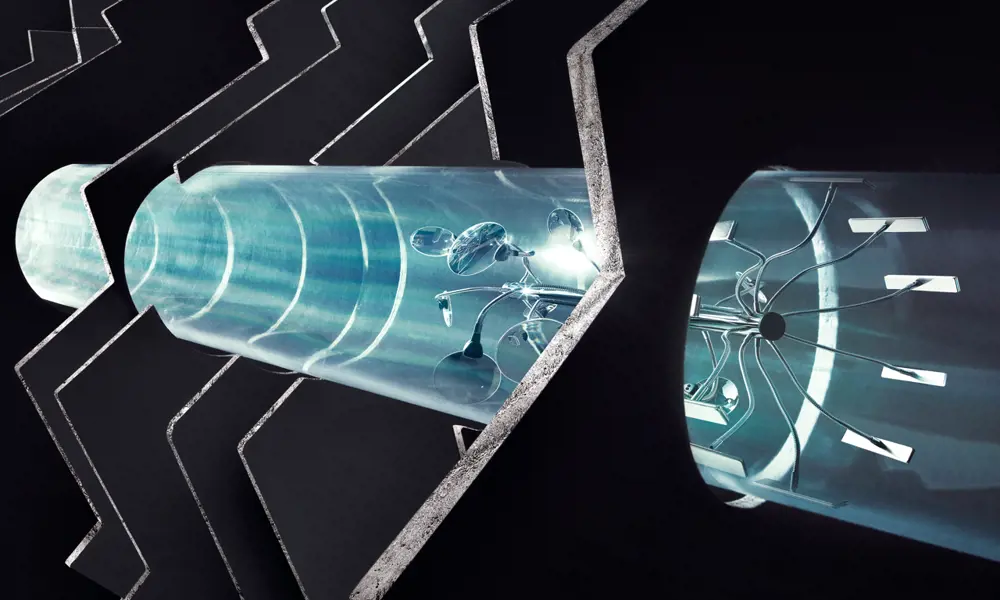
Adding value through maintenance
Did you know?
🛠️ The importance of preventative maintenance
- System failures result in reduced profitability, but can also cause disruptions to services and sometimes have more serious impacts
- Preventive maintenance can help to avoid or minimise such disruptions before a system fails
- Various technologies are being employed in combination to support this approach and deliver successful maintenance strategies
No component in any system lasts forever. For example, in a radio the components include resistors, transistors, capacitors, inductors, integrated circuits, and more – all of which are built to last several years and when any of these fail, the radio will more than likely stop working. On a bigger scale, such as in transport and other infrastructure, the knock-on effects of a failed component can cause a wider system failure that results in lost productivity and income at best. At worst, failures in safety critical industries can lead to injuries and fatalities to the workforce or the general public. Maintenance engineering brings together a growing suite of technologies to ensure that the systems that we rely on operate safely and at an acceptable cost. And those costs can be high. For example, organising maintenance to ensure a safe and reliable railway network is a massive and costly undertaking. In 2019/20 Network Rail spent more than £1.7 million on maintenance.
Other major engineering industries, such as aviation, nuclear power, and offshore oil and gas production, also spend staggering amounts to keep their infrastructure operating safely and reliably. For example, nearly a third of the total expenditure of Severn Trent, one of the largest regulated water and sewage companies in England and Wales, goes into maintaining reservoirs, treatment works, pumping stations, and pipes.
Maintenance engineering brings together a growing suite of technologies to ensure that the systems that we rely on operate safely and at an acceptable cost. And those costs can be high.
Poorly performed or ineffective maintenance can also prove costly in other ways, sometimes contributing to accidents. In aviation, about 12% of aircraft accidents cite maintenance as a factor. Public inquiries showed that poor maintenance played a part in train derailments at Hatfield in 2000 and Potters Bar in 2002, both resulting in fatalities. The Hatfield accident, caused by cracked rails, might not have happened had engineers maintained the rails following the appropriate comprehensive procedures. A Health and Safety Executive report into the Potters Bar accident indicated that bolts in a poorly maintained set of points had come loose causing the derailment.
For many years, maintenance was simplistically viewed as a responsive process, fixing components as and when they failed. Today, there is better understanding of maintenance’s impact on costs and profitability. Most industries now try to avoid, or minimise, system failures by moving from responsive, ‘fail and fix’ maintenance to a more sophisticated ‘predict and prevent’ approach. This approach taps into broader advances in engineering, such as artificial intelligence (AI) and data management, to analyse and control the state of the components in a system and to understand how to optimise the processes involved in supporting systems and devices in service and operation.
Prevention before failure
Preventive maintenance aims to replace components as they approach the end of their expected useful life – the closer the replacement is to the end of its life, the more efficient the process – to avoid the cost and inconvenience of breakdowns in service. Determining when to replace a component is a delicate compromise between its discarded life, the risk of system failure, and choosing the most convenient and least disruptive time to perform the work – closing a system for maintenance incurs costs for spares, equipment and workforce labour, and also impacts on the system’s ability to generate revenue. However, without this preventive maintenance, there could be more system failures and breakdowns that incur maintenance costs and lost revenue – which could be passed on to the general public through an increase in rail ticket fares, for example.
Determining when to replace a component is a delicate compromise between its discarded life, the risk of system failure, and choosing the most convenient and least disruptive time to perform the work
Using this approach gives engineers early warning of likely failures and dictates the type and frequency of the maintenance that they should carry out. Such strategies can determine the state of the system or structure, control its rate of deterioration and remove components before they fail. It will also define when maintenance will become ineffective and, for example, the system gets to a point where maintenance provides little improvement.
Engineers may also choose to carry out opportunistic maintenance: when a system is taken out of service for maintenance, they may take the opportunity to work on several parts of it. While one component could be degraded, other parts may not have reached the point that would normally need work, but early maintenance can prevent having to take the system out of service again when another part fails. This approach also proves to be cost-effective when specialist equipment is available for work on similar components, avoiding the need for the same specialist equipment in future.
Monitoring before maintenance
Manual inspection or some sort of monitoring of the system and its components is an essential element of maintenance. Inspection establishes the components’ condition and is used to decide interventions. For many, manual inspection guides when to do maintenance and what should be done; while for others, monitoring a key performance characteristic, such as vibration, can establish the system’s condition and how close it is to failure, issuing alerts when the system reaches specified levels of degradation.
Most of us are familiar with this strategy in the shape of the annual car service, which follows a checklist of things to examine – tyres, brakes and exhaust, for example. However, many car-makers are moving away from this rules-based scheduled check-up in favour of predictive maintenance. BMW Group, for example, makes increasing use of sensors, data analytics and AI as an alternative to the annual health check, to forecast when a car needs maintenance, when it is time to replace components and when premature replacement would be wasteful.
In the UK alone, Network Rail is responsible for about 30,000 bridges while National Highways is responsible for maintaining around another 9,400.
BMW also employs the same predictive maintenance approach to its production lines. In bodyshops, for example, it has welding guns performing 15,000 spotwelds a day. Welding guns around the world feed their data into a cloud-based computer system, where algorithms analyse what is going on and display the output on a dashboard to support the maintenance processes. A similar data-fed approach is also a part of the maintenance regime at BMW Group Plant Regensburg, where control units on conveyor systems send real-time data on electrical currents, temperatures and locations to the cloud. Again, predictive AI models analyse the data, detect anomalies and locate technical problems.
Manual inspection can be difficult when trying to monitor systems that are distant, difficult to reach or dangerous. In these cases, sensors can monitor an asset and report back on its performance to a data hub to establish the need for maintenance. The number of bridges worldwide is an obvious example of where remote condition monitoring could deliver significant benefits. In the UK alone, Network Rail is responsible for about 30,000 bridges while National Highways is responsible for maintaining around another 9,400. Sending engineers to inspect bridges is time-consuming and expensive; fortunately, research is making rapid advances in monitoring bridges and interpreting the data to establish management needs.
Effective decision making needs data-driven insights
The key to effective decision-making on maintenance of any asset is to understand how it deteriorates with use. For this, data is needed, an area that has benefited from the availability of cheap sensors and the ability to collect, store and process large quantities of data.
Industry makes increasing use of data-driven approaches to maintenance. A prime example is Rolls-Royce, which has many years of experience in collecting data from its fleet of aeroengines, and what it dubs the IntelligentEngine approach. The company’s engineers use advanced data analytics, AI and machine learning to manage the maintenance of aeroengines and monitor their health. This process can generate some 70 trillion data points each year. The benefits are substantial: as well as providing knowledge of when an aircraft might fail if it doesn’t receive maintenance, the data also feeds into engine design and operational fuel efficiency.
Omnicom Balfour Beatty and the University of York have developed computer software that uses AI and machine learning to digitise the inspection of railway lines. A camera on the front of train moves along rail tracks in need of inspection using machine vision to capture high-definition images of the rail track. The data is then transferred to a system that analyses it to highlight inaccuracies and faults on the tracks.
Rolls-Royce has also adopted robot technology in its Intelligent Engine concept for engine maintenance. This combines robotics and digital technologies to speed up inspection and to remove the need to take an engine off an aircraft for maintenance. One concept that Rolls-Royce is working on with researchers from Harvard University and the University of Nottingham is that small 'swarm' robots would crawl through an engine to visually inspect hard to reach areas. To learn more about swarm robots, visit 'engineering swarm robotics' in Issue 97. Another possibility is to permanently embed a network of ‘periscope’ cameras in an engine so that it could inspect itself and report any maintenance requirements
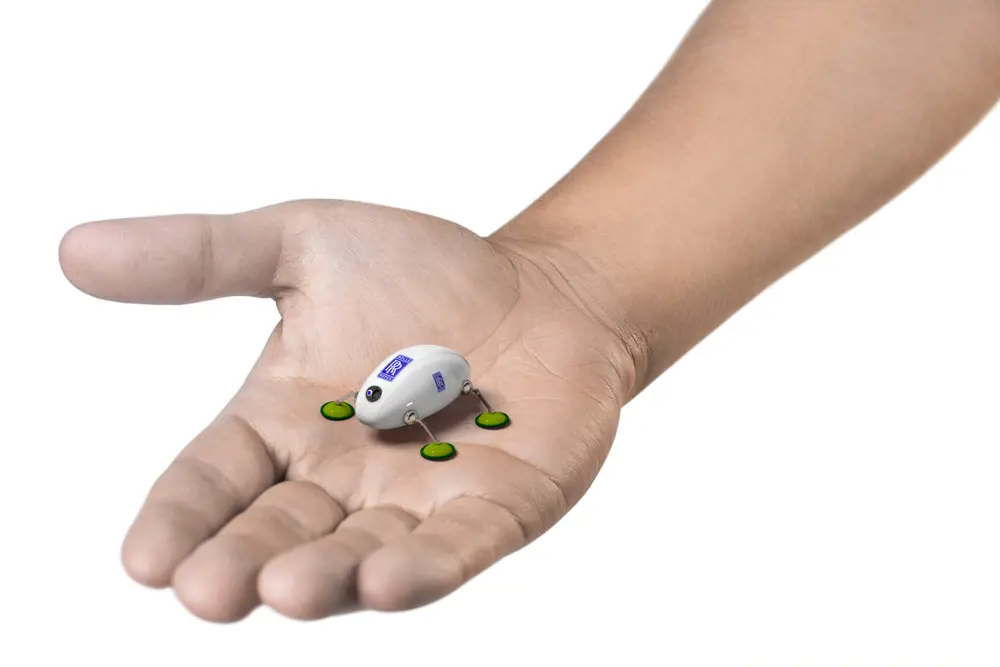
Rolls-Royce 'swarm' robot that would be used to access hard to reach or remote areas © Rolls-Royce
With knowledge of degradation trends, maintenance engineers can formulate mathematical models to predict a maintenance strategy’s performance. Models can predict the future state of an asset and how many times each maintenance activity will be performed. From this, engineers can estimate a strategy’s expected cost. Once formulated as a model, this approach can be embedded into an optimisation framework to minimise lifecycle costs and maximise an asset’s future condition. The more sophisticated approaches can also take account of uncertainties and make the selected strategy robust to changes in the system’s future and the costs of the maintenance resources such as spares and labour.
One challenge is that each bridge spans a unique obstacle: a road, river or railway line for example. One size doesn’t fit all when it comes to the analysis strategy. For some critical structures, sensors can measure movement and vibration. However, the large numbers involved means that installing sensors on all bridges, like performing manual inspections, is expensive. Researchers are tackling this challenge by putting sensors on vehicles that pass over bridges. In this way, vehicles can monitor the condition of structures as they travel over them, providing a substantially simpler and cheaper way to establish a bridge’s condition.
In some systems, an alternative to embedded sensors is for autonomous systems to remotely monitor assets. The petroleum industry has used uncrewed aerial of both the operational and maintenance periods.
Rectifying random failures in aviation and the military
System failures can be inconvenient and expensive – and sometimes components cannot be fixed or replaced beforehand. However, engineers are using innovative approaches in some areas to control when to take the system out of service for maintenance. One example is in aviation, where any need for repair can result in cancelled flights and stranded passengers. An aircraft may also be a long way from a maintenance hub, making the logistics of repair challenging and costly. In this situation, it would be preferable to continue with the flight, deliver passengers to their destination and perform maintenance at the operator’s own base. This need was met by full authority digital engine control (FADEC) systems, which were introduced to commercial aircraft to control all aspects of their engine performance.
When first used, FADEC systems took a conservative approach to the fault conditions under which aircraft could not fly. The system was more reliable than its predecessors, but delays and cancellations increased.
This was solved by time-limited dispatch, which allows aircraft to fly for a defined period of flying hours with certain known faults present in the engine control systems based on FADEC‘s high reliability and redundancy features. This is restricted to a limited number of flying hours, known as the dispatch period. When that period has passed, the fault must be rectified before further flights. This gives a window during which the aircraft can be taken out of service, at a convenient time and at a preferred location, to avoid disruptions to the service and high repair costs. To ensure safety, the dispatch period is set to ensure an acceptably small likelihood of other failures. Depending on the fault, a short or long time period is set, after which the fault has to have been corrected or the aircraft is grounded.
This was solved by time-limited dispatch, which allows aircraft to fly for a defined period of flying hours with certain known faults present in the engine control systems based on FADEC‘s high reliability and redundancy features.
Another innovative approach devised to address problems associated with the randomness at which component failures occur, uses maintenance-free operating periods (MFOP). Random failures hamper the planning of both the operational and maintenance periods. More certain knowledge of these two periods would benefit any industry but they have added significance in the military, where it is impossible to plan missions in detail, if the number and types of platforms, for example tanks, aircrafts, ships, or UAVs, are uncertain.
The UK’s Ministry of Defence put forward an idea that led to the concept of MFOPs in the 1990s. During this period, equipment can usually carry out missions without maintenance and without system faults or limitations restricting the operator in any way. Following each MFOP, during time known as a maintenance recovery period, equipment is maintained to a level so it can perform until the next MFOP. This means that forces can plan military missions with confidence that the equipment they needs will be available. They will also know in advance what maintenance resources will be needed and at what time.
To implement this strategy, the system must be designed to account for the need to carry some faults for the rest of the current MFOP. The system will need to tolerate these faults so that they won’t require immediate maintenance, which will need higher levels of redundancy (duplication of components so that if one fails the others will continue to work and allow the system to function – such as engines on an aircraft). This is one reason why this strategy has not been adopted for military aircraft where added redundancy would increase weight and reduce performance. However, while this approach has limitations as far as military aircraft are concerned, there are many other applications where MFOP proves beneficial, such as ships and submarines, where limited maintenance can be undertaken during a voyage.
Using robots and researching the most effective strategies
The quality of maintenance depends on the skills and ability of the engineer performing the work, the degree of repetition and boredom involved, and how long it takes to complete. This type of activity is where robots can deliver better performance and precision than human counterparts. Consequently, robots are increasingly employed in maintenance work.
Beyond fulfilling tedious tasks and improving accuracy, robots can carry out maintenance in dangerous environments. For example, nuclear power plants are clearly hazardous environments where robots can perform inspection and maintenance while avoiding human exposure to radioactivity. For example, the JET fusion facility at Culham recently announced new records for fusion after robot handling systems completed a refit of the radioactive tokamak device.
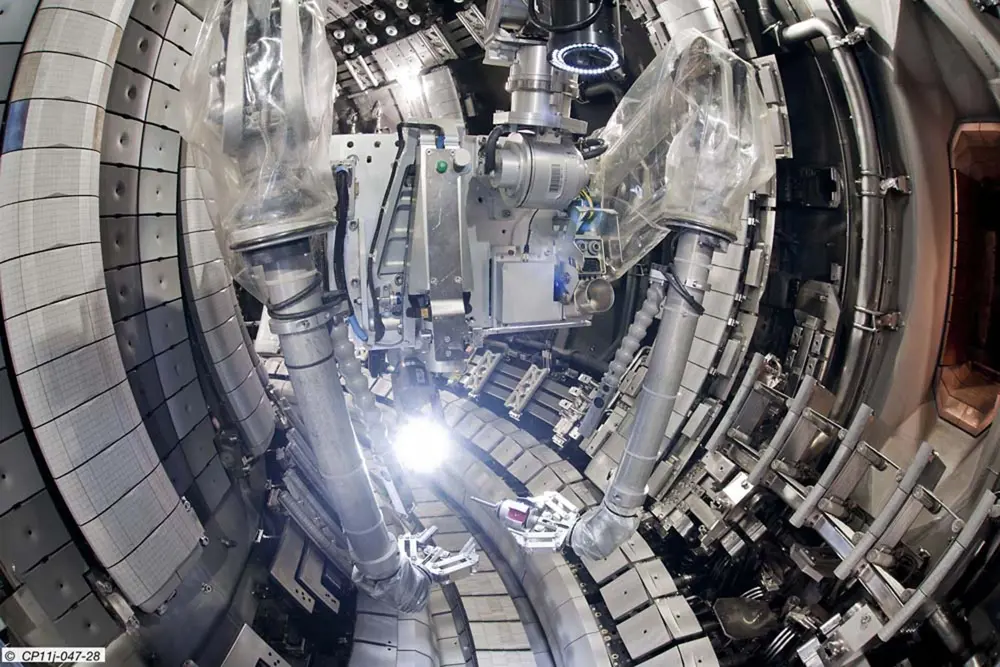
When the Joint European Torus (JET) recently set a new record for power output in fusion research, it did so after a maintenance and upgrade campaign that relied on robots. Since 1991, JET has conducted a series of experiments with deuterium-tritium (DT), the mixture of hydrogen isotopes that will fuel commercial fusion power plants. DT fusion creates neutrons that make the inner parts of JET radioactive. Only robots can safely enter the main chamber for maintenance operations © EUROfusion
And effective approaches to maintenance depend on using the best combination of techniques. Maintenance strategies are themselves the subject of research. At the University of Nottingham, for example, the Resilience Engineering Research Group has developed mathematical and statistical methods to support decisions of what maintenance to do and when to do it. Statistical and AI methods allow engineers to understand how a component’s condition will degrade with use, which can then integrate into a maintenance strategy that specifies how to respond to different levels of degradation.
Maintenance engineering has made considerable advances over the past two decades. Sensor technology, remote sensing, big data initiatives, AI, robotics, and system autonomy are multidisciplinary areas that have contributed to the maintenance revolution. These are also areas where research continues to make rapid progress, promising a bright future for the maintenance discipline. These new capabilities will deliver solutions to the new demands and opportunities that evolve from the wider technological advancements and the rising demands for maintenance.
***
This article has been adapted from "Adding value through maintenance", which originally appeared in the print edition of Ingenia 91 (June 2022).
Contributors
Professor John Andrews is the Head of the Resilience Engineering Research Group at the University of Nottingham where he was appointed to a Royal Academy of Engineering Research Chair in Infrastructure Asset Management. His research is focused on the development of mathematical models to predict system risk, resilience and failure likelihood, enabling the evaluation of alternative designs and maintenance regimes.
Keep up-to-date with Ingenia for free
SubscribeRelated content
Technology & robotics

When will cars drive themselves?
There are many claims made about the progress of autonomous vehicles and their imminent arrival on UK roads. What progress has been made and how have measures that have already been implemented increased automation?

Autonomous systems
The Royal Academy of Engineering hosted an event on Innovation in Autonomous Systems, focusing on the potential of autonomous systems to transform industry and business and the evolving relationship between people and technology.

Hydroacoustics
Useful for scientists, search and rescue operations and military forces, the size, range and orientation of an object underneath the surface of the sea can be determined by active and passive sonar devices. Find out how they are used to generate information about underwater objects.

Instilling robots with lifelong learning
In the basement of an ageing red-brick Oxford college, a team of engineers is changing the shape of robot autonomy. Professor Paul Newman FREng explained to Michael Kenward how he came to lead the Oxford Mobile Robotics Group and why the time is right for a revolution in autonomous technologies.
Other content from Ingenia
Quick read
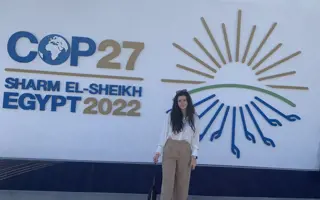
- Environment & sustainability
- Opinion
A young engineer’s perspective on the good, the bad and the ugly of COP27
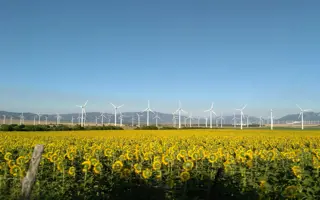
- Environment & sustainability
- Issue 95
How do we pay for net zero technologies?
Quick read
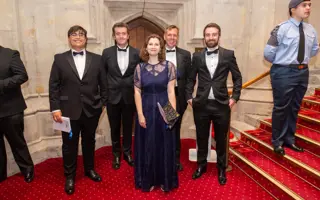
- Transport
- Mechanical
- How I got here
Electrifying trains and STEMAZING outreach
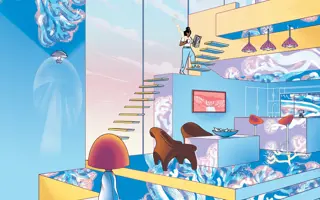
- Civil & structural
- Environment & sustainability
- Issue 95