
Reimagining the zoetrope

A modern replica of a Victorian zoetrope © Andrew Dunn
During the first 10 days of September 2022, the skyline of Canning Town’s Limmo Peninsula looked a little different to usual. Each night, a vertical zoetrope almost 10 metres in height, lit by strobes and powered by human volunteers, showed a 3D animation depicting the ferryman from Greek mythology, Charon. This art installation arrived from Nantes, on its tour of art festivals around Europe, and was originally devised for Nevada’s Burning Man festival in 2011.
Zoetropes are one of the earliest form of animations, dating back to the 1800s. Historically, they consist of a cylinder with a progression of images inside and slots to peer through. As the wheel spins, the rapidly changing sequence of images gives the viewer the illusion of movement, with the slots preventing the images from blurring into one. While at first based on strips of paper with sequences of illustrations (not unlike a flipbook), later developments would go on to use photographs and even sculptures.
Most zoetropes are toy-sized, intended for entertainment long before the world of film arrived; but in recent years, a handful of artists have built larger scale installations designed to wow audiences. However, it is by no means a common artistic medium. Mat Collishaw, one of the Young British Artist group, has exhibited several 3D zoetropes, some up to three metres across (coincidentally, his 2014 zoetrope All Things Fall was produced in collaboration with Factum Arte – see ‘Technology to recreate artworks’, to read about some of the company’s other work). But the zoetropes designed by San Francisco visual artist Peter Hudson are some of the world’s largest, measuring up to almost 10 metres in diameter, and have been displayed at well-known festivals from Burning Man to the UK’s Secret Garden Party.
The zoetropes designed by San Francisco visual artist Peter Hudson are some of the world’s largest, measuring up to almost 10 metres in diameter, and have been displayed at well-known festivals from Burning Man to the UK’s Secret Garden Party.

Image reproduced from 507movements.com
Mechanical inspirations
The Victorians had an impressive influence on everything from engineering to entertainment – and sometimes both at once. In 1868, Henry T Brown published a book called Five Hundred and Seven Mechanical Movements, including detailed illustrations of kinematic concepts important for engineers, from rotating pulleys to pendulums.
A 1908 edition included detailed illustrations of concepts such as epicyclic gear trains – also called planetary gears, today used in everything from cars to 3D printers and pencil sharpeners – and capstans, the rotating machines used by sailors to haul weights (such as anchors). It also included a diagram demonstrating how to convert an oscillating semicircular frame into rotary motion. This showed a device that can convert oscillating motion into rotary motion (see image). A semicircular piece (A) attached to a lever working on a fulcrum (a) is attached to the ends of two bands (C and D). The bands run around two pulleys, loose on the shaft of the flywheel (B). One of the bands (C) is open, and the other (D) is crossed. Pawls attached to the pulleys engage with ratchet-wheels on the flywheel shaft when piece A turns in either direction, producing continuous rotary motion.
Fast-forward to the start of the 21st century, and this diagram became a source of inspiration for Peter Hudson. He had spent the noughties creating a series of stroboscopic sculptural zoetropes, depicting everything from recurring universes to people swimming. However, Hudson’s previous projects had all been horizontal zoetropes, and he had something more ambitious in mind for his next design, which he was due to create for the 2011 edition of Burning Man festival.
Rites of passage
Hudson’s idea for the new project was to create an interactive depiction of Charon, the Greek mythological ferryman, who carried away departed souls across the river Styx to the afterlife. This was to tie in with the theme of that year’s festival, rites of passage, and Hudson chose to focus on the final rite of passage: death. The work was to be funded by a grant from the festival and multiple fundraising campaigns, with over 100 volunteers pitching in to construct the zoetrope. The zoetrope would be powered by audience members pulling ropes to create torque (rotational force). After exceeding a certain speed, the 3D animation would become apparent. The choice of ropes was a nod to cathedral belfries, where ropes are used to ring a bell.

The central structure of Charon visible from below. Participants can be seen pulling on the ropes to generate torque in the far right of the image © Trey Radcliff Haron
A vertical zoetrope of this scale had never been attempted before, and logistical challenges immediately arose from this Ferris wheel-esque design. Most important was the need to translate linear force from people pulling ropes to torque that could drive the rotational motion of the vertical zoetrope. The solution lay in Brown’s Victorian handbook, and the aforementioned diagram. It depicted a semicircular piece attached to a lever resting on a fulcrum, with two pulleys connecting it to a flywheel. A continuous rotary motion is maintained as the semicircular piece turns first one way and then the other. For aesthetic reasons, Hudson employed the same principle, but used 12 30-centimetre-diameter drums with custom clutch bearings. With this setup, the force produced by volunteers pulling ropes would be translated into torque to drive rotation of the zoetrope. This spinning motion, when allied to strobe lighting, creates an effect akin to a three-dimensional motion picture, and requires a rotational speed of 20 rpm (revolutions per minute).
Overcoming challenges
Hudson’s first horizontal zoetrope had a central rotational axis sandwiched by two tapered roller bearings, requiring only one support point. By contrast, some of his later horizontal zoetropes were supported by idler wheels, but each extra load point increased drag. Instead, Charon’s entire rotating structure would rest on a single hub (with four bearings). This vertical zoetrope would require both left and right support points and two tapered roller bearings on each side – all correctly aligned in space.
Furthermore, early prototypes relied on components from bicycle sprockets, which repeatedly failed because of the sheer torque being generated by Charon’s human participants. Eventually, an equivalent component from a Raptor quad bike was sourced, which could handle over 1,000 Newton-metres of torque. Another early setback involved the use of manila hemp rope. Not only did this struggle to grip each eight-inch custom-machined aluminium drum satisfactorily, but it also rubbed against itself creating friction and drag that contributed to premature wear. The solution involved encasing each rope in a repurposed fire hose, which had the twin benefits of increasing grip and minimising abrasion. Similarly, sharp internal hex-nut edges on the directional guide pulleys were discovered to be shredding the ropes. These hex-nut edges were sanded down, with Teflon rope glides employed to reduce wear.

The model skeletons spaced around the zoetrope, each adopting a unique pose to give a sense of the rowing motion © Mitzi Peirone
Next, attention turned to the skeletons that would comprise Charon’s zoetropic effects. Each model was made from polyester resin and urethane foam, with the skulls, femurs and ulnas custom-cast from foam and polyester resin. The more fragile torso components were purchased from a medicalgrade vendor since there was no need for these to move. The team invented a malleable and posable armature that the bones could be situated around, in what would become their final position, with a pivot point at the hips. Next, modelling software was used to create an animation that involved each skeleton adopting a unique pose, to contribute to the sense of movement as the wheel rotated.
Motion picture
In motion, the results of this modelling software and skeletal positioning are spectacular. Accompanied by the sound of a tolling bell, flame-coloured lights flicker around two Gothic A-frame archways with the wheel centrally mounted between them. A dozen participants tug on ropes that additionally serve to ring the bell. Once the six pairs of ropes are being pulled at a suitable speed, a strobe is activated that reveals the animation of the skeletons inside the wheel as they ‘paddle’ towards the unknown using wooden oars, creating an otherworldly effect as it towers above spectators. The frame itself – like much of Charon – is manufactured from I-Beam steel, contributing to a gross shipping weight of over 8,000 kilograms. Once fully erected, the zoetrope reaches nearly 10 metres tall.
The spinning wheel has a diameter of almost nine metres, with 20 spokes each supporting an animated skeleton, in various rowing positions. The wheel rests inside two double-strut A-frame support arches with cross bracing at both ends.
Building tension
Assembling Charon takes up to five days, partly because each side of the wheel has to be in perfect alignment. Two parallel points must be exactly square and level, within one millimetre of each other, to align the hub bearings. The team achieves these tolerances by using a five-beam laser. The assembly and transportation process has been further optimised by numbering every item, allocating it a dedicated place within its transportation containers, and ensuring each item is unloaded in the order of assembly. For instance, skeletons are attached to the wheel at 180-degree, then 90-degree, then 180-degree positions, maintaining wheel balance and preventing its weight becoming unequal. A variety of custom dollies, high-density polyethylene glides and platforms are used for moving components along with a forklift truck, a 10-metre-tall variable reach lift, a cherry picker, and a crane.
The entire structure is accommodated in two 24 metre shipping containers, and the installation manual alone extends to over 50 pages, with a team of 10 people employed to assemble Charon. Disassembly is quicker, taking three to four days, at the end of which a crew of six people is allocated portions of a grid pattern to check Charon’s former location for misplaced hardware. When in the desert they even use magnets to identify and rescue any components that have become submerged in the ground. Nothing can be left behind from such a meticulously engineered assembly, especially one that is constantly touring around the world.
***
This article has been adapted from "Reimagining the zoetrope", which originally appeared in the print edition of Ingenia 92 (September 2022).
Contributors
Neil Cumins
Author
Keep up-to-date with Ingenia for free
SubscribeRelated content
Arts & culture
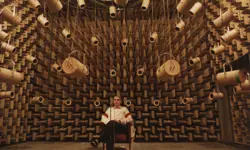
How to maximise loudspeaker quality
Ingenia asked Dr Jack Oclee-Brown, Head of Acoustics at KEF Audio, to outline the considerations that audio engineers need to make when developing high-quality speakers.

Engineering personality into robots
Robots that have personalities and interact with humans have long been the preserve of sci-fi films, although usually portrayed by actors in costumes or CGI. However, as the field of robotics develops, these robots are becoming real. Find out about the scene-stealing, real-life Star Wars droids.
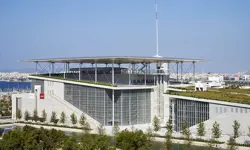
Design-led innovation and sustainability
The Stavros Niarchos Foundation Cultural Center, the new home of the Greek National Opera and the Greek National Library, boasts an innovative, slender canopy that is the largest and most highly engineered ferrocement structure in the world.
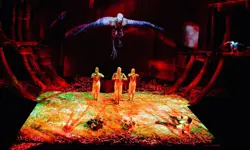
The technology behind ‘The Tempest'
William Shakespeare’s The Tempest is a fantastical play that features illusion and otherworldly beings. Discover how cutting-edge technology, such as motion capture and sensors, has brought the magic and spectacle to life on stage.
Other content from Ingenia
Quick read
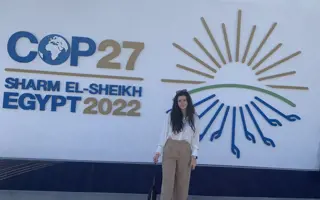
- Environment & sustainability
- Opinion
A young engineer’s perspective on the good, the bad and the ugly of COP27
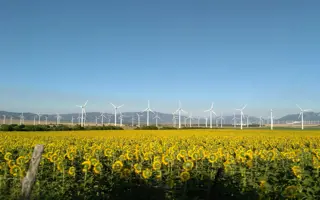
- Environment & sustainability
- Issue 95
How do we pay for net zero technologies?
Quick read
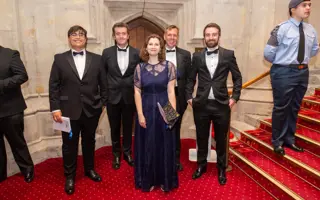
- Transport
- Mechanical
- How I got here
Electrifying trains and STEMAZING outreach
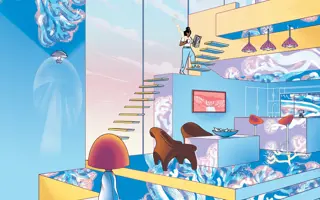
- Civil & structural
- Environment & sustainability
- Issue 95