describes the use of more accessible entry-level additive methods used within the home or small business. 3D printing is being widely championed as a way of enabling consumers to play a greater role in the design and manufacture of the products they buy. However, there is an emerging perception that consumer 3D printers have capabilities similar to their industrial big brothers, which is simply not the case at the moment.
These two kinds of manufacturing activity vary significantly in the types and complexity of the machine tools they use. 3D printing relies almost exclusively on building layers using molten polymers, while commercial AM systems typically use an energy source such as a laser or electron beam to fuse polymeric and metallic powders layer by layer. These powder-based processes produce significantly more robust parts and can create complex geometries and designs that are not acheivable by most current home-based extrusion 3D printers.

One way to create a 3D model for AM is to laser scan an existing object. This approach is particularly suited to making replicas of historical artefacts or copying handmade ‘artistic’ products. The laser is used to collect millions of data points representing the product’s surface. The point cloud data can then be reverse-engineered back into the 3D CAD envionment, prior to modifcation and additive manufacture © Econolyst
3D PRINTING
While a 3D printer can cost as little as £200 – though more typically around £1,500 – limitations in the quality of the output have, so far, prevented widespread take-up of the technology. These consumer devices bear little resemblance to their commercial AM counterparts. They can only process a handful of extruded thermoplastic materials, and are limited in the size, resolution, final part integrity and the complexity of the parts that they can produce.
Despite these shortcomings, there may already be as many as 50,000 to 70,000 machines worldwide that are printing applications. These vary from the creative and toy industries, to jewellery, electronics packaging for products such as USB sticks and Raspberry Pi computers, through to simple architectural models.
The machines available to buy for the home predominantly use a spool of plastic filament which is heated then squeezed out of a nozzle – very much like icing a cake in layers – to create objects. Some machines are also able to deposit material from mutiple heads, allowing parts to be made in different colours, or from different materials. These machines are typically capable of making parts the size of a loaf of bread. Newer machines are getting larger, faster and more accurate with a number of higher-resolution resin-based consumer 3D printing machines finding their way to market.
As educational tools, 3D printers are enabling more and more students to design and manufacture devices and products themselves rather than asking the lab technician to make up their models. This early introduction to rapid prototyping and part manufacture provides valuable insight into commercial processes and can help students to appreciate the honing of form and functionality that takes place in successful industrial design.
AM'S POTENTIAL
While the application of technology for end-use part manufacture is still in relative infancy, the potential benefits of additive manufacturing to industry could be profound. Logistically, AM could allow parts to be kept in digital form and manufactured on demand, thus ending the need for large warehouses keeping stock for years awaiting distribution. As the technology can be used to displace fixed assets such as tooling, it could also help support smaller companies entering manufacturing, or make products that would otherwise be prohibitively expensive to manufacture. Perhaps the most revolutionary potential offered by AM technology is the ability to produce designs that would not have been possible using traditonal processes such as casting or machining. These include products with complex internal channels and pathways or with intricate lattices and honeycombs which can replicate some of the strongest materials that occur in nature, such as bone. Useful in the aerospace and automotive industries, AM could enable the weight of structures to be reduced by up to 40%, while improving strength and using significantly less raw material in production.

A MakerBot Replicator and a 3D Systems Cube. Both machines retail for around £1,200 and are capable of producing plastic components in ABS plastic and poly-lactic acid (PLA). The machines are aimed at the consumer market and are being used to print out ‘maker’ projects, prototypes, toys, and gifts downloaded from the internet. The machines would typically take around two to four hours to print out an object the size of a computer mouse © Econolyst
By coupling the design freedoms of AM with cost-effective low-volume production of individual items, the technology is also well-suited to both the manufacture of patient-specific medical devices, such as surgical implants, along with customer specific consumer goods with ever-increasing levels of customisation, complexity and aesthetics.
MYTH BUSTING
There have been a lot of media headlines on the potentially transformative benefits to society of additive manufacturing and 3D printing. However, much of this attention has overstated the current readiness level of the technology. For example, although there are clearly economic and environmental benefits to be exploited within the aerospace sector, there has been very little actual technology adoption to date.
Examples of additive manufacturing have been limited to just a handful of non-structural aerospace parts such as heating and ventilation ducting. However, this should come as no surprise to the engineering community, who understand the time scales and costs associated with the introduction of both new technology and materials.
One of the most extreme claims is that that we will be 3D printing organic body parts within a decade. In reality, additive manufacturing represents just one of a number of enabling technologies that will be used within the regenerative medicine sector. These will allow new ways of building tissue scaffolds and constructs, which would then need to be seeded with cells prior to incubation and growth. This represents decades of work before the arrival of fully-functioning 3D printed organs.
AM IN ACTION
Commercial AM systems are now routinely used to produce economically viable personalised products. They are especially suited to orthopaedics, because CT imaging and MRI result in digital data which can be exported to CAD. AM involves building up layers and so the technologies work well together. Surgeons can take scan data of damaged bone and using proprietary software, in the form of surgical design tools, they are able to create bespoke implants that can then be additive manufactured.
Another role for AM in orthopaedics is as an economic alternative to traditional manufacturing with improved performance properties. AM can be used to manufacture an acetabular cup – the ‘ball’ of a hip joint – which has the necessary porosity to enable bone to fuse to it. In the past this was only achieved by machining a forged part and then applying a ceramic coating. This was the most expensive part of the process in traditional hip joint manufacture and is no longer necessary using AM.
Within the medical sector, AM is also being used as a cost-effective way of producing patient-specific medical devices. One example being the production of in-the-ear (ITE) hearing aids. Traditionally, ITE hearing aids were manufactured by copy-milling a wax or resin impression of the patient’s ear canal - a time-consuming and labour-intensive business. The digital AM approach is to take a wax impression of the patient’s ear canal and then to laser-scan the topology of the impression to digitally reproduce the 3D model. The 3D computer representation of the ear canal is then converted into a structural shell, prior to the automatic inclusion of geometry to allow for internal electronics such as the battery, amplified microphone and speaker. The resulting bespoke product design is then submitted for additive manufacture prior to assembly, testing and dispatch. It is believed that as many as 20 million ITE hearing aids have been produced worldwide using this appoach.

An acetabular cup (the ‘ball’ of a hip joint). Additive manufacturing, using the Arcam electron beam melting process, enables the fabrication of complex, porous, patient-specific implant components. This cup has integrated structures that allow for improved acceptance and development of the living bone and the surface of the load-bearing artificial implant © Econolyst
DESIGNING FROM HOME
Two other areas where AM is being used succesfully are the computer games industry and toy making. Here the technology is being used to turn virtual character designs into physical products.
Computer game players use their interface as a design tool enabling them to create their own avatars. Having realised their character in the virtual world, users can then hit a ‘3D Print’ button that orders their avatar to be made. A commercial AM system will then build their creation remotely, with the finished product delivered to their door, often within days. By letting the gamer design the product, the consumer effectively becomes both the front and back end of a supply chain.
This principle is also found with the MakieLab business concept, launched in 2011. Using match-funding of £100,000 from the Technology Strategy Board, MakieLab developed a dedicated computer interface for both PCs and iPad through which consumers are able to model their own Makieworld characters. Using back-end software tools, the company is able to send AM ‘print’ data to a number of AM service companies for production.
Early success led to an additional million pounds’ worth of funding being raised from venture capitalists last year which has led to an iPad app. This has enabled users, usually girls aged eight and upwards, to create designs on their tablets – 4,500 were created on iPads within two days of its launch in March 2013. Not all of these were made into physical toys, but the buyers are able to play, learn to design and exchange their try-outs.
The local-manufacturing point is important for small AM businesses in Europe. Exploiting the ‘digital supply chain’ benefits of AM, MakieLab currently makes its dolls in London and Amsterdam to sell to the UK and the Netherlands. It has ambitions to widen its manufacturing network as AM facilities become more widely available.
BARRIERS TO TECHNOLOGY ADOPTION
One of the most significant issues in designing for AM is the limitation imposed by existing CAD software traditionally used for creating 3D geometries. CAD was originally developed for conventional manufacturing processes, and has associated design limitations. These systems do not readily or efficiently support the generation of the complex geometries that many AM processes can manufacture.
‘Freeform curves’, shapes that do not follow a predictable mathematical geometry, for example, are difficult to realise in many CAD systems. This has produced the unusual position where the manufacturing process can make significantly more complicated geometries than a conventional CAD package is capable of. Now, a new generation of design software is being developed specifically for AM processes. For example, product-specific 3D packages are now being produced for items such as hearing aids and dental aligners, which can reduce the design time from days to minutes. AM is currently used globally to make 64,000 dental aligner moulds per day, hence the need for completely automated software.
However, the AM process cannot yet make any object from any material. The material to be processed – polymer, metal or ceramic – and the process involved – powder or liquid, laser or jetting – will limit the manufacturing options available. But with the elimination of mould tooling and other conventional techniques, AM does, overall, offer significantly greater design freedom.
SUSTAINABILITY PROS AND CONS
Another advantage presented by a shift to AM is the opportunity to compress the supply chain and allow manufacture at locations nearer to the point of consumption, with obvious potential benefits to the consumer, the local economy and the environment. That said, AM is not necessarily a panacea for sustainability in business, with big differences in the efficiencies of different polymer and metal systems. This is largely due to the energy needed to instigate material melting and due to the lack of recyclability of the current polymer powder-based materials.
Though the potential is there, it is not yet able to call AM an environmental manufacturing technique. The aerospace sector is an obvious example of where there is a clear benefit in moving to lighter components, and where there can be more efficient use of scarce raw materials. In the aerospace industry metal parts are typically machined from a solid billet of titanium or aluminium. With up to 90% of the material cut away, the waste is then no longer suitable for use in aircraft manufacture and is often down-cycled into other lower value supply chains. Titanium powder, on the other hand, can be used to print components as strong as machined parts using a fraction of the raw material, according to researchers at EADS, the European aerospace consortium.
INTELLECTUAL PROPERTY
The emergence of AM raises a number of complex legal issues. As well as manufacture being possible for anyone who has access to CAD versions of a product, many simple items could easily be copied without the need for expensive tooling, enabling the duplication and forgery of designs and brands.
The legal implications are also complex when the responsbility for the safety of 3D printed products is considered. In the event of product malfunction, untangling the cause and responsibilities between designer, printer and additive manufacturer, could be extremely complex. There are also issues around printing illegal items, such as weapons, and how sharing the designs for illegal items, or the printing of illegal items, could be controlled. As for any new area of technology, there may well be challenges while the legal frameworks catch up with the rate of technological change. Debating and developing legislation and regulation at an early stage will be important to make the most of the technologies’ benefits.
FUTURE POTENTIAL
To date, the use of AM has focused mostly on producing single-material, homogeneous structures in polymers, metals and ceramics. In the future, the inherent design flexibility of AM could enable multi-material ‘active’ processes; materials and designs that will ultimately allow the printing of complete systems in one manufacturing operation. For example, AM could ‘print’ electrical circuitry into components as they are built.
Though there remain significant technical challenges, research at the University of Nottingham, within the EPSRC’s Centre for Additive Manufacturing, shows that this approach could be extended to include conductive, optical or even biological circuitry. This would have the potential to unify printed electronics with additive manufacturing. So, instead of simply printing the mobile phone case or hearing aid shell, there would be the opportunity to print the entire mobile phone or hearing aid in a single operation.
Irrespective of the potential benefits, AM remains a nascent approach exploited today by only a small number of early adopters. The AM ‘industry’ – machine tool, materials sales and associated services – was valued at just £1.9 billion in 2011 (Wohlers Report 2012 – the annual worldwide analysis of AM and 3D printing).
The AM sector has, however, enjoyed sustained double-digit growth in recent years, growing by almost 30% in 2011 alone. By 2020, the AM supply chain could be in excess of £80 billion a year, although this will only happen if the industry is able to address the technological limitations that now prevent wider adoption. This will require a concentrated focus on improving process control and material validation, production economics, size limitations, accuracy and process repeatability.
For more information about AM and 3D printing visit www.econolyst.co.uk and www.nottingham.ac.uk/3dprg
For examples of 3D printing see www.thingiverse.com
The Royal Academy of Engineering held a 3D printing workshop in May 2013. See the results of the roundtable at www.raeng.org.uk
Keep up-to-date with Ingenia for free
SubscribeOther content from Ingenia
Quick read
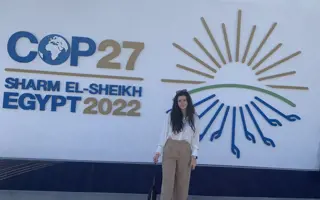
- Environment & sustainability
- Opinion
A young engineer’s perspective on the good, the bad and the ugly of COP27
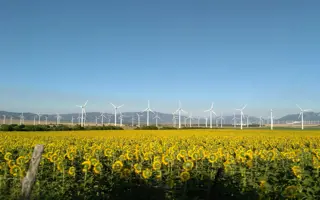
- Environment & sustainability
- Issue 95
How do we pay for net zero technologies?
Quick read
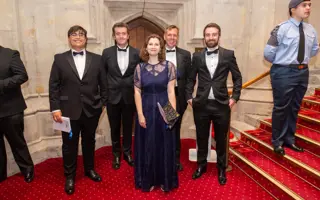
- Transport
- Mechanical
- How I got here
Electrifying trains and STEMAZING outreach
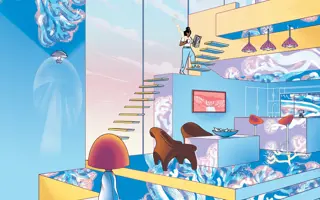
- Civil & structural
- Environment & sustainability
- Issue 95