
How AI can help 3D print perfect plane parts
In the past few years, engineers and innovators have 3D printed all kinds of exciting things. They've recreated lost Van Gogh paintings and fashioned ornate bridge structures that would otherwise be impossible to make. An entirely 3D-printed rocket launched from Cape Canaveral in May 2023. Back on Earth, 3D printers are even shaping the tissue structure of laboratory-grown meat (although some think 3D-printed food is a bridge too far and best limited to space). So far, so wild.
But the technology has yet to fully deliver in more conventional manufacturing settings.
Safety first
While 3D printers can make complex parts that cannot be made by traditional methods, they are prone to errors. In settings where safety is paramount and margins for error are narrow, this is a problem. For example, in a jet engine turbine blade, a defect as small as 300 microns could mean a print fails inspection, especially if it’s in a structurally important area.
"The challenge is it’s very unpredictable when making safety-critical parts, such as those used in aerospace," says Anas Achouri, Founder and CEO of Coventry-based startup, DONAA. "For prototyping, [3D printing is] OK. But for printing functional parts, you have no idea what to expect and then often you’re detecting defects later."
For prototyping, [3D printing is] OK. But for printing functional parts, you have no idea what to expect and then often you’re detecting defects later.
Anas Achouri, Founder and CEO of DONAA
Aiming to solve this problem, DONAA is developing an error-free 3D printing approach to detect defects during printing to save time and prevent waste. The idea is to enable engineers to halt printing before wasting resources on a whole part that will be discarded. At the very least, it will enable inspections to be much more targeted towards where defects are. Ultimately, the plan is for defects to be corrected, but this will require coordination with 3D printing manufacturers.
The scope and struggles of 3D printing
Putting aside its most established use case, rapid prototyping, 3D printing has gained traction with manufacturers for several reasons. For one thing, engineers like Anas believe printing parts locally, on demand, could make sourcing components significantly simpler.
“When I was managing manufacturing projects in the aerospace sector, often I had to deal with a lot of suppliers, quite a complex supply chain and a lot of specific parts. Managing projects like that can be a nightmare at times,” says Anas.
Then, there’s the ability to print higher performance designs that traditional manufacturing methods like metal casting, or machining, cannot make.
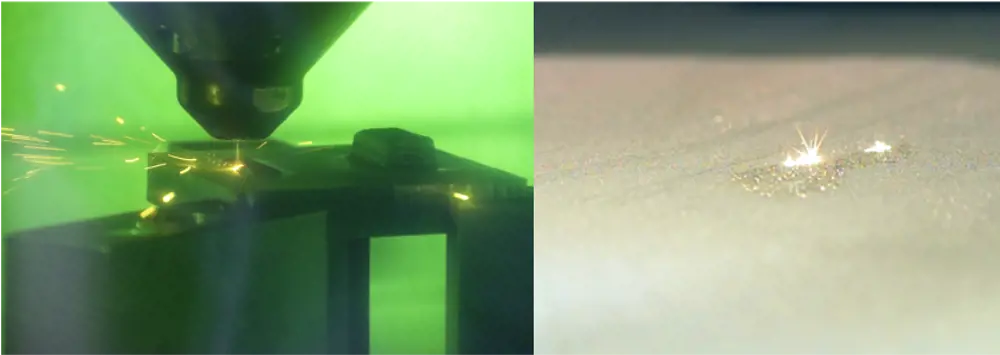
DONAA's solution has been used for different 3D printing technologies, including (left) directed energy deposition and (right) selective laser melting.
Anas gives the example of a jet engine. Better performance – higher speeds, lower fuel consumption – requires heating the turbine to temperatures approaching 1,800°C. But temperatures this high can damage the turbine blades, so engineers embed tiny slots or channels in the blades for air to penetrate and cool.
"With traditional manufacturing, it's just not possible to make some shapes. 3D printing can do that," Anas explains. "You can make a 3D model, put any channels inside the part, and then 3D print it, layer by layer. So, it unlocks new designs and makes complex parts possible."
The end result: potentially huge improvements in performance and efficiency… if you can successfully print the part.
The print itself can take days or weeks; inspection can then take months and incur costs and emissions as it may be sent to another country. If the testing engineers detect a defect, the process must start over, and is repeated until the part passes quality testing and is deemed fit for flying.
Inspections are painstaking because, in the worst-case scenario, if a defect is missed and the part is used, it could result in a "dramatic catastrophe", says Anas. Defects are often micron-scale and usually detected with a suite of non-destructive testing techniques, including visual inspection, microscopy, X-ray and ultrasound.
With traditional manufacturing, it's just not possible to make some shapes. 3D printing can do that.
Anas Achouri, Founder and CEO of DONAA
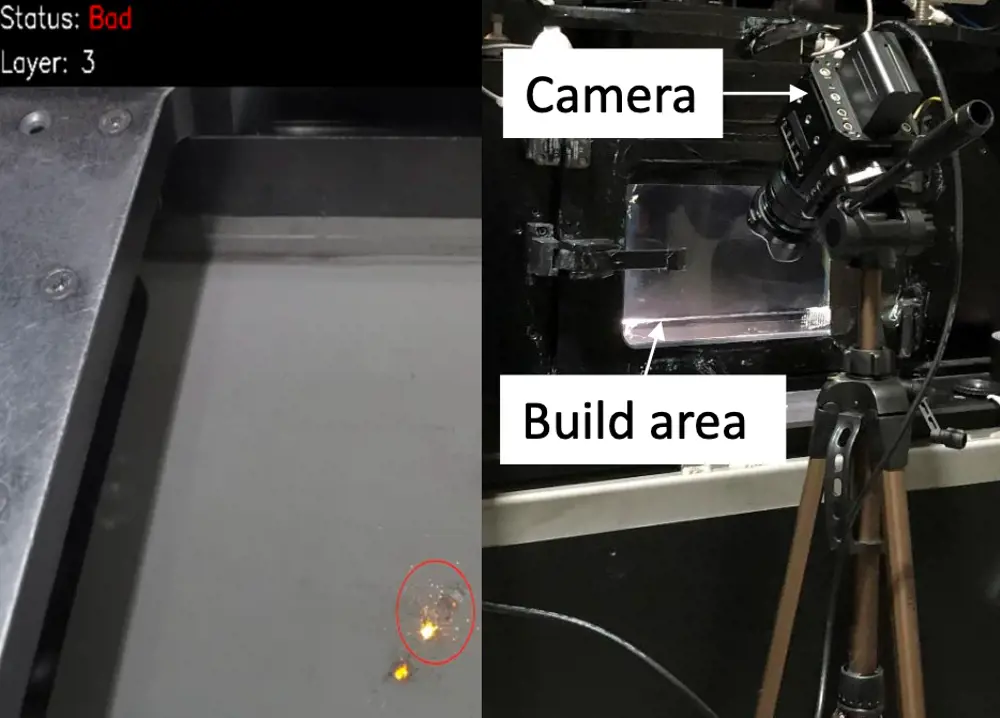
(Left) The camera captures a defect during printing (circled). (Right) Photograph of the setup, with camera and the print area.
Looking under DONAA’s hood
DONAA’s technology uses a straightforward principle: filming the print and then analysing key features on the footage with AI-based computer vision algorithms. DONAA’s software also uses finite element modelling to predict the material’s behaviour, which is important as not all defects are visible.
“We can detect geometrical defects, but also strength-related defects,” explains Anas. “Some of them you cannot even see by naked eye, or you can find out about them only after testing. We can predict [those].”
For now, the team records print footage with external cinematic cameras, but believe that in the future, all printers will come with built-in cameras to make their prints more reliable. DONAA is therefore aiming for its software to work with any type of camera.
One challenge the company is working to overcome is the sheer volume of data collected. “Printing can be very long, so every time we record the whole frame, we end up with terabytes of data for processing,” says Anas.
To minimise the data collected, the team is exploring neuromorphic cameras. “It’s similar to the human eye, [so] when there is a change in some areas, only the relevant pixels are triggered and then stored. You don’t store the whole frame. So we have less data, but higher quality – better signal to noise ratio,” says Anas.
The company is currently focusing on a type of 3D printing called laser powder bed fusion, which uses a laser to melt and fuse a computer-guided path through a bed of metal powder.
But according to Anas, DONAA’s technology can be applied to other additive manufacturing approaches, such as wire arc additive manufacturing. This technique, used for the 3D printed bridge in Ingenia 94, involves melting a metal wire with a welding tool mounted on a machine or robot.
DONAA’s technology uses a straightforward principle: filming the print and then analysing key features on the footage with AI-based computer vision algorithms.
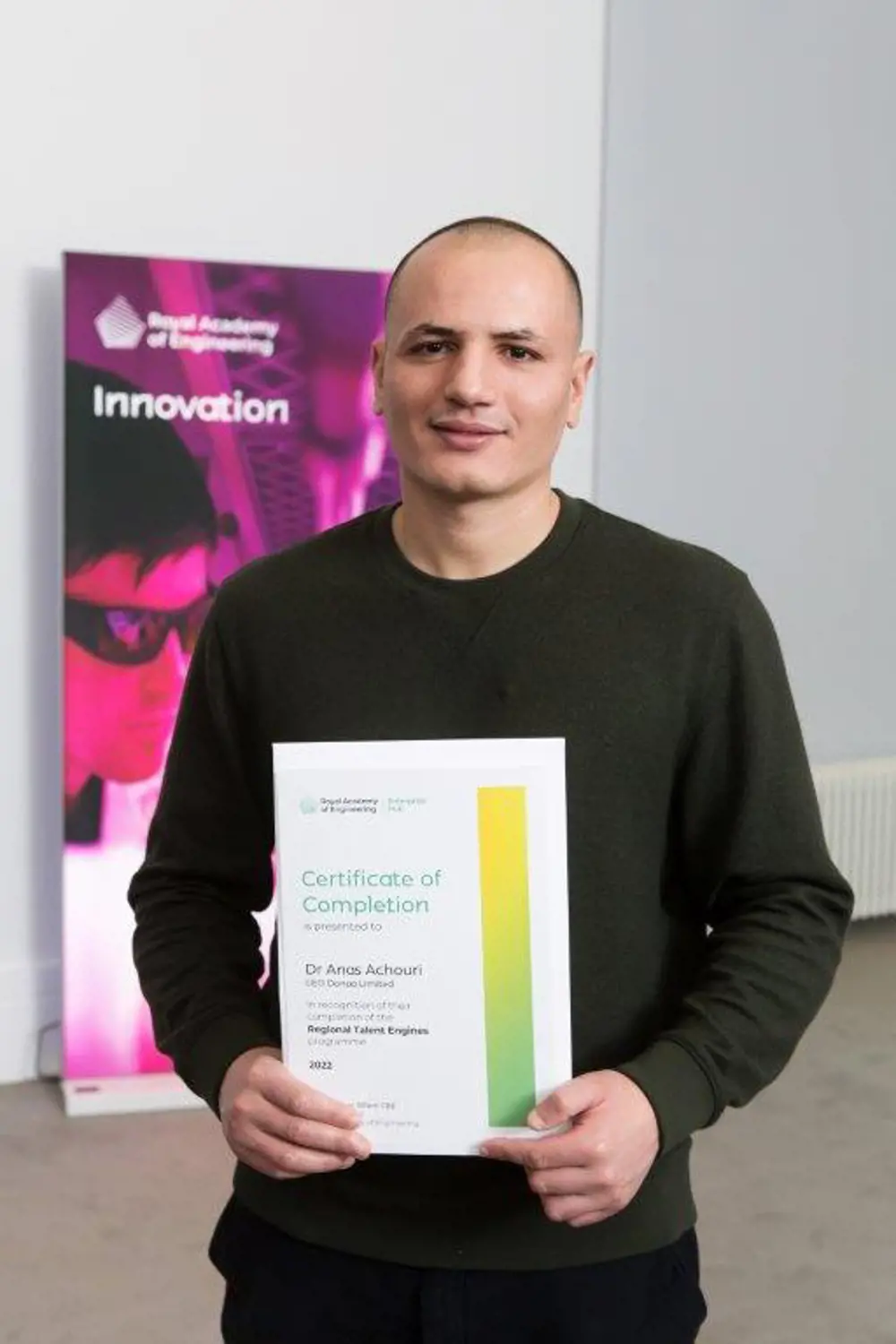
Anas on completing the Regional Talent Engines programme in 2022
Turbine blades and beyond
For DONAA, turbine blades are just the beginning. The company has three pilots currently underway: two with aerospace companies and one with a company in the nuclear power industry.
“They need some very specific material alloys and some of them are not easily machinable using traditional manufacturing,” says Anas, of the latter.
DONAA’s relationship with its partners is symbiotic. “They give us machine time, and then we can provide the feedback on their parts in the process,” he explains. “We also partner with lots of universities, because usually the universities have many different types of machines and currently each 3D printer is kind of unique. So, if you make the same part with the same machine, one after the other, they will be very different, usually.
"The more machines we use [with] our prototype, the higher performance our solution will be,” he adds.
The team has its sights set on other sectors too. Anas mentions customised, high-quality prosthetics as one avenue of interest. As with aerospace, DONAA wants to reduce waste and make the process more affordable, bringing down costs for end users.
“There is also automotive, like Formula One, for example, where they have very strict time constraints to design complex parts, so cannot afford to iterate,” says Anas.
Anas is grateful to the Royal Academy of Engineering Enterprise Hub’s Regional Talent Engines programme. “We were struggling before the programme and now we’re starting to take on excellent investors,” he says.
Anas also recently visited Silicon Valley with the Enterprise Hub’s EXPLORE 2.0 programme, and as a result secured a place on a competitive startup accelerator. In October the accelerator programme will be underway, and the team will doing their next fundraise for investment.
Clearly, there is much ahead for DONAA – and hopefully, they’ll be ready to help usher in a new era for 3D printing.
Keep up-to-date with Ingenia for free
SubscribeRelated content
Aerospace
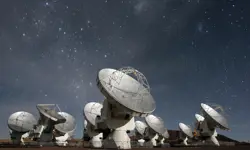
ALMA – the high altitude observatory
The Atacama Large Millimetre/submillimetre Array (ALMA) is the largest and most expensive ground-based telescope built, revolutionising our understanding of stars and planetary systems. Building it in the Atacama Desert in Chile required the ingenuity of hundreds of engineers.
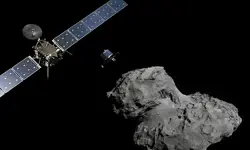
Communicating with outer space
The Royal Academy of Engineering awarded a team at BAE Systems the Major Project Award in June 2016 for their development of a powerful satellite modem system, pivotal in enabling the precise control of the pioneering Rosetta spacecraft and the first-ever soft landing of a spacecraft on a comet.
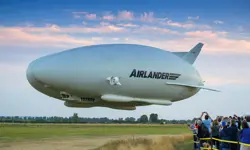
An aircraft like no other
The Airlander made headlines when it embarked on its first test flight in August 2016 as the world’s largest aircraft. Chris Daniels at Hybrid Air Vehicles Limited, and David Burns, Airlander’s Chief Test Pilot, talk about the engineering that helped it reach this stage and plans for the craft’s future.
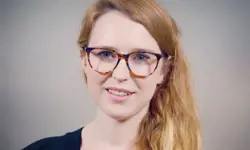
Q&A: Lucy Harden
Lucy Harden is a mechanical engineer on BAE Systems’ Digital Light Engine Head-Up Display development programme. She devises innovative solutions for pilots to display essential flight information that sits directly in their line of sight and is overlaid onto the real world.
Other content from Ingenia
Quick read
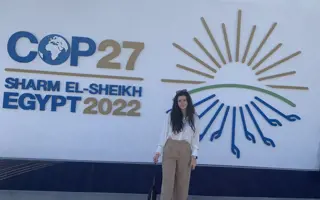
- Environment & sustainability
- Opinion
A young engineer’s perspective on the good, the bad and the ugly of COP27
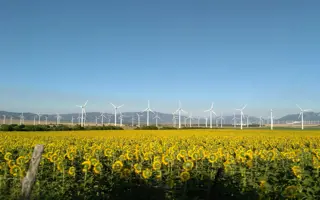
- Environment & sustainability
- Issue 95
How do we pay for net zero technologies?
Quick read
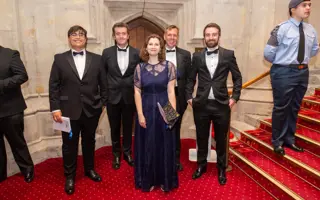
- Transport
- Mechanical
- How I got here
Electrifying trains and STEMAZING outreach
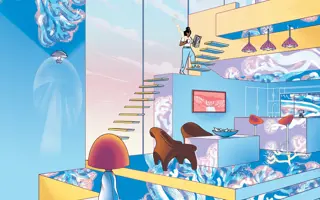
- Civil & structural
- Environment & sustainability
- Issue 95