A Flexible Jet Fighter
The inherently conflicting requirements of high speed, range, manoevrability, payload and short take-off and vertical landing have been optimised in the world’s largest fighter aircraft programme. Neil Mehta of Rolls-Royce, who is Programme Executive for the Joint Strike Fighter LiftSystem® writes for Ingenia about the engineering challenges involved in producing a propulsion system for the F-35 series of planes.

Computational fluid dynamic 3D model of airflow trails
Half a century ago, a new aviation era was sparked into life when engineers at an aero-engine test-bed in Bristol watched and listened as the prototype of a novel gas turbine ran for the first time. Called ‘Pegasus’, the engine became the world’s only operational power plant for short take-off vertical landing (STOVL) flight as it powered the hugely successful Harrier combat aircraft. Today, 50 years on, engineers at the same Bristol site are preparing an even more radical power system for the world’s most advanced fighter aircraft (see Ingenia,issue 20, for more on the development behind this MacRobert Award 2004 finalist).
The trial tests of the Pegasus engine in September 1959 helped establish a world lead in the field of STOVL engine technology for engineering teams at Rolls-Royce, a lead that we maintain today. Our experience with the Pegasus during those 50 years has earned us a place alongside Pratt & Whitney, General Electric, and Lockheed Martin in an international effort to develop the latest generation of combat aircraft: the F-35 Lightning II Joint Strike Fighter, currently the world’s biggest defence aerospace procurement programme.
The F-35 is a family of three similar and very advanced fighters that will enter service from 2012, equipping armed forces in the United States, the UK and a wide range of allied nations that are participating in the programme. One version, designated F-35A, is designed for conventional take-off and landing operations. The second (F-35B) is for duties that require the flexibility of short take-off and vertical landing; while the third (F-35C) is for carrier-based flying.
The three versions of the F-35 are technically advanced and pose formidable engineering challenges. The short take-off version, however, has entered uncharted realms of power system engineering that have pushed the Rolls-Royce teams in the UK and the United States to new levels of achievement.
All versions of the F-35 have a single main engine that exhausts through a nozzle at the back of the aircraft in the normal way. In the short take-off and vertical landing version, though, four completely novel power system features come into play, elements that together comprise the Rolls-Royce LiftSystem. This is where the most significant engineering challenges arose.
The Rolls-Royce LiftSystem, combined with the aircraft main engine, allows for vertical lift and supersonic capability in one propulsion package. The LiftSystem provides the vertical capability by generating thrust in the LiftFan and redirecting the thrust from the main engine through the 3 Bearing Swivel Module and Roll Post ducts. The LiftFan is a mechanically driven vertical 2 stage fan, driven by the low pressure turbine of the main engine. It generates approximately 20,000 lb thrust at full power, with 18,000 lb of thrust from the 3 Bearing Swivel Module and 2,000 lb from the Roll Post providing the 40,000 lb of gross thrust required in the vertical mode.
The system thus effectively increases the bypass ratio of the main engine through the induction of higher airflow by the LiftFan with not only higher airflow, but higher airflow with the ideal characteristics for vertical flight (high mass flow and low jet velocity). This revolutionary step redefines the relationship between horizontal thrust and vertical lift, and produces significant increases in performance, efficiency and safety.
Managing airflows
The first of the LiftSystem’s novel features is the 127cm diameter LiftFan, which is used for short take-offs and vertical landings and situated just behind the cockpit. At the heart of the LiftFan are two counter-rotating ‘blisks’. Each blisk features a high efficiency set of blades joined to a disc using state of the art linear friction welding technology. It is mounted vertically just behind the cockpit. The inlet of the LiftFan is parallel with the top of the fuselage and its exhaust flows downwards through a nozzle on the underside of the aircraft to provide a 20,000 lb column of thrust, which can be vectored fore and aft.
The fans of jet-powered aircraft typically face the oncoming airflow in line with the direction of flight. The LiftFan’s position, at 90 degrees to the direction of oncoming airflow of up to 250 knots, means we had to design a fan that can operate efficiently in the exceptionally turbulent environment created by extremes of airflow distortion at the face of the fan.
This challenge has been adressed by using the most advanced experimental and analytical modelling techniques, including world-class computational fluid dynamics methods. At the same time we have tested hardware in which a heavily instrumented full-scale fan runs in a test cell behind several different ‘stream-tubes’ that direct a variety of fierce airflows across its face, each representing particular flight conditions.
This work has effectively explored the stresses on fan blades and the LiftFan’s overall behaviour. It has enabled us to develop a two-stage fan using blades that combine exceptional robustness with high aerodynamic efficiency, ensuring that the LiftFan delivers 100% of its demanded thrust each time the F-35B requires it.
Flexible nozzle
The LiftFan’s task is to provide the F-35B’s forward element of vertical lift. At the rear of the aircraft, a rotating nozzle is the second of the key components for creating lift. The nozzle’s design, using circular bearings and elliptical casings, allows it to vector the aircraft’s rear thrust both longitudinally and laterally. The nozzle in normal wing-borne flight points rearwards, propelling the aircraft forwards at speeds of up to Mach 1.6 (around 1,300 mph). When vertical thrust is required this nozzle swivels downwards through a range of 95 degrees in 2.5 seconds, providing a rear column of vertical thrust of up to 18,000lb to balance the thrust of the LiftFan.
The big challenges for us were how to ensure that this exhaust duct – called the three-bearing swivel module, or 3BSM – functions with high reliability across an exceptionally wide range of conditions. Its task is to direct flows of very hot exhaust gases at thrusts of up to 40,000 lb, with ‘reheat’ in wing-borne flight, and some 18,000 lb in jet-borne phases of flight. As with the LiftFan, these conditions required us to explore and map entirely new areas of engineering.
One priority is ensuring the integrity of the entire 3BSM is maintained as it handles the operational demands pilots will put on it. For example, it is crucial that the large circular bearings of the 3BSM, each some 122 cm in diameter, operate successfully under the enormous thrust loads when in vertical mode.
We have addressed these challenges by applying analytical tools to help us assess key factors such as aerodynamic performance, thermal loadings and the behaviour of airflow streams as the nozzle swivels. This has given us knowledge that has helped us to develop and make use of the ideal materials in the construction of the 3BSM, such as high temperature lubricant , ceramics, and titanium, and develop effective manufacturing and production processes.
Stabilising ducts
While the 3BSM and the LiftFan provide the prime sources of vertical thrust, two smaller but equally critical components we call ‘roll posts’ represent the third main element of the Rolls-Royce LiftSystem. These are ducts, one in each wing, that direct 1,950 lb of thrust each from the main engine during short take-off and vertical landing, providing aircraft roll control and lateral stability. Each requires a flexible sealed joint to decouple the duct from the engine during wing deflections as the F-35B manoeuvres in flight – once again, a novel approach unique to the LiftSystem. The ability to regulate the amount of thrust produced by these roll posts is via a compact flap mechanism on the roll post nozzle, which can be closed entirely during normal flight.
The duct needs to contain up to 125 psi (8.6 bar) pressure at high temperatures within the wing and utilises titanium tubes formed under high pressure with highly controlled welding techniques to give the required strength, weight and integrity in the confined space within the wing.
High-power gearbox
To deliver the 20,000 lb of downward thrust needed to lift the F-35B, we have had to solve yet another major engineering problem: the need to provide a drive system for the LiftFan robust enough to handle an unprecedented 28,000 shaft horsepower (21MW). In addition, it needed to be light and compact enough to be practical for use in this small, agile combat aircraft.
The approach we have taken in this fourth key element of the LiftSystem involves a drive shaft running forward from the front of the F-35B’s main engine to a clutch and then gearbox on the casing of the LiftFan. This is a radical departure from any other combat aircraft power system, with the highest-loaded bevel gearbox ever used in an aircraft.
We have carried out some 6,000 hours of testing on the LiftSystem hardware during the past three years. These tests have helped us overcome the extensive challenges in getting these four prime LiftSystem elements to readiness for the rigours of everyday squadron service.
STOVL
For short take-off, the 3BSM is swivelled downwards, the roll post nozzles are opened and the clutch is engaged, the power of the main engine is increased and the LiftFan begins to produce thrust. As the F-35B accelerates it is lifted into the air by downward thrust from a combination of its LiftFan, the 3BSM and two roll-posts and within seconds it reaches the point where its wing provides all the lift it needs to fly conventionally. At this point, the drive to the LiftFan is disengaged, the 3BSM is swivelled rearwards and the roll post nozzles are closed allowing 100% of the main engine’s power to be delivered through the rear nozzle.
As the F-35B prepares for a vertical landing, thrust from its main engine is decreased, the clutch is engaged and the LiftFan begins to spool-up to close to 100% speed in readiness to provide downward thrust the moment it is required. But although the LiftFan is rotating at 100%, it must produce the absolute minimum of vertical thrust to avoid creating an unwanted pitch-up effect on the aircraft during the critical approach-to-landing phase.
This is an entirely novel challenge. Normally a fan running at 100% speed will produce 100% thrust. The LiftFan, however, must only begin to deliver its thrust when the pilot selects nozzles-down for short take-off or vertical landing.
Our solution has been to use the guide vanes at the front of the LiftFan’s inlet. We have designed these to operate at variable angles, constantly adjusting to optimise airflow into the LiftFan’s intake. As the F-35B slows for its transition from forward flight to hover, the LiftFan’s transmission system is engaged and within 10 seconds spools-up to 100% speed in readiness for instant power delivery. Its inlet guide vanes are closed, reducing airflow and minimising thrust. At the instant when downward thrust is needed from the LiftFan, the guide vanes begin to open. For 100% thrust they open fully.
Cross-over technology
To address challenges of this significance our team has fully exploited the most advanced experimental and simulation tools as well as technological gains made in other Rolls-Royce programmes. Techniques created for developing civil aerospace engines, for example, have guided us towards achieving solutions to several key challenge areas.
Dynamic computer-modelling methods developed in the Rolls-Royce civil aerospace business to investigate the field of bird ingestion have enabled us to simulate the effects of a bird strike on the LiftFan.
Another example of ‘read-across’ technology is our use of hollow blades in the first-stage rotor of the LiftFan, blades that are integral to the disk to create a bladed disk or ‘blisk’. Marrying the hollow blade technology from civil turbofans with the blisk technology developed in the defence industry cuts weight by some 68 kg to 540 kg compared with a conventional fan designs .
Crucially, our current efforts are also geared to ensure the LiftSystem can handle the rigours of everyday front-line service in the hands of squadron pilots when they meet the demands of future combat. The LiftSystem today is far tougher than the earlier version that proved this concept during basic flight demonstrations in a prototype aircraft in 2000. Today’s LiftSystem is not only some 320 kg lighter than that demonstrator hardware but also robustly prepared for service.
In fact, the LiftSystem has completed pit testing, where the aircraft is tethered above a pit and the LiftSystem is tested. The aircraft has also been flying since June 2008 in its conventional flight mode where the LiftSystem is not engaged. It is expected that the first inflight engagement of the STOVL system will take place by the end of 2009 culminating in a vertical landing.
These trials have shown how the performance of the F-35B will surpass that of the Harrier in every respect. The Harrier, powered by the Pegasus engine, has long proved itself in service. Soon, when the LiftSystem begins to show its qualities in flight, engineers in our team can reflect that our efforts, like those of our colleagues in the Pegasus programme in the past, may well ensure this remarkable new fighter will still be flying at the forefront of national defence in five decade’s time.
Keep up-to-date with Ingenia for free
SubscribeOther content from Ingenia
Quick read
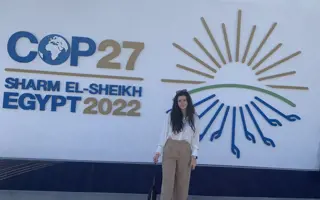
- Environment & sustainability
- Opinion
A young engineer’s perspective on the good, the bad and the ugly of COP27
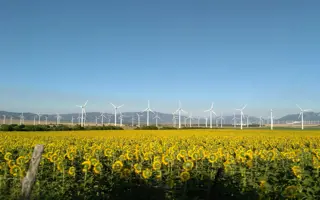
- Environment & sustainability
- Issue 95
How do we pay for net zero technologies?
Quick read
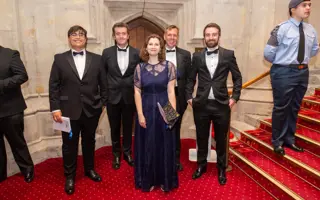
- Transport
- Mechanical
- How I got here
Electrifying trains and STEMAZING outreach
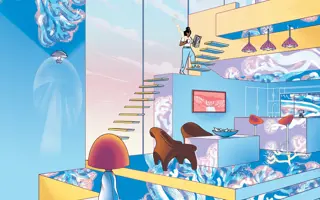
- Civil & structural
- Environment & sustainability
- Issue 95