Accessing the UK's subsea assets
Far from being yesterday’s industry, North Sea oil and gas remains an important part of the UK’s economy. Allen Leatt FREng, Senior Vice President Engineering at Subsea 7, explains how new production technologies and underwater installation and maintenance techniques are reversing the decline in production, making it possible to recover reserves from previously uneconomic fields.

A 7km pipeline bundle is towed from its fabrication site at Wick, Scotland. The bundle integrates the required oil and gas, water injection and gas lift flow lines with the control system for a subsea development, and assembles them within a steel outer carrier-pipe. Two powerful leading tugs will tow the bundle with a tug at the rear supporting the tailend. A guard boat will lead the convoy, accompanied by a survey vessel for checking the bundle en route to its subsea destination, typically 200-300 km away © Subsea 7
The UK became self-sufficient in oil production in 1980 and remained so for the next quarter of a century. Oil production from the UK continental shelf peaked in 1999 at 137 million tonnes, some 2.75 million barrels per day, and has been generally in decline ever since. By 2012, oil production had declined to 45 million tonnes, a third of its peak. Natural gas has exhibited a similar decline in production.
It is, however, far too soon to be writing obituaries for oil and gas production in the UK. The North Sea is enjoying record activity, with production set to rise again. This turnaround, fuelled in part by the rising price of oil and gas, owes much to the emergence of techniques for oil and gas recovery and new approaches to the maintenance of seabed production facilities.
Technological advances in the SURF market (subsea umbilicals, risers and flowlines) and the IRM market (inspection, repair and maintenance) have helped operators to exploit the smaller and more difficult reservoirs. These advances have also created export opportunities as offshore operators around the world adopt these engineering innovations. This new technology has been particularly relevant in deeper waters of up to 3km, such as those off West Africa, Brazil, and in the US Gulf of Mexico.
SUBSEA COMPONENTS

A subsea control umbilical being loaded into a large storage carousel located within the cargo hold of an offshore construction vessel. These specialist ships are able to automatically load umbilicals, many kilometres in length and several thousand tonnes in weight, at the quayside and accurately lay them on the seabed offshore. Remotely operated vehicles or divers then connect them to production hardware on the seabed
PIPELAYING METHODS
The pipelaying vessel lowers the pipelines onto the seafloor in a continuous process through a series of tensioners that grip and squeeze the outside of the pipes, holding the full weight of the line in the water column as it is laid. The scale of equipment for this efficient process is large for ultra-deep water, with top-tension capacities of 500 tonnes or more. There are several competing techniques for installing rigid steel flowlines.

A reelship laying a flowline at sea. When loaded onshore, the flowline is plastically strained as it is spooled on the reel. When offshore, the process is reversed and the flowline passes through a three-point straightener before being laid via tensioners positioned on a variable-angle ramp. The technology is extremely efficient for the relatively short flowlines used in the hub-and-spoke architecture in the North Sea SURF market © Subsea 7
The early development of the North Sea required large-diameter (about a metre) ‘trunklines’ for transporting oil and gas several hundred kilometres ashore. The overwhelming need today is for infield and intrafield flowlines. Two methods involve welding pipe joints together onshore (reel-lay and bundles) and then taking them offshore. Two other processes (S-lay and J-lay) involve welding the pipe joints together offshore.
The reel-lay method uses large purpose-built ships to spool pre-welded pipe onto a large reel, typically 3,000 tonnes, and fitted mid-ships. The vessel then travels offshore and reverses the technique to unspool the flowline onto the seabed. The reeling process plastically deforms the pipe, within predetermined limits, and the pipe is straightened again as part of the laying process. This fast technique reduces the need to wait for a favourable weather-window offshore. Onshore welding also helps take the weather out of the picture and reduces the operating cost of laying pipe offshore.
The bundle method is another land-based fabrication method. Multiple flowlines are preassembled inside a large outer carrier pipe, typically 1 m to 1.5 m in diameter. The whole assembly, often 5 km - 7 km long, is then towed off the beach to the North Sea location using what is called the controlled depth tow method (CDTM). The technology has been developed to a high degree over many years and the process has established a strong niche in the market.
INTERVENTION ALTERNATIVES
The UK was a pioneer in the commercialisation of deep-water saturation diving techniques, as well as in the evolution and development of equipment to make it safe and efficient. There is still strong demand for deep diving in the UK, and an active market for state-of-the-art diving support vessels (DSV). A DSV today will be dynamically positioned with two diving bells for round-the-clock diving. The diving bell will usually hold three divers, two of whom will ‘lock-out’ and go to work, while the third stays in the bell as a safety stand-by diver. The processes today are highly optimised, with large saturation diving chambers and life support systems.
In deeper water, beyond, say, 250m, remotely operated vehicles (ROVs) are the sole commercially viable intervention technology on a large scale. The work-class ROV is an electro-hydraulically powered (100-200kW) underwater flying vehicle, approximately the size of a small car, equipped with an array of cameras and remotely controlled manipulators and tooling systems for conducting construction and intervention tasks. An umbilical links the vehicle-to-surface power and control facilities on the vessel, where pilots and technicians drive and manoeuvre the vehicle remotely.
BIOGRAPHY
Allen Leatt FREng is Senior Vice President Engineering at Subsea 7, based in London. He was closely involved in early formation of what is now known as the subsea industry, and has held senior management positions with industry-leading organisations. He has worked internationally in both the construction and manufacturing sectors of the industry.
Keep up-to-date with Ingenia for free
SubscribeOther content from Ingenia
Quick read
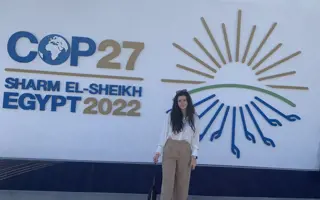
- Environment & sustainability
- Opinion
A young engineer’s perspective on the good, the bad and the ugly of COP27
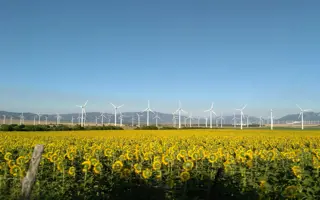
- Environment & sustainability
- Issue 95
How do we pay for net zero technologies?
Quick read
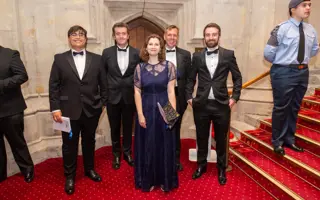
- Transport
- Mechanical
- How I got here
Electrifying trains and STEMAZING outreach
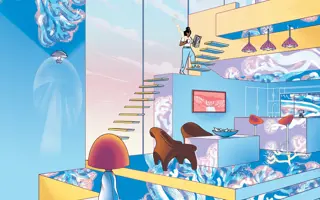
- Civil & structural
- Environment & sustainability
- Issue 95