Fusing glass and steel
Two new glasshouses in Hampshire push the engineering design of glass and steel structures to the limit. Utilising the inherent strength of folded glass panels opens up opportunities for these materials to be used more efficiently, sustainably and at less cost in the future. Graham Dodd, Director of Materials at Arup, and Felix Weber, ArupLead Engineer on the project, describe the evolution of the BombaySapphire glasshouses and consider the implications for design in glass and steel.

Looking from below, the final work being done on the Bombay Sapphire Mediterranean house, after the temporary internal supports were removed © Arup
Straddling the River Test on the site of an old paper mill in the village of Laverstoke, two new glasshouses form the central feature of a new distillery for Bombay Sapphire gin. In these greenhouses, designed by Heatherwick Studio (designers of the UK pavilion at the Shanghai Expo 2010 and the cauldron for the closing ceremony of the London 2012 Olympic Games), the distiller grows the 10 ‘botanicals’ at the heart of the gin’s special recipe. Opened in September 2014, the larger Mediterranean house – 11 m in diameter and 15 m tall – contains almond, angelica, juniper berries, lemon, coriander and orris root. The smaller tropical house – 9 m in diameter and 10 m tall – provides ideal growing conditions for cubeb berries, liquorice, cassia and grains of paradise.
The Laverstoke greenhouses bring together recent developments in the manufacture and shaping of glass and engineers’ ability to use software to optimise the geometry of structures built from glass and steel. ‘Glass houses’ no longer consist of steel skeletons supporting panes of glass, the classic example being Joseph Paxton’s Crystal Palace for the Great Exhibition in 1851.

The Heatherwick Studio’s design for the structure of each glasshouse consists of a series of pleats that rise vertically from the water they stand in, before twisting, turning and narrowing to terminate at the distillery wall. Stainless steel mullions form the ridges and valleys of the pleats. The architects wanted the steel mullions to be slender and the glass in between to be uninterrupted by highly visible cross-bracing: no ‘ladder effect’
Today’s designers and structural engineers can exploit the structural properties of glass itself, and their designs can benefit from the development of toughened and laminated glass – see A short history of structural glass. They can also use much larger sheets of glass. Design engineers can also use the strength of glass itself to substantially reduce how much steel they employ in their buildings. The glass houses have pleated forms composed of ruled surfaces that curve, twist and taper. This gives depth to the glass skin at every section making it attractive for engineers to work on as a primary structure. Recent advances in glass handling, and the ability to fold glass into increasingly complex shapes, make it possible to design such a large and complex form as a single steel-and-glass structure, with the glass itself carrying most of the loads. This is the first time that a glass and steel structure has been designed as a unit on such a scale, and with such a complex shape.
A SHORT HISTORY OF STRUCTURAL GLASS
The roots of modern glass production reach back to greenhouses built in Great Britain in the early 19th century. Joseph Paxton extended his greenhouse designs to the iconic Crystal Palace originally erected in Hyde Park for the Great Exhibition in 1851.
The Crystal Palace was essentially a rigid cast-iron structure designed to support the largest standard glass panels available at the time. Paxton also used curved glass.
Others in the 19th century designed more flexible iron structures that relied on the glass for stiffness, although the forces in the glass were no more than a few pounds, compared with up to six tonnes in the Bombay Sapphire glasshouses.
In the early decades of the 20th century, the construction industry adopted toughened and laminated glass, innovations driven by the burgeoning automobile industry.
Toughened (or tempered) glass is heat-treated to introduce compression into the outer surfaces, with the inner layers in tension. This not only increases strength, but also causes the glass to break into small pieces when smashed, like a car side window, rather than producing dangerous shards. Lamination involves sandwiching a transparent plastic layer between two layers of glass, helping the glass to retain its shape when smashed, again, like a car windscreen.
While glass plates became larger and better-quality laminates were developed, the technology remained much the same until the mid-‘60s when glass makers toughened much thicker plates. For example, Pilkington introduced thick glass with holes for bolts - used on the side wall of the Centre Point office block in London - prompting a big growth of structural assemblages using toughened glass in the 1970s. Countersunk bolts followed in the mid-80s, allowing the creation of flat surfaces. First used for squash courts, buildings such as Lloyds in London followed in the use of countersunk bolts soon after.
Laminated heat-strengthened glass entered use in the 1990s. While heat-strengthened glass has less strength than toughened glass, it also has less internal stress so it does not ‘dice’ when broken.
The use of laminated glass in construction posed problems. If fixed by clamping, over-tightening could crush the glass or squeeze out the laminate. If both glass layers broke, the sheet would remain intact but become floppy, which is no use for unsupported glass balustrades, for example. The introduction of stiffer and stronger interlayers has reduced both problems.
At the same time, production machinery has increased in size. In the late 1980s,the largest glass sheets available to the structural engineer were 4.2 m x 2 m. They can now use sheets up to 18 m x 3.6 m.
In recent years, engineers have started to design steel and glass together. Using the strength of glass can substantially reduce the amount of steel used. This is important, for example, in the windows of air traffic control towers where maximum visibility is critical. But most of these structures have been simple, symmetrical structures using plane glass: until the Bombay Sapphire distillery, that is.

The two completed glasshouses showcase the 10 exotic plant species or ‘botanicals’ used in the Bombay Sapphire distillation process © Hufton and Crow
Treating glass and steel as a single structure allowed the designers to minimise how much steel they used. The glass itself transfers the weight of the structure to the foundations. The steel does little more than hold the glass together. Engineers previously avoided treating glass and steel together for good reasons. The widely different coefficients of thermal expansion of the two materials mean that, as the temperature changes, they can move substantially relative to one another.
The usual solution to the different coefficients of thermal expansion is to limit the lengths of individual components and to bind them tightly together. This is not easy, as it risks crushing the glass or introducing large and unsightly fixings. Arup, the project’s structural engineers, solved the issue of thermal mismatch with a series of thin stainless strips bonded by an exceptionally strong, but flexible, silicone adhesive to both glass surfaces along the edges adjacent to the mullions. These strips could then be clamped rigidly to the mullions, to take all of the substantial shear forces.
The geometry of the structure is complex. Nearly every sheet of glass in the design is double-curved and each sheet is different. The designers developed a short computer programme that can subtly adjust geometrical structures to ‘unroll’ each double-curved sheet into the nearest cylindrical shape. By cold-bending the sheets, they twisted them to fit into the stainless steel mullions. Designers had already used this technique on flat glass but never on small panes of curved glass with such high stresses. This added another layer of complexity to the structural analysis.
The designers tested the structural computer models of the glasshouses under combinations of gravity, wind, snow and thermal loading, and for the ‘what if?’ case of individual panels breaking. The structure is fixed at its foundation, but to avoid introducing unnecessary additional stresses, each pleat in the glass is supported on a stiff spring controlling vertical movement and rotation.
SINGLE OR DOUBLE?

Detail showing the relationship between the tension rods and the glass panels acting in compression through the chamfered corner connection
© Bellapart
When the project was first considered, the designers had to decide if the glasshouses should be double-glazed. With sufficient waste heat available from the gin distillation, heat loss was not an issue. Indeed double glazing would have required a heavier, more intrusive structure. However, single glazing would result in condensation on the inside of the tropical house. Tests in a climate chamber revealed that a low-iron glass with a water-repellent, hydrophobic, coating was the most effective solution, as this caused the water to form on the glass as beads but not to obscure vision.
The designers adjusted the numbers and angles of the pleats, eventually opting for 31 pleats on each glasshouse, which kept the pleat width below 1.2 m. The thickness of the glass was a compromise between the need for strength and limitations in the curvature of the glass that production methods allow. The solution was two 6-mm-thick layers of tempered glass with a 1.52 mm thick interlayer of SentryGlas N-UV ionoplast, an exceptionally stiff plastic that maximises ultraviolet light transmission, reducing plant pests and diseases. Some sheets would have required too much cold-bending stress to achieve the closest approximate cylindrical shape. So the glass makers had to produce curved and twisted panels.
Glass cannot be toughened by heat treatment in that shape so the glass makers used a different process, chemical strengthening in a hot potassium chloride bath. This method strengthens only a very thin layer on the surface (around 30 micrometres, compared with 1 mm for conventional heat treatment), so surface imperfections or small scratches can reduce the strength. Glass produced this way was used in areas where loading could be kept to a minimum.
The production of these complex glass shapes clearly required specialist knowledge and expertise. Bellapart, a Spanish contractor that specialises in steel and glass structures, won the competitive tender for detailed design manufacture and assembly. The two greatest challenges for the project were cost and time. The original tender was well over the planned budget, mainly because of the quantity and high cost of the transparent structural silicone adhesive (TSSA). Used originally in the automobile and aeronautical industries, TSSA can be applied in surprisingly thin layers, around 1 mm, and has an extraordinary ability to transfer shear loads. Bellapart was appointed in the summer of 2013 with work on site due to start the following June to meet Bombay Sapphire’s timetable. With six months needed to make the glass, there were just a few weeks left to resolve design issues.
BUILDING CHALLENGES
This required considerable amount of redesign in a short time and some compromises on Arup’s original concept. The engineers focused on transferring most of the vertical forces on to the steel mullions, leaving the glass to provide stability and prevent the steel from buckling. Inserting lightweight stainless-steel tension rods connecting the mullions at the glass joints allowed the glass to act in pure compression, greatly simplifying the design of the joints.

Stress analysis of an aluminium ‘super-connector’ with angled faces to engage with the corners of the glass and bolts to connect with the flat steel plates of the mullions © Bellapart
The next problem to overcome was buckling of the glass along its short edges as a result of the larger compression forces from not using the glass in tension. This was resolved by introducing small clamps to restrain the glass midway along each tension rod. They also found that they needed to add extra steel members joining the bottoms of the valleys of the pleats inside the glasshouses.
After the developed shape of each plate was laser-cut from the largest available sheet of stainless steel the strips were plastically deformed to twist them into the required shape. Specially designed connectors joined the two plates together at 400 mm intervals to form each mullion. ‘Super-connectors’ at each glass joint also fixed the glass and anchored the tension rods. With 770 sheets of glass, the completed structure needed more than 3,000 connectors and super-connectors, each with a unique shape that had to be milled from a single block of metal using a five-axis milling machine. Softer aluminium was chosen over steel for the connectors to reduce milling time.
The manufacture of the connectors used the latest computer-controlled techniques. The computer model fed the parameters for each connector into the milling machine, so that the connectors emerged complete and in a sequence that matched the construction programme. This system worked well; only a few connectors required some human intervention to correct errors. Once installed, 6 mm thick aluminium cover plates could be added on the outside to hide the connectors.

Each stainless steel mullion had to be formed from two flat plates, 85 mm or 110 mm wide, joined longitudinally to form a V-section. The angle of the V varied with the angle of the pleat, and as the mullion turned and twisted in three dimensions © Bellapart

The construction team took care with the critical joints at the corners of the glass, where compression forces of up to 6 tonnes had to be transferred. The angle of the aluminium super connector was varied to match the orientation of the adjacent tension rod, but always shaped to suit the 45º chamfer at the corners of the glass. The builders pressure-injected a specialist epoxy resin into the gap. This had the bearing strength to take the large loads, even overlong periods of time, but was also sufficiently soft to avoid any stress concentrations in the glass © Bellapart
AWARD WINNING
The Bombay Sapphire Experience opened to the public in October 2014. The project became the first distillery, and the first ever refurbishment project, to receive an outstanding rating by BREEAM (the leading sustainability measure for buildings). All of the materials from the demolished paper mill buildings went into the new complex. In addition, spent botanicals from the distillery fuels a biomass boiler that supplies heat and hot water across the site. Waste heat from the distillation process also heats the glasshouses. The site’s renewable energy strategy also includes a photovoltaic array, and a 6 kW hydroelectric turbine in the river.
Making the glass work harder not only enables designers to produce more complex shapes, it will also lead to more structurally efficient glazed structures. If glass can be folded and used together with steel, then structural engineers can greatly reduce how much steel they use, with a corresponding reduction in embodied energy and greater sustainability. The costs of complexity may currently outweigh the material savings in such structures, but that is likely to change as material prices rise and as manufacturing costs fall for non-standard shapes and fittings.
BIOGRAPHIES
Graham Dodd CEng MIMechE FSFE is a Director at Arup where he leads a team of specialists in all kinds of construction materials and processes. He has over 25 years’ experience in the structural use of glass and is Chairman of the Society of Façade Engineering.
Felix Weber, Arup Lead Engineer on the Bombay Sapphire project, is trained as an architect and an engineer, specialising in designing structures with uncommon materials. He currently leads the Arup facade team in San Francisco.

The two completed glasshouses showcase the 10 exotic plant species or ‘botanicals’ used in the Bombay Sapphire distillation process © Hufton and Crow
Keep up-to-date with Ingenia for free
SubscribeOther content from Ingenia
Quick read
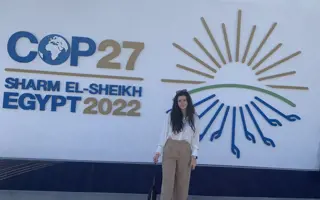
- Environment & sustainability
- Opinion
A young engineer’s perspective on the good, the bad and the ugly of COP27
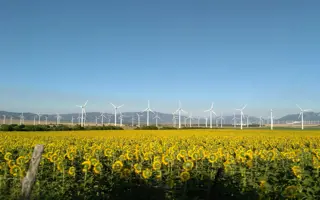
- Environment & sustainability
- Issue 95
How do we pay for net zero technologies?
Quick read
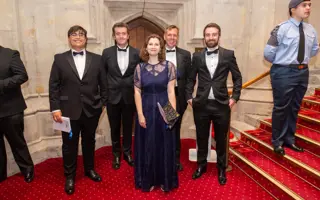
- Transport
- Mechanical
- How I got here
Electrifying trains and STEMAZING outreach
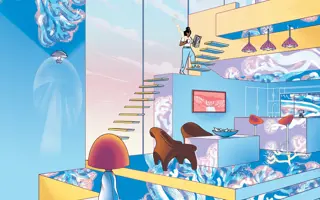
- Civil & structural
- Environment & sustainability
- Issue 95