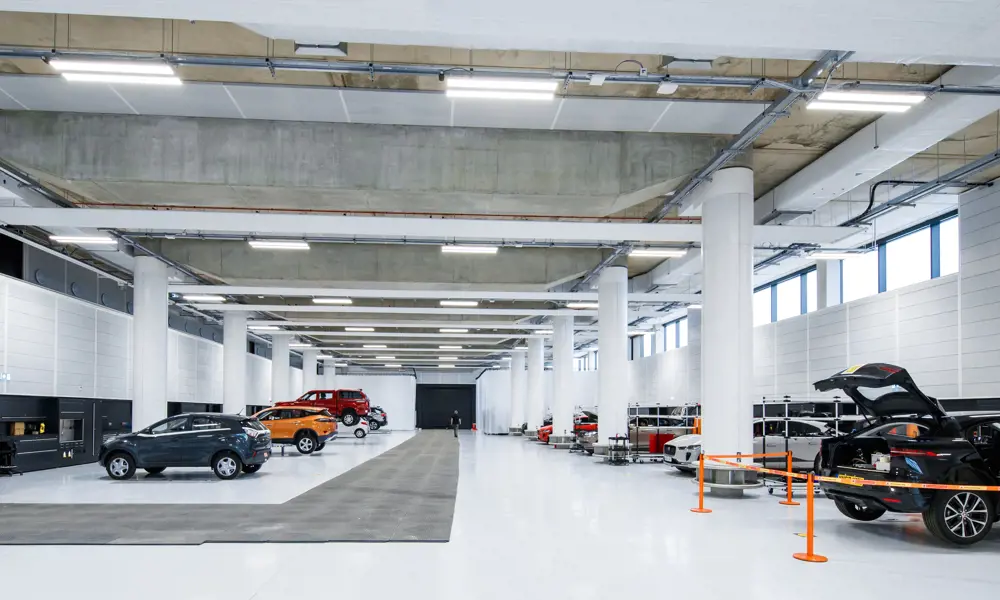
A centre fit for future transport
Mobility is fundamental to modern life. Our ability to move people and products from one place to another is essential to economic and societal success.
One of the UK government’s Grand Challenge Missions in its industrial strategy is to become a leader in the development and manufacture of zero-emission vehicles. The ambition is for all new cars and vans to be effectively zero emissions by 2040, and not only greener, but also safer and smarter.
Developed as part of the industrial strategy, the Automotive Sector Deal has resulted in carmakers and their suppliers working together with government to support a significant increase in research and development (R&D): £225 million will be invested in automotive R&D from 2023 to 2026. This will focus on ultra-low and zero-emission cars and the next generation of connected and autonomous vehicles while improving the innovation of the UK supply chain.
These innovation areas are crucial if we are to reach what Jaguar Land Rover, Britain’s largest car manufacturer, is calling ‘Destination Zero’ – zero-emission vehicles, zero congestion and zero accidents
These innovation areas are crucial if we are to reach what Jaguar Land Rover, Britain’s largest car manufacturer, is calling ‘Destination Zero’ – zero-emission vehicles, zero congestion and zero accidents. Helping to address this challenge is the £150 million National Automotive Innovation Centre (NAIC) at the University of Warwick – the largest automotive research centre of its kind in Europe. A partnership between WMG, Jaguar Land Rover and Tata Motors European Technical Centre, it will focus on everything involved in the shift to autonomous, connected, electric and low-carbon vehicles. From looking at the design, testing and refining of batteries at scale and managing vehicle weights to compensate for the size of battery packs; to ensuring autonomous vehicles can identify and avoid danger and that connected vehicles are data-secure and error-free. Global automotive suppliers, such as Bosch and AVL, have already worked on these issues at the University of Warwick Science Park.
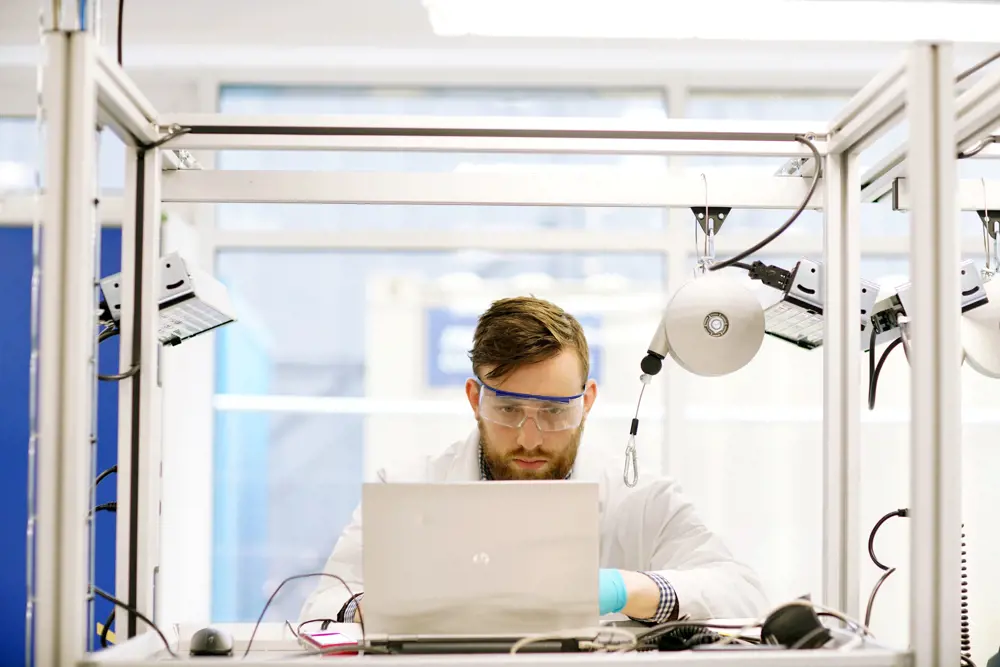
Professor Dr Ralf Speth KBE FREng, Chief Executive of Jaguar Land Rover, says the centre’s state-of-the-art facilities will offer a “critical mass of research capability in an environment designed to encourage cross-fertilisation of ideas on an unrivalled scale”
State of the art
The 33,000-square-metre centre provides space for engineers, designers and academics to work together, from apprentices to senior managers. This joint investment has £15 million of support from the government’s UK Research Partnership Investment Fund (UKRPIF), through Research England, to identity green, smart, safe solutions for future mobility.
There are already 700 designers, engineers and researchers located within the centre. It will eventually host 1,000 people working on a range of future vehicle and mobility projects. Design and engineering students and apprentices will also share the space and work alongside staff.
The centre features design studios; a vast engineering hall and laboratories for advanced powertrain, hybrid and chassis research; an immersive modelling and simulation suite; and an advanced propulsion research laboratory, all equipped with the latest technology such as engine dynamometers, virtual reality rooms and drive-in simulators. It has over 50 specialist areas, which include acoustic quiet facilities; noise, vibration and harshness testing equipment; and electrical development and high voltage laboratories.
To support the design modelling operations, NAIC has a three-axis milling machine to create the wooden structure (buck) that the clay models are constructed over, a paint shop consisting of three full-size vehicle paint booths and a wood mill, which will be used to make the buck.
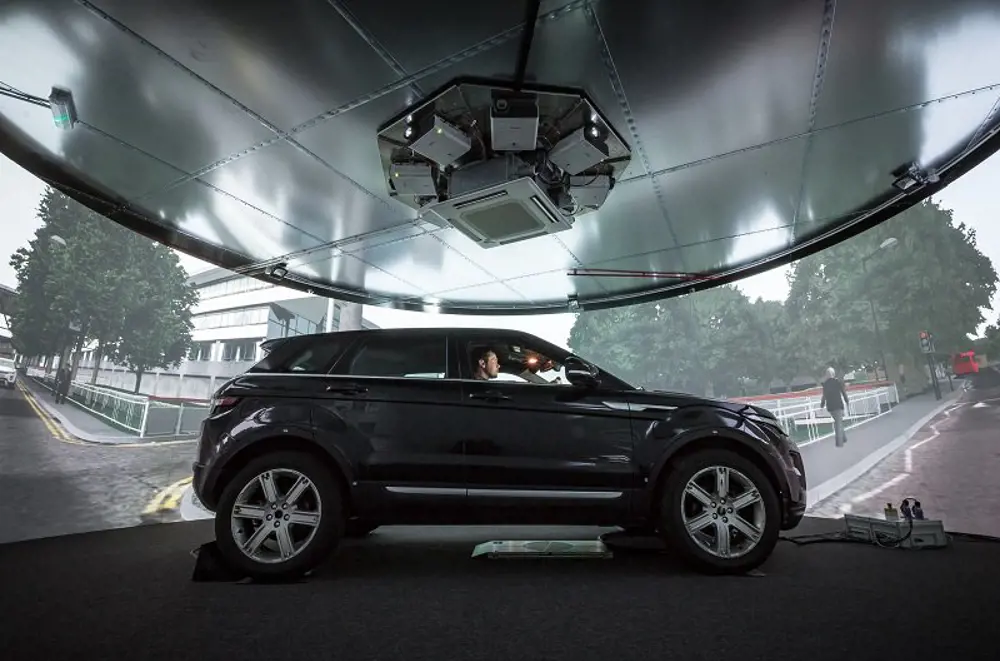
The 360o driving simulator allows testing of smart and connected vehicles in a safe, controlled immersive environment
Automotive technology research
NAIC aims to encourage inspiration and collaboration on research projects between designers, engineers, manufacturers, academia, suppliers, customers and governments.
The Advanced Propulsion Research Laboratory at NAIC, which also benefits from UKRPIF support, is the UK’s first complete and dedicated facility for the research, development and industrialisation of low-carbon automotive technologies in the UK. For these to be successful, researchers will need to develop propulsion systems that appeal to consumers and are profitable for manufacturers. Research will look at reducing the cost and improving the performance of electrified powertrains compared to conventional engines. To do this, engineers and academics will research ways to increase the integration of electrical and electronic components into system architectures; help suppliers scale up and manufacture parts in sufficient, cost-effective quantities; and ensure this is done while maintaining quality, performance and safety.
This research encompasses adapting internal combustion engines in the short term, alongside hybrid and electric systems, lightweight vehicle technology and advanced automotive control systems.
WMG’s research team in advanced propulsion systems will address the technology needs that are critical to the future competitiveness of the automotive industry. These facilities will be available to manufacturers and suppliers so the whole supply chain can work together to make cars and commercial vehicles greener.
Key challenges include: energy storage and management; battery systems; power electronics; systems control and integration; lightweight materials; and fuels. This work will be done collaboratively and knowledge will be shared across the transport sector.
Key challenges include: energy storage and management; battery systems; power electronics; systems control and integration; lightweight materials; and fuels
One example of this collaborative approach is WMG’s AMPLiFII (Automated Module-to-pack Pilot Line for Industrial Innovation) and AMPLiFII 2 projects, supported by the Advanced Propulsion Centre and Innovate UK. Both projects are developing battery systems for vehicles across a range of sectors including high-performance automotive, buses and off-highway vehicles. The low volume of very specialised battery packs needed for these sectors means that manufacturers have found it difficult to justify the high cost of developing electric vehicles.
Working closely with industry partners, Jaguar Land Rover, ADL, Ariel, Delta Motorsport, Potenza, Trackwise, HORIBA MIRA, and the University of Oxford, WMG’s work has developed a scalable, modular pack centred around cylindrical cells. Looking initially at packs of 18,650 cells, the project has now entered its second stage – AMPLiFII 2 – and is now working with 21,700 cells.
This battery architecture supports both high-power and high-energy requirements, meaning that manufacturers will be able to aggregate demand for components and benefit from significant economies of scale.
The research will help create an electric vehicle supply chain that offers robust, low cost and quick-to-market mass production standards, while also informing the development of battery technologies for Jaguar Land Rover.
To reach ‘Destination Zero’, safer roads are needed as well as zero-emission vehicles. Engineers need to understand how vehicles communicate with each other and with the transport network, as well as how drivers interact with cars, giving them the right tools to drive safely. Testing these technologies on the road in real-world driving situations is often complicated and potentially dangerous for early-stage development. It is also reliant on the production of costly physical prototypes.
To reach ‘Destination Zero’, safer roads are needed as well as zero-emission vehicles. Engineers need to understand how vehicles communicate with each other and with the transport network, as well as how drivers interact with cars, giving them the right tools to drive safely
To overcome this challenge, WMG created a drive-in, driver-in-the-loop, multi-axis, 360o cylindrical screen, high definition driving simulator – the world’s first immersive, simulated environment for smart and connected vehicles. It fully reproduces wireless communications, putting a real car in an immersive virtual environment so that smart and connected vehicles can be tested and refined. It finds the problems that occur at the extreme and risk points for road safety and data security in a safe, controlled environment.
The next generation of the simulator, which is currently under construction in NAIC, will support the accelerated development and adoption of advanced technologies for next-generation vehicles. For example, research will be looking at how you can fool and confuse smart vehicles via their data sources and how they will deal with confusing or contradictory information.
The Midlands Future Mobility programme, where WMG works with Amey Consulting, AVL, Costain, Coventry University, MIRA, Transport West Midlands, and the Wireless Infrastructure Group, will also evaluate connected and autonomous vehicle technologies with support from the government’s Centre for Connected and Autonomous Vehicles. These have been developed using simulation in NAIC, on test tracks and on roads in real-world driving situations. This will provide invaluable additional learning in development of the vehicles as commercially viable and desirable means of road transport.
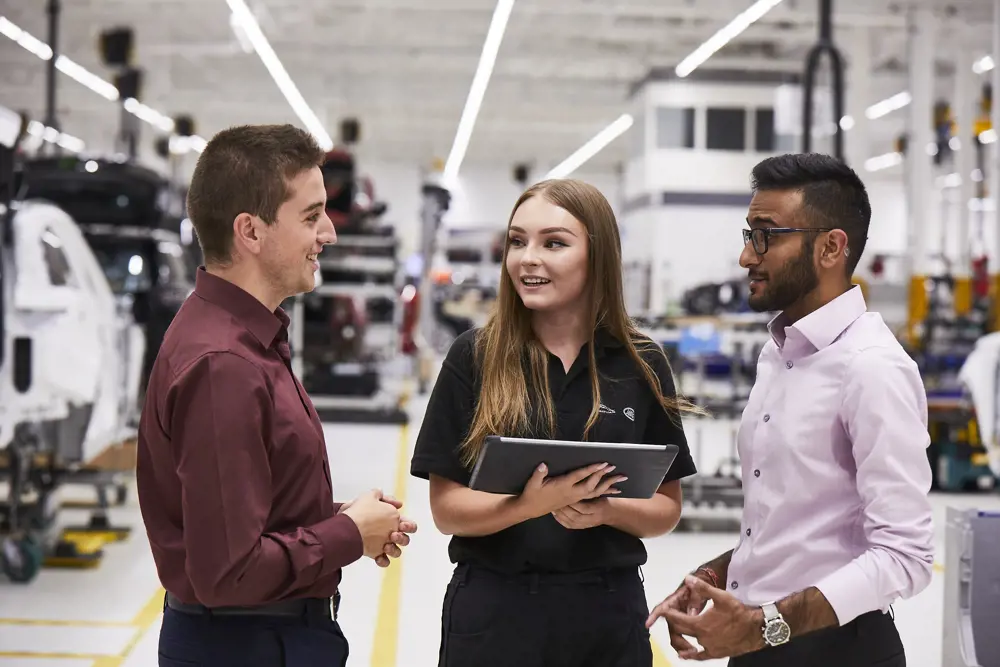
Apprentices studying at the NAIC will have a real and immediate impact within the businesses they are placed with, as the courses include work on improving paintshops, refining aerodynamic features on vehicles and working with suppliers to reduce costs © Nick Dimbleby
Engineering education to keep the UK globally competative
The partners in NAIC are committed to delivering the skills to keep the UK globally competitive. The teaching facilities – such as workshops, collaborative learning spaces and a business incubator – support the education of tomorrow’s engineers with degree apprentices studying in the centre and students from the WMG Academies for Young Engineers, university technical colleges where 14 to 19-year-olds work on real-world projects as part of their curriculum.
The new WMG Degree Apprenticeship Centre, which opens in September alongside the NAIC, will focus on apprenticeship courses for advanced engineering and manufacturing companies. It will provide training programmes up to master’s degree level to 1,000 students each year. At undergraduate level these include engineering, applied engineering, digital technology solutions, and health, wellbeing, science and technology. At postgraduate level, they cover engineering business management, systems engineering and senior leadership.
While they study, the apprentices will be employed by companies such as Jaguar Land Rover, Airbus, Caterpillar, Aston Martin, GE and Lear. They will undertake their academic studies at the centre. All of the courses are tailored to meet the automotive industry’s needs.
As they learn and work, the apprentices will benefit from NAIC’s facilities, especially the state-of-the-art teaching workshop. Meanwhile all NAIC partners are developing curricula, including apprenticeships and lifelong learning, that will support emerging technologies in mobility at NAIC.
Lord Bhattacharyya
🚘 The vision for the automotive sector that resulted in the Lord Bhattacharyya Building
The late Professor Lord Kumar Bhattacharyya KT CBE FREng FRS founded Warwick Manufacturing Group, now WMG, in 1980. For four decades, Lord Bhattacharyya led WMG, at the University of Warwick, on a singular mission: to combine academic excellence with industrial relevance, in both education and research.
WMG pioneered part-time modular courses relevant to real business needs, so staff could immediately contribute to their business while they learned. He saw engineering education as appropriate for all, offering teenagers the chance to become young engineers at WMG’s two academies for 14 to 19-year-olds, right through to enabling experienced industrial engineers to innovate by earning research degrees
Lord Bhattacharyya saw innovation and collaboration as being at the heart of WMG. He led collaborative research partnerships on vehicle lightweighting, computer-aided design, powertrains and experiential engineering, each project with commercial partners and real-world impact.
The culmination of Lord Bhattacharyya’s vision for Britain’s automotive sector is brought to life in the NAIC, bringing together government, academia and business to address the great challenges of future mobility. As a tribute to his enduring vision, the research he championed will be conducted in the Lord Bhattacharyya Building.
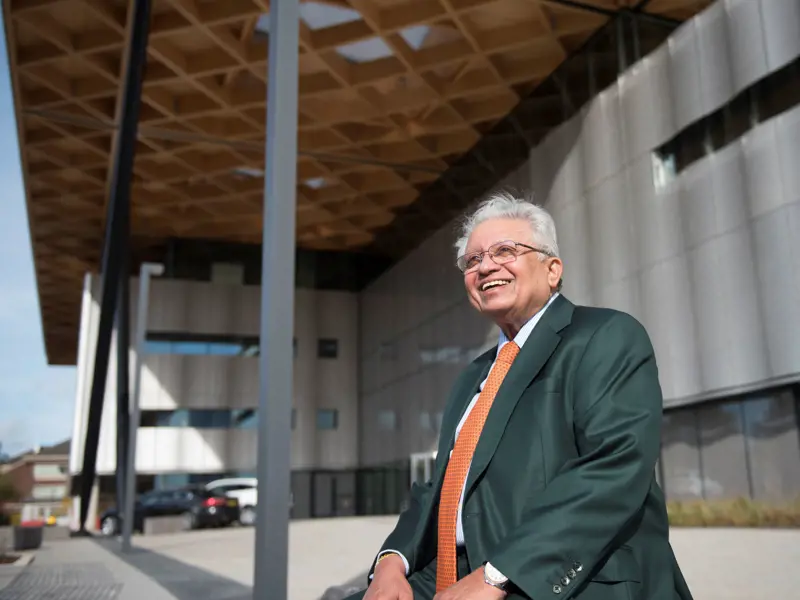
Professor Lord Kumar Bhattacharyya KT CBE FREng FRS, Regius Professor of Manufacturing, outside the centre that bears his name
Transport in the future
The future of transport could well be one where zero-emission vehicles, public transport and self-driving pods form a single transport system, securely networked to each other and via digital platforms for maximum safety and minimal congestion.
People might drive – or be driven in – electrified, zero-emission vehicles, powered by an integrated smart-charging network using renewable and zero-emission energy.
These vehicles could be constructed with sustainable, self-repairing, stronger, lighter materials, which have been developed from technology advances in materials science, including natural fibres and recycled materials that reduce emissions in the production process.
Achieving greener, safer and smarter mobility requires partnership – between researchers, companies and government – and a workforce with the right skills, facilities and laboratories to find the answers together.
***
This article has been adapted from "A centre fit for future transport", which originally appeared in the print edition of Ingenia 79 (June 2019).
Contributors
Professor David Mullins is Interim Head of WMG at the University of Warwick. He is involved in the design and implementation of WMG’s research, education and knowledge transfer strategy, and has been responsible for the development of major WMG initiatives, including the NAIC. Before joining the university in 1997, he worked in UK Research Councils and was a regional coordinator for the ACME manufacturing directorate.
Keep up-to-date with Ingenia for free
SubscribeRelated content
Design & manufacturing

Super cool(er)
Welsh startup Sure Chill has developed a cooler that uses the properties of water to keep its contents cool for around 10 days without electricity. This is ideal for storing items such as vaccines where electricity sources are unreliable.

R&D investment makes good business sense
In just five years, Dr Ralf Speth FREng has presided over a revolution in design and manufacturing that has helped create a new family of engines and has overhauled Jaguar Land Rover (JLR) production facilities.

Steel can arise from the ashes of coal
Thousands of people were laid off in the UK steel industry in 2015 and there are pessimistic future forecasts. Professor Sridhar Seetharaman of the Warwick Manufacturing Group argues that smaller, flexible steel mills implementing new technology would better cope with fluctuating global trends.

Integrating metrology in business and academe
Professor Jane Jiang’s interest in measuring began when she worked on a bus production line in China. She found that the best way to improve quality, consistency and productivity was through metrology, the science of measurement. Today, she runs the UK’s largest metrology research group.
Other content from Ingenia
Quick read
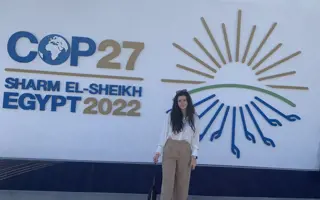
- Environment & sustainability
- Opinion
A young engineer’s perspective on the good, the bad and the ugly of COP27
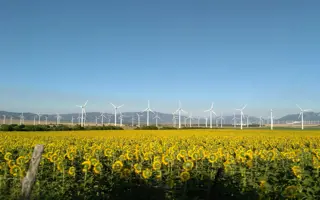
- Environment & sustainability
- Issue 95
How do we pay for net zero technologies?
Quick read
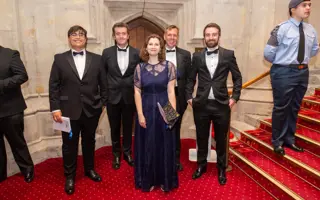
- Transport
- Mechanical
- How I got here
Electrifying trains and STEMAZING outreach
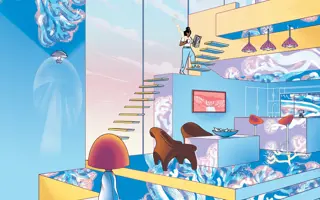
- Civil & structural
- Environment & sustainability
- Issue 95