A skyline air bridge
Simplicity requires greater imagination in the modern world of advanced technologies. The air bridge at London Gatwick Airport satisfies the requirements of the airport, the aircraft and the passengers in a simple but very distinctive way. It is the combination of these requirements that determined its shape and the ambitious manner in which it was built.
Many travellers through Gatwick Airport will soon have the unique experience of walking over aircraft as they taxi to and from the terminal. The Gatwick air bridge was part of a novel solution to the challenge that BAA faced when it set out to increase the capacity of the North Terminal at Gatwick Airport. It is the first bridge over a taxiway to be built outside the USA, and caters for much larger aircraft than the only previous air bridge of its type in Denver, Colorado. What makes it truly unique in engineering terms, however, is its scale and the way it was built.
The air bridge concept
The air bridge is a key component of the new 11-aircraft stand building, Pier 6, at the North Terminal of London Gatwick Airport. This development – the largest at Gatwick since the North Terminal opened in 1988 – will increase terminal capacity and quality of service to both airlines and passengers without the need for the compulsory purchase of adjoining land, which could leave long-term scars on both the environment and the local community.
The BAA team at London Gatwick Airport envisaged from the very outset that terminal expansion could be achieved through a remote satellite terminal pier built in an area previously used as aircraft parking stands; in simple terms, an island solution. The way to link this island to the main North Terminal was long debated and, having evaluated the two main options – above the aircraft taxiway or underneath it – the team chose an air bridge (Figure 1).
Airport, aircraft and passengers
Environmentally, the air bridge was a better solution than a tunnel, which would have meant disposing of 81 000 tonnes of earth. Equally important, the BAA team wanted to give passengers the truly unique experience of crossing one of Gatwick’s busiest taxiways above the taxiing aircraft with panoramic views of the whole airport. The project design brief for the air-link was completed by the addition of two other major requirements; it should have landmark status for the airport, and its construction should have the absolute minimum impact on airport operations.
From the early stages of the project, the overall size and shape of the air bridge was dictated by the need to provide sufficient clearance to the largest aircraft in use at Gatwick Airport, the Boeing 747-400 (Figure 2), and to maintain the lowest overall height so that obstructions to the airport’s ground radar were minimised. Hence, bridge types that involved masts or tall piers were eliminated.
Realisation of the design
A dedicated design team was charged with the realisation of the design brief. Architecture played a major part in the engineering, and vice versa, the form and shape of the air bridge being dictated by the engineering needs of both its assembly and completed state.
The 198 m long air bridge is fully enclosed, providing the pedestrian and buggy link between the North Terminal and the new island pier. Since all services are within the enclosure, external maintenance requirements are minimised. The bridge terminates at both ends in vertical circulation cores containing lifts, stairs and services routes. Escalators provide a direct link between the bridge and the arrivals and departures levels at both ends.
During assembly the deck was a simply supported beam, and the whole completed bridge is a continuous frame fixed on piled foundations. The main structure, made entirely from high strength steel, consists of two basic elements: a 198 m long spine beam which supports the deck, and a pair of Y-shaped 22 m tall supporting columns above the taxiway (Figure 3).
The spine beam comprises a triangular plated box of a constant 2.5 m depth as its bottom element, and a variable depth triangulated space truss in the form of inverted pyramids as its top element, visible to the passengers. With a total depth varying from 6.0 m to 9.3 m on a subtle curve, the resulting shape emulates a real bending moment diagram. The gentle vertical curve of the structure was then transposed to the cladding and to the interior.
The two Y-shaped columns are placed symmetrically about the centre of the taxiway and the bridge, the 128 m spacing between them allowing for future taxiway widening. The shape of the columns increases the effectiveness of the main beam by reducing its effective structural span. In cross-section the columns form an Ashape to provide the required strength to the deck in the direction of major loads such as wind.
The detailed design used a 3-D skeletal model of the complete bridge and 2-D plate element models of key connections (Figure 4).
The passenger experience
In creating the passenger tube, the concept of the human spine and ribs was adopted. The spine beam is positioned centrally in the floor along the length of the bridge and so provides the required physical segregation for departing and arriving passengers. It supports the floor and roof rib beams which carry the floor and the external skin of the bridge. The tube is completed by struts between roof and floor ribs supporting the full-height glazed façade. This is inclined inwards by 11° from the constant width roof towards the floor, thus creating a curved deck floor that narrows at the mid-span (Figure 5).
The only vertical planar surface inside the bridge is a segregational glass screen placed in the middle of the inverted truss pyramids at the spine, together with a high-level bulkhead concealing the ductwork. The continuously varying and curved form is what makes the inside of the bridge such a dynamic and interesting space to experience. Lines are elegantly smooth curves and the vertical space at mid-span almost reaches cathedral dimensions. It is the combination of the gently curved planes forming the space that gives the pedestrian the feeling that the bridge moves along with him, whilst underneath it is the aircraft that are evidently on the move. Four 61 m long auto-walks are provided, with a convenient gap of 10 m at mid-span for those who wish to pursue some serious plane-spotting.
Specification and maintenance
The elements and materials that were used in the air bridge were very carefully selected both for quality and type. The needs of the airport, in terms of standardisation and maintenance; those of the aircraft, in terms of safety; and those of the passengers, in terms of an exciting and distinctive environment, were just a few of the drivers in the selection process.
Although the air bridge appears to consist almost entirely of curved planes and lines, the individual elements forming them are planar or straight – standard components that not only give a cost-efficient solution to start with but can also be efficiently maintained in the future.
How it was built
The delivery on site was by a single team for the whole of the Pier 6 project.
Airports are extremely busy environments, even at night when the runways are shut. To build anything above a taxiway without disrupting airport operations requires both a high degree of planning and technology and the collective contribution of many individuals and organisations, especially when it involves the construction of a 2000-tonne structure complete with all its internal and external glazing.
The principle behind the air bridge was simple: design it, build it, move it and then erect it. Rarely is this scale of prefabrication seen outside the offshore industry, and certainly it was a pioneering process for a UK airport environment – a sequence that could not possibly have been executed without modern techniques in heavy moving and lifting equipment.
The key to success in projects of this sort is that the build/move/erect process is known in advance, so that risks are designed out and coordination with all the other activities of a modern airport is organised in advance.
Safety
Inevitably there are risks associated with this process. These range from simple accidents to complicated scenarios where delayed flights from other continents could require last-minute alterations to the timings of moving the prefabricated bridge across a live taxiway.
An Operational Safety Case encompassed the whole design and delivery process and its implementation was ensured through a very rigorous quality assurance process. All the perceived risks were meticulously assessed and mitigation measures were prepared and ready for implementation with both backup equipment and resources on standby.
Build
The build employed traditional techniques and took place 1.5 km from the airport in a yard specially equipped with all the necessary infrastructure (Figure 6). The air bridge was built in five component parts: the 164 m long central deck section, the two Y-shaped columns and the two 17 m long end deck sections that were to be erected last and connect the bridge with the cores.
The challenge was to ensure that these five components would fit together geometrically when brought into their final position. Fit-up is influenced – especially for steel structures – by the quality procedures during build, by the weather conditions, and by the way prefabricated structures are handled. Problems with fit-up could have caused major disruption to airport operations, so the quality assurance procedures were paramount for the successful implementation of the next two phases. These included testing all the equipment under more severe conditions than those expected at a later stage.
Move
Placing a 2000-tonne structure on wheels and moving it is an ambitious undertaking, but when that structure is fully glazed and therefore more sensitive to movement variations, it becomes even more of a challenge. The answer lay in the design of the air bridge and its components, and the technology of controlling movements.
A self-propelled modular transporter (SPMT) was used, the basic principle of which is: add any number of units together to give the required load capacity and the wheels will share the load equally and move it as a unit with precision (Figure 7).
Two beams, 128 m apart, supported the 164 m section of the air bridge at this stage. Two groups of ten transporter units supported these beams and the lifting towers: 2400 tonnes in total. At that stage the air bridge was a simply-supported structure with the bending moment diagram echoed in the curved roof profile.
The electronic controls of the electro-hydraulic steering system, and suspension of the 240 pairs of rubber-tyred wheels, ensured that the terrain imperfections along the 1.5 km travel distance could be minimised while keeping the cargo level.
The move of the air bridge was a spectacular overnight event, particularly for the pilots of the planes using the taxiway just before and after the bridge crossed it (Figure 8). The gentle roar of the SPMT power units, and the single driver controlling all the moves remotely, were the only evidence of the enormous technological achievements of this unique project.
Erect
At a stately 0.5 km/h, the cargo reached its destination on time. With great accuracy the transporters rotated the whole assembly by 360°, and manoeuvred and placed it exactly above its permanent foundations (Figure 9).
The weight was then transferred from the transporters to the lifting towers, thanks to the ability of the transporters to lift and lower their bed by ±300 mm. At this stage the scene was set, with the pair of 36 m tall lifting towers holding the bridge on the two transfer beams by strand jacks. The bridge was then lifted 24.5 m above the taxiway, some 2.5 m above its final soffit level, in a matter of a few hours by remote electronic control of the hydraulically operated strand jacks.
In the meantime the transporters had gone back to the yard and returned with the pair of Y-shaped columns (Figure 10). These were driven underneath the air bridge, and by simultaneously lowering the bridge and raising the transporters’ platform, the tops of the columns were connected to the bridge deck via specially designed pin connections. This was one of the most critical milestones, since the connections were designed to accommodate a tolerance of only 5 mm – a testament to the equipment’s accuracy and manoeuvrability, and a triumph for technology.
The air bridge had taken shape – effectively hanging by the lifting towers. The 164 m long central part, together with the two Y-shaped columns, were lowered onto specially prepared foundations to enable the connection with the ground to take place and give a fully stable and safe structure.
After 10 days in total, the taxiway reopened and the aircraft pilots and passengers were able to experience the uniqueness of taxiing underneath a structure (Figure 11).
Further lifting operations took place to erect the two 17 m long end spans to complete the bridge and connect it to the adjacent buildings (Figure 12).
Conclusion
The air bridge is an architectural statement of engineering, or an engineering statement of architecture, whichever way you want to see it. In my view it is a clear example of the two disciplines working in harmony. The main curve of the deck, related to a simple bending moment diagram, will always be an elegant reminder of how it was built. Whether this air bridge is classified as a ‘bridge’ or as a ‘building on two columns’ is something that will almost certainly be debated by those who will use it. It opens to the public in the early part of 2005.
Four 61 m long autowalks are provided, with a convenient gap of 10 m at mid-span for those who wish to pursue some serious plane-spotting.
Acknowledgements
The author would like to acknowledge the contributions of colleagues from a number of organisations, namely from BAA, MACE, Watson Steel and WilkinsonEyre Architects, as well as the full Arup team involved in this project.
Stephanos Samaras
Associate Director, ARUP
Stephanos Samaras is an Associate Director of Arup and specialises in design realisation, having led design teams for a variety of challenging infrastructure projects. An Imperial College graduate, he is a Chartered Structural Engineer and a member of IStructE.
Keep up-to-date with Ingenia for free
SubscribeOther content from Ingenia
Quick read
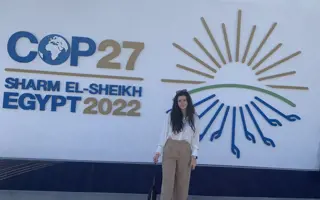
- Environment & sustainability
- Opinion
A young engineer’s perspective on the good, the bad and the ugly of COP27
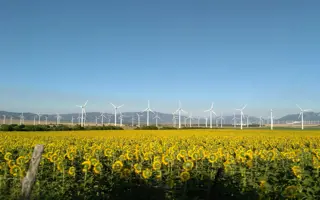
- Environment & sustainability
- Issue 95
How do we pay for net zero technologies?
Quick read
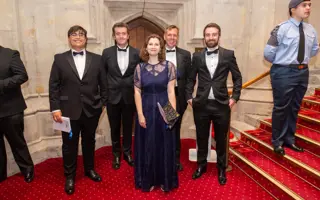
- Transport
- Mechanical
- How I got here
Electrifying trains and STEMAZING outreach
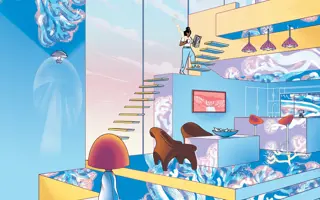
- Civil & structural
- Environment & sustainability
- Issue 95